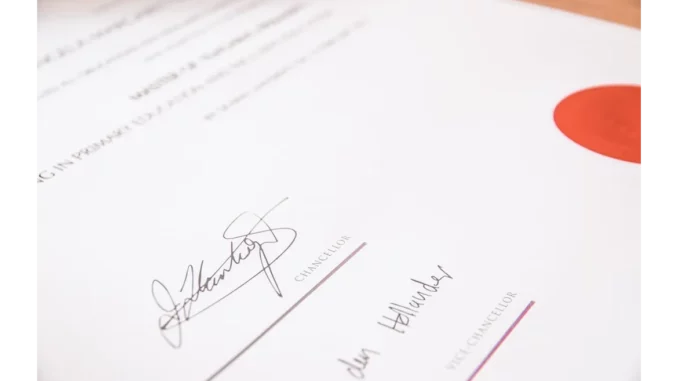
When I sat down with Catherine Edwards, Quality Assurance Manager at a mid-sized pharmaceutical manufacturing company, I expected a routine discussion about the run-of-the-mill tasks involved in creating a Certificate of Analysis (COA). What unfolded, however, was an enlightening conversation about how the process has evolved from paper trails to digital efficiency.
Discover how Focus360 Energy can help with BREEAM certification.
The Genesis of Change
“Before we switched to digital,” Catherine began, her tone reflective, “the entire process of creating a COA was cumbersome and error-prone. We relied heavily on paper documentation, which meant hours of manual data entry, checking, and rechecking to ensure everything was in compliance.”
COAs are essential documents that certify a product meets its specified quality and safety standards. These certificates are crucial not only for customer assurance but also for regulatory compliance, particularly in industries like pharmaceuticals and food manufacturing. Catherine explained that a COA includes detailed information such as the product name, batch number, test results, and dates of manufacture and expiry. “Accuracy is non-negotiable,” she added.
The Move to Digital
“Our transition to digital checklists was driven by a need to streamline operations and reduce errors,” Catherine said. The company adopted SafetyCulture, a platform known for its digital checklist capabilities, to manage their COA creation process. “Going paperless was a game-changer for us. The ability to create, manage, and store COAs electronically not only saved us time but also improved our accuracy and compliance.”
Why SafetyCulture?
When asked why they chose SafetyCulture, Catherine noted, “The platform’s user-friendly interface and robust features made it an obvious choice. We needed something that could handle the complexity of our COA requirements while being easy for our team to use.”
Using digital checklists, the company could standardise the COA creation process. “Every step is now documented and traceable,” Catherine explained. “From entering test conditions and results to final approval, everything is streamlined and logged. This ensures that nothing falls through the cracks.”
The Benefits of Going Digital
One of the most significant advantages of using digital checklists, Catherine highlighted, was the reduction in human error. “Manual entry is always fraught with risks—typos, missed fields, and misfiled documents. With digital checklists, these risks are minimised. The system prompts you to fill in all necessary fields and won’t allow you to proceed unless everything is complete.”
Another advantage was the ease of updating information. “If there’s a change in regulatory requirements or internal quality standards, we can quickly update our checklists. This ensures we’re always compliant without having to redo everything from scratch.”
Compliance and Traceability
Compliance is a critical aspect of COA creation, especially in the pharmaceutical industry where regulatory scrutiny is intense. Catherine pointed out, “The FDA requires specific elements in a COA, such as the manufacturer’s name, product details, batch number, and test results. With digital checklists, we can ensure all these elements are consistently included.”
Traceability is another key benefit. “Every action taken within the system is logged, creating an audit trail. This is invaluable during inspections or audits, as we can easily demonstrate compliance and trace back any issues to their source.”
The Human Element
While the digital transformation has streamlined many aspects of COA creation, Catherine was quick to note that the human element remains crucial. “Our quality control team still plays a vital role in overseeing the process, interpreting test results, and making final approvals. The technology supports them, but it doesn’t replace their expertise.”
Implementing the Change
Transitioning to digital checklists wasn’t without its challenges. “Change management is always tricky,” Catherine admitted. “We had to train our staff and get everyone on board with the new system. There was some initial resistance, but once people saw the benefits, they quickly adapted.”
She also mentioned the importance of choosing the right technology partner. “We worked closely with the SafetyCulture team to customise the platform to our needs. Their support was instrumental in making the transition smooth.”
Final Thoughts
As our conversation drew to a close, Catherine reflected on the journey. “Switching to digital checklists has been transformative. It has made our COA creation process more efficient, accurate, and compliant. I would recommend it to any company looking to improve their quality assurance processes.”
Her words resonated with me long after our interview ended. The move from paper to digital is not just about adopting new technology; it’s about embracing a more efficient, reliable, and transparent way of working. As companies like Catherine’s continue to innovate, the benefits of going digital become increasingly evident.
By Tobiasz Karcz
Be the first to comment