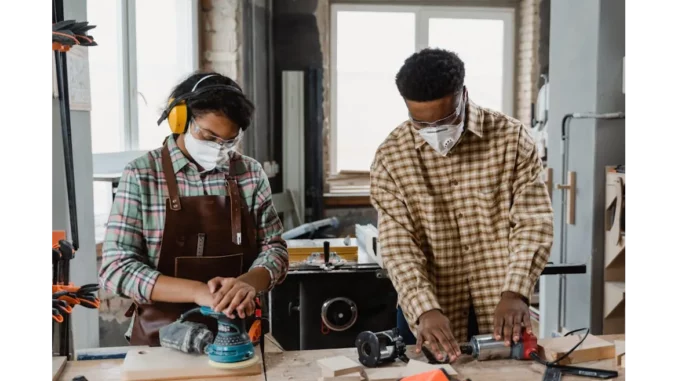
During my recent conversation with James Cartwright, the Project Manager at British Offsite, it quickly became evident that their collaboration with Weston Homes represents more than a mere contractual engagement; it signifies a pivotal moment. James’s enthusiasm was unmistakable as he elaborated on the company’s inaugural implementation of the UNisystemLB (Load Bearing) technology for Weston Homes’ Tayfen Court project in Bury St Edmunds—a 171-home development with a valuation of £3.8 million.
Successful low-energy building design hinges on careful planning. Focus360 Energy can help.
“British Offsite has consistently been a trailblazer in construction innovation,” James remarked, settling into his chair with a palpable sense of pride. “However, this project holds particular significance as it marks our first utilisation of the UNisystemLB technology. This is a transformative development for us and, I believe, for the wider construction industry.”
The UNisystemLB is a load-bearing, structurally self-supporting system designed for edifices up to six storeys, with a maximum finished floor height of 18 metres. It comprises UNipanelLB for external walls and UNiwallLB for internal compartmentalisation, both engineered for swift deployment. This renders it exceptionally suitable for mid-rise apartment complexes, healthcare facilities, educational institutions, and student accommodation projects.
As James delved into the technical aspects of the technology, his excitement was palpable. “The UNisystemLB aims to reduce build programme durations by 30-50% or more. That’s a game-changer! For the Tayfen Court project, we’ve deployed 513 UNipanelLB panels for external walls and 397 UNiwallLB panels for internal compartmentalisation. These panels are pre-installed with head shutters, windows, and doors customised to Weston Homes’ specifications, ensuring airtightness, thermal efficiency, acoustic performance, and fire safety.”
One of the most remarkable attributes of the UNisystemLB is its adaptability. The panels can be manufactured up to a maximum width of 8.4 metres and a height of 3.2 metres. For requirements beyond these dimensions, such as uniquely shaped panels like gable ends, bespoke solutions are available. “This flexibility is one of the primary reasons Weston Homes was eager to collaborate with us,” James pointed out.
The Tayfen Court project also reaps the benefits of offsite manufacturing, significantly expediting the construction timeline. “By the time the panels arrive on-site, they are ready for immediate installation. This facilitates quicker compartmentalisation of floors and allows for earlier customer viewings, a substantial advantage for developers aiming to enhance asset value,” James explained.
Moreover, the lightweight nature of the UNisystemLB permits traditional pad foundations and vented voids to be substituted with a ground-bearing slab, thus offering further programme and cost efficiencies. “The panels are equipped with weather sheathing boards and fire panels on both sides, filled with insulation that meets thermal, acoustic, and fire performance standards. It’s about delivering a comprehensive, efficient solution,” James added.
When the conversation shifted to the internal fit-out, James’s eyes sparkled with excitement. “Our involvement extends beyond mere structural elements. The internal fit-out is customised to Weston Homes’ precise specifications. We’re talking 225 bathrooms with bespoke vanity units, taps, shower trays, screens, baths, and tiles. Additionally, 146 wardrobe systems with mirrored sliding doors and timber decors, and 146 quartz kitchen worktops. Everything is precision-engineered using laser templating and CNC machining. Even the sink, hob, tap, and instant boiling water installations are included.”
I could discern why British Offsite was particularly enthusiastic about this project. Shaun Weston, the Managing Director, had previously expressed his excitement in a press release, stating, “We are thrilled to announce that the first UNisystemLB panels have been delivered and installed on-site in Bury St Edmunds. Tayfen Court exemplifies the potential of our UNisystemLB technology in delivering high-quality, energy-efficient homes swiftly and reliably. Our product is fast, flexible, reliable, and competitive, making it an ideal solution for modern construction needs. This partnership showcases our dedication to innovation and excellence in offsite construction.”
As our conversation concluded, I inquired what this project signified for the future of British Offsite. James paused momentarily, contemplating the journey ahead. “This is just the beginning. The success of the Tayfen Court project will pave the way for more developments employing the UNisystemLB. We’re already exploring applications in healthcare, education, and other residential projects. The potential is enormous, and we’re prepared to lead the charge.”
Leaving the British Offsite headquarters, I found myself sharing in the optimism and excitement. The UNisystemLB technology is poised to be more than a progressive step for British Offsite; it has the potential to revolutionise the entire construction industry. As James aptly put it, this is merely the beginning.
Be the first to comment