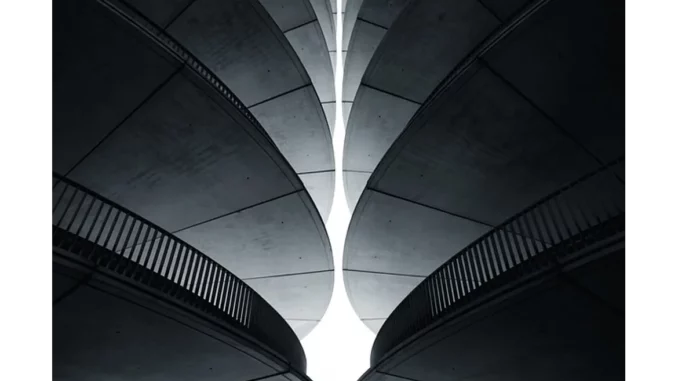
When I sat down with Martin Davies, a seasoned project manager in the construction industry, I knew we were about to delve into a topic that was not only timely but critical for the future of the built environment. Martin has been at the forefront of integrating sustainability into construction projects, and his insights into why we must combine cost and carbon considerations were nothing short of illuminating.
Air quality is vital in planning. See how Focus360 Energy can assist.
“Reducing carbon emissions is a challenge that everybody in our industry has the power to get behind – it’s not just the remit of quantity surveyors, designers, or engineers,” Martin began, setting the tone for our discussion. “We all have a role to play, and it’s time we start seeing cost and carbon as two sides of the same coin.”
Here are the six compelling reasons Martin shared for why it’s essential to combine cost and carbon in construction.
1. It’s More Efficient and Saves Time
Martin emphasised that the industry has long been plagued by siloed working, where social, environmental, and cost implications are evaluated separately. “In a poll of 300 construction professionals, 51% told us that cost and carbon tend to be considered as separate issues. This needs to change,” he stressed. By integrating cost and carbon assessments, the data collection exercise becomes a one-time effort, making the whole life carbon assessment (WLCA) process more efficient and time-saving. “It’s about streamlining our processes and making better use of our resources.”
2. Maximising Our Existing Cost Experts
One of the most striking points Martin made was about leveraging the skills of quantity surveyors. “Quantity surveyors are already adept at measuring and benchmarking costs. The principles of cost estimating are very similar to those required for carbon measurement,” he explained. According to a poll, 40% of respondents believed that a quantity surveyor or cost consultant would be best-placed to assess whole life carbon emissions alongside costs. “It’s logical and efficient to utilise their expertise in this new dimension.”
3. Seamless Integration into Value Engineering
Value engineering has always been about delivering the most economical solutions while meeting client requirements. Martin noted that the demands are evolving. “Clients are increasingly asking for whole life carbon assessments—33% of contractors reported this, up from 14% last year,” he said. By integrating carbon considerations into the value engineering process, the industry can ensure that decisions are not only cost-effective but also environmentally sound. “It’s a natural progression that aligns with our evolving priorities.”
4. On the Path to Mandating Carbon Reporting
Martin highlighted the impending legislative changes that could make carbon reporting mandatory. “The Future Homes and Buildings Standards, set to come into force in 2025, will likely mandate the reporting and measuring of whole life embodied carbon,” he pointed out. “By getting ahead of these regulations, industry professionals can ensure they are not left behind.” This proactive approach could also help businesses stay competitive and compliant in a rapidly changing regulatory landscape.
5. Financial Incentives and Market Demand
“The finance sector is increasingly favouring projects with strong sustainability credentials,” Martin said. Investors are using frameworks like those from the Institutional Investors Group for Climate Change (IIGCC) to assess and manage climate-related risks. “Buildings with high environmental ratings are commanding higher rents—Property Week found that BREEAM ‘Outstanding’ buildings in central London have rents 23% higher than average,” he added. By combining cost and carbon, developers can better predict project viability and attract investment.
6. Essential for Global Growth and Sustainability
With the global construction market predicted to grow by 42% by 2030, Martin underscored the necessity of factoring carbon into design choices. “Evaluating both cost and carbon allows us to choose materials that are sustainable and cost-effective,” he said. While there is no one-size-fits-all solution, the ability to balance these factors can drive innovation and lead to lower whole life carbon outcomes. “It’s about making informed decisions that benefit both the environment and the bottom line.”
As our conversation drew to a close, Martin left me with a powerful thought: “The tools and methodologies are now in place. It’s time for everyone in the industry to embrace this dual approach and make a tangible impact on reducing carbon emissions.”
His insights made it clear that the integration of cost and carbon is not just a trend but a necessary evolution for the construction industry. By adopting this holistic approach, we can not only meet regulatory requirements and market demands but also contribute to a more sustainable future.
Emily Thompson
Be the first to comment