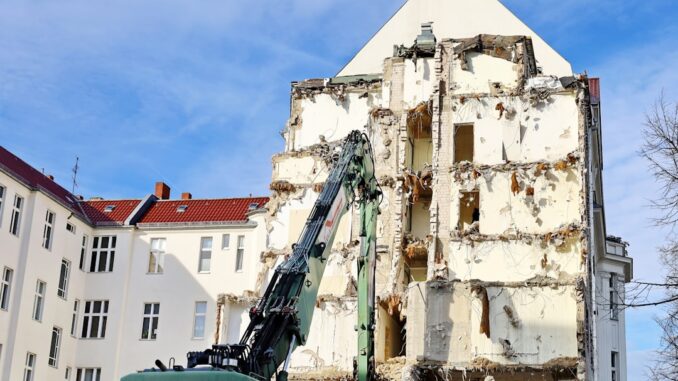
Abstract
Demolition, traditionally viewed as a singular endpoint in the building lifecycle, is undergoing a fundamental re-evaluation. This research report argues for a paradigm shift towards deconstruction, a systematic process of dismantling buildings to recover materials for reuse and recycling. While demolition focuses on efficiency and speed, deconstruction prioritizes resource conservation, waste reduction, and the creation of skilled labor opportunities. This report explores the limitations of current demolition practices, the economic and environmental benefits of deconstruction, the technical challenges involved in implementing deconstruction at scale, policy and regulatory frameworks that can incentivize deconstruction, and the societal implications of transitioning towards a circular economy in the built environment. A comprehensive analysis of case studies, technological advancements, and regulatory landscapes across different regions highlights the potential for deconstruction to become the standard practice for end-of-life building management, contributing to a more sustainable and resource-efficient construction industry.
Many thanks to our sponsor Focus 360 Energy who helped us prepare this research report.
1. Introduction: Beyond Demolition – A Call for Deconstruction
The construction industry stands as a significant consumer of natural resources and a major contributor to global waste streams. Traditional demolition practices, characterized by their speed and cost-effectiveness, often result in the irreversible destruction of valuable materials. This ‘cradle-to-grave’ approach is increasingly unsustainable, particularly in light of growing resource scarcity, environmental concerns, and the urgent need to transition towards a circular economy.
Demolition, at its core, is a destructive process. While advancements in demolition techniques have improved safety and efficiency, the fundamental outcome remains the same: the reduction of a building to rubble, much of which ends up in landfills. The environmental and economic costs associated with this approach are substantial. Landfilling construction and demolition (C&D) waste consumes valuable land, contributes to greenhouse gas emissions through decomposition and transportation, and represents a significant loss of embodied energy and valuable materials.
Deconstruction, in contrast, offers a more sustainable alternative. It involves the systematic dismantling of buildings, prioritizing the recovery of materials for reuse and recycling. Deconstruction is not simply a more meticulous form of demolition; it represents a fundamental shift in perspective. It treats buildings as material banks, recognizing the potential for components and materials to be repurposed and reintegrated into new construction projects or other applications. By prioritizing material recovery, deconstruction can significantly reduce C&D waste, conserve natural resources, and create economic opportunities in the reuse and recycling sectors.
This report argues that deconstruction should be viewed as a critical component of a circular economy in the built environment. A circular economy aims to minimize waste and maximize resource utilization by keeping materials in use for as long as possible. Deconstruction plays a crucial role in this paradigm by enabling the recovery and reuse of building materials, thereby reducing the demand for virgin resources and minimizing environmental impact. The transition from demolition to deconstruction requires a concerted effort involving policymakers, architects, engineers, contractors, and building owners. This report aims to provide a comprehensive overview of the challenges and opportunities associated with deconstruction, highlighting the potential for this approach to transform the way we manage end-of-life buildings and contribute to a more sustainable future.
Many thanks to our sponsor Focus 360 Energy who helped us prepare this research report.
2. Demolition Practices: An Overview and Critical Assessment
Demolition, broadly defined, encompasses the complete or partial dismantling of a building or structure. The methods employed vary significantly depending on the size and complexity of the building, site conditions, and regulatory requirements. Common demolition techniques include:
- Mechanical Demolition: This is the most prevalent method, utilizing heavy machinery such as excavators, bulldozers, and wrecking balls. Mechanical demolition is typically employed for large-scale projects and is favored for its speed and cost-effectiveness. However, it often results in significant material damage and is less selective in material recovery.
- Implosion: Controlled implosions involve strategically placing explosives to collapse a building in a predetermined manner. This method is primarily used for high-rise buildings and large structures in urban environments. While implosions are efficient, they generate substantial dust and noise pollution and offer limited opportunities for material recovery.
- Selective Demolition: This technique involves the careful removal of specific building components, such as windows, doors, and fixtures, prior to the complete demolition of the structure. Selective demolition aims to salvage valuable materials and reduce waste. However, it is often labor-intensive and may not be economically viable for all projects.
The advantages of conventional demolition lie primarily in its speed and cost-effectiveness. The use of heavy machinery and explosive techniques allows for the rapid dismantling of buildings, minimizing disruption to surrounding areas and reducing labor costs. However, these advantages come at a significant environmental and social cost.
The primary limitations of demolition practices are:
- Waste Generation: Demolition generates massive amounts of C&D waste, a significant portion of which ends up in landfills. This waste includes materials such as concrete, wood, asphalt, metal, and drywall, many of which could be recycled or reused.
- Resource Depletion: The reliance on demolition perpetuates the unsustainable cycle of resource extraction, manufacturing, and disposal. By failing to recover and reuse building materials, demolition contributes to the depletion of natural resources and increases the environmental impact of the construction industry.
- Environmental Pollution: Demolition activities can generate significant air and water pollution. Dust and debris can contaminate air and water sources, posing health risks to nearby residents and ecosystems. Demolition can also release hazardous materials, such as asbestos and lead, into the environment if not handled properly.
- Loss of Embodied Energy: Buildings contain significant amounts of embodied energy, which is the energy consumed during the extraction, processing, and transportation of building materials. Demolition results in the loss of this embodied energy, requiring the expenditure of additional energy to manufacture new materials.
- Destruction of Cultural Heritage: In some cases, demolition can lead to the destruction of historically significant buildings and structures. This can result in the loss of cultural heritage and architectural character.
Critical assessment of these practices reveals a clear need for more sustainable approaches to end-of-life building management. The limitations of demolition highlight the potential benefits of deconstruction as a viable alternative.
Many thanks to our sponsor Focus 360 Energy who helped us prepare this research report.
3. Deconstruction: Principles, Techniques, and Benefits
Deconstruction, also known as dismantling or selective demolition, is a systematic process of carefully taking apart a building, with the primary goal of recovering materials for reuse and recycling. It represents a fundamental shift from the destructive approach of traditional demolition to a more sustainable and resource-efficient model.
The key principles of deconstruction are:
- Material Recovery: The primary objective of deconstruction is to maximize the recovery of building materials for reuse and recycling.
- Waste Reduction: By recovering and repurposing materials, deconstruction significantly reduces the amount of C&D waste sent to landfills.
- Resource Conservation: Deconstruction conserves natural resources by reducing the demand for virgin materials.
- Skill Development: Deconstruction creates opportunities for skilled labor and workforce development.
- Environmental Protection: Deconstruction minimizes environmental pollution by reducing waste and conserving resources.
Deconstruction techniques vary depending on the type of building, the materials used, and the desired level of material recovery. Common techniques include:
- Manual Dismantling: This involves the careful disassembly of building components using hand tools. Manual dismantling is particularly well-suited for recovering delicate or valuable materials, such as windows, doors, and fixtures.
- Mechanical Dismantling: This involves the use of small-scale machinery, such as forklifts and cranes, to assist in the disassembly of building components. Mechanical dismantling can increase efficiency and reduce labor costs compared to manual dismantling.
- Selective Demolition with Targeted Recovery: This technique combines elements of both demolition and deconstruction. It involves carefully removing specific building components for reuse or recycling, while demolishing the remaining structure using conventional methods.
The benefits of deconstruction are multifaceted and extend beyond environmental considerations. These benefits include:
- Environmental Benefits: Deconstruction reduces C&D waste, conserves natural resources, reduces greenhouse gas emissions, and minimizes environmental pollution.
- Economic Benefits: Deconstruction creates jobs in the reuse and recycling sectors, reduces landfill costs, and provides access to affordable building materials.
- Social Benefits: Deconstruction promotes skill development, strengthens local economies, and preserves cultural heritage.
Studies have consistently shown that deconstruction can be economically competitive with traditional demolition, especially when considering the long-term environmental and social benefits. While deconstruction may require higher initial labor costs, these costs can be offset by the revenue generated from the sale of recovered materials and the reduced costs of landfill disposal. Furthermore, the environmental benefits of deconstruction, such as reduced greenhouse gas emissions and resource conservation, can have significant long-term economic value.
However, the successful implementation of deconstruction requires careful planning and execution. It is essential to conduct a thorough building assessment to identify valuable materials and develop a deconstruction plan. Proper training and safety protocols are also crucial to ensure the safety of workers and the integrity of recovered materials.
Many thanks to our sponsor Focus 360 Energy who helped us prepare this research report.
4. Technological Advancements in Deconstruction and Material Recovery
The adoption of deconstruction practices is increasingly facilitated by technological advancements in various areas, including building information modeling (BIM), robotic dismantling, and advanced material sorting and processing.
- Building Information Modeling (BIM): BIM is a digital representation of a building’s physical and functional characteristics. BIM can be used to create a detailed inventory of building materials, identify potential hazards, and develop a deconstruction plan. By providing a comprehensive understanding of the building’s structure and materials, BIM can significantly improve the efficiency and effectiveness of deconstruction projects. BIM models that integrate lifecycle information, including the materials used in construction and their potential for reuse or recycling, can greatly enhance the planning and execution of deconstruction projects. This includes identifying hazardous materials and optimizing the sequence of dismantling.
- Robotic Dismantling: The use of robots in deconstruction is a rapidly developing field. Robots can be used to automate repetitive tasks, improve safety, and increase efficiency. For example, robots can be used to remove drywall, dismantle structural components, and sort materials. While the widespread adoption of robotic dismantling is still in its early stages, the potential benefits are significant.
- Advanced Material Sorting and Processing: Efficient material sorting is essential for maximizing the value of recovered materials. Advanced sorting technologies, such as optical sensors and automated sorting systems, can be used to separate different types of materials with high accuracy. Furthermore, advanced processing techniques, such as shredding, crushing, and cleaning, can be used to prepare recovered materials for reuse or recycling. Examples include sensor-based sorting technologies to separate different types of plastics or metals, and mobile crushing units that can process concrete on-site.
The integration of these technologies can significantly reduce the cost and complexity of deconstruction, making it a more viable option for a wider range of projects. However, the successful implementation of these technologies requires careful planning and investment. Furthermore, it is important to consider the environmental impact of these technologies, ensuring that they are used in a sustainable manner.
The development of new technologies specifically tailored for deconstruction is crucial. This includes sensors for identifying material composition, robotic systems for selective dismantling, and advanced material processing techniques that can improve the quality and value of recovered resources. Continued investment in research and development in these areas is essential for accelerating the adoption of deconstruction practices.
Many thanks to our sponsor Focus 360 Energy who helped us prepare this research report.
5. Policy and Regulatory Frameworks: Incentivizing Deconstruction
The successful transition from demolition to deconstruction requires supportive policy and regulatory frameworks. Governments can play a crucial role in incentivizing deconstruction through a variety of measures, including:
- Waste Diversion Targets: Setting mandatory waste diversion targets for C&D waste can encourage the adoption of deconstruction practices. These targets can be implemented at the national, regional, or local level.
- Landfill Bans: Banning the disposal of recyclable materials in landfills can create a strong incentive for deconstruction. This measure can be particularly effective for materials such as wood, concrete, and metal.
- Tax Incentives and Subsidies: Providing tax incentives or subsidies for deconstruction projects can reduce the upfront costs and make deconstruction more economically attractive.
- Building Codes and Standards: Incorporating deconstruction principles into building codes and standards can promote the design of buildings that are easier to deconstruct at the end of their life. This includes promoting the use of modular construction, reversible connections, and standardized components.
- Extended Producer Responsibility (EPR) Schemes: EPR schemes can hold manufacturers responsible for the end-of-life management of their products. This can incentivize manufacturers to design products that are easier to deconstruct and recycle.
- Green Building Certifications: Green building certification programs, such as LEED and BREEAM, can award points for deconstruction practices. This can encourage building owners and developers to prioritize deconstruction.
Regulatory frameworks can also be used to address the challenges associated with deconstruction, such as the handling of hazardous materials and the potential for increased labor costs. For example, regulations can be put in place to ensure the safe removal and disposal of asbestos and lead-based paint. Furthermore, government-funded training programs can help to develop a skilled workforce for deconstruction projects.
Examples of successful policy initiatives in different regions include:
- European Union Waste Framework Directive: The EU Waste Framework Directive sets a target of 70% reuse, recycling, and other material recovery of non-hazardous C&D waste by 2020. This directive has driven significant progress in C&D waste management across Europe.
- US LEED Rating System: The LEED rating system awards points for deconstruction and material reuse. This has encouraged building owners and developers in the United States to prioritize deconstruction.
- Local Ordinances: Some cities and counties have implemented local ordinances that require deconstruction for certain types of buildings or projects. These ordinances can be particularly effective in promoting deconstruction in specific areas.
Effective policy and regulatory frameworks are essential for creating a level playing field and driving the widespread adoption of deconstruction practices. These frameworks should be designed to be flexible and adaptable to local conditions, while also providing clear and consistent guidance for industry stakeholders.
Many thanks to our sponsor Focus 360 Energy who helped us prepare this research report.
6. Case Studies: Successful Deconstruction Projects and Lessons Learned
Analyzing real-world deconstruction projects provides valuable insights into the practical challenges and opportunities associated with this approach. Several successful deconstruction projects have demonstrated the feasibility and benefits of deconstruction in various contexts.
- The Reclaimed Materials Marketplace (RMM): While not a single building deconstruction, RMM serves as a case study for infrastructure supporting reuse. Platforms like RMM, and others that function as architectural salvage marketplaces, directly facilitate the use of reclaimed building materials. The lessons learned from these platforms show the importance of ease of access to materials, quality control and grading and the importance of marketing and logistics infrastructure.
- The 19th Century Schoolhouse Deconstruction (USA): In Iowa, a 19th Century one-room schoolhouse was carefully deconstructed. The project yielded lumber used in new construction. This demonstrates the ability to salvage valuable materials from older structures, preserving embodied energy and historical significance.
- The CMU Deconstruction Project at Carnegie Mellon University (USA): This project demonstrated the systematic recovery of CMU blocks for reuse, showcasing the potential for circular economy practices even in large-scale institutional settings. The project demonstrated the use of careful planning and execution to maximize material recovery and minimize waste.
These case studies highlight several key lessons learned:
- Planning is Essential: Thorough planning is crucial for the success of deconstruction projects. This includes conducting a detailed building assessment, developing a deconstruction plan, and securing the necessary permits and approvals.
- Worker Training is Critical: Deconstruction requires a skilled workforce with expertise in dismantling techniques, material handling, and safety protocols. Providing adequate training is essential for ensuring the safety of workers and the integrity of recovered materials.
- Material Marketing is Important: Successfully marketing recovered materials is essential for generating revenue and reducing waste. This may involve grading, cleaning, and packaging materials to meet market demand.
- Collaboration is Key: Collaboration between architects, engineers, contractors, and building owners is essential for the success of deconstruction projects. This includes sharing knowledge, coordinating activities, and developing innovative solutions.
- Flexibility is Necessary: Deconstruction projects often encounter unexpected challenges. It is important to be flexible and adaptable in order to overcome these challenges and achieve the desired outcomes.
By studying successful deconstruction projects and learning from past experiences, we can improve the efficiency and effectiveness of deconstruction practices and accelerate the transition towards a more sustainable construction industry.
Many thanks to our sponsor Focus 360 Energy who helped us prepare this research report.
7. Societal Implications: Deconstruction as a Driver of Circular Economy and Green Jobs
The shift from demolition to deconstruction has significant societal implications, extending beyond environmental and economic benefits. Deconstruction can act as a catalyst for the development of a circular economy in the built environment, fostering sustainable consumption patterns and reducing our reliance on virgin resources.
Furthermore, deconstruction has the potential to create green jobs and stimulate economic growth. Deconstruction projects require a skilled workforce with expertise in dismantling techniques, material handling, and recycling. This creates opportunities for training and employment in the reuse and recycling sectors. Studies have shown that deconstruction can create more jobs per ton of waste processed compared to traditional demolition. This creates opportunity for social impact.
The transition to deconstruction also has implications for education and workforce development. Educational institutions need to incorporate deconstruction principles into their curricula, training architects, engineers, and construction workers in sustainable building practices. Furthermore, government-funded training programs can help to develop a skilled workforce for deconstruction projects, particularly in underserved communities. Training programs should emphasize safe work practices, material identification and sorting, and the use of appropriate tools and equipment. Furthermore, education programs should address the social and economic benefits of deconstruction, promoting a culture of sustainability and resource conservation.
Deconstruction can also contribute to community revitalization by providing access to affordable building materials. Recovered materials can be used to renovate existing buildings, construct affordable housing, and create community gardens. This can help to improve the quality of life in low-income communities and promote social equity.
The long-term societal implications of deconstruction are profound. By reducing waste, conserving resources, and creating green jobs, deconstruction can contribute to a more sustainable and equitable future. However, realizing these benefits requires a concerted effort involving policymakers, industry stakeholders, and community members. This includes promoting public awareness of the benefits of deconstruction, developing supportive policies and regulations, and investing in education and workforce development.
Many thanks to our sponsor Focus 360 Energy who helped us prepare this research report.
8. Challenges and Barriers to Widespread Adoption
Despite its numerous benefits, deconstruction faces several challenges and barriers that hinder its widespread adoption. These challenges can be broadly categorized as economic, technical, regulatory, and cultural.
- Economic Barriers: Deconstruction can be more labor-intensive and time-consuming than traditional demolition, resulting in higher upfront costs. Furthermore, the market for recovered materials may be limited or uncertain, making it difficult to generate revenue from the sale of these materials. Successfully addressing the economic barriers requires creating a strong demand for recovered materials and streamlining the deconstruction process through technological advancements and improved planning.
- Technical Barriers: Deconstruction requires specialized skills and equipment, which may not be readily available in all areas. Furthermore, some buildings may be difficult or impossible to deconstruct due to their design, materials, or condition. Addressing these technical barriers requires investing in training and workforce development, developing new deconstruction technologies, and promoting the design of buildings that are easier to deconstruct.
- Regulatory Barriers: Existing building codes and regulations may not adequately address deconstruction, creating uncertainty and confusion for industry stakeholders. Furthermore, some regulations may unintentionally discourage deconstruction, such as those related to hazardous materials and waste management. Addressing these regulatory barriers requires updating building codes and regulations to reflect the principles of deconstruction and providing clear and consistent guidance for industry stakeholders.
- Cultural Barriers: Traditional demolition is often seen as the quickest and cheapest way to dispose of unwanted buildings. Overcoming this cultural inertia requires educating the public and industry stakeholders about the benefits of deconstruction and promoting a culture of sustainability and resource conservation. This includes showcasing successful deconstruction projects, highlighting the economic and environmental benefits of deconstruction, and promoting the value of recovered materials.
Addressing these challenges requires a multi-faceted approach involving policymakers, industry stakeholders, and community members. This includes providing financial incentives for deconstruction projects, developing new deconstruction technologies, updating building codes and regulations, and educating the public about the benefits of deconstruction. Furthermore, it is important to foster collaboration between architects, engineers, contractors, and building owners to promote the adoption of deconstruction practices.
Many thanks to our sponsor Focus 360 Energy who helped us prepare this research report.
9. Future Directions and Research Needs
Deconstruction is a rapidly evolving field with significant potential to transform the construction industry. To fully realize the benefits of deconstruction, further research is needed in several key areas:
- Life Cycle Assessment (LCA): Conducting comprehensive LCAs of deconstruction projects compared to traditional demolition is essential for quantifying the environmental benefits of deconstruction. This includes assessing the energy consumption, greenhouse gas emissions, and waste generation associated with each approach.
- Market Analysis: Further research is needed to understand the demand for recovered materials and develop strategies for creating a stronger market for these materials. This includes identifying potential end-use applications for recovered materials, developing quality standards, and promoting the use of recovered materials in new construction projects.
- Technology Development: Continued investment in research and development is needed to develop new deconstruction technologies that are more efficient, cost-effective, and environmentally friendly. This includes developing robotic dismantling systems, advanced material sorting technologies, and new processing techniques for recovered materials.
- Policy Analysis: Further research is needed to evaluate the effectiveness of different policy and regulatory frameworks for promoting deconstruction. This includes analyzing the impact of waste diversion targets, landfill bans, tax incentives, and building codes on the adoption of deconstruction practices.
- Social Impact Assessment: Research is needed to assess the social impacts of deconstruction, including the creation of green jobs, the improvement of community revitalization, and the promotion of social equity.
- Hazardous Materials Remediation: Advanced research into cost-effective and environmentally sound methods for the safe removal and disposal of hazardous materials, such as asbestos and lead-based paint, during deconstruction is critical.
By addressing these research needs, we can advance the science and practice of deconstruction and accelerate the transition towards a more sustainable construction industry. This requires collaboration between researchers, policymakers, industry stakeholders, and community members. It also requires a commitment to innovation and a willingness to challenge traditional approaches to building management.
Many thanks to our sponsor Focus 360 Energy who helped us prepare this research report.
10. Conclusion: Towards a Sustainable Built Environment
The traditional demolition-centric approach to end-of-life building management is unsustainable and incompatible with the principles of a circular economy. Deconstruction offers a viable and compelling alternative, promoting resource conservation, waste reduction, and the creation of green jobs. The transition from demolition to deconstruction requires a paradigm shift in thinking, viewing buildings as material banks rather than disposable assets.
While challenges remain, the benefits of deconstruction are undeniable. By embracing deconstruction practices, we can create a more sustainable built environment, conserve natural resources, reduce greenhouse gas emissions, and foster a more equitable society. This requires a concerted effort involving policymakers, industry stakeholders, and community members, working together to create a supportive ecosystem for deconstruction.
The future of the construction industry lies in embracing circular economy principles and prioritizing sustainability. Deconstruction is a crucial component of this vision, offering a path towards a more resource-efficient and environmentally responsible built environment. By investing in research, developing supportive policies, and promoting collaboration, we can unlock the full potential of deconstruction and create a more sustainable future for generations to come.
Many thanks to our sponsor Focus 360 Energy who helped us prepare this research report.
References
- Addis, B. (2006). Building: 3000 Years of Design, Engineering & Construction. Phaidon Press.
- Allenby, B. R. (2006). Industrial Ecology: Policy and Implementation. Prentice Hall.
- Bossink, B. A. (2012). Building Technology: Innovation and Integration. Routledge.
- CIRIA (Construction Industry Research and Information Association). (2017). Deconstruction and Materials Reuse: A Guide. CIRIA.
- Crowther, P. (2011). Deconstruction: A Designer’s Sourcebook. Gibbs Smith.
- Ghisellini, P., Cialani, C., & Ulgiati, S. (2016). A review on circular economy: Definitions, critical aspects, and example applications. Journal of Cleaner Production, 114, 11-24.
- Haas, R., & Degerth, C. (2011). Deconstruction: A Tool for Sustainable Building. Birkhäuser.
- Langerak, M. H., Princen, M. H., & Nijhuis, S. (2019). Circular urbanism: Towards a planning and design agenda for urban resource flows. Landscape and Urban Planning, 189, 325-334.
- Webster, K. (2017). The Circular Economy: A Wealth of Flows (2nd ed.). Ellen MacArthur Foundation Publishing.
So, deconstruction is like open-source hardware for buildings? Imagine the IKEA instructions… but in reverse. “Allen wrench not included, find it in the rubble.” Seriously though, standardizing materials would be a game changer.
That’s a great analogy! The open-source hardware comparison is spot on. Standardizing materials would definitely streamline deconstruction and make material reuse much easier. Imagine the efficiency gains if building components were designed for disassembly from the start! It would also create more value for the end of life value chain.
Editor: FocusNews.Uk
Thank you to our Sponsor Focus 360 Energy
The societal implications of deconstruction extend beyond environmental benefits. Creating green jobs and stimulating local economic growth through deconstruction projects offers significant opportunities for workforce development, especially in underserved communities.
Absolutely! The workforce development aspect is key. Deconstruction projects can be tailored to provide valuable skills training and employment opportunities within local communities. By prioritizing these initiatives, we can create a more inclusive and sustainable construction industry, benefitting both people and the planet. It creates great opportunities for entrepreneurs too!
Editor: FocusNews.Uk
Thank you to our Sponsor Focus 360 Energy