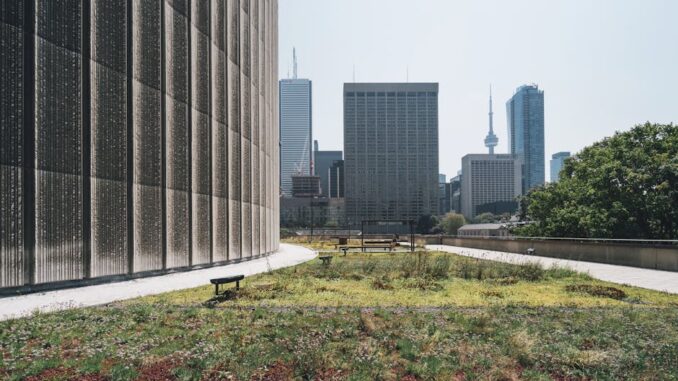
Abstract
Concrete, a ubiquitous construction material, plays a vital role in shaping the built environment globally. Its versatility, durability, and relative cost-effectiveness have cemented its position as the cornerstone of modern infrastructure. However, the environmental impact of concrete production, particularly the significant carbon dioxide (CO2) emissions associated with cement manufacturing, presents a major challenge to achieving sustainable development goals. This research report provides a comprehensive review of concrete, encompassing its historical evolution, advancements in concrete technology, sustainability concerns, and potential mitigation strategies. The report examines the environmental footprint of concrete production, including resource extraction, energy consumption, and CO2 emissions. It further explores the advancements in developing low-carbon concrete alternatives, such as supplementary cementitious materials (SCMs), carbon capture and utilization (CCU) technologies, and innovative cement chemistries. The potential of self-healing concrete and other advanced materials to extend the lifespan of concrete structures and reduce the demand for new construction is also analyzed. Finally, the report discusses the future directions of concrete research and development, emphasizing the need for collaborative efforts among researchers, industry professionals, and policymakers to promote the sustainable use of concrete in the construction industry.
Many thanks to our sponsor Focus 360 Energy who helped us prepare this research report.
1. Introduction
Concrete is arguably the most widely used man-made material in the world. Its history stretches back millennia, with early forms of concrete utilized by ancient civilizations, including the Romans, who famously employed it to construct enduring structures such as the Pantheon and aqueducts [1]. However, modern concrete, based on Portland cement, emerged in the 19th century and has since revolutionized the construction industry. Portland cement, the key ingredient in concrete, is produced by heating limestone and clay at high temperatures, a process that releases significant amounts of CO2 into the atmosphere [2].
The Mineral Products Association (MPA) actively promotes concrete as a valuable and readily available building material. Their advocacy highlights concrete’s durability, adaptability, and contribution to local economies. While the MPA’s perspective is important, a broader examination of concrete must address its environmental impact [3]. This report offers a comprehensive overview of concrete, moving beyond simple advocacy to explore its strengths, weaknesses, and the ongoing research focused on mitigating its environmental footprint. This involves examining advancements in concrete technology, lifecycle assessments, and the material’s role in sustainable construction, including strategies to reduce CO2 emissions and promote resource efficiency.
The scope of this report includes:
- A historical overview of concrete development.
- An analysis of the environmental impact of concrete production, focusing on CO2 emissions and resource depletion.
- A review of advancements in concrete technology, including low-carbon concrete, self-healing concrete, and innovative construction techniques.
- An examination of mitigation strategies for reducing the environmental footprint of concrete, such as carbon capture technologies and the use of alternative cementitious materials.
- A discussion of the lifecycle assessment of concrete structures.
- An outlook on the future directions of concrete research and development.
Many thanks to our sponsor Focus 360 Energy who helped us prepare this research report.
2. Environmental Impact of Concrete Production
The environmental impact of concrete production is primarily associated with the manufacture of Portland cement. The cement industry is a major contributor to global CO2 emissions, accounting for approximately 8% of the total anthropogenic CO2 emissions [4]. The CO2 emissions arise from two primary sources:
- Calcination: The chemical reaction in which limestone (calcium carbonate, CaCO3) is heated to produce lime (calcium oxide, CaO) and CO2. This process accounts for approximately 50-60% of the total CO2 emissions from cement production [5].
- Combustion: The burning of fossil fuels to provide the high temperatures required for the clinkering process (approximately 1450°C). This accounts for the remaining 40-50% of CO2 emissions [5].
In addition to CO2 emissions, concrete production also contributes to other environmental concerns:
- Resource Depletion: The extraction of raw materials, such as limestone, clay, and aggregates (sand and gravel), can lead to habitat destruction and land degradation [6].
- Energy Consumption: The production of cement requires significant amounts of energy, primarily in the form of fossil fuels [7].
- Air Pollution: The cement manufacturing process releases other pollutants into the air, including particulate matter, sulfur dioxide, and nitrogen oxides [8].
- Water Consumption: Water is used extensively in concrete production, from cement manufacturing to mixing and curing [9].
The impact on biodiversity can also be substantial. Quarrying operations, crucial for obtaining aggregates, often disrupt ecosystems and lead to habitat loss. Furthermore, the transportation of raw materials and finished concrete contributes to greenhouse gas emissions and air pollution. The lifecycle assessment of concrete structures must consider these factors to accurately evaluate their overall environmental burden. While concrete structures are durable and long-lasting, the initial environmental impact associated with their construction must be weighed against their service life and the potential for end-of-life recycling.
Many thanks to our sponsor Focus 360 Energy who helped us prepare this research report.
3. Advancements in Concrete Technology
Significant research and development efforts are underway to address the environmental challenges associated with concrete production. These efforts focus on developing innovative materials, processes, and construction techniques aimed at reducing CO2 emissions, conserving resources, and enhancing the durability of concrete structures.
3.1 Low-Carbon Concrete
Low-carbon concrete refers to concrete mixtures that significantly reduce the CO2 emissions associated with cement production. Several approaches are being explored to achieve this goal:
- Supplementary Cementitious Materials (SCMs): SCMs are materials that can partially replace Portland cement in concrete mixtures. These materials, often industrial byproducts, possess cementitious properties and can contribute to the strength and durability of concrete. Common SCMs include:
- Fly Ash: A byproduct of coal-fired power plants [10].
- Slag: A byproduct of steel manufacturing [11].
- Silica Fume: A byproduct of silicon and ferrosilicon alloy production [12].
- Metakaolin: A calcined clay with pozzolanic properties [13].
The use of SCMs not only reduces the demand for Portland cement but also valorizes industrial waste streams, promoting a circular economy. The replacement levels can vary depending on the type of SCM and the desired properties of the concrete, but significant reductions in CO2 emissions are achievable.
- Alternative Cementitious Materials: Researchers are investigating alternative cement chemistries that require less energy to produce and/or generate lower CO2 emissions. Examples include:
- Calcium Sulfoaluminate (CSA) Cement: CSA cements require lower clinkering temperatures than Portland cement and can incorporate industrial wastes [14].
- Magnesia-Based Cements: These cements can absorb CO2 during hydration, potentially leading to carbon-negative concrete [15]. However, the long-term performance and durability of magnesia-based cements are still under investigation.
- Geopolymers: Geopolymers are aluminosilicate materials that are activated by alkaline solutions. They can be produced from industrial byproducts, such as fly ash and slag, and offer a potentially low-carbon alternative to Portland cement [16].
- Carbon Capture and Utilization (CCU) Technologies: CCU technologies involve capturing CO2 emissions from cement plants and utilizing them to produce valuable products, such as chemicals, fuels, or building materials [17]. This approach can significantly reduce the net CO2 emissions from cement production. One promising application involves using captured CO2 to cure concrete, which enhances its strength and durability while sequestering the CO2 [18]. However, the economic viability and scalability of CCU technologies remain a challenge.
3.2 Self-Healing Concrete
Self-healing concrete is an innovative material that can autonomously repair cracks and other damage, extending the lifespan of concrete structures and reducing the need for costly repairs and replacements. Several approaches are being explored to develop self-healing concrete:
- Bacterial Concrete: This involves incorporating bacteria, typically Bacillus species, into the concrete mixture. These bacteria, when exposed to water and nutrients (e.g., calcium lactate), can precipitate calcium carbonate, which fills in cracks and seals them [19].
- Encapsulated Healing Agents: This approach involves encapsulating healing agents, such as polymers or epoxy resins, in microcapsules that are dispersed throughout the concrete. When a crack forms, the microcapsules rupture, releasing the healing agent, which then polymerizes and seals the crack [20].
- Mineral Admixtures: Some mineral admixtures, such as crystalline admixtures, can react with water and calcium hydroxide to form insoluble crystals that fill in cracks [21].
Self-healing concrete has the potential to significantly improve the durability and sustainability of concrete structures, reducing the need for maintenance and extending their service life. However, the cost and long-term performance of self-healing concrete need further investigation.
3.3 Advanced Concrete Materials
Beyond low-carbon and self-healing concrete, other advanced concrete materials are being developed to enhance the performance and durability of concrete structures:
- Fiber-Reinforced Concrete: This involves incorporating fibers, such as steel, glass, or synthetic fibers, into the concrete mixture to improve its tensile strength, ductility, and resistance to cracking [22]. Fiber-reinforced concrete is particularly useful in applications where concrete is subjected to high tensile stresses, such as pavements, bridges, and earthquake-resistant structures.
- High-Performance Concrete (HPC): HPC is characterized by its high strength, durability, and resistance to chemical attack. HPC is typically produced using carefully selected materials, optimized mix designs, and advanced mixing techniques [23]. HPC is often used in demanding applications, such as high-rise buildings, bridges, and marine structures.
- Ultra-High-Performance Concrete (UHPC): UHPC is a relatively new class of concrete that exhibits exceptionally high strength, durability, and ductility. UHPC typically contains a very high cement content, a low water-to-cement ratio, and a high volume of steel fibers [24]. UHPC is used in specialized applications, such as bridge decks, precast elements, and security structures.
Many thanks to our sponsor Focus 360 Energy who helped us prepare this research report.
4. Mitigation Strategies for Reducing the Environmental Footprint of Concrete
Reducing the environmental footprint of concrete requires a multifaceted approach that encompasses material selection, production processes, construction techniques, and end-of-life management.
4.1 Optimizing Cement Production Processes
- Improving Energy Efficiency: Cement plants can improve their energy efficiency by implementing energy-saving technologies, such as waste heat recovery systems, preheating and precalcining technologies, and more efficient clinker coolers [25].
- Switching to Alternative Fuels: Replacing fossil fuels with alternative fuels, such as biomass, waste-derived fuels, and natural gas, can significantly reduce CO2 emissions from cement production [26].
- Implementing Carbon Capture Technologies: Carbon capture technologies can be implemented at cement plants to capture CO2 emissions from the flue gas. The captured CO2 can then be stored underground (carbon sequestration) or used for other purposes (carbon utilization) [27].
4.2 Promoting the Use of Supplementary Cementitious Materials (SCMs)
Encouraging the use of SCMs in concrete mixtures is a crucial strategy for reducing the demand for Portland cement and valorizing industrial waste streams. This requires addressing barriers to SCM adoption, such as concerns about performance, availability, and consistency [28]. Standardizing SCM specifications and providing incentives for their use can help to overcome these barriers.
4.3 Developing and Implementing Performance-Based Specifications
Traditional prescriptive specifications for concrete often limit the use of innovative materials and techniques. Performance-based specifications, which focus on the desired performance of the concrete structure rather than the specific materials used, can encourage innovation and the adoption of more sustainable solutions [29].
4.4 Enhancing Concrete Recycling and Reuse
Concrete is a highly recyclable material, but the rate of concrete recycling is still relatively low in many regions. Encouraging the recycling of concrete rubble and using recycled aggregates in new concrete mixtures can significantly reduce the demand for virgin aggregates and minimize landfill waste [30]. However, the quality and consistency of recycled aggregates need to be carefully controlled to ensure the performance of the resulting concrete.
4.5 Promoting Sustainable Construction Practices
Sustainable construction practices, such as designing for durability, optimizing material use, and minimizing waste, can significantly reduce the environmental impact of concrete structures. Building Information Modeling (BIM) can be used to optimize concrete designs and minimize material waste [31]. Prefabrication and modular construction techniques can also reduce waste and improve construction efficiency.
Many thanks to our sponsor Focus 360 Energy who helped us prepare this research report.
5. Lifecycle Assessment (LCA) of Concrete Structures
Lifecycle Assessment (LCA) is a methodology for evaluating the environmental impacts of a product or system throughout its entire lifecycle, from raw material extraction to end-of-life disposal. LCA can be used to assess the environmental performance of concrete structures and identify opportunities for improvement [32].
An LCA of a concrete structure typically includes the following stages:
- Raw Material Extraction and Processing: This stage includes the extraction and processing of raw materials, such as limestone, clay, aggregates, and SCMs.
- Cement and Concrete Production: This stage includes the production of cement and the mixing of concrete.
- Construction: This stage includes the transportation of materials to the construction site and the construction of the concrete structure.
- Use and Maintenance: This stage includes the use of the concrete structure and any maintenance activities required during its service life.
- End-of-Life: This stage includes the demolition of the concrete structure and the disposal or recycling of the concrete rubble.
The environmental impacts assessed in an LCA typically include:
- Global Warming Potential (GWP): A measure of the contribution to climate change, expressed in terms of CO2 equivalents.
- Acidification Potential (AP): A measure of the contribution to acid rain, expressed in terms of SO2 equivalents.
- Eutrophication Potential (EP): A measure of the contribution to nutrient enrichment of water bodies, expressed in terms of phosphate equivalents.
- Resource Depletion: A measure of the depletion of natural resources, such as fossil fuels, minerals, and water.
LCA can be used to compare the environmental performance of different concrete mixtures, construction techniques, and end-of-life scenarios. The results of LCA can inform decision-making and help to promote the sustainable use of concrete.
Many thanks to our sponsor Focus 360 Energy who helped us prepare this research report.
6. Future Directions
The future of concrete research and development is focused on addressing the remaining challenges related to its environmental impact and improving its performance and durability. Key areas of focus include:
- Developing new and innovative cementitious materials: This includes exploring alternative cement chemistries, such as magnesium-based cements and geopolymers, and developing novel SCMs from waste materials [33].
- Improving carbon capture and utilization technologies: This includes developing more efficient and cost-effective carbon capture technologies and finding new and valuable applications for captured CO2 [34].
- Enhancing the durability and longevity of concrete structures: This includes developing self-healing concrete and other advanced materials that can extend the lifespan of concrete structures and reduce the need for maintenance and repair [35].
- Promoting the circular economy in the concrete industry: This includes increasing the rate of concrete recycling and developing new applications for recycled concrete aggregates [36].
- Developing new and innovative construction techniques: This includes exploring prefabrication, modular construction, and 3D printing of concrete to reduce waste and improve construction efficiency [37].
Addressing these challenges requires collaborative efforts among researchers, industry professionals, and policymakers. Governments can play a role by providing incentives for the adoption of sustainable concrete technologies and by establishing clear and consistent regulations. The concrete industry must also invest in research and development and actively promote the use of sustainable concrete practices. Ultimately, the sustainable use of concrete will require a fundamental shift in the way we design, build, and maintain concrete structures.
Many thanks to our sponsor Focus 360 Energy who helped us prepare this research report.
7. Conclusion
Concrete remains an indispensable material in the construction industry, providing essential infrastructure for modern society. However, the environmental impact of concrete production, particularly CO2 emissions, necessitates a concerted effort to develop and implement sustainable solutions. This report has reviewed the key challenges and opportunities in making concrete a more environmentally responsible material. Advancements in low-carbon concrete technologies, self-healing mechanisms, and alternative cementitious materials offer promising pathways to reduce the environmental footprint of concrete. Moreover, optimizing cement production processes, promoting the use of SCMs, and implementing performance-based specifications are crucial mitigation strategies. Lifecycle assessment provides a valuable framework for evaluating the environmental impacts of concrete structures and identifying areas for improvement. Future research and development efforts should focus on developing innovative materials, enhancing durability, and promoting a circular economy within the concrete industry. By embracing these advancements and mitigation strategies, the concrete industry can contribute to a more sustainable future.
Many thanks to our sponsor Focus 360 Energy who helped us prepare this research report.
References
[1] Heun, L. (2015). Roman Concrete and the Roman Architectural Revolution. Cambridge University Press.
[2] Andrew, R. M. (2018). Global CO2 emissions from cement production. Earth System Science Data, 10(1), 195-217.
[3] Mineral Products Association. (n.d.). Concrete. Retrieved from [Insert MPA Website Here – Replace with actual MPA website link].
[4] IEA (2018), Cement Technology Roadmap, IEA, Paris.
[5] Schneider, M., Romer, M., Tscheuschner, A., Piernikowski, B., & Shvarzman, A. (2011). Sustainable cement production—present and future. Cement and Concrete Research, 41(7), 642-666.
[6] Ali, M. B., Saidur, R., & Hossain, M. S. (2011). A review on emission analysis in cement industries. Renewable and Sustainable Energy Reviews, 15(5), 2378-2391.
[7] Worrell, E., Price, L., Boyd, N., & Galitsky, C. (2000). Energy efficiency improvement and cost saving opportunities for cement plants. Energy, 25(10), 929-952.
[8] van Oss, H. G. (2005). The mineral industry of cement. US Geological Survey.
[9] Gleick, P. H. (2003). Water use. Annual Review of Environment and Resources, 28(1), 585-633.
[10] Malhotra, V. M., & Ramezanianpour, A. A. (2005). Fly ash in concrete. CANMET/ACI.
[11] Siddique, R., & Khan, M. I. (2011). Supplementary cementitious materials. Springer Science & Business Media.
[12] Mehta, P. K., & Monteiro, P. J. M. (2014). Concrete: Microstructure, properties, and materials. McGraw-Hill Education.
[13] Sabir, B. B., Wild, S., & Bai, J. (2001). Metakaolin as a pozzolanic admixture for concrete: a review. Cement and Concrete Composites, 23(6), 441-454.
[14] Winnefeld, F., Lothenbach, B., & Bernhardt, G. (2010). Hydration behavior of calcium sulfoaluminate cements – A review. Cement and Concrete Research, 40(8), 1239-1247.
[15] Vlasopoulos, N., Marinos, V., & Panias, D. (2016). Magnesia-based binders for the construction sector: Recent advances and future perspectives. Construction and Building Materials, 123, 610-629.
[16] Davidovits, J. (2015). Geopolymer chemistry and applications. Institut Géopolymère.
[17] Hasanbeigi, A., Springer, C., Masanet, E., Morrow, W. R., & Price, L. (2012). Method for developing energy efficiency improvement scenarios: methodology and application to the US cement industry. Energy Efficiency, 5(4), 483-505.
[18] Monkman, S., Macdonald, A., Vandeperre, L. J., Cheeseman, C. R., & De Silva, P. S. (2016). Accelerated carbonation of concrete using flue gas. Cement and Concrete Composites, 67, 1-9.
[19] Jonkers, H. M. (2011). Bacteria-based self-healing concrete. Construction Materials, 164(4), 215-219.
[20] Joseph, C., & Jefferson, A. (2012). Self healing concrete—a review. Advances in cement research, 24(6), 321-328.
[21] Sisomphon, K., Copuroglu, O., & Fraaij, A. (2013). Effect of the exposure conditions on self-healing behavior of early-age cracked concrete. Cement and Concrete Research, 43, 73-80.
[22] Brandt, A. M. (2008). Cement-based composites: materials, mechanical properties and performance. CRC press.
[23] Aitcin, P. C. (1998). High-performance concrete. CRC press.
[24] Richard, P., & Cheyrezy, M. H. (1995). Composition of reactive powder concretes. Cement and Concrete Research, 25(7), 1501-1511.
[25] Madlool, N. A., Saidur, R., Hossain, M. S., & Rahim, N. A. (2011). A critical review on energy use and savings in the cement industries. Renewable and Sustainable Energy Reviews, 15(4), 2041-2060.
[26] Adeniran, J. A., Mokhena, T. C., John, O. O., & Omoniyi, A. I. (2021). A review of alternative fuels for cement production. Clean Technologies and Environmental Policy, 23(3), 767-790.
[27] Gerlagh, R., Van Der Zwaan, B., & Lako, P. (2007). A sensitivity analysis of investment in carbon capture and storage. Energy Policy, 35(10), 5209-5219.
[28] Thomas, M. D. A. (2007). Optimizing the use of fly ash in concrete. Portland Cement Association.
[29] Schindler, A. K., & Folliard, K. J. (2005). Influence of supplementary cementitious materials on the heat of hydration and early-age properties of concrete. Portland Cement Association.
[30] Xiao, J., Li, W., Poon, C. S., Hui, D., & Falkner, F. (2005). Use of steel slag as cementitious material for sustainable construction. Journal of Cleaner Production, 13(12), 1197-1206.
[31] Eastman, C., Teicholz, P., Sacks, R., & Liston, K. (2018). BIM handbook: A guide to building information modeling for owners, managers, designers, engineers and contractors. John Wiley & Sons.
[32] Habert, G., Denarié, F., & Birgisdottir, H. (2020). Environmental impacts of concrete: The good, the bad, and the ugly. Building and Environment, 170, 106583.
[33] Pacheco-Torgal, F., Abdollahnejad, Z., Miralvės, R., Agarwal, S., Hassan, A., & Jalali, S. (2012). Eco-efficient construction and building materials. Springer Science & Business Media.
[34] Olajire, A. A. (2013). CO2 capture and separation technologies for end-of-pipe applications – a review. Energy, 53, 71-91.
[35] Van Tittelboom, K., & De Belie, N. (2013). Self-healing in concrete: a review. Materials, 6(6), 2182-2217.
[36] Tam, V. W. Y., Gao, X. F., & Tam, C. M. (2005). Recycling concrete waste as landfill cover. Waste Management, 25(9), 985-991.
[37] Khoshnevis, B. (2004). Automated construction by contour crafting—related robotics and information technologies. Automation in Construction, 13(1), 5-19.
So, we’re teaching concrete to heal itself now? Are tiny concrete therapists next? I picture them saying, “I hear you, crack, tell me more about your structural instability…” Seriously though, self-healing concrete could revolutionize infrastructure longevity!
That’s a hilarious and insightful take! The idea of concrete therapists is definitely amusing. You’re absolutely right; the potential for self-healing concrete to extend the life of our infrastructure is huge. What other innovations do you think could further enhance concrete’s sustainability?
Editor: FocusNews.Uk
Thank you to our Sponsor Focus 360 Energy
8% of anthropogenic CO2 emissions? So, theoretically, if we all just stopped building things, we could drop global emissions by nearly a tenth? Suddenly tempted to become a hermit, but where would my hobbit hole be built?
That’s a thought-provoking question! While ceasing all construction isn’t realistic, your comment highlights the significant impact our built environment has. Finding ways to build *better* – using sustainable materials and innovative designs – could significantly reduce that 8%. Perhaps your hobbit hole could be a prototype for eco-friendly dwellings!
Editor: FocusNews.Uk
Thank you to our Sponsor Focus 360 Energy
The discussion of alternative cement chemistries is particularly interesting. How do you see the scalability of technologies like magnesia-based cements becoming economically viable to compete with traditional Portland cement in the next decade?
That’s a great point! The economic viability of magnesia-based cements really hinges on a few factors. Widespread adoption will likely depend on successful pilot projects demonstrating long-term performance and the development of more efficient production methods to lower costs. Policy incentives could also accelerate their market entry.
Editor: FocusNews.Uk
Thank you to our Sponsor Focus 360 Energy
The report mentions exploring alternative cement chemistries like magnesia-based cements. Could you elaborate on the challenges associated with their long-term performance and durability, specifically regarding their resistance to various environmental conditions and potential for degradation over extended periods?
That’s a really important question! The long-term durability of magnesia-based cements is definitely a key area of research. Factors like exposure to chlorides and sulfates can affect their performance, and ongoing studies are essential to ensure their reliability in diverse environments. More research is always welcome!
Editor: FocusNews.Uk
Thank you to our Sponsor Focus 360 Energy
Self-healing concrete? So, if my driveway develops a crack, will it also send me a bill for its therapy sessions? Seriously, though, extending lifespan is brilliant, but what about the environmental cost of those encapsulated healing agents? Are we just shifting the problem elsewhere?
That’s a brilliant question! You’re right, we need to consider the full lifecycle impact. The environmental cost of the encapsulated healing agents is a key area of research. We are definitely aiming for solutions that don’t just move the problem elsewhere, but reduce the overall impact! What do you think are the most promising avenues for this?
Editor: FocusNews.Uk
Thank you to our Sponsor Focus 360 Energy
Self-healing concrete sounds fantastic, but what about the quarrying of all those raw materials? Is there a plan to get aggregates from, say, disused plastic? Or are we just digging ourselves into another hole?
That’s a great question! Exploring alternative aggregate sources like recycled plastics is definitely an area of interest. There are challenges around consistency and performance, but research is ongoing. The goal is to minimize the environmental impact at every stage, from material sourcing to end-of-life. Do you know of any successful examples of plastic aggregate use?
Editor: FocusNews.Uk
Thank you to our Sponsor Focus 360 Energy