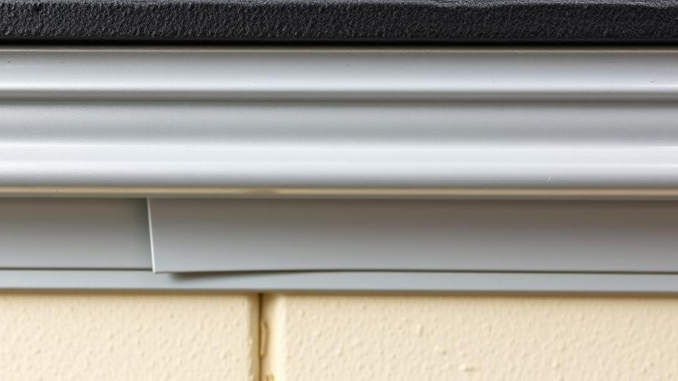
Abstract
The building envelope plays a crucial role in energy efficiency, indoor environmental quality, and structural durability. While static building components like walls and roofs have received substantial research attention, dynamic elements such as operable windows and doors present ongoing challenges for effective sealing. Weatherstripping, a traditional method for mitigating air leakage around these openings, has evolved considerably in materials, designs, and performance characteristics. This report provides a comprehensive overview of weatherstripping technologies, encompassing material science aspects, installation methodologies, performance evaluation metrics, and emerging innovations. We explore the limitations of conventional weatherstripping and delve into advanced sealing solutions, including intumescent seals, magnetic seals, and integrated systems, analyzing their potential to enhance the overall performance of dynamic building envelopes. The report also addresses the critical considerations of long-term durability, environmental impact, and cost-effectiveness in selecting and implementing sealing solutions, aiming to guide building professionals towards optimized strategies for minimizing air infiltration and promoting sustainable building practices.
Many thanks to our sponsor Focus 360 Energy who helped us prepare this research report.
1. Introduction
Buildings are complex systems designed to provide shelter, comfort, and functionality. The building envelope, comprising the exterior walls, roof, windows, and doors, serves as the primary barrier against external environmental conditions. Effective sealing of the building envelope is essential for maintaining indoor temperature and humidity, preventing air leakage, and minimizing energy consumption. Air leakage, or infiltration, occurs when uncontrolled airflow enters or exits the building through cracks, gaps, and openings in the envelope. This can lead to significant energy losses, discomfort for occupants, and potential moisture problems that can compromise building durability [1].
Weatherstripping, the focus of this report, is a traditional and widely used method for sealing gaps around operable windows and doors. It involves the application of flexible materials that conform to the irregular surfaces of these openings, creating a barrier against air leakage. While weatherstripping has proven effective in many applications, its performance can vary depending on the type of material, installation quality, and environmental conditions. This report aims to provide a detailed analysis of weatherstripping technologies, evaluating their strengths and limitations, and exploring alternative sealing solutions for dynamic building envelopes.
Many thanks to our sponsor Focus 360 Energy who helped us prepare this research report.
2. Weatherstripping Materials and Properties
A wide range of materials are used in the manufacturing of weatherstripping, each with unique properties that influence its performance, durability, and cost-effectiveness. The choice of material depends on several factors, including the size and shape of the gap to be sealed, the expected frequency of operation of the window or door, and the environmental conditions to which the weatherstripping will be exposed.
2.1. Foam Weatherstripping
Foam weatherstripping is a common and relatively inexpensive option. It is typically made from closed-cell or open-cell foam polymers, often with an adhesive backing for easy installation. Closed-cell foam offers better resistance to water absorption and compression set compared to open-cell foam [2]. However, foam weatherstripping is generally less durable than other materials and can degrade over time due to exposure to sunlight, moisture, and mechanical wear. Its primary advantage is its compressibility, allowing it to conform to uneven surfaces. Foam products also tend to exhibit higher rates of air leakage, especially after compression, and are best suited for use in areas with minimal temperature or humidity variations.
2.2. Felt Weatherstripping
Felt weatherstripping consists of strips of compressed wool or synthetic fibers. It is a relatively inexpensive option and is easy to install. However, felt is susceptible to moisture absorption and can degrade quickly, especially in humid environments. It is also less effective at sealing larger gaps compared to other materials. Felt weatherstripping is generally suitable for light-duty applications where air leakage is not a major concern. Its longevity is limited, typically requiring replacement every few years.
2.3. Rubber Weatherstripping
Rubber weatherstripping offers superior durability and performance compared to foam and felt. It is typically made from materials such as EPDM (ethylene propylene diene monomer) rubber, silicone rubber, or neoprene rubber. EPDM rubber is known for its excellent resistance to weathering, ozone, and UV radiation [3]. Silicone rubber offers exceptional flexibility and temperature resistance, making it suitable for use in extreme climates. Neoprene rubber provides good resistance to oil and chemicals. Rubber weatherstripping is more expensive than foam or felt but offers a longer lifespan and better sealing performance. Rubber weatherstripping is commonly available in a variety of profiles, including D-shaped, P-shaped, and bulb-shaped, to accommodate different gap sizes and shapes.
2.4. Vinyl Weatherstripping
Vinyl weatherstripping is a durable and cost-effective option. It is resistant to weathering, moisture, and insects. Vinyl weatherstripping is typically available in rigid or flexible profiles. Rigid vinyl weatherstripping is often used in combination with foam or rubber to provide a more robust seal. Flexible vinyl weatherstripping can conform to irregular surfaces and is suitable for use in a variety of applications. However, vinyl can become brittle over time, particularly in cold climates, which can lead to cracking and reduced sealing performance.
2.5. Metal Weatherstripping
Metal weatherstripping, typically made from bronze, aluminum, or stainless steel, offers exceptional durability and longevity. It is more expensive than other materials but can provide a long-lasting seal. Metal weatherstripping is resistant to weathering, moisture, and insects. It is often used in historic buildings where preserving the original aesthetic is important. Metal weatherstripping requires specialized installation techniques and may not be suitable for all applications.
Many thanks to our sponsor Focus 360 Energy who helped us prepare this research report.
3. Installation Techniques and Best Practices
Proper installation is critical for maximizing the performance of weatherstripping. Even the highest quality materials will fail to provide an effective seal if not installed correctly. Key considerations include surface preparation, material selection, and installation technique.
3.1. Surface Preparation
Before installing weatherstripping, the surfaces to which it will be applied must be clean, dry, and free of debris. Any old weatherstripping, paint, or dirt should be removed. The surface should be inspected for any cracks or imperfections that could compromise the seal. Repairing or filling any gaps or cracks before installing weatherstripping will improve its effectiveness [4].
3.2. Material Selection
The selection of the appropriate weatherstripping material depends on the size and shape of the gap to be sealed, the expected frequency of operation of the window or door, and the environmental conditions to which the weatherstripping will be exposed. For small gaps, foam or felt weatherstripping may be sufficient. For larger gaps, rubber or vinyl weatherstripping is recommended. In areas with extreme temperature variations, silicone rubber weatherstripping is a good choice. Metal weatherstripping is suitable for historic buildings or applications where durability and longevity are paramount.
3.3. Installation Techniques
Different types of weatherstripping require different installation techniques. Adhesive-backed weatherstripping is relatively easy to install, but it is important to ensure that the adhesive is properly applied and that the weatherstripping is firmly pressed against the surface. Nail-on or screw-on weatherstripping requires more skill and precision. It is important to use the correct size nails or screws and to avoid over-tightening them, which could damage the weatherstripping or the surrounding material. Interlocking weatherstripping requires precise alignment and may require specialized tools. The instructions provided by the manufacturer should be followed carefully to ensure proper installation.
3.4. Best Practices
- Accurate Measurement: Measure the gaps around the window or door carefully to ensure that the weatherstripping is the correct size.
- Proper Alignment: Align the weatherstripping properly to ensure a tight seal.
- Secure Attachment: Attach the weatherstripping securely to prevent it from coming loose over time.
- Compression Adjustment: Adjust the compression of the weatherstripping to ensure a proper seal without impeding the operation of the window or door.
- Regular Inspection: Inspect the weatherstripping regularly for signs of wear or damage and replace it as needed.
Many thanks to our sponsor Focus 360 Energy who helped us prepare this research report.
4. Performance Evaluation Metrics
The performance of weatherstripping can be evaluated based on several metrics, including air leakage reduction, durability, and cost-effectiveness. Quantifying the effectiveness of different weatherstripping strategies is crucial for making informed decisions about building envelope design and retrofitting.
4.1. Air Leakage Reduction
The primary function of weatherstripping is to reduce air leakage. Air leakage rates can be measured using various methods, including blower door tests and tracer gas techniques [5]. Blower door tests involve pressurizing or depressurizing the building and measuring the airflow required to maintain a constant pressure difference. Tracer gas techniques involve introducing a tracer gas into the building and measuring its concentration over time to determine the air exchange rate. The effectiveness of weatherstripping in reducing air leakage can be quantified by comparing air leakage rates before and after installation. Air leakage is usually expressed in cubic feet per minute (CFM) at a pressure differential of 50 Pascals (CFM50).
4.2. Durability
Durability is an important consideration when selecting weatherstripping. The lifespan of weatherstripping can vary depending on the material, installation quality, and environmental conditions. Accelerated aging tests can be used to simulate the effects of weathering and mechanical wear on weatherstripping materials. These tests involve exposing the weatherstripping to elevated temperatures, humidity, UV radiation, and mechanical stress. The performance of the weatherstripping is then evaluated based on changes in its physical properties, such as flexibility, compression set, and air leakage resistance.
4.3. Cost-Effectiveness
The cost-effectiveness of weatherstripping depends on the initial cost of the materials and installation, as well as the long-term energy savings achieved. A life-cycle cost analysis can be used to evaluate the cost-effectiveness of different weatherstripping options. This analysis takes into account the initial cost, the expected lifespan, the energy savings, and the maintenance costs associated with each option. The results of the life-cycle cost analysis can be used to determine the most cost-effective weatherstripping solution for a particular application. Tools such as the Department of Energy’s BEopt (Building Energy Optimization) can assist in these calculations [6].
Many thanks to our sponsor Focus 360 Energy who helped us prepare this research report.
5. Limitations of Conventional Weatherstripping
While conventional weatherstripping has proven effective in reducing air leakage, it has several limitations that can affect its performance and longevity.
5.1. Degradation over Time
Most weatherstripping materials degrade over time due to exposure to sunlight, moisture, and mechanical wear. This degradation can lead to reduced sealing performance and increased air leakage. Frequent replacement of weatherstripping is often necessary to maintain optimal performance. Materials such as foam and felt exhibit especially quick degradation.
5.2. Compression Set
Some weatherstripping materials, such as foam, can develop a compression set over time. This means that the material loses its ability to return to its original shape after being compressed. Compression set can reduce the effectiveness of the weatherstripping in sealing gaps.
5.3. Inconsistent Performance
The performance of weatherstripping can vary depending on the size and shape of the gap to be sealed. Weatherstripping may not be effective in sealing large or irregular gaps. Careful measurement and selection of the appropriate weatherstripping material are essential for achieving consistent performance.
5.4. Installation Challenges
Proper installation of weatherstripping can be challenging, especially for inexperienced installers. Incorrect installation can lead to reduced sealing performance and premature failure of the weatherstripping. It is important to follow the manufacturer’s instructions carefully and to use the appropriate tools and techniques.
Many thanks to our sponsor Focus 360 Energy who helped us prepare this research report.
6. Advanced Sealing Solutions
To overcome the limitations of conventional weatherstripping, researchers and manufacturers have developed advanced sealing solutions that offer improved performance, durability, and ease of installation.
6.1. Intumescent Seals
Intumescent seals are designed to expand when exposed to heat, creating a fire-resistant barrier. They are often used in fire-rated doors and windows to prevent the spread of fire and smoke. Intumescent seals can also provide effective air and water sealing. These materials typically incorporate graphite or other expandable compounds that swell when heated, filling gaps and preventing passage of flames [7].
6.2. Magnetic Seals
Magnetic seals consist of a flexible magnetic strip that is attached to the window or door frame and a corresponding metal strip that is attached to the window or door. The magnetic attraction between the two strips creates a tight seal. Magnetic seals offer excellent sealing performance and are easy to install. These are commonly found on refrigerator doors, and are now being applied to building envelopes.
6.3. Integrated Sealing Systems
Integrated sealing systems are designed to be incorporated into the window or door during the manufacturing process. These systems typically consist of a combination of weatherstripping materials and interlocking components that provide a tight and durable seal. Integrated sealing systems offer superior performance and are less susceptible to installation errors. For example, some window manufacturers now embed the weatherstripping within the window frame extrusion itself, creating a more robust and long-lasting seal. This reduces the impact of installer error and material degradation over time.
6.4. Compression Seals with Optimized Geometry
Beyond simple flat strips, advanced compression seals now incorporate complex geometries designed to maximize sealing performance. These may include multiple ribs, internal air chambers, or interlocking features that enhance compression and maintain a tight seal even under varying pressure conditions. Finite element analysis (FEA) is often used to optimize the shape and material properties of these seals for specific applications [8].
Many thanks to our sponsor Focus 360 Energy who helped us prepare this research report.
7. Environmental Impact and Sustainability
The environmental impact of weatherstripping should be considered when selecting materials and installation methods. Choosing sustainable materials and minimizing waste can help reduce the environmental footprint of building projects.
7.1. Material Selection
Selecting weatherstripping materials made from recycled content or renewable resources can reduce the environmental impact of building projects. For example, weatherstripping made from recycled rubber or bio-based polymers is a more sustainable option than weatherstripping made from virgin petroleum-based materials. The embodied energy of the material, including extraction, manufacturing, and transportation, should also be considered [9].
7.2. Waste Reduction
Minimizing waste during installation can also reduce the environmental impact of weatherstripping projects. Proper measurement and cutting techniques can help avoid unnecessary waste. Recycling old weatherstripping materials can also help reduce landfill waste. Programs like the U.S. Green Building Council’s LEED (Leadership in Energy and Environmental Design) rating system incentivize the use of recycled content and waste reduction strategies.
7.3. Life-Cycle Assessment
A life-cycle assessment (LCA) can be used to evaluate the environmental impact of weatherstripping over its entire lifespan, from material extraction to disposal. LCA takes into account the energy consumption, water usage, and greenhouse gas emissions associated with each stage of the product’s life cycle. The results of the LCA can be used to identify opportunities for reducing the environmental impact of weatherstripping.
Many thanks to our sponsor Focus 360 Energy who helped us prepare this research report.
8. Conclusion
Weatherstripping is an important component of the building envelope, playing a crucial role in reducing air leakage and improving energy efficiency. While conventional weatherstripping has limitations, advanced sealing solutions offer improved performance, durability, and ease of installation. Selecting appropriate materials, using proper installation techniques, and considering the environmental impact can help ensure that weatherstripping provides a long-lasting and effective seal. Future research should focus on developing more sustainable and durable weatherstripping materials, optimizing installation techniques, and integrating advanced sealing systems into building components. The shift towards increasingly airtight building envelopes, driven by stricter energy codes and sustainability initiatives, necessitates continuous innovation in sealing technologies to ensure optimal building performance and occupant comfort.
Many thanks to our sponsor Focus 360 Energy who helped us prepare this research report.
References
[1] Straube, J. F. (2009). High-Performance Enclosures. Building Science Press.
[2] TenWolde, A., & Rose, W. B. (1995). Air Leakage Performance of Exterior Envelopes of Buildings. ASHRAE.
[3] Blowers, R. (2000). Rubber Technology. Butterworth-Heinemann.
[4] Lstiburek, J. (2008). Builder’s Guide to Cold Climates. Taunton Press.
[5] Sherman, M. H. (1990). Air Infiltration Measurements for Residential Buildings. Lawrence Berkeley National Laboratory.
[6] National Renewable Energy Laboratory (NREL). BEopt: Building Energy Optimization. https://www.nrel.gov/
[7] Drysdale, D. (2011). An Introduction to Fire Dynamics. John Wiley & Sons.
[8] Cook, R. D., Malkus, D. S., Plesha, M. E., & Witt, R. J. (2002). Concepts and Applications of Finite Element Analysis. John Wiley & Sons.
[9] Allenby, B. R. (2006). Industrial Ecology: Policy and Implementation. Prentice Hall.
Fascinating report! Who knew weatherstripping could be so complex? Makes you wonder if all those drafts in your house are just a sign you need to upgrade to magnetic seals, or if it’s just ghosts being dramatic again.
Thanks for your comment! Magnetic seals are definitely worth considering for drafty homes. They’re quite effective, and as we discussed in the report, are becoming more common in residential applications. Have you considered trying them out yourself, and if so, what factors are influencing your decision?
Editor: FocusNews.Uk
Thank you to our Sponsor Focus 360 Energy
So, metal weatherstripping is exceptional, eh? Does that mean I should finally embrace the steampunk aesthetic for my house? Seems like a *durable* choice, but what about the noise when the wind really howls?
Metal weatherstripping definitely offers great durability! Regarding wind noise, that’s a valid concern. The installation method and the specific profile of the metal strip can significantly impact noise reduction. Consider consulting with a specialist to ensure proper fitting and potentially explore noise-dampening materials alongside the metal for optimal results!
Editor: FocusNews.Uk
Thank you to our Sponsor Focus 360 Energy
The report mentions integrated sealing systems embedded during manufacturing. Could wider adoption of these systems, perhaps incentivized through building codes, significantly reduce reliance on traditional, less durable weatherstripping methods over the long term?
That’s a great point! Integrated systems definitely hold long-term promise. Building codes could play a significant role in driving adoption and ensuring consistent performance. Perhaps a tiered approach within the codes, rewarding higher performing integrated systems? What are your thoughts on potential barriers to widespread implementation?
Editor: FocusNews.Uk
Thank you to our Sponsor Focus 360 Energy