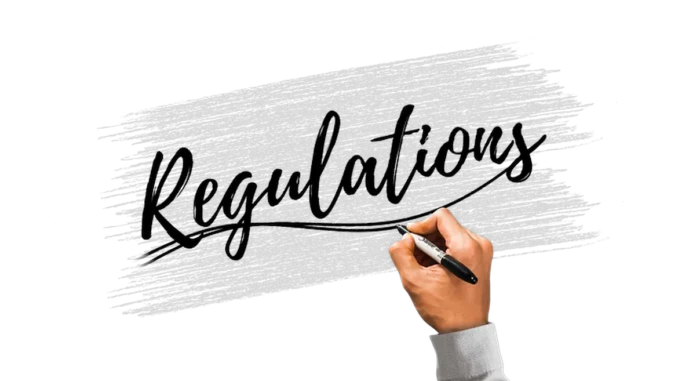
In the realm of construction and renovation, adherence to building regulations is paramount, with floor insulation occupying a critical role. Floor insulation not only impacts energy efficiency but also influences heating and cooling costs, while significantly contributing to the comfort of building occupants. For builders, architects, and homeowners, a thorough understanding of the regulations surrounding floor insulation is indispensable. This article examines the nuances of these regulations, shedding light on essential considerations and key aspects.
Focus360 Energy: property compliance services – pre-planning to post-construction. Learn more.
Floor insulation plays a vital role within the building envelope, directly affecting a structure’s energy efficiency. When installed correctly, it serves to reduce heat loss during colder seasons and minimise heat gain when temperatures rise, thereby lowering energy consumption. This dual function results in notable cost savings and a diminished carbon footprint. Central to the discourse on floor insulation is the understanding of U-values, which measure the rate of heat transfer through building elements. A lower U-value signifies superior insulation performance by indicating reduced heat transfer. Consequently, building regulations mandate specific maximum U-values for floors to ensure optimal thermal performance.
The regulatory framework for floor insulation is delineated in both national and local building codes. In the United Kingdom, for instance, the pertinent regulations are outlined in Approved Document L: Conservation of Fuel and Power. This document establishes the energy performance standards for both new and existing buildings. Different sections of the document, such as Approved Document L1A and L1B, detail the requirements for new and existing dwellings, respectively. It is noteworthy that while the overarching principles are consistent across regions such as Wales, Scotland, and Northern Ireland, there are slight variations to accommodate regional climatic conditions. These codes provide comprehensive guidelines regarding insulation materials, installation practices, and U-value benchmarks.
Achieving compliance with insulation standards necessitates meeting specific U-value targets, which vary depending on factors such as building type, geographical location, and climate zone. For example, buildings situated in colder regions may require lower U-values to guarantee sufficient insulation, whereas warmer areas may have more lenient thresholds. To adhere to these standards, builders and architects must judiciously select appropriate insulation materials and installation methods. Common materials employed in floor insulation include rigid foam boards, fibreglass batts, and mineral wool, each possessing unique thermal properties suitable for different applications. Proper installation is imperative to ensure that the insulation performs as intended and aligns with regulatory standards.
As building codes evolve, innovative practices and materials have emerged, enabling builders to meet or even surpass insulation requirements. Fibreglass and mineral wool, for example, offer cost-effective solutions with excellent thermal performance, available in various forms such as batts, rolls, and loose-fill. Additionally, the technique of embedding ductwork within ceiling insulation is gaining traction. This approach can lower energy code compliance costs by reducing the necessity for high-capacity HVAC systems and limiting air leakage, ultimately leading to substantial energy savings and enhanced building performance.
The importance of proper installation of floor insulation cannot be overstated. Adhering to Grade I installation standards, which represent the pinnacle of workmanship, is increasingly becoming a requirement in state energy codes. Failure to meet these standards can result in construction delays, failed inspections, and heightened energy costs. To facilitate proper installation, builders and contractors should adhere to manufacturer guidelines and best practices. Training programmes and resources, like those provided by organisations such as NAIMA, offer invaluable insights into achieving Grade I installation standards.
In summary, a comprehensive understanding and compliance with building regulations for floor insulation are crucial for the creation of energy-efficient, comfortable, and sustainable buildings. By comprehending the significance of U-values, selecting suitable insulation materials, and following top-tier installation practices, builders and homeowners can ensure compliance while reaping the benefits of reduced energy consumption and enhanced thermal comfort. As building codes continue to evolve, staying abreast of innovative practices and materials will be essential in meeting forthcoming insulation requirements and contributing positively to a greener built environment.
Be the first to comment