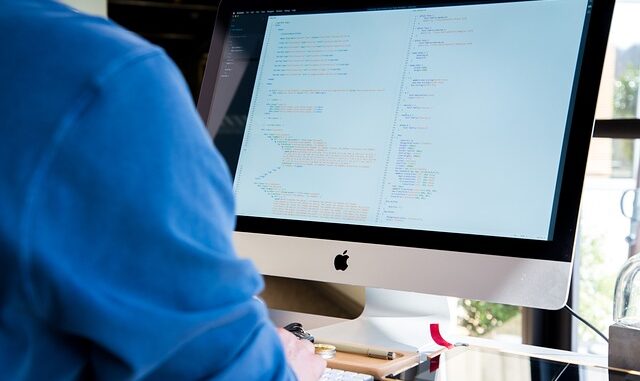
Abstract
The traditional blueprint, while foundational, represents only a fraction of the complex information ecosystem necessary for the successful execution of modern construction projects. This report delves into the broader landscape of information management systems (IMS) employed throughout the project lifecycle, from conception and design to construction, commissioning, and long-term maintenance. It critically analyzes the limitations of blueprint-centric approaches, exploring the evolution towards integrated digital platforms and the challenges and opportunities they present. Furthermore, it examines the critical role of semantic interoperability, data governance, and collaborative workflows in ensuring information accuracy, accessibility, and actionable insights. Finally, it proposes future research directions, focusing on the integration of artificial intelligence (AI) and machine learning (ML) techniques to optimize information flow and decision-making within complex construction environments.
Many thanks to our sponsor Focus 360 Energy who helped us prepare this research report.
1. Introduction: The Blueprint and Beyond
The blueprint, historically, served as the primary conduit for communicating design intent and construction specifications. Its mastery, as the starting point suggests, remains fundamental. However, relying solely on blueprints in contemporary large-scale projects introduces significant limitations. The sheer volume of information required – encompassing architectural, structural, mechanical, electrical, plumbing (MEP), and increasingly sophisticated building systems – overwhelms the capacity of traditional two-dimensional representations. The complexity is further compounded by the need for coordination across multiple disciplines, subcontractors, and stakeholders, each generating and consuming vast amounts of data. The blueprint, in isolation, lacks the dynamic capabilities necessary to manage this information deluge effectively.
The limitations of the blueprint-centric approach include:
- Information Siloing: Blueprints are typically discipline-specific, hindering holistic project understanding and cross-disciplinary collaboration.
- Static Nature: Blueprints represent a snapshot in time, failing to capture the iterative design process, change orders, and as-built modifications effectively. The cost of reprinting and distributing revised blueprints can be significant, and errors are common.
- Lack of Interactivity: Blueprints offer limited interactive capabilities, making it difficult to query specific details or perform advanced analysis.
- Coordination Challenges: Overlapping or conflicting information across multiple blueprints can lead to errors, rework, and project delays.
To overcome these limitations, the construction industry has witnessed a gradual shift towards integrated information management systems (IMS). These systems encompass a wide range of digital tools and platforms, aiming to centralize, organize, and distribute project information effectively. This report will explore the key components of these IMS, their benefits, and the challenges associated with their implementation.
Many thanks to our sponsor Focus 360 Energy who helped us prepare this research report.
2. Evolution of Information Management in Construction
The evolution of information management in construction can be broadly categorized into distinct phases:
- Pre-Digital Era: Characterized by manual processes, paper-based blueprints, and limited communication tools. Information was often fragmented and difficult to access.
- Early Digital Adoption: Introduction of computer-aided design (CAD) software for creating and managing digital drawings. While CAD improved drafting efficiency, it often perpetuated information silos, as drawings remained largely isolated.
- Building Information Modeling (BIM) Era: BIM represents a significant paradigm shift, moving beyond two-dimensional drawings to create intelligent 3D models that incorporate comprehensive project information. BIM facilitates collaboration, clash detection, and improved decision-making.
- Integrated Digital Platforms: The current phase involves the integration of BIM with other digital tools and platforms, such as project management software, enterprise resource planning (ERP) systems, and cloud-based collaboration platforms. This integration aims to create a unified information ecosystem that supports all phases of the project lifecycle.
BIM, in particular, has been instrumental in transforming information management practices. A BIM model serves as a central repository for geometric data, material specifications, cost estimates, and scheduling information. It enables stakeholders to visualize the project in 3D, identify potential conflicts early on, and make informed decisions based on accurate and up-to-date information. While BIM is often associated with the design phase, its value extends throughout the entire project lifecycle, from construction to facility management.
However, the successful implementation of BIM requires more than just adopting the software. It necessitates a fundamental shift in organizational culture, workflows, and contractual relationships. Collaboration, information sharing, and standardization are crucial for realizing the full potential of BIM.
Many thanks to our sponsor Focus 360 Energy who helped us prepare this research report.
3. Components of Modern Information Management Systems
A modern IMS in construction comprises several interconnected components, each playing a critical role in managing and distributing project information. These components include:
- Building Information Modeling (BIM) Software: As discussed earlier, BIM software is the cornerstone of many modern IMS, providing a platform for creating, managing, and sharing intelligent 3D models.
- Project Management Software: Project management software helps to plan, schedule, and track project progress. It integrates with BIM to provide real-time visibility into project status and potential delays.
- Document Management Systems (DMS): DMS are used to store, organize, and manage all project-related documents, including contracts, specifications, permits, and as-built drawings. Cloud-based DMS facilitate access and collaboration from anywhere with an internet connection.
- Enterprise Resource Planning (ERP) Systems: ERP systems integrate various business functions, such as finance, accounting, procurement, and human resources. They provide a holistic view of the project and enable better resource allocation.
- Collaboration Platforms: Collaboration platforms facilitate communication and information sharing among project stakeholders. They typically include features such as instant messaging, video conferencing, and document sharing.
- Reality Capture Technologies: Technologies such as laser scanning and photogrammetry are used to capture existing site conditions and create accurate 3D models. This information can be used to verify construction progress and identify discrepancies between the design and the as-built conditions.
- Internet of Things (IoT) Devices: IoT devices, such as sensors and trackers, are increasingly being used to monitor construction equipment, materials, and environmental conditions. This data can be used to improve efficiency, safety, and quality control.
The effective integration of these components is crucial for creating a seamless information flow throughout the project lifecycle. Data should be easily accessible, consistent, and reliable, enabling stakeholders to make informed decisions based on a single source of truth.
Many thanks to our sponsor Focus 360 Energy who helped us prepare this research report.
4. Challenges and Opportunities in Implementing IMS
While the benefits of IMS are well-documented, their implementation presents several challenges:
- Interoperability Issues: A major challenge is the lack of interoperability between different software systems. Data formats and standards vary across different platforms, making it difficult to exchange information seamlessly. Semantic interoperability, where data meaning is preserved during exchange, remains a significant hurdle.
- Data Governance and Security: Effective data governance policies are essential to ensure data quality, accuracy, and consistency. Robust security measures are needed to protect sensitive project information from unauthorized access.
- Resistance to Change: Implementing new IMS often requires significant changes to existing workflows and organizational culture. Resistance to change from stakeholders can hinder adoption and reduce the effectiveness of the system.
- Cost and Complexity: Implementing and maintaining a comprehensive IMS can be expensive and complex. Organizations need to carefully evaluate the costs and benefits before investing in new technologies.
- Lack of Skilled Personnel: The successful implementation of IMS requires skilled personnel who are proficient in using the various software tools and platforms. There is a shortage of qualified professionals in the construction industry who possess the necessary skills.
Despite these challenges, the opportunities presented by IMS are significant:
- Improved Collaboration: IMS facilitate collaboration among project stakeholders by providing a centralized platform for communication and information sharing.
- Reduced Errors and Rework: By identifying potential conflicts and errors early on, IMS can significantly reduce rework and improve project quality.
- Enhanced Decision-Making: IMS provide stakeholders with access to accurate and up-to-date information, enabling them to make informed decisions.
- Increased Efficiency: IMS automate many manual processes, such as document management and reporting, freeing up resources and improving efficiency.
- Better Project Outcomes: By improving collaboration, reducing errors, and enhancing decision-making, IMS can lead to better project outcomes, including lower costs, faster schedules, and higher quality.
Overcoming the interoperability challenges requires a concerted effort from industry stakeholders, including software vendors, owners, and contractors. Developing and adopting open standards for data exchange is crucial for ensuring seamless information flow across different platforms. Furthermore, investing in training and education is essential for developing a skilled workforce capable of implementing and managing IMS effectively.
Many thanks to our sponsor Focus 360 Energy who helped us prepare this research report.
5. The Role of Semantic Interoperability and Data Governance
Semantic interoperability and data governance are critical aspects of successful IMS implementation. Semantic interoperability refers to the ability of different software systems to exchange information in a way that preserves its meaning. This requires the use of standardized data formats, ontologies, and semantic models. Without semantic interoperability, data exchange can be prone to errors and misinterpretations.
Data governance, on the other hand, encompasses the policies, processes, and standards that ensure data quality, accuracy, and consistency. Effective data governance policies should address issues such as data ownership, data security, data privacy, and data retention. It establishes clear roles and responsibilities for managing and maintaining project information.
Both semantic interoperability and data governance are essential for creating a trusted and reliable information environment. They enable stakeholders to make informed decisions based on accurate and consistent data. Furthermore, they facilitate compliance with regulatory requirements and industry standards.
The development of Industry Foundation Classes (IFC) is a significant step towards achieving semantic interoperability in the construction industry. IFC is an open, international standard for exchanging BIM data. It defines a common data schema that allows different software systems to understand and interpret BIM data consistently. While IFC has made significant progress, challenges remain in fully implementing and supporting the standard across different software platforms. Further development and refinement of IFC are needed to address the evolving needs of the industry.
Many thanks to our sponsor Focus 360 Energy who helped us prepare this research report.
6. Emerging Technologies and Future Trends
The construction industry is undergoing a rapid transformation, driven by emerging technologies such as artificial intelligence (AI), machine learning (ML), and blockchain. These technologies have the potential to revolutionize information management practices and further improve project outcomes.
- Artificial Intelligence (AI) and Machine Learning (ML): AI and ML can be used to automate tasks such as clash detection, quantity takeoff, and risk assessment. They can also be used to analyze large datasets to identify patterns and predict future outcomes. For example, ML algorithms can be trained to predict construction delays based on historical data, enabling project managers to take proactive measures to mitigate potential risks.
- Blockchain: Blockchain technology can be used to create a secure and transparent record of all project transactions. This can help to reduce fraud, improve accountability, and streamline payment processes. Blockchain can also be used to manage supply chain information, ensuring the authenticity and traceability of materials.
- Digital Twins: A digital twin is a virtual representation of a physical asset. It can be used to monitor the performance of the asset in real-time and predict future maintenance needs. Digital twins can also be used to simulate different scenarios and optimize the operation of the asset. The creation of digital twins relies heavily on comprehensive and accurate data, making effective IMS crucial.
- Augmented Reality (AR) and Virtual Reality (VR): AR and VR can be used to visualize construction projects in immersive environments. This can help stakeholders to better understand the design intent and identify potential problems early on. AR can also be used to provide real-time guidance to construction workers on-site.
The integration of these emerging technologies into IMS will further enhance their capabilities and enable more efficient and effective project management. However, it is important to note that these technologies are still in their early stages of development and require further research and experimentation.
Many thanks to our sponsor Focus 360 Energy who helped us prepare this research report.
7. Conclusion: Towards a Data-Driven Construction Industry
The traditional blueprint, while still relevant, is no longer sufficient for managing the complexities of modern construction projects. Integrated information management systems are essential for centralizing, organizing, and distributing project information effectively. The evolution from paper-based blueprints to BIM and integrated digital platforms represents a significant paradigm shift, enabling improved collaboration, reduced errors, and enhanced decision-making.
Overcoming the challenges associated with IMS implementation requires a concerted effort from industry stakeholders. Addressing interoperability issues, establishing robust data governance policies, and investing in training and education are crucial for realizing the full potential of these systems. Furthermore, embracing emerging technologies such as AI, ML, and blockchain will further transform the construction industry, leading to more efficient, sustainable, and resilient built environments.
The future of construction is undoubtedly data-driven. By leveraging the power of information, the industry can optimize processes, reduce waste, and deliver better project outcomes. Moving beyond the blueprint and embracing a holistic approach to information management is essential for achieving this vision. Future research should focus on developing standardized data models, improving semantic interoperability, and exploring the ethical implications of AI in construction. Furthermore, research is needed to understand how to effectively integrate emerging technologies into existing IMS and to develop best practices for data governance and security.
Many thanks to our sponsor Focus 360 Energy who helped us prepare this research report.
References
- Eastman, C., Teicholz, P., Sacks, R., & Liston, K. (2018). BIM Handbook: A Guide to Building Information Modeling for Owners, Designers, Engineers, Contractors, and Facility Managers. John Wiley & Sons.
- Succar, B. (2009). Building information modelling framework: A research and delivery foundation. Automation in Construction, 18(3), 357-375.
- Froese, T. (2010). The integrated digital project model. Wiley-Blackwell.
- Kreider, R., Messner, J., & Dubbs, C. (2010). Building information modeling: Planning and managing construction projects. McGraw-Hill Professional.
- Bernstein, P., & Pittman, J. H. (2004). Building information modeling (BIM) strategy. McGraw-Hill.
- Bryde, D., Broquetas, M., & Volm, J. M. (2013). The project benefits of Building Information Modelling (BIM). International Journal of Project Management, 31(7), 971-980.
- Smith, D. K., & Tardif, M. (2009). Building Information Modeling (BIM): A standards roadmap. National Institute of Standards and Technology (NIST).
- National BIM Standard – United States (NBIMS-US). (Various years). National Institute of Building Sciences (NIBS).
- ISO 16739:2013. Industry Foundation Classes (IFC) for data sharing in the construction and facility management industries.
- O’Donovan, A., & Brilakis, I. (2013). Automated construction progress monitoring using images and 4D models. Advanced Engineering Informatics, 27(4), 609-621.
- Bilal, M., Oyedele, L. O., Qadir, J., Munir, K., Ajayi, S. O., & Akande, A. (2016). Big data in the construction industry: A review of present status, opportunities, and future trends. Journal of Construction Engineering and Management, 142(3), 04015097.
- Wong, A. K. D., Wong, F. K. W., & Nadeem, A. (2015). Attributes and benefits of building information modelling for project management. Journal of Construction Engineering and Management, 141(11), 04015054.
The discussion on semantic interoperability highlights a critical need for standardized data models. How might blockchain technology contribute to ensuring data integrity and traceability across various project phases and stakeholders in construction?
That’s a great point about blockchain’s potential! Beyond data integrity, its decentralized nature could foster greater trust and transparency in multi-party construction projects. Smart contracts, for instance, could automate payments upon verified milestones, reducing disputes and delays. It would be interesting to explore the scalability challenges of integrating blockchain into large projects.
Editor: FocusNews.Uk
Thank you to our Sponsor Focus 360 Energy
So, blueprints are becoming relics, huh? I’m curious, with AI/ML promising to optimize everything, will we soon see algorithms designing entire buildings, making architects more like AI whisperers than drafters? Now, THAT’S a future I’d like a blueprint for.
So, blueprints becoming museum pieces, eh? Makes you wonder if hard hats will be replaced by tinfoil hats to protect us from rogue AI construction bots. I’m just waiting for the day robots unionize.