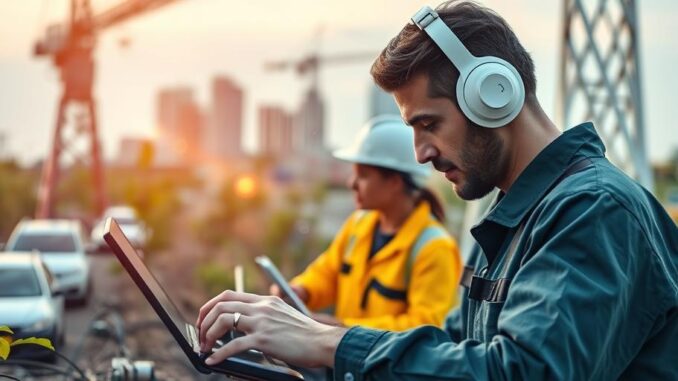
The Evolving Landscape of the Global Construction Industry: Technological Disruption, Sustainability Imperatives, and Workforce Dynamics
Abstract
The global construction industry is undergoing a period of profound transformation driven by technological advancements, increasing demands for sustainable practices, and evolving workforce demographics. This research report provides a comprehensive analysis of these key forces shaping the industry’s present and future. It explores the impact of Building Information Modeling (BIM), automation, and artificial intelligence (AI) on project efficiency, cost reduction, and quality control. Furthermore, it examines the growing emphasis on green building practices, circular economy principles, and the adoption of sustainable materials in response to climate change concerns. Finally, the report delves into the challenges and opportunities associated with workforce development, skills gaps, and the need for increased diversity and inclusion within the industry. The report synthesizes insights from academic literature, industry reports, and case studies to provide a nuanced understanding of the complexities and opportunities facing the global construction industry today.
Many thanks to our sponsor Focus 360 Energy who helped us prepare this research report.
1. Introduction
The construction industry plays a vital role in global economic development, contributing significantly to infrastructure development, housing, and commercial building projects. However, the industry has historically been characterized by low productivity growth, cost overruns, and environmental impacts. In recent years, a confluence of factors has created a compelling need for transformation. These factors include:
- Technological disruption: The emergence of new technologies such as BIM, automation, AI, and 3D printing is revolutionizing traditional construction processes and offering opportunities for significant efficiency gains.
- Sustainability imperative: Growing awareness of climate change and environmental degradation is driving demand for green building practices, sustainable materials, and energy-efficient designs.
- Workforce challenges: An aging workforce, skills gaps, and a lack of diversity are creating significant challenges for the industry, necessitating innovative approaches to workforce development and recruitment.
This research report aims to provide a comprehensive overview of these key trends and their impact on the global construction industry. It will examine the challenges and opportunities associated with each trend and explore potential strategies for navigating this evolving landscape. The report is structured into three main sections, each focusing on a specific aspect of the industry’s transformation:
- Technological Disruption: This section will analyze the impact of BIM, automation, AI, and other emerging technologies on construction processes, project management, and overall industry productivity.
- Sustainability Imperatives: This section will explore the growing emphasis on green building practices, circular economy principles, and the adoption of sustainable materials in the construction industry.
- Workforce Dynamics: This section will examine the challenges and opportunities associated with workforce development, skills gaps, diversity and inclusion, and the changing nature of work in the construction industry.
Many thanks to our sponsor Focus 360 Energy who helped us prepare this research report.
2. Technological Disruption in Construction
The construction industry has historically lagged behind other sectors in terms of technology adoption. However, the potential benefits of technological innovation are now widely recognized, leading to a rapid increase in the adoption of new technologies across the construction value chain. This section will examine the impact of several key technologies:
2.1 Building Information Modeling (BIM)
BIM is a digital representation of physical and functional characteristics of a facility. It is a shared knowledge resource for information about a facility forming a reliable basis for decisions during its lifecycle, defined as existing from earliest conception to demolition. BIM goes beyond simple 3D modeling by integrating data and information related to various aspects of a project, including design, construction, and operation.
Impact:
- Improved Design and Coordination: BIM allows architects, engineers, and contractors to collaborate more effectively, identify potential design conflicts early on, and optimize building designs for constructability and performance (Eastman et al., 2018).
- Reduced Errors and Rework: By creating a comprehensive digital model, BIM helps to reduce errors and omissions during the design and construction phases, minimizing the need for costly rework.
- Enhanced Project Management: BIM provides a centralized platform for managing project information, tracking progress, and coordinating activities across different stakeholders, leading to improved project outcomes.
- Lifecycle Cost Optimization: BIM can be used to simulate building performance over its entire lifecycle, allowing owners and operators to optimize energy consumption, maintenance costs, and overall building performance.
Challenges:
- High Initial Investment: Implementing BIM requires significant upfront investment in software, hardware, and training.
- Lack of Interoperability: Compatibility issues between different BIM software platforms can hinder collaboration and data exchange.
- Resistance to Change: Some stakeholders may be resistant to adopting new technologies and processes.
2.2 Automation and Robotics
Automation and robotics are increasingly being used in construction to perform repetitive, physically demanding, and dangerous tasks. Examples include bricklaying robots, concrete pouring robots, and automated excavation equipment.
Impact:
- Increased Productivity: Automation can significantly increase productivity by performing tasks faster and more efficiently than human workers.
- Improved Safety: Robots can be used to perform tasks in hazardous environments, reducing the risk of accidents and injuries.
- Reduced Labor Costs: Automation can reduce the need for manual labor, leading to lower labor costs.
- Enhanced Quality Control: Robots can perform tasks with greater precision and consistency, leading to improved quality control.
Challenges:
- High Capital Costs: Investing in automation and robotics requires significant capital investment.
- Job Displacement: Concerns about job displacement due to automation need to be addressed through workforce retraining and upskilling programs.
- Technical Complexity: Implementing and maintaining automated systems requires specialized technical expertise.
2.3 Artificial Intelligence (AI)
AI is being used in construction for a variety of applications, including project planning, risk management, predictive maintenance, and quality control.
Impact:
- Improved Project Planning: AI algorithms can analyze historical data and project requirements to optimize project schedules, resource allocation, and cost estimates.
- Enhanced Risk Management: AI can identify potential risks and vulnerabilities in construction projects, allowing project managers to take proactive measures to mitigate these risks.
- Predictive Maintenance: AI can analyze sensor data from building systems to predict equipment failures and schedule maintenance proactively, reducing downtime and maintenance costs.
- Automated Quality Control: AI-powered computer vision systems can automatically inspect construction work for defects and deviations from design specifications.
Challenges:
- Data Requirements: AI algorithms require large amounts of high-quality data to train and perform effectively.
- Algorithmic Bias: AI algorithms can perpetuate biases present in the data they are trained on, leading to unfair or discriminatory outcomes.
- Ethical Concerns: The use of AI in construction raises ethical concerns related to job displacement, data privacy, and algorithmic transparency.
2.4 3D Printing
3D printing, also known as additive manufacturing, is a process of building three-dimensional objects from a digital design using successive layers of material. In construction, 3D printing is being used to create building components, walls, and even entire buildings.
Impact:
- Faster Construction: 3D printing can significantly reduce construction time compared to traditional methods.
- Reduced Waste: 3D printing can minimize material waste by precisely depositing material only where it is needed.
- Design Flexibility: 3D printing allows for the creation of complex and customized building designs.
- Lower Costs: 3D printing can potentially reduce construction costs by minimizing labor and material waste.
Challenges:
- Material Limitations: The range of materials that can be used in 3D printing is currently limited.
- Scalability: Scaling up 3D printing technology to build large-scale structures remains a challenge.
- Regulatory Issues: Building codes and regulations may not be well-suited for 3D-printed structures.
Many thanks to our sponsor Focus 360 Energy who helped us prepare this research report.
3. Sustainability Imperatives in Construction
The construction industry is a significant contributor to environmental pollution and resource depletion. The growing awareness of climate change and environmental degradation is driving a strong emphasis on sustainable practices in construction. This section will explore key aspects of sustainability in the industry:
3.1 Green Building Practices
Green building practices aim to minimize the environmental impact of buildings throughout their lifecycle, from design and construction to operation and demolition. This includes factors such as energy efficiency, water conservation, material selection, and indoor environmental quality.
Key Strategies:
- Energy-Efficient Design: Designing buildings to minimize energy consumption through passive heating and cooling strategies, efficient lighting, and high-performance insulation.
- Water Conservation: Implementing water-efficient fixtures and landscaping to reduce water consumption.
- Sustainable Materials: Using materials that are recycled, renewable, and locally sourced.
- Indoor Environmental Quality: Ensuring good indoor air quality through proper ventilation, low-VOC materials, and daylighting.
- Waste Management: Implementing strategies to minimize construction waste and maximize recycling.
Benefits:
- Reduced Environmental Impact: Green buildings consume less energy and water, generate less waste, and contribute less to air and water pollution.
- Lower Operating Costs: Green buildings can significantly reduce energy and water bills, leading to lower operating costs.
- Improved Occupant Health and Productivity: Green buildings provide a healthier and more comfortable indoor environment for occupants, leading to improved health and productivity.
- Enhanced Property Value: Green buildings are increasingly valued by tenants and investors, leading to higher property values.
3.2 Circular Economy Principles
The circular economy is a model of production and consumption that involves sharing, leasing, reusing, repairing, refurbishing and recycling existing materials and products as long as possible. In the context of construction, this means designing buildings for disassembly and reuse, using materials that can be easily recycled, and minimizing waste generation.
Key Strategies:
- Design for Disassembly (DfD): Designing buildings so that they can be easily disassembled at the end of their life, allowing for the reuse of building components and materials.
- Material Reuse and Recycling: Using reclaimed materials and recycled content in construction projects and implementing effective recycling programs to minimize waste.
- Modular Construction: Using prefabricated modules that can be easily disassembled and reconfigured.
- Building Information Modeling (BIM) for Deconstruction: Using BIM to plan and manage the deconstruction process, optimizing the recovery of valuable materials.
Benefits:
- Reduced Resource Consumption: Circular economy principles reduce the demand for virgin materials, conserving natural resources.
- Reduced Waste Generation: By reusing and recycling materials, the circular economy minimizes waste generation and landfill disposal.
- Economic Opportunities: The circular economy creates new economic opportunities in the areas of material recovery, remanufacturing, and recycling.
- Reduced Environmental Impact: Circular economy principles reduce the environmental impact of the construction industry by minimizing resource extraction, waste generation, and pollution.
3.3 Sustainable Materials
The choice of materials plays a crucial role in the environmental impact of construction projects. Sustainable materials are those that have a lower environmental impact than conventional materials, considering factors such as embodied energy, resource depletion, and pollution.
Examples of Sustainable Materials:
- Recycled Concrete Aggregate (RCA): Concrete made from recycled concrete is durable and reduces the need for virgin materials.
- Wood from Sustainably Managed Forests: Wood that is certified by organizations such as the Forest Stewardship Council (FSC) comes from forests that are managed sustainably.
- Bamboo: Bamboo is a rapidly renewable resource that can be used for a variety of construction applications.
- Recycled Plastics: Recycled plastics can be used to make a variety of building products, such as decking, roofing, and insulation.
- Bio-Based Materials: Materials derived from renewable biological sources, such as hempcrete and straw bales, offer sustainable alternatives to conventional materials.
Challenges:
- Availability and Cost: Sustainable materials may not always be readily available or cost-competitive with conventional materials.
- Performance Concerns: Some sustainable materials may have different performance characteristics than conventional materials, requiring careful consideration in design and construction.
- Lack of Awareness: Some stakeholders may not be aware of the benefits and availability of sustainable materials.
Many thanks to our sponsor Focus 360 Energy who helped us prepare this research report.
4. Workforce Dynamics in Construction
The construction industry faces significant workforce challenges, including an aging workforce, skills gaps, and a lack of diversity and inclusion. Addressing these challenges is critical to ensuring the industry’s long-term sustainability and competitiveness. This section will examine these challenges and explore potential solutions:
4.1 Aging Workforce and Skills Gaps
The construction workforce is aging, with a significant portion of workers approaching retirement age. At the same time, the industry is facing a shortage of skilled workers in key trades. This skills gap is exacerbated by the increasing adoption of new technologies, which requires workers to have new skills and competencies.
Causes:
- Lack of Interest in Construction Careers: Young people are often not attracted to construction careers due to perceptions of low pay, physically demanding work, and limited opportunities for advancement.
- Declining Enrollment in Vocational Training Programs: Enrollment in vocational training programs for construction trades has declined in recent years.
- Rapid Technological Advancements: The rapid pace of technological change requires workers to continuously update their skills and knowledge.
Consequences:
- Reduced Productivity: Skills gaps can lead to reduced productivity and increased project costs.
- Increased Safety Risks: Inexperienced workers are more likely to be involved in accidents and injuries.
- Delays in Project Completion: Skills shortages can lead to delays in project completion.
Solutions:
- Promote Construction Careers: Develop outreach programs to promote construction careers to young people and highlight the opportunities for high pay, advancement, and rewarding work.
- Invest in Vocational Training: Increase funding for vocational training programs and apprenticeships to train the next generation of skilled construction workers.
- Provide Ongoing Training and Upskilling: Offer ongoing training and upskilling opportunities to help workers adapt to new technologies and changing job requirements.
- Improve Working Conditions: Improve working conditions in the construction industry by addressing issues such as low pay, long hours, and unsafe working environments.
4.2 Diversity and Inclusion
The construction industry has historically been dominated by white males. Increasing diversity and inclusion in the industry is essential to creating a more equitable and inclusive workforce and to attracting and retaining top talent.
Benefits of Diversity and Inclusion:
- Increased Innovation: Diverse teams are more likely to generate innovative ideas and solutions.
- Improved Problem Solving: Diverse teams bring a wider range of perspectives and experiences to problem solving.
- Enhanced Employee Engagement: Employees are more likely to be engaged and productive when they feel valued and respected.
- Improved Company Reputation: Companies that are committed to diversity and inclusion are more likely to attract and retain top talent and to enhance their reputation.
Strategies for Promoting Diversity and Inclusion:
- Recruitment and Hiring: Implement inclusive recruitment and hiring practices to attract a diverse pool of candidates.
- Training and Development: Provide training and development opportunities to help employees from diverse backgrounds succeed.
- Mentoring and Sponsorship: Establish mentoring and sponsorship programs to support the career advancement of underrepresented groups.
- Inclusive Workplace Culture: Create an inclusive workplace culture where all employees feel valued and respected.
4.3 Changing Nature of Work
The nature of work in the construction industry is changing due to the increasing adoption of new technologies and the growing demand for specialized skills. This requires workers to be more adaptable, flexible, and tech-savvy.
Trends:
- Increased Use of Technology: Workers are increasingly using technology such as BIM, mobile devices, and drones in their daily work.
- Greater Emphasis on Collaboration: Construction projects are becoming more complex and require greater collaboration among different stakeholders.
- Demand for Specialized Skills: There is a growing demand for workers with specialized skills in areas such as BIM, automation, and sustainable construction.
Implications:
- Need for Continuous Learning: Workers need to continuously learn and adapt to new technologies and changing job requirements.
- Importance of Soft Skills: Soft skills such as communication, teamwork, and problem-solving are becoming increasingly important.
- Flexibility and Adaptability: Workers need to be flexible and adaptable to changing project requirements and working conditions.
Many thanks to our sponsor Focus 360 Energy who helped us prepare this research report.
5. Conclusion
The global construction industry is undergoing a period of significant transformation driven by technological disruption, sustainability imperatives, and workforce dynamics. Embracing these changes and adapting to the evolving landscape is crucial for the industry’s long-term success.
Technological innovation offers tremendous opportunities for improving efficiency, reducing costs, and enhancing quality control. However, successful implementation requires careful planning, investment in training, and a willingness to embrace new processes. Sustainability is no longer a niche concern but a fundamental requirement for the industry. Adopting green building practices, embracing circular economy principles, and using sustainable materials are essential for minimizing the environmental impact of construction projects. Addressing workforce challenges, including the aging workforce, skills gaps, and lack of diversity and inclusion, is critical to ensuring the industry has the talent it needs to thrive in the future.
By embracing these challenges and opportunities, the construction industry can transform itself into a more efficient, sustainable, and equitable sector that contributes significantly to global economic development and societal well-being.
Many thanks to our sponsor Focus 360 Energy who helped us prepare this research report.
References
- Eastman, C., Teicholz, P., Sacks, R., & Liston, K. (2018). BIM handbook: A guide to building information modeling for owners, designers, engineers, contractors, and facility managers. John Wiley & Sons.
- Gallaher, J. P., O’Connor, J. T., Dettwiler, U. E., & Gilday, J. C. (2002). Cost Analysis of Inadequate Interoperability in the U.S. Capital Facilities Industry. National Institute of Standards and Technology.
- Haas, C. T., & Yorio, P. L. (2020). Automation and robotics for construction. Journal of Construction Engineering and Management, 146(1), 03119004.
- Lu, W., & Yuan, H. (2011). A framework for understanding the project waste management system in construction. Waste management, 31(6), 1248-1257.
- WBCSD. (2016). Building life cycle: Framework and system for measuring and reporting. World Business Council for Sustainable Development.
- World Economic Forum. (2016). Shaping the future of construction: A breakthrough in mindset and technology. World Economic Forum.
3D printing entire buildings? Suddenly, my Lego habit feels like serious career prep. But real talk, how long before building codes catch up and we’re all living in giant, structurally-sound plastic bricks?
That’s a fantastic point! The building codes are definitely a key piece of the puzzle. It will be interesting to see how regulations evolve to accommodate these innovations and ensure safety and structural integrity. Perhaps modular designs will bridge the gap as new materials get accredited. #3DPrinting #ConstructionTech
Editor: FocusNews.Uk
Thank you to our Sponsor Focus 360 Energy
The discussion of BIM for deconstruction is particularly compelling. Could leveraging BIM beyond design to manage the entire lifecycle, including end-of-life disassembly and material recovery, become a standard practice? This could significantly impact waste reduction and promote circularity.
That’s a great point! Extending BIM to manage the entire lifecycle, including deconstruction, is an exciting prospect. Standardizing this practice could revolutionize how we approach building lifecycles and substantially reduce waste. Imagine the impact on material recovery rates!
Editor: FocusNews.Uk
Thank you to our Sponsor Focus 360 Energy
3D printing entire buildings – now *that’s* a bold move! Wonder if we’ll see custom house designs available on Etsy soon? Perhaps regulations need a fast-track lane to keep up!
That’s a fun thought! It is a bold move. The idea of custom home designs being readily available is interesting; especially with the possibilities for personalization and unique architectural styles. The regulations, as you say, are essential to consider, ensuring safety as things progress.
Editor: FocusNews.Uk
Thank you to our Sponsor Focus 360 Energy
Regarding workforce dynamics, how can the industry effectively leverage remote collaboration tools to tap into a wider, more diverse talent pool, particularly in specialized areas like BIM or sustainable design?
That’s a great question! Remote collaboration tools are essential. By offering flexible work options, we can attract talent from diverse geographic locations and socioeconomic backgrounds who might otherwise be excluded. Focusing on training programs tailored to these tools is also key. This could allow greater access for marginalized groups. Does anyone have experience with this? #construction #BIM #workforcediversity #sustainability
Editor: FocusNews.Uk
Thank you to our Sponsor Focus 360 Energy