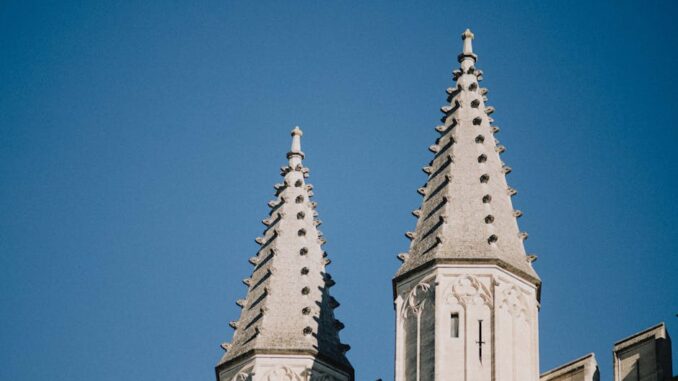
Abstract
Thermal retrofitting of historic buildings represents a critical intersection of architectural conservation and sustainable engineering, aiming to significantly enhance energy efficiency without compromising the irreplaceable cultural and aesthetic value of these structures. This comprehensive report meticulously examines the intricate engineering principles and advanced material science underpinning effective thermal retrofitting strategies. It provides an in-depth analysis of a diverse range of insulation materials, including but not limited to advanced aerogel compositions, hygroscopic wood fiber systems, and naturally breathable sheep’s wool, detailing their nuanced performance characteristics and suitability for heritage contexts. Furthermore, the report elaborates on sophisticated moisture management techniques, emphasizing hygrothermal resilience, and advanced air sealing methodologies for complex and often irregular building junctions inherent to historic construction. Through rigorous analysis of multiple real-world case studies, the report furnishes detailed technical insights into both the successes achieved and the formidable challenges encountered in the multifaceted retrofitting process, offering a valuable resource for practitioners and researchers in the field.
Many thanks to our sponsor Focus 360 Energy who helped us prepare this research report.
1. Introduction
The enduring significance of historic buildings extends beyond their structural longevity; they are tangible embodiments of collective memory, cultural identity, and architectural evolution. Their preservation is a non-negotiable imperative for societies committed to safeguarding their heritage. However, the original construction methodologies and material palettes of these venerable structures, often predating modern energy efficiency paradigms, inherently present formidable challenges in achieving contemporary thermal performance standards. Traditional building envelopes, designed for natural ventilation and often relying on thermal mass rather than insulation, typically exhibit high rates of heat loss through conduction, convection, and radiation, alongside uncontrolled air infiltration. This leads to considerable energy consumption for heating and cooling, elevated operational carbon footprints, and often compromised indoor comfort.
Thermal retrofitting emerges as a strategic intervention, meticulously designed to ameliorate the energy performance of these buildings while rigorously upholding their historical integrity and aesthetic character. This necessitates a delicate balance: the introduction of modern building science principles must be harmonized with a profound respect for original craftsmanship, material compatibility, and reversibility of interventions where appropriate. The overarching objective is not merely to reduce energy bills, but to enhance the long-term resilience and sustainability of the historic built environment, ensuring its continued relevance and functionality for future generations. This report delves deeply into the foundational engineering and material science principles indispensable for executing effective thermal retrofitting projects, placing particular emphasis on the judicious selection and application of appropriate insulation materials, robust moisture management strategies that acknowledge the unique hygrothermal behavior of historic fabrics, and precision air sealing techniques to address inherent leakiness without detriment to the building’s ‘breathability’. The multidisciplinary nature of this endeavor demands a nuanced understanding of building physics, conservation ethics, and construction practice.
Many thanks to our sponsor Focus 360 Energy who helped us prepare this research report.
2. Engineering Principles in Thermal Retrofitting
The success of any thermal retrofitting project hinges upon a thorough understanding and application of fundamental engineering principles, meticulously tailored to the unique characteristics of historic structures. Unlike new builds, interventions in heritage assets require a diagnostic approach that prioritizes preservation and minimizes irreversible alteration.
2.1. Energy Audits and Performance Assessment
Before embarking on any retrofitting measures, a comprehensive and iterative energy audit is not merely beneficial but absolutely essential. This diagnostic phase aims to establish a baseline of the building’s current thermal performance, precisely pinpointing areas of excessive heat loss or gain, identifying air leakage pathways, and assessing the existing thermal mass and insulation properties of the building envelope. A multi-faceted approach employing various advanced diagnostic techniques is typically required:
- Thermographic Surveys (Infrared Imaging): This non-invasive technique utilizes infrared cameras to visualize surface temperature differences across the building envelope. Hot spots indicate areas of heat loss (thermal bridges, air leaks, missing insulation), while cold spots may suggest moisture ingress or inadequate insulation. Carried out typically during cold weather conditions with a significant temperature differential between interior and exterior, thermography provides compelling visual evidence of thermal defects. It is crucial to interpret these images with an understanding of emissivity and reflections.
- Blower Door Tests (Air Permeability Testing): A blower door system, consisting of a powerful fan temporarily installed in an exterior doorway, is used to depressurize or pressurize the building. This creates an exaggerated air pressure difference across the building envelope, making air leakage pathways more apparent. Specialized equipment measures the airflow required to maintain a specific pressure differential (e.g., 50 Pascals). Results are typically expressed as air changes per hour at 50 Pascals (ACH50) or normalized leakage area. This quantitative data is invaluable for identifying the cumulative effect of air leaks and prioritizing air sealing efforts. Smoke pencils or theatrical fog can be used in conjunction with a blower door to visually locate specific leakage points.
- U-Value Measurements: While historical U-values can be estimated from construction drawings and material properties, on-site U-value measurements (using heat flux plates and temperature sensors) provide a more accurate assessment of the actual thermal transmittance of specific building elements (walls, roofs, floors). This empirical data is critical for validating theoretical calculations and informing detailed energy models.
- Co-heating Tests: For a more holistic and accurate measurement of a building’s whole-house heat loss coefficient (HLC), co-heating tests can be performed. This involves heating the unoccupied building to a constant elevated internal temperature over several days or weeks, while meticulously measuring the energy input and environmental factors (external temperature, solar radiation). This method provides a highly reliable measure of overall thermal performance, accounting for all heat loss mechanisms including unknown thermal bridges and air leakage, but it is time-consuming and expensive.
- Qualitative Assessments and Historical Research: Beyond technological diagnostics, a thorough understanding of the building’s construction history, original materials, and any previous alterations is crucial. Visual inspections for signs of damp, efflorescence, timber decay, or structural movement provide invaluable qualitative insights into the building’s condition and potential vulnerabilities. Consultation of archival documents, original plans, and local building traditions can inform material compatibility decisions.
The data gathered from these audits is then synthesized to create a comprehensive energy model, which helps predict the effectiveness of proposed interventions and allows for the optimization of retrofitting strategies to achieve specific energy reduction targets while respecting conservation principles. These insights inform where insulation is most effectively applied and how moisture and air movement can be managed.
2.2. Thermal Bridging and Its Mitigation
Thermal bridges, also known as cold bridges, are localized areas within the building envelope where the thermal resistance is significantly lower than that of the surrounding construction elements, leading to accelerated heat transfer. They represent a major source of avoidable heat loss and can account for a substantial proportion of a building’s overall energy consumption, even in otherwise well-insulated structures. Beyond energy waste, thermal bridges also pose a significant risk for localized surface condensation and interstitial condensation, which can lead to mold growth, material degradation, and compromised indoor air quality. There are several categories of thermal bridges:
- Geometric Thermal Bridges: Occur at corners (internal and external) where the heat transfer surface area on the warm side is larger than on the cold side, or vice versa, causing heat flow to concentrate.
- Material Thermal Bridges: Arise from the juxtaposition of materials with widely differing thermal conductivities, such as a concrete floor slab extending through an insulated wall, or steel beams penetrating insulation layers.
- Constructional Thermal Bridges: Result from discontinuities in the insulation layer due to structural elements like wall ties, joist ends, lintels above openings, or penetrations for services (pipes, ducts).
Identifying and meticulously mitigating thermal bridges is therefore paramount in any effective retrofitting strategy. This requires a detailed understanding of the building’s structural anatomy and careful detailing during the design and construction phases. Strategies for mitigation include:
- Insulation Continuity: The primary strategy is to ensure a continuous and unbroken layer of insulation around the entire building envelope, wrapping around structural elements wherever possible. This might involve extending wall insulation over floor slabs or roof junctions.
- Thermal Breaks: Introducing materials with very low thermal conductivity (thermal breaks) at junctions where structural elements penetrate the insulation layer. Examples include insulated lintels above windows and doors, composite wall ties, or structural thermal breaks in balconies or roof parapets. These materials effectively interrupt the continuous path for heat flow.
- Insulating Around Elements: Where full continuity is not feasible, insulating around structural elements (e.g., wrapping steel columns or concrete beams with insulation) can significantly reduce localized heat loss. This requires careful consideration of available space and potential impact on historic fabric.
- Improved Detailing: Meticulous design and execution of construction details are critical. This includes staggering insulation layers, overlapping membranes, and ensuring precise interfaces between different elements to minimize gaps. For historic buildings, this often means bespoke solutions rather than off-the-shelf details.
- Junction Design Optimization: For complex junctions common in historic buildings (e.g., wall-to-floor, wall-to-roof, chimney breasts), advanced numerical modeling, such as 2D or 3D thermal modeling (e.g., using software like THERM or COMSOL), can accurately predict heat flow and surface temperatures, allowing for optimized design solutions that minimize thermal bridging effects. This allows designers to evaluate the effectiveness of different insulation configurations before physical implementation.
- Internal vs. External Insulation Considerations: When applying internal insulation, thermal bridges at internal walls, floors, and ceiling junctions become more pronounced. Solutions include ‘wrapping’ internal partition walls with insulation for a short distance or using specific thermal bridge insulation boards. External insulation, conversely, typically provides a more continuous thermal envelope, effectively encapsulating most thermal bridges within the conditioned space.
2.3. Moisture Management and Condensation Control
Moisture control is arguably the most critical and complex aspect of retrofitting historic buildings. Historic structures, often constructed with hygroscopic materials like stone, brick, lime mortar, and timber, rely on the ability of their fabric to absorb and release moisture, facilitating a natural ‘breathing’ process. Disrupting this delicate balance can lead to severe and irreversible damage, including timber decay (rot), spalling of masonry, efflorescence, frost damage, and detrimental mold growth, posing risks to both structural integrity and occupant health. Understanding the building’s hygrothermal behavior – the combined movement of heat and moisture – is paramount.
- Sources of Moisture: Moisture can originate from various sources:
- External: Rain penetration (wind-driven rain, defective gutters, porous masonry), rising damp (capillary action from ground), and atmospheric humidity.
- Internal: Occupant activities (breathing, cooking, showering), plant watering, and construction moisture. Each source requires specific management strategies.
- Vapor Permeability and Vapor Drive: Moisture in the form of water vapor moves through building materials from areas of higher vapor pressure to areas of lower vapor pressure (vapor drive). This movement is critical. Historic buildings typically have vapor-open, or ‘breathable’, envelopes, allowing moisture to diffuse through and evaporate. Introducing modern, vapor-closed materials (e.g., polyethylene vapor barriers, impervious insulation boards) into such a system can trap moisture within the wall assembly, leading to interstitial condensation if the dew point is reached within the structure. The dew point is the temperature at which water vapor condenses into liquid water.
- Role of Vapor Control Layers (VCLs) vs. Vapor-Open Systems: In modern construction, VCLs are strategically placed on the warm side of the insulation to prevent vapor from reaching the colder parts of the wall where it could condense. However, in historic buildings, particularly those with internal insulation, a VCL can be counterproductive, hindering outward drying and trapping moisture. Instead, vapor-permeable (vapor-open) insulation systems are often preferred, allowing for controlled moisture diffusion and outward drying. ‘Smart’ vapor retarders, whose permeability varies with humidity levels, can also be employed, becoming more vapor-open when humidity is high to allow drying.
- Capillary Action and Capillary Active Materials: Many traditional building materials are capillary active, meaning they can wick liquid water through their pores. Some insulation materials (e.g., wood fiber, mineral wool, certain calcium silicate boards) are also capillary active, which can be beneficial in moving condensed moisture away from vulnerable parts of the structure towards the interior or exterior surface where it can evaporate. This is a crucial distinction from vapor impermeability.
- Hygrothermal Modeling (e.g., WUFI): For complex retrofits, particularly those involving internal insulation or significant changes to the envelope, advanced dynamic hygrothermal simulation software (e.g., WUFI – Wärme- und Feuchtetransport instationär) is invaluable. These models simulate the coupled heat and moisture transport through building components over time, considering variable climatic conditions and internal moisture loads. This allows designers to predict the risk of interstitial condensation and evaluate the effectiveness of different material combinations and ventilation strategies, ensuring long-term performance and preventing moisture-related failures. These simulations are far more accurate than static dew point calculations alone.
- Ventilation and Drainage: Beyond material selection, designing for proper ventilation (both within the building and, in some cases, within wall cavities or roof spaces) and effective drainage (gutters, downspouts, ground levels) is essential to manage moisture. Natural ventilation patterns often need to be re-evaluated and potentially enhanced after thermal upgrades. Balanced mechanical ventilation with heat recovery (MVHR) systems can also play a vital role in maintaining optimal indoor humidity levels while recovering heat.
2.4. Hygrothermal Performance Assessment
Beyond simply assessing heat transfer, a thorough understanding of hygrothermal performance is critical for historic buildings. This concept integrates the simultaneous movement of heat and moisture within building elements. Traditional static condensation risk analyses (Glaser Method/Dew Point Method) are often insufficient for historic structures due to their reliance on steady-state conditions and inability to account for material hygroscopicity, capillary transport, and fluctuating environmental conditions. Modern approaches include:
- Dynamic Hygrothermal Simulations: As mentioned, tools like WUFI simulate transient heat and moisture transfer. They consider hourly climatic data (temperature, relative humidity, solar radiation, rain), material properties (vapor permeability, thermal conductivity, moisture storage function, capillary conductivity), and internal boundary conditions (temperature, humidity, moisture production). These simulations can predict:
- Moisture content profiles within building components over years.
- Risk of mold growth at various interfaces (e.g., wall-insulation).
- Surface and interstitial condensation phenomena.
- Drying potential of assemblies.
This allows for a nuanced assessment of different retrofit options, ensuring that the proposed solution does not inadvertently create new moisture problems, which is a common pitfall in historic building retrofits.
- On-site Monitoring: Post-retrofit, continuous monitoring of temperature, relative humidity, and moisture content within selected wall sections can validate simulation results and provide early warning of potential issues. Embedded sensors can track performance over time, offering valuable feedback for future projects.
Many thanks to our sponsor Focus 360 Energy who helped us prepare this research report.
3. Material Science in Thermal Retrofitting
The judicious selection of insulation materials is paramount in thermal retrofitting, particularly for historic buildings where material compatibility, breathability, and long-term durability are as critical as thermal performance. The choice must be sensitive to the existing building fabric’s characteristics, including its hygric behavior, chemical composition, and structural capacity. Materials must be capable of managing moisture effectively, preventing its accumulation within the building envelope, and ideally contributing to indoor air quality.
3.1. Selection of Insulation Materials
The market offers a wide array of insulation materials, each with distinct properties. For historic buildings, a shift away from impermeable synthetic foams towards ‘breathable’ or ‘vapor-open’ and hygroscopic natural materials is often recommended to maintain the building’s inherent moisture buffering capacity and allow for outward drying. Key properties to consider include:
- Thermal Conductivity (λ-value): Measured in W/(m·K), this indicates how well a material conducts heat. Lower values signify better insulation performance.
- Specific Heat Capacity (c-value): Measured in J/(kg·K), this represents a material’s ability to store heat. Higher values contribute to thermal mass, helping to flatten temperature fluctuations.
- Density (ρ): Measured in kg/m³, density influences thermal mass and structural load. Less dense materials are typically better insulators by volume, but denser materials often have higher specific heat capacities.
- Vapor Permeability (μ-value): A dimensionless factor indicating how much a material resists vapor diffusion compared to still air. Lower μ-values mean higher vapor permeability (more breathable).
- Capillary Activity: The ability of a material to absorb and transport liquid water through capillary action. Capillary-active materials can help redistribute moisture, preventing localized saturation.
- Fire Resistance: How a material reacts to fire (flammability, smoke production, dripping). Many natural insulations require fire retardant treatments.
- Environmental Impact: Embodied energy, recyclability, renewability, and potential health impacts (VOCs).
3.2. Detailed Analysis of Key Insulation Materials
3.2.1. Aerogel
- Composition and Structure: Aerogel, often dubbed ‘frozen smoke,’ is a synthetic porous ultralight material derived from a gel in which the liquid component has been replaced with gas. Its incredibly low density (often just three times that of air) and highly porous, nanostructured silica network (with pore sizes typically 20-50 nm) give it exceptional thermal insulation properties. The tiny pores restrict the movement of air molecules, significantly reducing heat transfer through convection and conduction.
- Forms and Applications: Aerogel is available in various forms, including flexible blankets (e.g., encased in fiberglass matting), rigid boards, granular particles, and as an additive in renders or paints. Its primary advantage is its incredibly low thermal conductivity (λ ≈ 0.013 – 0.021 W/(m·K)), making it ideal for thin-profile insulation applications where space is severely limited, such as around historic window reveals, behind decorative plasterwork, or in narrow wall cavities. Its translucency can also be exploited in some glazing applications.
- Advantages:
- Outstanding Thermal Performance: Best-in-class lambda value, allowing for very thin insulation layers.
- Hydrophobic (typically): Many aerogels are surface-treated to be hydrophobic, preventing water absorption while remaining vapor-permeable, which is beneficial for moisture management.
- Lightweight: Minimal added load on existing structures.
- Non-combustible (silica aerogel): Inherently fire resistant.
- Disadvantages:
- High Cost: Significantly more expensive per square meter than conventional insulation materials.
- Brittleness/Fragility: Pure aerogel is fragile, though blanket forms are more robust. Handling can generate fine dust.
- Processing Challenges: Can be challenging to cut and install cleanly, requiring specialized tools and PPE.
3.2.2. Wood Fiber
- Composition and Production: Wood fiber insulation is derived from wood processing residues, primarily softwood timber chips (e.g., spruce, pine, fir). It is manufactured either through a wet process (slurry formed into boards, then dried) or a dry process (fibers bonded with natural resins under heat and pressure). It’s available as flexible batts, semi-rigid and rigid boards, and loose-fill insulation.
- Properties: Wood fiber insulation typically has a thermal conductivity (λ) ranging from 0.038 to 0.045 W/(m·K). Crucially for historic buildings, it is highly vapor-permeable (μ-value typically 2-5) and possesses excellent hygroscopic properties, meaning it can absorb, store, and release significant amounts of moisture without compromising its insulating performance. Its high specific heat capacity (around 2100 J/(kg·K)) provides good thermal mass, contributing to phase shift and reducing summer overheating.
- Advantages:
- Excellent Breathability: Allows moisture vapor to diffuse through the wall, reducing condensation risk.
- Hygroscopic: Buffers internal humidity, contributing to stable indoor air quality.
- Good Thermal Mass: Helps regulate internal temperatures by absorbing and slowly releasing heat, reducing peak heating/cooling loads.
- Sustainable: Made from renewable resources, often from sustainably managed forests, and sequesters carbon during its lifetime.
- Sound Insulation: Good acoustic performance due to its fibrous structure.
- Recyclable: Biodegradable and can be recycled at the end of its life.
- Disadvantages:
- Thickness: Requires thicker layers than synthetic insulations to achieve equivalent U-values.
- Fire Treatment: Typically requires non-toxic fire retardants (e.g., ammonium polyphosphate).
- Susceptibility to Water Saturation: While breathable, direct prolonged water exposure must be avoided.
3.2.3. Sheep’s Wool
- Composition and Structure: Sheep’s wool insulation is a natural, renewable fiber derived from the shearing of sheep. Its unique protein structure (keratin), natural crimp, and layered fiber arrangement trap vast amounts of air, providing excellent thermal insulation. It’s typically available in flexible rolls, batts, or loose-fill.
- Properties: Sheep’s wool insulation boasts a thermal conductivity (λ) ranging from 0.035 to 0.042 W/(m·K) (ecohome.net). One of its most remarkable properties is its ability to absorb up to 35% of its weight in moisture without significant loss of insulating value (ecohome.net, woolconcept.be). This makes it an exceptional humidity buffer, actively regulating indoor moisture levels. It has a high specific heat capacity (around 1700 J/(kg·K)). Importantly, sheep’s wool is naturally fire-resistant due to its high nitrogen and water content; it chars rather than melts or ignites, having a high ignition temperature (around 560°C) and not emitting toxic fumes when exposed to flames (ecohome.net). It may undergo a non-toxic moth-proofing treatment.
- Advantages:
- Exceptional Hygroscopic Properties: Actively manages humidity, absorbing moisture when levels are high and releasing it when low, which helps prevent condensation and improve indoor air quality.
- Excellent Thermal Performance: Good lambda value for its density.
- Natural Fire Resistance: Inherently self-extinguishing and does not melt or drip.
- Sustainable and Renewable: A truly renewable resource, requiring minimal processing.
- Sound Absorption: Excellent acoustic properties.
- Non-Irritant: Pleasant to handle compared to some other fibrous insulations.
- Formaldehyde Absorption: Has a natural ability to absorb and neutralize formaldehyde and other VOCs from the air (thesustainableinvestor.org.uk).
- Disadvantages:
- Cost: Generally more expensive than conventional mineral wool or synthetic insulations.
- Moth Treatment: Some products require a borax-based treatment to deter insect pests, although some manufacturers offer untreated varieties for specific applications where this is less of a concern or where natural resistance is sufficient.
3.2.4. Other Bio-based and Natural Materials
- Hemp (Cannabis sativa): Hemp fiber is processed into flexible batts or semi-rigid boards. It shares many properties with wood fiber: good breathability, hygroscopicity, and sustainability. Thermal conductivity is typically around 0.040-0.045 W/(m·K). It’s naturally pest-resistant.
- Cellulose (Recycled Paper): Made from recycled newspapers, cellulose is a highly effective, low-cost, and environmentally friendly insulation. Available as loose-fill (blown-in) or dense-pack, it can fill irregular cavities well. It’s treated with fire retardants (borates) and anti-fungal agents. Lambda values typically range from 0.038 to 0.042 W/(m·K). It is vapor-permeable and offers good thermal mass.
- Cork: Cork is harvested from the bark of cork oak trees. Available in rigid boards (often baked, which expands the cork and binds it without synthetic glues). It is naturally resistant to moisture, insects, and decay, and has good thermal (λ ≈ 0.036-0.040 W/(m·K)) and acoustic properties. It is durable and dimensionally stable, suitable for both internal and external applications, though often more expensive.
3.2.5. Mineral Wool (Rock Wool, Glass Wool)
While not bio-based, mineral wools are widely used. They are inorganic, fibrous materials made from molten rock (basalt) or recycled glass. They are non-combustible and offer good thermal performance (λ ≈ 0.032-0.040 W/(m·K)). They are generally vapor-permeable but not hygroscopic, meaning they don’t buffer humidity in the same way natural fibers do. While cost-effective, their production is energy-intensive, and their handling can cause irritation.
3.2.6. Rigid Foams (PIR, Phenolic)
Polyisocyanurate (PIR) and Phenolic foams offer extremely low thermal conductivities (λ ≈ 0.020-0.025 W/(m·K)), allowing for very thin insulation layers. However, they are typically vapor-impermeable (high μ-value) and have high embodied energy. Their use in historic buildings is generally discouraged for internal insulation due to the risk of trapping moisture, though they might be considered for external applications with appropriate detailing.
3.3. Compatibility and Durability
Beyond intrinsic material properties, successful integration of insulation in historic contexts demands rigorous attention to compatibility and long-term durability:
- Hygric Compatibility: New insulation must work harmoniously with existing materials regarding moisture movement. Vapor-open, capillary-active insulations are often preferred, preventing moisture accumulation at interfaces.
- Chemical Compatibility: Avoid materials that could react adversely with historic lime mortars, timber, or plasters. For instance, some synthetic glues or sealants may be incompatible with traditional hygroscopic surfaces.
- Mechanical Compatibility: The new system must not exert undue stress on the existing fragile structure. Lightweight solutions are often preferred. Adhesion methods must be reversible where possible and avoid damage to historic fabric.
- Durability and Longevity: The chosen materials should have a demonstrated track record of long-term performance in similar conditions. Natural materials like sheep’s wool and wood fiber, when properly installed and protected from bulk water, have proven extremely durable.
- Reversibility: A core conservation principle, especially for listed buildings, is the ability to remove or reverse interventions without damaging the original fabric. This influences adhesive choices, fixing methods, and insulation type.
Many thanks to our sponsor Focus 360 Energy who helped us prepare this research report.
4. Advanced Techniques for Moisture Management and Condensation Risk
Effective moisture management in historic buildings goes beyond simply blocking vapor. It involves understanding and facilitating the building’s inherent ability to ‘breathe’ while mitigating new condensation risks introduced by insulation. This often necessitates sophisticated design and material choices.
4.1. Vapor-Permeable Insulation Systems
Utilizing vapor-permeable insulation materials, often referred to as ‘breathable’ or ‘vapor-open’ systems, is a cornerstone of modern historic building retrofitting. These systems permit water vapor to diffuse through the building envelope in a controlled manner, significantly reducing the risk of interstitial condensation – condensation occurring within the wall assembly itself. This approach is particularly beneficial where maintaining the integrity and hygrothermal performance of the original materials is paramount. Key elements include:
- ‘Breathing Wall’ Concept: This philosophy advocates for building assemblies that allow continuous, controlled moisture transfer. The wall is designed to be progressively more vapor-open from the interior to the exterior, ensuring that any moisture driven into the wall can easily diffuse out, preventing its accumulation. Materials like wood fiber, sheep’s wool, mineral wool, and specialized porous boards (e.g., calcium silicate, cellular glass) are integral to this concept.
- Smart Vapor Retarders: Unlike traditional vapor barriers that are impermeable, ‘smart’ or ‘variable-permeability’ vapor retarders adjust their permeability based on ambient humidity. In dry conditions (winter), they act as a vapor retarder, limiting moisture ingress into the cold wall cavity. In humid conditions (summer or during drying-out periods), they become more vapor-open, allowing trapped moisture to escape. This dynamic behavior makes them highly suitable for historic solid walls, especially when applying internal insulation, as they mitigate winter condensation risk while promoting summer drying.
- Capillary Active Insulation: Some insulation materials (e.g., wood fiber, mineral wool, certain calcium silicate boards) are specifically designed to be capillary active. This means they can absorb small amounts of liquid water and transport it via capillary action away from colder surfaces (where condensation might occur) towards warmer surfaces where it can evaporate. This active transport mechanism is a significant advantage in managing incidental condensation within the wall structure, complementing vapor diffusion.
4.2. External Insulation (EWI) and Ventilated Facades
External Wall Insulation (EWI) systems involve applying insulation to the exterior of the building, followed by a protective render or cladding. This approach is generally considered the most effective for achieving significant energy savings and is often the preferred method from a building physics perspective as it keeps the entire original wall structure warm and dry, largely eliminating interstitial condensation risks.
- Advantages of EWI:
- Optimal Thermal Performance: Encapsulates the thermal mass of the existing wall within the conditioned space, improving thermal comfort and dampening temperature swings.
- Eliminates Cold Bridging: Provides a continuous thermal envelope, effectively mitigating most thermal bridges.
- Protects Historic Fabric: Shields the original wall from external temperature fluctuations, wind-driven rain, and freeze-thaw cycles, thereby extending its lifespan.
- Minimal Internal Disruption: Avoids reducing internal floor area, disturbing internal decorative features, or creating messy interior works.
-
Challenges of EWI for Historic Buildings:
- Aesthetic Impact: EWI significantly alters the external appearance, obscuring original brickwork, stone, or architectural detailing (e.g., cornices, quoins, decorative window surrounds). This is often unacceptable for listed buildings or those in conservation areas.
- Planning Permission: Highly regulated in heritage contexts, often requiring extensive justification and potentially being refused.
- Detailing Issues: Complex junctions around windows, doors, and rooflines require meticulous detailing to avoid new thermal bridges and ensure weather-tightness. Window reveals often need extending outwards.
- Structural Integrity: The weight of the EWI system must be properly supported, and fixings must be compatible with the existing wall structure without causing damage.
-
Ventilated Facades (Rainscreen Systems): A specific type of EWI, a ventilated facade involves an outer cladding (e.g., timber, metal, terracotta tiles) separated from the insulation layer by a ventilated air cavity. This cavity promotes air circulation, allowing any moisture that penetrates the cladding or diffuses from the wall to evaporate and be carried away. This ‘rainscreen’ principle provides superior moisture management and durability.
4.3. Internal Insulation (IWI)
Internal Wall Insulation (IWI) is frequently the only viable option for historic buildings, particularly listed properties or those within conservation areas, where external alterations are not permitted due to aesthetic or planning constraints. While preserving the external appearance, IWI introduces its own set of complex challenges related to moisture and thermal bridging.
- Challenges of IWI:
- Interstitial Condensation Risk: The original wall becomes colder, increasing the risk of moisture condensing within the wall assembly, at the interface between the existing wall and the new insulation, or within the insulation itself. This is the primary concern and necessitates careful hygrothermal assessment.
- Thermal Bridging: IWI can exacerbate thermal bridging at internal junctions (e.g., where internal partition walls, floor joists, or ceiling joists meet the external wall), leading to localized cold spots and condensation risks internally.
- Reduced Internal Space: All IWI solutions reduce the internal usable floor area, which can be a significant drawback in smaller historic properties.
- Disturbance to Historic Interiors: Application of IWI requires removal of internal plasterwork, skirting boards, and potentially architraves, disturbing historic finishes and decorative elements.
- Strategies for Mitigating IWI Risks:
- Capillary-Active Boards: Materials like calcium silicate, wood fiber boards, or cellular glass are often preferred. They are vapor-permeable and can actively manage moisture, drawing it away from the cold wall and allowing it to evaporate towards the interior. This reduces the risk of water accumulation at the critical wall-insulation interface.
- Smart Vapor Retarders: As discussed, these membranes can be positioned on the warm side of the insulation, adapting their permeability to help manage moisture flow and prevent condensation.
- Airtightness Layer: Crucially, an effective internal airtightness layer must be created on the warm side of the insulation, preventing warm, moist interior air from bypassing the insulation and condensing on the cold historic wall. This often involves careful taping of membranes or precise plastering.
- Thermal Bridge Detailing: Mitigating thermal bridges at internal junctions with IWI is complex. Solutions include wrapping the insulation around internal partitions for a certain distance, using insulated reveals around windows/doors, or employing specific thermal break materials. Numerical thermal modeling is essential to optimize these details.
- Controlled Ventilation: Adequate ventilation, often mechanical ventilation with heat recovery (MVHR), is vital to manage internal humidity levels and prevent surface condensation on cold spots that might persist despite IWI.
- Moisture Surveys: Thorough pre-retrofit moisture surveys (e.g., using resistance meters, carbide meters) are crucial to ensure the historic wall is dry before insulation, as IWI can trap pre-existing moisture.
4.4. Monitoring and Maintenance
Implementing a robust monitoring system for temperature and humidity levels within the building envelope, and sometimes within the wall assemblies themselves (using embedded sensors), can provide invaluable data. This allows for early detection of potential moisture issues, confirms the effectiveness of retrofitting measures, and allows for proactive intervention. Regular maintenance and periodic inspections are vital to ensure the continued effectiveness of moisture management strategies, including checking for roof leaks, gutter blockages, and render defects.
4.5. Integrated Ventilation Strategies
While thermal retrofitting aims to make buildings more airtight, it’s essential to ensure adequate fresh air supply for occupant health and to remove pollutants and excess moisture.
- Mechanical Ventilation with Heat Recovery (MVHR): In well-sealed historic buildings, MVHR systems are often recommended. They provide continuous fresh air supply while recovering up to 90% of the heat from the outgoing stale air. This significantly improves indoor air quality, helps control humidity, and prevents heat loss through ventilation, complementing the insulation efforts.
- Demand-Controlled Ventilation (DCV): These systems adjust ventilation rates based on real-time indoor air quality parameters (e.g., CO2 levels, humidity), ensuring adequate ventilation only when needed, further optimizing energy use.
- Augmenting Natural Ventilation: For buildings where MVHR is not feasible or desirable, careful consideration of enhancing existing natural ventilation pathways (e.g., ensuring trickle vents are functional, optimizing window opening strategies) is important, albeit less controlled than mechanical systems.
Many thanks to our sponsor Focus 360 Energy who helped us prepare this research report.
5. Air Sealing Complex Junctions
Air leakage, often overlooked in favor of insulation, can account for a significant portion of heat loss in historic buildings. Uncontrolled air movement carries heat, and critically, moisture, through the building fabric, leading to reduced thermal performance, increased heating costs, discomfort (draughts), and potential condensation risks. Historic buildings, due to their construction methods (e.g., lime mortars, timber frames, large openings) and the passage of time (settlement, material shrinkage), typically exhibit high levels of air permeability. Addressing these leaks, particularly at complex and irregular junctions, is crucial.
5.1. Identifying Critical Junctions
Before undertaking any sealing work, a thorough diagnostic process is required to pinpoint air leakage pathways. This often involves:
- Blower Door Testing: As detailed previously, this quantifies overall airtightness and helps identify general leakiness.
- Smoke Pencil/Puffer Bottle: In conjunction with a blower door, a smoke pencil or puffer bottle can visually trace air currents at suspected leakage points (e.g., around windows, electrical outlets, pipe penetrations).
- Thermographic Surveys: Infrared cameras can detect localized cold spots caused by air infiltration, especially around junctions.
- Visual Inspection and Experience: Experienced surveyors can identify common leakage points in historic construction, such as gaps around floorboards, skirting boards, window and door frames, loft hatches, and where services penetrate the building fabric.
Common critical junctions prone to significant air leakage include:
- Wall-to-Roof Junctions: Often large, unsealed gaps where the wall plate meets the roof structure, or at eaves where insulation may be poorly fitted.
- Wall-to-Floor Junctions: Gaps between external walls and floorboards or joists, especially in suspended timber floors.
- Around Windows and Doors: Gaps between frames and masonry reveals, and around sashes/casements themselves.
- Service Penetrations: Holes for pipes, electrical cables, flues, and ventilation ducts.
- Chimney Breasts and Flues: Disused flues can act as significant air bypasses if not properly sealed at top and bottom.
- Party Walls: Air can bypass insulation through gaps in party walls, particularly where joists penetrate.
- Loft Hatches: Often unsealed and uninsulated, providing a direct pathway for air leakage.
5.2. Sealing Techniques and Materials
Effective air sealing requires a combination of appropriate materials and meticulous application techniques, always considering the need to maintain breathability where necessary and avoid damage to historic fabric. The goal is to create a continuous ‘pressure plane’ or ‘air barrier’ around the conditioned space.
- Flexible Sealants (Caulks/Mastics): For small gaps and cracks (e.g., between window frames and walls, around skirting boards), high-quality, durable, and flexible sealants are effective. For historic buildings, choosing breathable, paintable, and non-shrinking acrylic or polymer-based sealants that adhere well to various substrates (timber, masonry) is important. Avoid rigid, non-flexible fillers that will crack with building movement.
- Airtight Tapes: Specialized airtight tapes, often acrylic-based and breathable, are excellent for sealing membrane overlaps, timber-to-membrane junctions, and around penetrations. They offer strong adhesion and long-term durability. Some tapes are vapor-variable, offering further hygrothermal benefits.
- Gaskets and Weatherstripping: For operable components like windows and doors, installing high-quality compression gaskets or brush weatherstripping significantly enhances airtightness. These should be durable, resistant to UV and temperature changes, and not impede operation. For historic sash windows, bespoke draught-proofing systems that retain the window’s character are available.
- Continuous Air Barrier Membranes: For internal insulation projects, the creation of a continuous air barrier membrane on the warm side of the insulation is paramount. This membrane (which might also be a smart vapor retarder) must be meticulously taped at all overlaps, sealed to existing structures (e.g., floor, ceiling), and carefully detailed around penetrations. The success of the air sealing relies on the continuity of this layer.
- Wet Plastering/Airtight Renders: Traditional lime plaster, when applied continuously and well, can form an effective air barrier directly onto masonry walls. Newer breathable airtight renders specifically designed for internal retrofits offer an alternative, providing both air sealing and a base for insulation boards. This is often the most appropriate method for solid masonry walls where membranes are impractical or undesirable.
- Expanding Foams (Caution Advised): While polyurethane expanding foams can quickly fill large gaps (e.g., around pipe penetrations), they are generally vapor-impermeable and can be difficult to remove without damaging historic fabric. Their use should be limited and carefully considered, opting for ‘low-expansion’ or ‘flexible’ types where unavoidable, and ensuring compatibility with adjacent materials.
- Draught Excluders/Brushes: For floorboards and around skirting, discrete brush seals or flexible strips can reduce draughts without altering the appearance.
- Chimney Balloons/Caps: For disused chimneys, inflatable chimney balloons or rigid caps can block air flow and prevent heat loss, while allowing for some moisture movement to prevent damp.
5.3. Testing and Verification
After air sealing measures are implemented, it is critical to verify their effectiveness. This ensures that the effort and investment have translated into tangible improvements in airtightness.
- Post-Retrofit Blower Door Tests: Repeating the blower door test after air sealing provides a quantitative measure of the improvement in the building’s airtightness (e.g., reduced ACH50 value). This is the definitive way to assess success.
- Target Air Permeability: For historic buildings, while achieving Passivhaus levels (n50 < 0.6 h-1) might be unrealistic and potentially detrimental to the fabric, significant improvements (e.g., reducing ACH50 from 15-20 h-1 down to 5-10 h-1) are achievable and highly beneficial. Targets should be set based on the specific building’s characteristics and the overall retrofit strategy.
- Smoke Testing and Thermography (Post-Sealing): These qualitative methods can be used again to identify any remaining significant leakage paths that might have been missed or to check the efficacy of specific details.
- Phased Testing: For larger projects, it can be beneficial to perform intermediate blower door tests during the construction phase (e.g., after the air barrier is installed but before finishes) to identify and rectify leaks when they are easier to access.
Many thanks to our sponsor Focus 360 Energy who helped us prepare this research report.
6. Case Studies
Real-world case studies provide invaluable insights into the practical application of thermal retrofitting principles, illustrating both successful outcomes and the challenges inherent in working with historic structures.
6.1. Case Study 1: Retrofitting a Victorian Terrace House, London
Building Description: A typical mid-Victorian terrace house in a conservation area in Central London, constructed circa 1880. The building featured solid brick walls (approx. 225mm thick), timber suspended floors, and a pitched slate roof. Original windows were single-glazed timber sashes. The house suffered from high heating bills, noticeable draughts, and cold spots, indicative of poor thermal performance common in its typology. Maintaining the external appearance was a critical planning constraint.
Retrofit Strategy: Due to conservation area restrictions, external insulation was not feasible. The retrofit primarily focused on internal insulation and comprehensive air sealing, coupled with selective window upgrades.
- Internal Wall Insulation (IWI):
- Material Selection: After extensive hygrothermal modeling using WUFI, a 60mm thick wood fiber insulation board (λ ≈ 0.040 W/(m·K)) was selected for the solid brick external walls. This material was chosen for its breathability, hygroscopic properties, and compatibility with lime-based plasters. A breathable, yet airtight, lime-based render was applied directly to the existing brick wall as the air barrier, followed by the insulation board adhered with a breathable lime-based adhesive.
- Application: All existing plasterwork on external walls was carefully removed. A continuous air barrier was established by meticulously sealing all junctions and penetrations. The wood fiber boards were installed, followed by a final breathable lime-based plaster finish. Special attention was paid to thermal bridging at internal party walls and floor junctions by wrapping the insulation around the corners and using insulated plasterboard reveals for windows.
- Roof Insulation:
- Material Selection: 200mm of sheep’s wool insulation batts (λ ≈ 0.038 W/(m·K)) were installed between the rafters in the pitched roof, above the ceiling joists. A breathable membrane was laid over the insulation to prevent dust migration and act as a secondary air barrier.
- Ventilation: Ensuring adequate ventilation of the roof space above the insulation was critical to prevent condensation, achieved through eaves and ridge vents.
- Floor Insulation:
- Insulation was installed within the suspended timber floor void. A breathable, durable membrane was laid across the joists to support 150mm of mineral wool insulation (chosen for its cost-effectiveness in an unseen, well-ventilated cavity), ensuring airflow underneath to prevent damp in the timber.
- Air Sealing: A comprehensive air sealing strategy was implemented, including:
- Sealing gaps around window and door frames with flexible, breathable sealants.
- Installing brush draught-proofing to all historic sash windows.
- Sealing service penetrations (pipes, cables) through walls and floors with airtight grommets and tapes.
- Airtightness detailing around the new IWI layer, ensuring continuity at all corners and junctions.
- Insulating and sealing the loft hatch.
- Window Upgrades: Existing single-glazed sash windows were carefully repaired, draught-proofed, and fitted with internal secondary glazing units. This maintained the external aesthetic while significantly improving thermal and acoustic performance.
Results and Outcomes:
- Energy Reduction: Post-retrofit energy assessments, including analysis of utility bills and a follow-up blower door test, showed a 45% reduction in heating demand. The ACH50 value improved from an initial 14 h-1 to 5 h-1.
- Thermal Comfort: Occupants reported a significant improvement in thermal comfort, with reduced draughts and more stable internal temperatures.
- Moisture Management: Continuous monitoring over 12 months showed no adverse effects on indoor air quality or moisture levels. The breathable wood fiber insulation and careful detailing successfully managed moisture transfer, with no signs of interstitial condensation or mold growth.
- Conservation Impact: The external appearance of the Victorian terrace was entirely preserved, satisfying planning requirements. The internal interventions were sensitively designed to minimize impact on original features where possible.
Challenges Encountered:
- Irregular Walls: The historic brick walls were uneven, requiring careful leveling and preparation before insulation application.
- Service Integration: Routing new electrical wiring and plumbing within the new insulation layer required careful planning to maintain airtightness.
- Skilled Labour: The project demanded highly skilled craftspeople experienced in traditional building materials and sensitive retrofit techniques.
6.2. Case Study 2: Insulating a Timber-Framed Cottage, Scottish Borders
Building Description: A 17th-century vernacular timber-framed cottage, historically rendered with lime harl over a wattle-and-daub infill, situated in a damp, exposed rural location in the Scottish Borders. The building suffered from significant heat loss, particularly through its walls, and intermittent damp issues due to wind-driven rain and an inability for the original fabric to dry out effectively in certain areas. Its historical significance and protected status necessitated a highly breathable and reversible approach.
Retrofit Strategy: The primary focus was on enhancing thermal performance while fundamentally improving the building’s ability to manage moisture, leveraging its natural ‘breathing’ characteristics.
- Wall Insulation (External Application where permissible):
- Material Selection: A wood fiber external wall insulation (EWI) system was chosen for its excellent breathability, hygroscopic properties, and ability to handle moisture. 120mm thick rigid wood fiber boards (λ ≈ 0.040 W/(m·K)) were mechanically fixed to the external face of the existing timber frame and infill.
- Finishing: The insulation was finished with a breathable, silicone-enhanced lime render system, providing durable weather protection while maintaining high vapor permeability. This system was chosen to be compatible with the underlying historic lime harl and timber structure.
- Limited Internal Insulation: In areas where EWI was not aesthetically or practically possible (e.g., specific historic decorative features on a small section of façade), a thin, capillary-active internal insulation system (20mm calcium silicate board) was applied to ensure continuity of insulation, carefully detailed to manage condensation risk.
- Roof Insulation:
- Material Selection: A combination of dense-pack cellulose insulation (λ ≈ 0.038 W/(m·K)) blown into a newly created airtight layer above the ceiling, coupled with sheep’s wool batts between rafters in the sloped roof sections.
- Airtightness: A smart vapor retarder membrane was installed on the warm side of the ceiling and roof insulation, meticulously taped and sealed to all penetrations and junctions, creating a continuous air barrier.
- Floor Insulation:
- The suspended timber floor was lifted, and 200mm of breathable, netted wood fiber insulation was installed between joists, supported by a permeable membrane. A robust ground-level ventilation strategy was maintained beneath the floor to manage subfloor moisture.
- Air Sealing:
- Extensive air sealing focused on the interface between the walls and floor, walls and roof, and around all window and door openings. Breathable airtight tapes were used extensively to seal membrane overlaps and junctions.
- Special attention was given to sealing around original structural timbers (e.g., exposed cruck frames) where they met the infill or roof structure, using flexible, breathable sealants.
- Fenestration: Original timber windows were carefully repaired, reglazed with slimline double-glazed units (to minimize visual impact), and thoroughly draught-proofed.
Results and Outcomes:
- Thermal Performance: Monitoring indicated a substantial improvement in thermal comfort and a calculated 55% reduction in space heating energy demand. U-values for walls improved from approximately 1.8 W/(m²K) to 0.3 W/(m²K).
- Moisture Resilience: The combination of vapor-open EWI, smart vapor retarders, and controlled ventilation significantly enhanced the building’s moisture management. Sensors embedded within the walls showed no signs of condensation or elevated moisture content within the timber frame or insulation. The pre-existing damp issues were successfully resolved as the building could now effectively dry out.
- Structural Health: By keeping the primary timber frame within the warm, dry envelope, the long-term structural health of the building was significantly improved, mitigating future risks of rot.
- Aesthetics: The external lime render finish maintained the traditional aesthetic of the cottage, blending seamlessly with the local architectural vernacular, and securing necessary planning approvals.
Challenges Encountered:
- Irregularities of Timber Frame: The historic timber frame was highly irregular, requiring bespoke cutting and fitting of insulation boards and careful detailing to ensure continuity of the air and thermal layers.
- Managing Existing Damp: Thorough pre-retrofit assessment and addressing existing sources of damp (e.g., defective rainwater goods, ground levels) were critical before applying insulation.
- Finding Skilled Installers: Locating contractors with expertise in applying wood fiber EWI and sensitive retrofit techniques on timber-framed buildings was challenging but essential.
Many thanks to our sponsor Focus 360 Energy who helped us prepare this research report.
7. Challenges and Considerations
Thermal retrofitting of historic buildings is a multifaceted undertaking, fraught with challenges that demand a nuanced approach balancing the imperatives of energy efficiency with the principles of conservation.
7.1. Balancing Energy Efficiency and Preservation
This is the core philosophical and practical dilemma. Achieving modern energy efficiency standards often implies significant alterations to the building fabric, which can conflict directly with the ‘do no harm’ principle central to heritage conservation. Key considerations include:
- Minimal Intervention: Prioritizing solutions that involve the least possible alteration to the historic fabric. This often means focusing on air sealing and thin-profile insulation where possible, before considering more invasive measures.
- Reversibility: Where interventions are necessary, seeking solutions that can be removed in the future without causing permanent damage to the original structure or materials. This informs choices of adhesives, fixings, and insulation types.
- Authenticity: Preserving the aesthetic, material, and experiential authenticity of the building. External insulation, for instance, can drastically alter the appearance of a building, obscuring original masonry or architectural detailing, making it largely unacceptable for listed buildings or those in conservation areas. Internal insulation, while preserving the exterior, can impact internal decorative features and spatial qualities.
- Regulatory Frameworks: Navigating stringent planning regulations and listed building consent processes is crucial. Conservation officers and heritage bodies often require detailed justification, impact assessments, and adherence to specific guidelines that prioritize the preservation of character and significance.
- Performance Gap: Recognizing that the calculated or theoretical energy savings (U-values, energy models) may not fully translate to actual operational performance due to occupant behavior, installation quality, or unforeseen issues. A holistic approach focusing on comfort and durability is often more appropriate than solely pursuing aggressive U-value targets.
7.2. Material Compatibility
Ensuring that new materials are compatible with existing historic structures is paramount to prevent long-term issues such as moisture accumulation, chemical reactions, or structural damage. Historic materials often behave differently from modern ones.
- Hygric Compatibility: As extensively discussed, new materials must allow for moisture movement in a way that is compatible with the existing fabric. Introducing vapor-impermeable layers into a ‘breathing’ historic wall can trap moisture, leading to interstitial condensation, mold growth, and timber decay. Preference should be given to vapor-open, hygroscopic, and capillary-active materials that can buffer and release moisture.
- Chemical Compatibility: Some modern materials (e.g., Portland cement-based renders, harsh chemicals in some treatments) can react adversely with historic lime mortars, stone, or timber, leading to degradation, efflorescence, or spalling. It’s essential to use chemically inert or compatible materials, often traditional lime-based products or specialist breathable modern alternatives.
- Differential Movement: Historic buildings are dynamic; they expand, contract, and settle with changes in temperature, moisture, and time. New materials must accommodate this movement without cracking, delaminating, or transferring undue stress to the existing, often fragile, fabric. Flexible sealants and detailing are crucial.
- Structural Loads: The added weight of insulation systems must be within the structural capacity of the existing building. Lightweight insulation options are often preferred, especially for internal applications or where structural stability is a concern.
7.3. Cost Implications and Lifecycle Analysis (LCA)
The upfront cost of thermal retrofitting, particularly using natural and specialized materials, can be significantly higher than conventional methods, posing a barrier to widespread adoption.
- Higher Material Costs: Natural insulation materials like sheep’s wool, wood fiber, and aerogel are generally more expensive per unit than synthetic alternatives (e.g., EPS, PIR boards) or mineral wool. This is often due to smaller production scales, specialized processing, or inherent material properties.
- Higher Labour Costs: The installation of these materials, especially in complex historic contexts, often requires highly skilled, specialist craftspeople and more time-consuming, bespoke detailing, leading to higher labour costs.
- Long-Term Savings: Despite the higher upfront investment, the long-term benefits can justify the cost. These include substantial reductions in heating and cooling bills, improved indoor air quality and comfort, reduced carbon emissions over the building’s lifespan, and enhanced property value. The payback period needs to be carefully calculated.
- Grants and Incentives: Many governments and local authorities offer grants, tax incentives, or loan schemes to encourage energy efficiency improvements in historic buildings, which can help offset the initial costs.
- Lifecycle Analysis (LCA): A holistic approach considers not just the operational energy savings but also the ’embodied energy’ of the materials – the energy consumed in their extraction, manufacture, transport, and disposal. Natural materials often have significantly lower embodied energy and can even be carbon-sequestering (e.g., timber, hemp). An LCA provides a more complete picture of the environmental impact and true cost-effectiveness over the building’s entire lifecycle.
7.4. Skills and Training
The specialized nature of historic building thermal retrofitting necessitates a highly skilled workforce. Traditional building trades are increasingly rare, and the application of modern building physics principles to historic structures requires a unique blend of conservation knowledge and technical expertise.
- Shortage of Skilled Craftsmen: There is a recognized shortage of masons, plasterers, carpenters, and retrofit coordinators with the specific knowledge and experience required to work sensitively and effectively on historic fabric.
- Need for Continuous Professional Development: Designers, architects, surveyors, and installers need continuous training in hygrothermal analysis, material compatibility, air sealing techniques for irregular surfaces, and conservation best practices. Accredited training programs for ‘Retrofit Coordinators’ and ‘Retrofit Installers’ are becoming increasingly important to ensure quality and compliance.
- Integrated Design and Construction: Successful projects often rely on close collaboration between conservation architects, building physics engineers, and specialist contractors from the outset, ensuring that design decisions are technically sound and practically implementable within conservation constraints.
7.5. Regulatory and Planning Context
Navigating the planning and regulatory landscape for historic building retrofits can be complex and time-consuming.
- Listed Building Consent: For buildings on statutory lists (e.g., Grade I, II* and II in England; Category A, B, C in Scotland), virtually any alteration that affects the building’s character, even internal insulation, requires listed building consent. This process is rigorous and demands detailed justification of the proposed works, often requiring evidence of minimal impact and reversibility.
- Conservation Areas: Buildings within designated conservation areas, even if not individually listed, are subject to planning controls that seek to preserve or enhance the area’s character or appearance. External insulation or changes to windows in such areas can be difficult to obtain approval for.
- Policy Ambiguity: Sometimes, national energy efficiency targets can conflict with local conservation policies, leading to a degree of ambiguity or tension in the planning process. Clear guidelines from heritage bodies and local authorities are crucial.
Many thanks to our sponsor Focus 360 Energy who helped us prepare this research report.
8. Conclusion
Thermal retrofitting of historic buildings is an inherently complex yet indispensable undertaking, demanding a multidisciplinary approach that seamlessly integrates advanced engineering principles with nuanced material science. It represents a vital strategy for mitigating climate change, reducing energy poverty, and extending the functional lifespan of our irreplaceable architectural heritage. The foundational steps involve comprehensive energy audits utilizing state-of-the-art diagnostic tools such as thermographic surveys and blower door tests, providing empirical data to pinpoint areas of heat loss and air leakage. A deep understanding of building physics, particularly the intricacies of thermal bridging and the coupled transport of heat and moisture, is non-negotiable for designing resilient and effective interventions.
The judicious selection of insulation materials is paramount. For historic structures, there is a compelling case for prioritizing vapor-permeable, hygroscopic, and ideally natural materials such as aerogel (for thin-profile applications), wood fiber, and sheep’s wool. These materials not only deliver excellent thermal performance but also actively manage moisture within the building envelope, mitigating the critical risk of interstitial condensation that can plague solid wall constructions. Their inherent compatibility with traditional building fabrics ensures long-term durability and preserves the ‘breathability’ crucial for historic buildings’ health.
Sophisticated moisture management strategies, moving beyond simple vapor barriers to embracing vapor-open systems, capillary-active materials, and dynamic hygrothermal modeling (e.g., WUFI), are essential to avoid unintended consequences. Whether employing internal insulation (IWI) with its attendant challenges of condensation and thermal bridging, or external insulation (EWI) where aesthetically permissible, careful detailing and an understanding of moisture pathways are critical. Complementary strategies such as integrated ventilation systems, including MVHR, are vital to maintain optimal indoor air quality and humidity control in increasingly airtight envelopes.
Furthermore, precision air sealing of complex junctions – from window reveals to roof-wall interfaces – is fundamental. Identifying these leakage points through rigorous testing and implementing robust sealing techniques with appropriate, compatible materials significantly reduces convective heat loss and enhances thermal comfort. The iterative process of testing and verification ensures the efficacy of these measures.
Through the detailed analysis of real-world case studies, it is unequivocally demonstrated that, with meticulous planning, rigorous technical analysis, and the deployment of skilled craftsmanship, it is indeed possible to substantially enhance the energy efficiency of historic buildings while scrupulously preserving their architectural and historical integrity. The challenges, including balancing conservation ethics with energy targets, ensuring material compatibility, managing higher upfront costs, and addressing the skills gap, are considerable. However, the long-term benefits in terms of reduced operational carbon emissions, improved indoor environmental quality, and the continued relevance of these cultural assets underscore the profound importance and immense value of this specialized field. Continued research into novel materials, refined diagnostic techniques, and holistic lifecycle assessment will further advance the sustainable stewardship of our historic built environment.
Many thanks to our sponsor Focus 360 Energy who helped us prepare this research report.
References
- Ecohomes. (n.d.). The Pros and Cons of Sheep Wool Insulation for Homes. Retrieved from https://www.ecohome.net/en/guides/4013/the-pros-and-cons-of-sheep-wool-insulation-for-homes/
- MDPI. (n.d.). Energies journal articles. Retrieved from https://www.mdpi.com/1996-1073/18/10/2420, https://www.mdpi.com/1996-1073/15/20/7472, https://www.mdpi.com/1996-1073/16/12/4676
- MDPI. (n.d.). Materials journal article. Retrieved from https://www.mdpi.com/1996-1944/17/13/3339
- MDPI. (n.d.). Buildings journal article. Retrieved from https://www.mdpi.com/2079-6439/11/9/76
- Wikipedia. (n.d.). Wool Insulation. Retrieved from https://en.wikipedia.org/wiki/Wool_insulation
- Architects’ Journal. (n.d.). Natural insulation materials. Retrieved from https://www.architectsjournal.co.uk/specification/natural-insulation-materials
- Woolconcept. (n.d.). Performance of Sheep Wool Insulation. Retrieved from https://woolconcept.be/en/performance
- The Sustainable Investor. (n.d.). Perspective: How do nature’s insulation materials compare?. Retrieved from https://www.thesustainableinvestor.org.uk/perspective-how-do-natures-insulation-materials-compare/
The emphasis on breathability with materials like sheep’s wool seems critical. How do you balance this breathability with the need for effective air sealing, particularly around complex junctions, to prevent heat loss? Are there specific techniques that work best in older buildings?
That’s a great point about balancing breathability and airtightness! In older buildings, we often use flexible, breathable sealants at junctions and prioritize ‘smart’ vapor retarders that adapt to humidity levels. This allows moisture to escape while minimizing uncontrolled airflow and heat loss. Meticulous detailing is key!
Editor: FocusNews.Uk
Thank you to our Sponsor Focus 360 Energy
Wow, quite the deep dive into hygrothermal resilience! Makes one wonder, if historic buildings could talk, would they thank us for the thermal makeover or complain about losing their “natural” drafts? Maybe a séance is the next step in the retrofitting process?
That’s a fun thought! It really brings up the question of how we define ‘comfort’ and ‘authenticity’ when preserving these spaces. I think some buildings might appreciate the stable temperatures, while others would definitely miss the drafts! The séance idea might be useful to ensure that there are no ghosts that might be disturbed by the thermal makeover!
Editor: FocusNews.Uk
Thank you to our Sponsor Focus 360 Energy