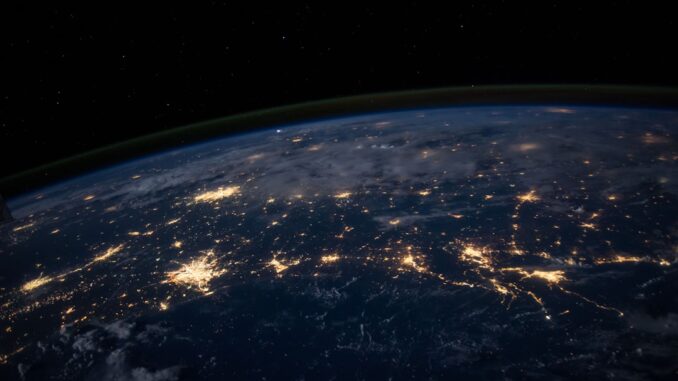
Bridging the Performance Gap: Unlocking True Energy Efficiency in New Buildings
When we embark on designing a brand-new building, there’s this inherent expectation, isn’t there? We envision a structure that not only looks fantastic but also performs optimally, especially when it comes to energy efficiency. We picture a lean, green machine, humming along, consuming minimal energy, and keeping operational costs impressively low. But here’s the rub, and it’s a significant one: a surprising number of these shiny new buildings just don’t live up to those grand expectations. They often end up guzzling far more energy than predicted, leading to higher bills, a bigger carbon footprint, and a collective sigh of frustration from everyone involved. This disparity, this frustrating chasm between what’s anticipated and what actually happens, is what we in the industry call the ‘performance gap.’
It’s not just a minor discrepancy we’re talking about; sometimes it’s an enormous gulf, a canyon really, that can swallow up budgets and tarnish reputations. But here’s the good news, the crucial takeaway: this gap isn’t some inevitable force of nature. It arises from a combination of factors, yes, but with proactive, integrated, and frankly, smarter measures, we absolutely can bridge it effectively. Let’s delve into why this happens and, more importantly, what we can do to fix it, making our new buildings truly perform as designed.
Successful low-energy building design hinges on careful planning. Focus360 Energy can help.
Understanding the Elusive Performance Gap
At its core, the performance gap is the quantifiable difference—the sometimes alarming delta—between a building’s theoretical, anticipated energy consumption during its meticulous design phase and its actual, metered energy usage once it’s up, running, and occupied. Think about it: during design, engineers use sophisticated models, plug in specific parameters, and predict a beautiful energy profile. Then the building opens its doors, and suddenly, the meter’s spinning like a top, far faster than anyone envisioned.
This isn’t just an academic problem; its implications are profound. Firstly, there’s the financial hit. Increased operational costs erode profitability and strain budgets, which, let’s be honest, no one wants. Secondly, and perhaps even more critically in our current climate, it means a higher environmental impact. More energy consumed often translates directly to more greenhouse gas emissions, undermining sustainability goals and corporate social responsibility initiatives. Identifying the precise root causes of this discrepancy is the absolute first step toward mitigating this pervasive and costly issue. It’s about peeling back the layers, isn’t it?
Unpacking the Common Culprits Behind the Gap
The performance gap isn’t caused by a single smoking gun; it’s more like a conspiracy of factors, each contributing its bit to the problem. Let’s break down the major players.
1. Design Assumptions vs. Real-World Conditions: The Ideal Versus the Actual
Designers, bless their hearts, work with the best information they have at the time. They pore over blueprints, run simulations, and make a slew of assumptions about how the building will perform. But here’s where the rubber meets the road: these assumptions, however well-intentioned, often diverge significantly from the messy, unpredictable reality of an occupied building. It’s like planning a perfect road trip route but forgetting about traffic jams and unexpected detours.
For instance, they might assume occupants will diligently adjust thermostats to optimal settings, or that lighting will always be switched off when rooms are empty. But do we really do that? Not always. Humans are creatures of habit, convenience often trumping efficiency. Similarly, relying on synthetic weather data, like a Typical Meteorological Year (TMY) file, which averages decades of weather patterns, doesn’t always accurately represent the local conditions a building experiences day-to-day. That freak heatwave we had last summer, or the unexpectedly harsh winter? Those aren’t perfectly captured in averaged data, and they can skew energy predictions dramatically. We saw this unfold with a commercial office block in London; their design-stage modelling suggested impressive numbers, but when the actual bills came in after an unusually cold winter, it was a different story entirely. The systems just couldn’t keep up efficiently with those sustained low temperatures they hadn’t truly accounted for.
Moreover, assumptions about internal heat gains—from people, computers, lighting, and other equipment—can be wildly off. A space designed for 20 people might routinely house 30, generating more heat and demanding more cooling. The theoretical efficiency of an HVAC system in a controlled lab environment often doesn’t translate perfectly to a bustling, real-world building, especially when components aren’t perfectly installed or maintained.
2. Quality of Construction and Commissioning: From Blueprint to Reality
Even with the most precise, meticulously crafted designs, the journey from paper to bricks and mortar is fraught with potential pitfalls. Poor construction practices can utterly undermine design intent. Think about it: a perfectly spec’d insulation material is useless if it’s installed incorrectly, leaving gaps or getting compressed. Air leaks, those silent energy thieves, can plague a building if seals aren’t properly applied around windows, doors, or utility penetrations. I’ve personally seen new buildings where ductwork resembled Swiss cheese, leaking conditioned air into interstitial spaces rather than where it was needed. These aren’t just minor blemishes; they’re direct conduits for energy waste.
Then there’s the critical, yet often overlooked, phase of commissioning. Commissioning, in simple terms, is the quality assurance process that ensures all building systems—HVAC, lighting controls, security, plumbing, you name it—are installed, tested, and operate as intended by the designer and owner. It’s about making sure the symphony plays in harmony, not just that each instrument is present. If building systems aren’t commissioned correctly, meaning they’re not set up, calibrated, and tested to operate as a cohesive unit, they will almost certainly underperform. Imagine a sophisticated building management system (BMS) with sensors that aren’t calibrated, or dampers that don’t close fully, or pumps running constantly when they only need to cycle. It’s a recipe for disaster, leading directly to higher energy use and occupant discomfort. This isn’t just about turning systems on; it’s about fine-tuning them, ensuring every component talks to each other and works optimally under various conditions. It’s the critical step that transforms a collection of parts into a high-performing machine.
3. Occupant Behavior: The Unpredictable Human Factor
This is perhaps one of the trickiest variables to control, yet it has an enormous impact. The way occupants actually use a building, their habits and preferences, significantly influences its energy performance. We’re talking about behaviors like leaving windows open while the air conditioning is blasting, or cranking up personal space heaters to arctic levels in a centrally heated building. And don’t even get me started on the ubiquitous charging of devices, contributing to ever-increasing plug loads that are rarely fully accounted for in design. These unpredictable actions, often driven by comfort, convenience, or simply a lack of awareness, can completely derail the most carefully designed energy strategies.
Without proper training or ongoing awareness campaigns, occupants simply might not use energy-efficient systems effectively. They might override sensors, ignore smart controls, or just not understand the ripple effect of their actions on the building’s overall energy footprint. It’s like giving someone a high-performance sports car but not teaching them how to drive it efficiently. It’s a challenge, certainly, but also a massive opportunity for engagement and education.
4. Operations and Maintenance (O&M) Deficiencies: The Post-Occupancy Slide
Even if a building is designed brilliantly, constructed well, and commissioned perfectly, its performance can degrade rapidly without diligent ongoing operations and maintenance. This is where the long-term slide often begins.
- Lack of Preventative Maintenance: Systems aren’t serviced regularly. Filters get clogged, coils get dirty, fans lose efficiency, and pumps wear out. This increases the energy needed to do the same amount of work, sometimes dramatically. It’s a bit like not changing the oil in your car; eventually, things seize up or run extremely inefficiently.
- Deferred Maintenance: When budgets are tight, maintenance often gets pushed down the priority list. Small issues become big, expensive problems that further impact energy performance.
- Staff Training Gaps: Modern building systems are complex. If facility managers and their teams aren’t properly trained on how to operate, troubleshoot, and optimize these systems, they simply can’t achieve peak performance. They might run equipment continuously, not understanding optimal scheduling, or miss opportunities for energy savings.
- Outdated or Malfunctioning Equipment: Over time, equipment ages. Its efficiency degrades. Replacing or upgrading components isn’t just about preventing breakdowns; it’s about maintaining or improving efficiency. Many buildings also struggle with legacy systems that don’t communicate well with newer technologies, creating inefficiencies.
These O&M issues can be particularly insidious because they manifest gradually, often going unnoticed until energy bills start climbing steeply. They represent a significant portion of the ongoing performance gap in many existing, and even relatively new, buildings.
Strategic Pathways to Bridge the Gap and Achieve True Efficiency
Now, for the actionable part. Addressing the performance gap isn’t about magical thinking; it’s about a systematic, multi-pronged approach that tackles each of the culprits we’ve discussed. It demands collaboration, foresight, and a commitment to continuous improvement.
1. Integrate Smart Building Technologies and Analytics
This is where technology really shines, transforming buildings from static structures into dynamic, responsive ecosystems. It’s about more than just smart thermostats, though they’re certainly a good start.
- Advanced Building Management Systems (BMS) / Building Automation Systems (BAS): These are the brains of the building, integrating various systems like HVAC, lighting, security, and access control. A robust BMS collects vast amounts of data, allowing facility managers to monitor, control, and optimize performance from a central dashboard. They can set schedules, adjust setpoints, and identify anomalies.
- Internet of Things (IoT) Sensors: Deploying a dense network of sensors for occupancy, daylight levels, CO2, temperature, humidity, and even air quality provides granular, real-time data. This data feeds into the BMS, enabling highly localized and responsive control. Imagine lights dimming only in the occupied parts of an open-plan office, or ventilation adjusting based on real-time CO2 levels, not just a preset schedule.
- Predictive Analytics and Artificial Intelligence (AI): This is the next frontier. AI algorithms can learn occupancy patterns, predict energy demand based on weather forecasts, and even anticipate equipment failures. They can then automatically adjust HVAC setpoints, lighting levels, and equipment schedules for optimal efficiency, often finding energy savings that human operators might miss. For instance, an AI might learn that a conference room is rarely used on Fridays after 3 PM and adjust pre-cooling schedules accordingly.
- Automated Shading Systems: Dynamic control of external or internal blinds based on sun angles and interior light levels can significantly reduce solar heat gain in summer and maximize daylight harvesting year-round, cutting down on both cooling and lighting loads.
- Smart Lighting Systems: Beyond basic occupancy sensors, these include daylight harvesting controls (dimming lights when natural light is sufficient), task tuning, and even personal control options for occupants. LED technology, combined with these smart controls, delivers massive savings.
Implementing these technologies isn’t just about installation; it’s about ensuring they’re integrated seamlessly and that the data they generate is actionable. The goal is to move from reactive management to proactive, intelligent optimization.
2. Enhance Building Envelope Performance: The First Line of Defense
The building envelope—the roof, walls, windows, and foundation—is your primary barrier against the elements. A leaky, poorly insulated envelope is like trying to heat your home with the windows open. No amount of smart technology inside can compensate for a fundamentally flawed outer shell.
- Superior Insulation: Go beyond minimum code requirements. Different insulation types (mineral wool, rigid foam boards, spray foam) offer varying R-values and installation benefits. Ensuring continuous insulation (minimizing thermal bridging) and meticulously filling all cavities are paramount. Thermal bridging, where heat bypasses insulation through conductive materials like steel studs, can significantly degrade overall envelope performance if not addressed through thoughtful design and careful installation.
- Air Sealing Mastery: This is absolutely critical. Identifying and sealing every tiny crack, gap, and penetration prevents conditioned air from escaping and unconditioned air from entering. Techniques include meticulous caulking, robust weatherstripping around doors and windows, specialized tapes for sheathing seams, and proper sealing around all penetrations for pipes, wires, and ducts. Blower door testing during construction is an invaluable tool to identify problem areas before the building is enclosed.
- High-Performance Glazing: Windows are often the weakest link in the envelope. Opt for double or even triple-pane glazing with low-emissivity (low-e) coatings that reflect heat. Insulated frames and gas fills (like argon or krypton) between panes further reduce heat transfer. Understanding U-values (how well a window insulates) and Solar Heat Gain Coefficient (SHGC – how much solar radiation passes through) is crucial for selecting the right windows for your climate and orientation.
- Continuous Thermal Breaks: Designers must incorporate thermal breaks at every point where a highly conductive material, like a steel beam, penetrates the insulated envelope. This prevents heat from simply ‘walking’ around the insulation.
Investing in a high-performance envelope upfront pays dividends for the entire lifecycle of the building. It reduces the load on HVAC systems, making them smaller, cheaper to run, and longer-lasting.
3. Implement Robust Energy Management Systems (EMS) and Monitoring
While a BMS manages building operations broadly, an EMS focuses specifically on energy. It’s the analytical engine that turns raw data into actionable insights, helping you truly understand where energy is going and how to manage it better.
- Real-time Monitoring and Sub-metering: You can’t manage what you don’t measure. Installing sub-meters for different energy uses (lighting, HVAC, specific departments, or even large equipment) provides granular data. Dashboards displaying real-time consumption allow facility managers to spot spikes or inefficiencies immediately. Imagine seeing the energy consumption of a specific floor jump unexpectedly on a Saturday; that’s an immediate flag for investigation.
- Benchmarking and Target Setting: An EMS allows you to compare your building’s energy performance against its design intent, against similar buildings, or against industry benchmarks. This helps identify if you’re truly underperforming or doing well, and allows you to set realistic, yet ambitious, energy reduction targets.
- Fault Detection & Diagnostics (FDD): This is a game-changer. FDD software uses algorithms to automatically identify and diagnose system malfunctions or inefficiencies. It can flag issues like ‘chiller operating inefficiently,’ ‘AHU supply air temperature too high,’ or ‘valve stuck open’ long before they become critical failures or significantly impact energy bills. It’s like having an always-on, expert technician monitoring your systems.
- Reporting and Analytics: Beyond just data, an EMS should provide clear, customizable reports and analytics. This helps facility managers understand trends, justify investments in upgrades, and demonstrate progress to stakeholders. Standards like ISO 50001 provide frameworks for establishing, implementing, maintaining, and improving an energy management system, giving you a structured approach to continuous energy performance improvement.
An effective EMS isn’t just a reporting tool; it’s a dynamic feedback loop that empowers proactive energy management.
4. Conduct Continuous Commissioning and Regular Energy Audits
Energy efficiency isn’t a ‘set it and forget it’ endeavor. It requires ongoing attention. This is where continuous commissioning and regular energy audits come into play.
- Continuous Commissioning (Cx): Beyond the initial commissioning at handover, continuous commissioning (sometimes called re-commissioning or ongoing commissioning) is about periodically reviewing, testing, and fine-tuning building systems throughout their lifespan. Buildings change: occupancy shifts, equipment ages, new technologies are introduced. Continuous Cx ensures that systems adapt and remain optimized. It’s an iterative process, focusing on maintaining peak performance, identifying new opportunities for savings, and correcting drift in control systems over time.
- Energy Audits: These are essential health checks for your building’s energy performance. During an energy audit, a professional assessor will meticulously inspect the building envelope, mechanical systems, lighting, controls, and operational practices. They’ll review utility bills, perform measurements, and often use specialized equipment (like thermal cameras to spot air leaks or insulation gaps). Audits typically come in levels:
- Level 1 (Walk-Through Audit): A basic assessment to identify obvious issues and potential low-cost/no-cost opportunities.
- Level 2 (Detailed Audit): A more in-depth analysis, including energy consumption breakdown, detailed calculations of savings for recommended measures, and estimated costs.
- Level 3 (Investment Grade Audit): The most comprehensive, often involving extensive data collection, sub-metering, and sophisticated energy modeling to provide precise costs and savings, suitable for major capital investments. The assessor will identify any potential areas of energy waste and provide concrete, actionable recommendations on how to improve energy efficiency, often with payback period analyses. This information is invaluable for prioritizing upgrades and justifying expenditure.
Regular audits and continuous commissioning ensure your building’s energy performance doesn’t just meet initial design but actively evolves and improves over time.
5. Educate Occupants and Empower Facility Managers
Technology and infrastructure are vital, but people are the ultimate key. Engaging occupants and empowering facility managers can unlock significant, often low-cost, energy savings.
- Occupant Engagement and Education: People won’t change their habits if they don’t understand why, or how. Providing occupants with clear, simple feedback on the relationship between their daily activities and energy consumption (e.g., displaying real-time energy dashboards in lobbies or common areas) can be incredibly effective. Simple tips, like ‘dress for the weather, not the thermostat,’ or ‘turn off lights when you leave the room,’ coupled with clear signage and periodic communication campaigns, can foster a culture of energy awareness. Gamification, where teams or floors compete to reduce energy use, can also be a powerful motivator. And make it personal: ‘Here’s how reducing your personal heater use impacts the building’s overall carbon footprint.’
- Empowering Facility Managers: These unsung heroes are on the front lines of building performance. They need:
- Comprehensive Training: As systems become more complex, facility staff require continuous training on new technologies, control systems, and optimal operational strategies. They need to understand not just ‘how to turn it on’ but ‘how to optimize its performance.’
- Access to Data and Tools: Provide them with the real-time energy data, analytics, and software tools needed to monitor, troubleshoot, and optimize systems effectively. They can’t manage what they can’t see or measure.
- Budget and Authority: Ensure they have the budget for preventative maintenance, necessary repairs, and timely upgrades. Empower them to make decisions that impact energy performance.
- Involvement in Design and Commissioning: Involving facility managers early in the design and commissioning phases ensures that operational considerations are built in from the start, and that they are familiar with the systems they will ultimately manage.
When people understand the ‘why’ and are given the ‘how,’ amazing things happen. They become active participants in the building’s energy story.
6. Design for Adaptability and Future-Proofing
Buildings aren’t static entities; their uses, technologies, and even their surrounding environments evolve over time. Designing for adaptability and future-proofing can help maintain energy efficiency and avoid costly retrofits down the line.
- Flexible Layouts and Systems: Consider how spaces might be reconfigured in the future. Can HVAC zones be easily re-partitioned? Are lighting controls flexible enough to adapt to new desk arrangements? Modular systems can make future changes easier and less disruptive.
- Oversizing for Future Technology: While not advocating for massive oversizing, consider making provisions for future technology integration. This might mean including extra conduit capacity, easily accessible wiring chases, or flexible communication networks that can support new sensors or smart devices as they emerge.
- Designing for Deconstruction: A truly sustainable approach considers the entire lifecycle. Designing buildings with components that can be easily disassembled, reused, or recycled at the end of their life reduces the embodied energy of future construction, contributing to overall environmental sustainability.
Anticipating future needs and designing for flexibility means your building won’t just be efficient today, but will have the inherent capacity to remain efficient tomorrow.
7. Embrace Integrated Project Delivery (IPD)
Traditionally, building projects have been fragmented, with designers, contractors, and owners often working in silos. This ‘linear’ approach can be a breeding ground for miscommunications, cost overruns, and, yes, the performance gap. Integrated Project Delivery (IPD) offers a powerful alternative.
- Collaboration from Day One: IPD brings all key stakeholders—owner, architect, engineers, general contractor, and often key subcontractors—together from the very beginning of the project. They collaborate intensively, sharing risks and rewards, working towards shared goals.
- Early Problem Solving: With everyone at the table, potential issues related to constructability, system integration, and energy performance can be identified and resolved much earlier in the design phase, when changes are far less costly to implement.
- Shared Knowledge and Accountability: This collaborative environment fosters a deep understanding of the project’s objectives and challenges across all disciplines. Everyone has a vested interest in the building’s success, including its energy performance, reducing the blame game often seen when things go wrong.
- Building Information Modeling (BIM): IPD often leverages advanced tools like BIM, which creates a comprehensive digital model of the building. This model allows for clash detection (identifying where different systems might interfere), performance simulation, and better visualization, further improving design and construction quality.
IPD isn’t just a contract type; it’s a philosophy that prioritizes collective success over individual gain, making it a powerful strategy for delivering high-performing, energy-efficient buildings.
The Path Forward: Cultivating a Culture of Performance
Ultimately, achieving and maintaining optimal energy efficiency in new buildings isn’t a one-off task. It’s a continuous journey, a shift in mindset, really, that demands a comprehensive, holistic approach. We’re talking about embedding performance at every stage of a building’s life: from the initial design assumptions, through the rigor of construction and commissioning, to the ongoing diligence of operation and the active engagement of everyone who steps through its doors. It’s about designing buildings that aren’t just theoretically good, but are proven performers in the real world.
By integrating cutting-edge smart technologies, meticulously enhancing the building envelope, implementing robust energy management and monitoring systems, committing to continuous commissioning and regular audits, educating and empowering all stakeholders, designing for future flexibility, and embracing collaborative project delivery methods, we can significantly reduce, and perhaps even eliminate, the infamous performance gap. This isn’t just about saving money, though the cost savings are considerable; it’s about creating healthier, more comfortable spaces for people, reducing our collective environmental footprint, and building a more sustainable future, one high-performing building at a time. It’s a responsibility, and an incredible opportunity, for all of us in the built environment sector.
References
The discussion on occupant behavior is crucial. How can we better leverage behavioral science to encourage energy-conscious actions within buildings, moving beyond simple awareness campaigns to create lasting habits?
That’s a great point! Beyond awareness, we could use gamification techniques – leaderboards or challenges – to incentivize energy-saving behaviors. Also, personalized feedback on energy consumption could motivate lasting habit changes. It’s about making efficiency fun and relevant!
Editor: FocusNews.Uk
Thank you to our Sponsor Focus 360 Energy
The discussion highlights the “performance gap” and the critical role of ongoing operations and maintenance. Could you elaborate on specific strategies for incentivizing building owners and managers to prioritize long-term energy efficiency over short-term cost savings in O&M?