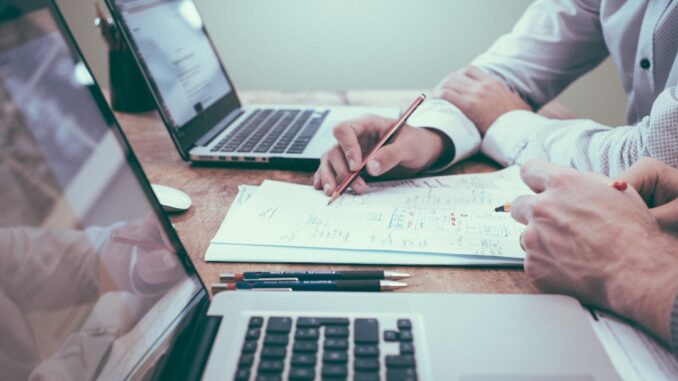
Navigating the Construction Labyrinth: Your Step-by-Step Blueprint for Project Success
Embarking on a new construction project, whether it’s a cozy residential dream or a towering commercial marvel, truly feels like standing at the foot of a magnificent mountain. It’s exhilarating, no doubt, but also daunting, packed with complexities and potential pitfalls. To conquer this peak successfully, you don’t just need grit; you need a meticulously crafted map. We’re talking about a clear, actionable blueprint for the building planning process. Forget just winging it, because that’s a quick route to budget blowouts and timelines stretching into the abyss.
Over the years, I’ve seen countless projects, from the tiny additions to sprawling campuses, succeed or falter based on the strength of their initial planning. It’s the invisible foundation, the bedrock upon which everything else rests. So, let’s unroll this map together, focusing on a robust, step-by-step approach that can save you a world of headaches, and quite frankly, a heap of cash.
Successful low-energy building design hinges on careful planning. Focus360 Energy can help.
1. Define Project Objectives and Scope: Your North Star
Before you even think about putting a shovel in the ground, or even sketching a preliminary design, you absolutely must define what it is you’re actually building and why. This isn’t just a casual chat; it’s a deep dive into the very soul of your project. Are you planning a sleek, modern residential home, perhaps a multi-family dwelling designed for urban living, or is it a bustling commercial office building? Maybe it’s an industrial facility, or perhaps even a mixed-use development that cleverly blends retail, residential, and green spaces. The purpose, the why, becomes your ultimate North Star, guiding every single decision that follows.
Think about it. If you’re constructing a residential home, your objectives might revolve around creating a harmonious, energy-efficient living space with ample natural light and smart home technologies. I remember when my partner and I were planning our own place. We weren’t just building four walls; we envisioned a sanctuary, a living machine that actively generated its own power, recycled its water, and felt seamlessly connected to the outdoors. It was a lofty goal, but defining that early on meant every architect’s sketch, every material choice, and every design discussion circled back to those core principles of modern aesthetics fused with robust sustainable features. On the other hand, a commercial building’s objectives might prioritize maximizing leasable space, achieving LEED certification, or optimizing for specific tenant needs like high-speed connectivity or specialized ventilation.
Once those objectives are etched in stone, it’s time to delineate the project’s scope. This is where you get granular, outlining precisely what work will be completed, the specific deliverables expected, and any critical constraints or exclusions. A well-defined scope isn’t just a nice-to-have; it’s a vital preventative measure against the dreaded ‘scope creep.’ That insidious phenomenon where little additions and ‘just one more thing’ requests slowly, but surely, inflate your budget and push out your timeline. Imagine signing off on a scope document that clearly states ‘client-supplied kitchen appliances’ only to later have the client assume you’re sourcing and installing them. Clarity here prevents massive headaches later.
Your scope document should detail the project’s boundaries, clearly articulating what is included and, equally important, what isn’t. It typically encompasses the functional requirements, performance specifications, design criteria, quality standards, and even the project’s lifecycle expectations. It sounds like a lot, I know, but trust me, getting all stakeholders — the owner, architects, engineers, contractors, and even key end-users — aligned on this shared understanding of the project’s boundaries from day one is absolutely non-negotiable. It creates a common language, ensuring everyone is rowing in the same direction toward a clearly articulated outcome. Without this compass, your project, regardless of its initial brilliance, is adrift.
2. Conduct a Feasibility Study: Probing the Groundwork
So, you’ve got your grand vision, your objectives are crystal clear, and your scope is meticulously defined. Fantastic. But before you plunge headfirst into detailed design and construction plans, pause. You need to assess the project’s actual viability. This is where the feasibility study comes in, acting as your crucial reality check. It’s an in-depth exploration of whether your dream project can actually become a tangible reality, considering all the practical implications.
This isn’t just about checking a box; it’s a multi-faceted evaluation encompassing technical, economic, legal, operational, and even scheduling considerations. For instance, what about the very ground you’ll build on? You’ll need to meticulously evaluate site conditions. This goes beyond a casual glance; it involves comprehensive geological surveys to understand soil composition, groundwater levels, and potential seismic risks. You might also commission environmental impact assessments to identify existing contamination, sensitive ecosystems, or historical artifacts. Access to the site, the proximity and capacity of existing utilities like water, sewer, and power, and even the site’s topography – its slopes and elevations – all play a huge role. I remember one project where an early geotechnical report flagged unexpectedly unstable bedrock requiring far more extensive blasting than anticipated, which, you guessed it, significantly impacted both the budget and the schedule. Catching that early was a game-changer, allowing us to pivot before breaking ground.
Then there are the legal constraints, which can be a veritable minefield. You’ll need to navigate local zoning ordinances, which dictate what can be built where and to what height. Are there any easements or rights-of-way crossing your property that could restrict development? What about local building codes, fire safety regulations, and environmental protection laws? And don’t forget historical preservation guidelines, which can throw a curveball if your site is near or contains protected structures. It’s a complex web, and misunderstanding just one thread can unravel the whole thing. For example, we once identified an obscure local ordinance about facade materials in a historic district during a feasibility study. Had we missed it, a beautifully designed, but non-compliant, facade would have necessitated a costly redesign and significant delays. Proactive discovery saves tears.
For commercial or even larger residential projects, market demands are also paramount. Is there an actual need for what you’re planning to build? This involves market research, demand analysis, and a thorough assessment of the competitive landscape. Building a luxury apartment complex in an area saturated with them might not be the wisest economic move, right? Similarly, for an industrial facility, you’d assess the availability of skilled labor in the region, proximity to transportation networks, and relevant supply chains.
Finally, the feasibility study also involves a preliminary identification of potential risks. We’re talking about everything from economic downturns impacting funding, to unforeseen material shortages, or even changes in local politics that could affect permitting. It’s a holistic view, designed to identify any potential challenges that might arise and, crucially, to allow for proactive solutions or, in some cases, to determine that the project simply isn’t viable as currently envisioned. The output of a thorough feasibility study is usually a go-no-go decision, providing the confidence (or the caution) needed to proceed or revise.
3. Assemble the Project Team: The Architects of Your Vision
With your project’s viability confirmed, the next crucial step is to gather the talented individuals who will breathe life into your vision. This isn’t just about hiring a bunch of people; it’s about curating a high-performing team, each member bringing specialized expertise to the table. Think of it as assembling an orchestra, where each musician, from the first violin to the timpani, plays a vital, unique role in creating a masterpiece.
At the core, you’ll undoubtedly need a skilled architect. They translate your objectives into tangible designs, creating the aesthetic and functional blueprint for the entire structure. They’re the visionaries, but also the detail-oriented experts who ensure your building complies with complex regulatory requirements. Working in tandem will be various engineers: structural engineers who ensure your building stands strong against gravity and the elements; Mechanical, Electrical, and Plumbing (MEP) engineers who design the intricate systems that make your building comfortable and functional; and civil engineers who handle site grading, drainage, and utility connections. If you’re creating outdoor spaces, a landscape architect becomes indispensable, seamlessly integrating the building with its surroundings.
Then there’s the general contractor, or perhaps a construction manager, who oversees the actual construction, coordinating subcontractors, managing timelines, and ensuring quality control. They’re the boots-on-the-ground leaders. And depending on your project’s complexity, you might also bring in specialized consultants – perhaps an acoustic engineer for a concert hall, a kitchen consultant for a restaurant, or an interior designer to refine the indoor spaces. Each member must understand their specific role and responsibilities, but more importantly, how their piece fits into the larger puzzle.
Selecting the right team isn’t just about qualifications on paper. It’s about experience, yes, but also reputation, communication style, and perhaps most importantly, their ability to collaborate effectively. I’ve learned, often the hard way, that a team with brilliant individual minds but poor chemistry can lead to more friction than progress. Conversely, a cohesive team, even when faced with daunting challenges, can innovate and problem-solve their way through anything. I recall a particularly tricky foundation pour during a commercial build. Unexpected rain turned the site into a mud bath, threatening to halt progress for days. But because our general contractor, structural engineer, and project manager had such strong rapport, they huddled, made swift decisions, and together devised a plan involving emergency drainage and temporary shelters that kept us on schedule. It was a beautiful example of collaboration in action, something you don’t always get. That shared commitment to the project’s success truly can make or break a project’s outcome, transforming obstacles into opportunities.
4. Develop a Detailed Project Schedule: The Rhythm of Progress
You’ve got your team, you’ve got your plan, now you need the rhythm. A comprehensive project schedule is the heartbeat of your construction project, outlining every single phase, task, and dependency from conception to completion. It isn’t just a simple list of deadlines; it’s a dynamic, intricate roadmap designed to keep everyone synchronized, marching to the same beat. Without it, you’re effectively flying blind, hoping to somehow land on schedule.
Your schedule needs to break down the entire project into manageable phases: pre-construction (design, permitting), procurement (ordering long-lead items), construction itself (foundations, framing, finishes), and post-construction (inspections, commissioning, occupancy). Within each phase, you’ll list individual tasks, assigning specific start and end dates. Crucially, you’ll identify dependencies between tasks. For instance, you can’t pour concrete foundations until the excavation is complete and inspections have passed. Similarly, you can’t install the plumbing fixtures until the rough-in plumbing is done and walls are framed. These dependencies, often depicted with lines connecting tasks, are fundamental to identifying the ‘critical path’ – the sequence of activities that dictates the minimum possible time to complete the project. Any delay on the critical path directly impacts the overall project completion date.
Tools like Gantt charts are incredibly valuable here. Imagine a visual timeline where each task is represented by a bar, showing its duration and overlap with other tasks. It’s a powerful visual aid for tracking progress, identifying potential bottlenecks, and communicating the timeline to all stakeholders. Many project management software solutions, from industry titans like Primavera P6 and Microsoft Project to more agile tools like Asana or Trello, offer sophisticated scheduling capabilities. They allow for resource leveling, helping you allocate labor and equipment efficiently across tasks to avoid over-utilization or idle time. They also provide real-time updates as tasks are completed, giving you an immediate snapshot of where you stand.
I vividly recall one particularly complex university building project where we had countless overlapping trades and long lead-time custom components. Our initial schedule looked like a spaghetti diagram. But meticulously building out the Gantt chart, with every dependency accounted for, allowed us to pinpoint potential clashes between different teams weeks in advance. It revealed, for instance, that a specific structural steel delivery, if even a day late, would cascade into weeks of delays for multiple follow-on trades. This early warning system meant we could proactively work with our supplier, expediting their delivery and avoiding a massive setback. The schedule isn’t a static document, by the way. It’s a living, breathing entity that needs regular updates and adjustments as realities on the ground shift. It’s your early warning system, your performance monitor, and your communication backbone all rolled into one.
5. Estimate Costs and Allocate a Budget: The Financial Backbone
Okay, let’s talk money. Because, let’s be honest, even the most brilliantly designed project can fall apart without a rock-solid financial plan. Developing a realistic budget isn’t just about putting a number on paper; it’s about building the financial backbone of your project, encompassing every single anticipated expense. You want to avoid the painful surprise of costs spiraling out of control mid-project, leaving you scrambling or, worse, stalled.
Your budget needs to account for various types of costs. First, there are the direct costs: the tangible expenses directly attributable to construction, such as labor (wages for workers, sub-contractors), materials (concrete, steel, timber, finishes), and equipment (rentals for cranes, excavators, scaffolding). Then come the indirect costs, sometimes called ‘soft costs,’ which are essential but not physically part of the structure. This includes design fees (architects, engineers), permits and approvals (a surprisingly hefty category sometimes!), insurance, legal fees, project management salaries, site supervision, temporary facilities, and even financing charges. Neglecting these indirect costs is a rookie mistake that can quickly derail an otherwise well-planned budget.
Accurate cost estimation methods vary depending on the project phase. Early on, you might use conceptual or ‘ballpark’ estimates based on historical data or unit costs (e.g., cost per square foot). As the design progresses, you move to more detailed itemized estimates, often based on quantity take-offs from drawings. This means precisely calculating the amount of concrete, the lineal feet of pipe, the number of electrical outlets – every single component. Value engineering, a process where you analyze costs versus functionality, can also come into play here, finding more cost-effective materials or methods without compromising quality or performance. It’s a bit like trying to get the most bang for your buck, ethically and smartly.
Crucially, your budget must include a contingency fund. This isn’t ‘extra money’; it’s an essential buffer for the unforeseen. Unforeseen ground conditions, supply chain disruptions, minor design changes requested mid-build, escalating material prices – these are all realities of construction. A typical contingency fund might range from 5% to 15% of the total project cost, depending on the project’s complexity and the level of risk. In a previous multi-story residential project, we allocated a 10% contingency, which proved absolutely vital. We encountered unexpected underground utility lines that needed rerouting – a costly, time-consuming endeavor. Without that contingency, we’d have been in serious financial trouble, possibly having to halt work or seek additional, expensive financing. It’s the difference between a minor setback and a full-blown crisis, trust me on this. And once your budget is set, it becomes a living document, requiring continuous monitoring of actual expenditures against planned costs, complete with variance analysis and meticulous management of any change orders.
6. Secure Necessary Permits and Approvals: Navigating the Regulatory Maze
Before you can legally lift a finger on site, before the first piece of rebar is even delivered, you absolutely, unequivocally need to secure all necessary permits and approvals. This is often the most frustrating, labyrinthine, and time-consuming part of the pre-construction phase. It’s a bureaucratic dance, and one wrong step can lead to significant delays and penalties. Think of it as passing through customs for your building; you need all your papers in order, or you’re simply not getting in.
The types of permits and approvals you’ll need are incredibly varied and depend heavily on your location and project type. You’ll definitely need a building permit from your local municipality, ensuring your design complies with building codes related to structural integrity, fire safety, and accessibility. But it doesn’t stop there. You might also need zoning approvals or variances if your project deviates from the standard zoning regulations for your area – perhaps you want to build slightly taller than allowed, or your proposed use isn’t explicitly permitted. Environmental clearances are often required, especially for larger projects or those in sensitive ecological areas, sometimes involving extensive environmental impact assessments.
Utility connection permits are vital for bringing water, sewer, gas, and electricity to your site. You might need specific fire department approvals for sprinkler systems or egress plans, and even health department approvals for commercial kitchens or specialized facilities. For certain urban projects, you could be dealing with traffic impact assessments, historical preservation reviews, or even public hearing processes if your project requires community input or significant changes to the urban fabric. It’s a lot, I know.
Navigating this permitting process demands patience, meticulous documentation, and often, early engagement with regulatory authorities. Scheduling pre-application meetings with planning departments and building officials can be incredibly beneficial. It allows you to introduce your project, clarify specific requirements, and often pre-empt potential issues before you submit formal plans. In one of my more memorable projects, we experienced a truly agonizing delay because a new stormwater management regulation had just been implemented, and our initial plans didn’t fully comply. We had to go back to the drawing board for a significant portion of our civil engineering plans, causing a multi-week delay in the overall timeline. This taught me a valuable lesson: stay aggressively current with regulatory changes, and always, always start the permitting process earlier than you think you need to. And whatever you do, avoid the temptation to cut corners. Non-compliance can lead to stop-work orders, hefty fines, and potentially even forced demolition of non-conforming work – a nightmare scenario no one wants to live through. It’s a marathon, not a sprint, but finishing it means you’re officially cleared for construction.
7. Plan Resource Allocation: Fueling the Engine
With permits in hand, it’s time to talk about the practicalities of making it all happen. This is where resource allocation comes into play – determining precisely what resources you need, when you need them, and ensuring they’re available. Think of your project as a complex engine; without the right fuel, lubricants, and parts delivered precisely when required, it grinds to a halt.
Resources aren’t just about cash. We’re talking about the triumvirate: labor, materials, and equipment. For labor, this means assessing the skilled and unskilled workforce required for each phase of construction. Do you have enough electricians for the electrical rough-in, or enough plumbers for the fit-out? Is there a skilled workforce available locally, or do you need to bring in specialists? Effective labor planning involves scheduling trades efficiently, ensuring continuity of work, and avoiding costly idle time. It also involves rigorous safety training and adherence to all labor laws, which is not just a legal requirement, but a moral imperative. After all, your people are your most valuable resource.
Material planning is equally critical. This involves identifying all necessary raw materials and finished goods, from structural steel and concrete to flooring, cabinetry, and light fixtures. But it doesn’t stop at identification; you must consider lead times for ordering, especially for custom or specialized items which can sometimes take months to arrive. You’ll need to manage procurement, working with suppliers, negotiating contracts, and scheduling deliveries to coincide with construction progress. Storage on-site, protection from the elements, and inventory management are also key considerations. I recall a project where a specific type of imported tile for a luxury bathroom was on a ridiculously long lead time. We hadn’t ordered it early enough, and by the time it was needed, we faced a three-month delay in finishing those bathrooms. It was a painful lesson in the criticality of foresight and supply chain diligence. We ultimately had to procure a temporary, less desirable tile just to get the project occupancy, only to replace it later. What a mess!
Equipment allocation covers everything from heavy machinery like excavators and cranes to smaller tools and scaffolding. Do you rent or buy? Is the equipment available when needed? What about maintenance and servicing? Optimizing equipment use can significantly impact efficiency and cost. Building Information Modeling (BIM) can be incredibly useful here, allowing you to visualize construction sequences and identify potential clashes or bottlenecks in advance, optimizing material take-offs and coordinating equipment movements. It’s about ensuring that every moving part of your project has what it needs, precisely when it needs it, to maintain a smooth, uninterrupted flow.
8. Identify and Mitigate Risks: Foreseeing the Storms
Construction projects are inherently risky endeavors. There’s a wonderful quote, something like, ‘No battle plan survives first contact with the enemy.’ In construction, the ‘enemy’ isn’t just one thing; it’s a myriad of potential problems, from an unexpected downpour to a sudden labor shortage. Therefore, you can’t just cross your fingers and hope for the best. Proactive risk management isn’t just good practice; it’s absolutely non-negotiable for project success.
This step goes beyond merely ‘anticipating’ risks. It involves a systematic process: risk identification, risk analysis, and risk response planning. Risk identification involves brainstorming sessions with your team, reviewing historical data from similar projects, using checklists, and conducting expert interviews. You’re looking for anything that could negatively impact your project’s scope, schedule, budget, or quality. Common categories include financial risks (currency fluctuations, funding issues), operational risks (equipment breakdown, material defects), environmental risks (unexpected soil conditions, natural disasters), legal risks (permit rejections, litigation), safety risks (accidents on site), and even reputational risks.
Once identified, you analyze each risk for its likelihood of occurring and its potential impact if it does. This helps you prioritize. Is it a high-likelihood, high-impact risk? That needs immediate attention. Is it a low-likelihood, low-impact risk? You might simply accept it and monitor. Then comes risk response planning: mitigation (reducing the likelihood or impact, like implementing robust safety protocols), avoidance (changing the plan to eliminate the risk altogether, perhaps by choosing a different site), transfer (shifting the risk to another party, often through insurance or specific contract clauses), or acceptance (acknowledging the risk and having a contingency plan if it occurs). Building a comprehensive ‘risk register’ – a living document that tracks identified risks, their potential impact, likelihood, and proposed mitigation strategies – is a powerful tool here.
For instance, we always plan for weather delays. You can’t control the rain, right? But you can mitigate its impact through flexible scheduling, using weather-resistant materials where possible, or having temporary shelters ready for sensitive work. Similarly, we often have backup suppliers or pre-approved alternatives for critical materials to mitigate supply chain disruptions. In one instance, our primary supplier for custom-fabricated steel components faced a significant labor dispute. Because we had a backup plan, a pre-vetted secondary fabricator, we were able to pivot quickly, negotiate a new contract, and while it caused a slight adjustment, it prevented what could have been a month-long, devastating delay. That’s the power of proactive risk management; it doesn’t eliminate problems, but it dramatically reduces their sting, saving you considerable time and money in the long run. It’s about turning potential crises into mere bumps in the road.
9. Implement a Communication Plan: The Lifeline of Collaboration
Finally, and perhaps most importantly, none of these steps truly matter if you don’t have clear, consistent communication threading through every aspect of your project. Think of a construction project as a complex organism. Communication is its nervous system, connecting every part and ensuring that messages flow freely, accurately, and promptly. Without it, confusion festers, misunderstandings proliferate, and even the smallest issues can spiral into massive problems.
Your communication plan needs to establish clear channels for information exchange among all stakeholders. This includes everyone: the owners, investors, the project management team, architects, engineers, general contractors, sub-contractors, suppliers, regulatory bodies, and even, at times, the local community. It dictates who needs to know what, when, and how. Will there be weekly progress meetings with the core team? Monthly executive updates for the owners? Daily stand-ups with site supervisors? Formal written reports? Informal check-ins?
Regular updates and consistent meetings are vital. I’ve found that weekly check-ins with the entire project team – architects, engineers, and key contractors – are invaluable. These aren’t just ‘status updates’; they’re opportunities for open dialogue. It’s where potential clashes in the schedule are identified, design questions are clarified on the spot, and emerging issues are raised before they escalate. For example, during one of these weekly meetings, our MEP engineer mentioned a minor conflict between a new ducting route and a planned structural beam, a detail caught early because of the open communication. Had we waited for formal RFI (Request for Information) submissions, it would have delayed the beam fabrication and, consequently, the entire framing schedule. Because it was brought up verbally and immediately, the architect and engineer could quickly collaborate on a solution, averting a costly re-design.
Beyond formal meetings, fostering an environment of transparent, approachable communication is key. Encourage informal check-ins, use dedicated project management platforms (like Microsoft Teams, Slack, or Trello) for quick questions and document sharing, and ensure all critical decisions and changes are documented in writing – meeting minutes, decision logs, change orders. This creates an auditable trail and reduces ‘he said, she said’ disputes. Effective communication isn’t just about relaying information; it’s about fostering trust, building strong relationships, and enabling swift, collective problem-solving. When everyone is informed, feels heard, and understands the big picture, collaboration flourishes, and the project stays firmly on track. It truly is the lifeline of project success.
There you have it. Building a significant project isn’t for the faint of heart, but by following these detailed, actionable steps, you’re not just hoping for success; you’re actively architecting it. Each phase builds upon the last, creating a robust framework that can withstand the inevitable twists and turns. Remember, meticulous planning in the beginning saves a tremendous amount of stress, time, and money down the line. So go forth, plan diligently, and build something remarkable!
Defining project objectives as a North Star is vital. How do you ensure those initial objectives remain central throughout the entire construction process, especially when faced with unexpected challenges or scope adjustments?
That’s a fantastic question! Maintaining that ‘North Star’ is key. We’ve found regular review meetings, where decisions are explicitly tied back to those initial objectives, helps keep us on track. Scope adjustments are inevitable, but framing them through the lens of the original goals allows for smarter, more aligned solutions. Thanks for sparking this discussion!
Editor: FocusNews.Uk
Thank you to our Sponsor Focus 360 Energy
Scope creep, the silent budget killer! I especially appreciated the warning about client-supplied appliances. Is there a construction horror story tax write-off? Asking for a friend who thought they were “just winging it”.