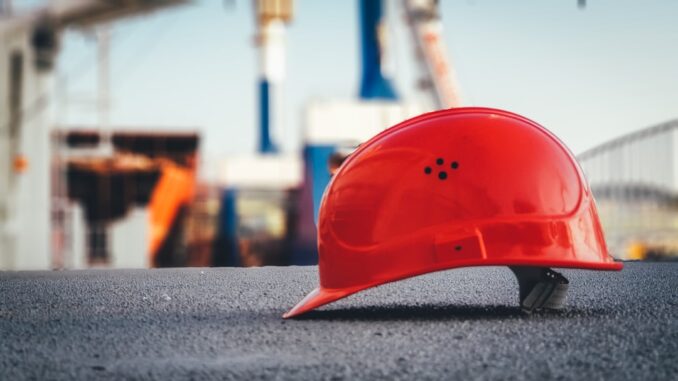
UK Building Regulations: A Deep Dive into the Construction Sector’s Shifting Sands
In July 2025, the UK government didn’t just tweak building regulations; they effectively unveiled a blueprint for a fundamentally transformed construction landscape. We’re talking about a pivotal, indeed seismic, shift in how we design, build, and manage our structures. These aren’t minor adjustments; they encompass a sweeping reform of fire safety measures, a significant ramp-up in energy efficiency requirements, and a concerted effort to streamline what has often felt like a labyrinthine regulatory process. Ultimately, the aim is clear: bolster safety, champion sustainability, and inject much-needed efficiency into a sector vital to our nation’s progress. It’s a big ask, isn’t it?
This isn’t just about ticking boxes for compliance; it’s about reshaping the built environment for future generations. For anyone in construction, or even those just watching the market, understanding these changes isn’t merely beneficial—it’s absolutely critical. Let’s unpack the core pillars of these reforms, shall we?
Focus360 Energy: property compliance services – pre-planning to post-construction. Learn more.
Unpacking Enhanced Fire Safety: Beyond Compliance
The shadow of the Grenfell Tower tragedy still looms large over the construction industry, and understandably so. It was a catalyst, a stark reminder that our existing systems, frankly, weren’t sufficient. The reforms announced are, in many ways, a direct response to the lessons painfully learned from that inferno, pushing for a robust, proactive approach to fire safety that goes far beyond the bare minimum.
The European Standard: A Leap Towards Consistency
A cornerstone of these new fire safety regulations is the definitive transition from the long-standing National Classes (BS 476) to the European Standard (BS EN 13501) for fire safety assessments. Why is this significant, you ask? Well, it’s about alignment. Historically, our national standards, while comprehensive, operated somewhat in isolation. Moving to BS EN 13501 aligns UK practices directly with international, specifically European, benchmarks. This means more consistent, arguably more rigorous, testing protocols and classifications. It’s a move away from bespoke British methods towards a globally recognized system, which can only be a good thing, can’t it?
Think about it from a manufacturer’s perspective. If you’re producing insulation, cladding, or fire doors, you’ve likely tested to BS 476 for years. Now, you face a substantial undertaking. The government has granted a transition period: a generous five years for fire resistance classifications and a tighter six months for reaction to fire classifications, for products to be retested accordingly. That six-month window for reaction to fire, in particular, will necessitate rapid action and investment from manufacturers, potentially creating short-term supply chain pressures as products await reclassification.
This shift isn’t just about new builds; it impacts the entire supply chain. Designers must specify products compliant with the new standard, contractors must procure them, and building control bodies must verify their use. It’s a systemic change that demands widespread adaptation, ensuring, for instance, that a fire door classified as resistant in Manchester meets the same fundamental criteria as one in Munich.
Sprinkler Systems: Protecting Our Most Vulnerable
Another hugely impactful requirement mandates the installation of sprinkler systems in all new care homes, irrespective of their height. This isn’t just a nod to safety; it’s a profound recognition of the unique vulnerabilities present in these environments. Residents in care homes often have mobility issues, cognitive impairments, or other health conditions that make rapid evacuation incredibly challenging, if not impossible, during a fire event. A functioning sprinkler system provides invaluable time, containing fires and suppressing smoke, giving residents and staff precious moments to escape or for emergency services to arrive.
I remember a conversation with a fire safety officer, not long ago, who simply stated, ‘Sprinklers save lives, plain and simple. Especially where people can’t save themselves.’ This isn’t an optional extra; it’s a fundamental life-saving measure that prioritizes the welfare of some of our most at-risk citizens. While developers may initially grumble about the added cost, the societal benefit and enhanced peace of mind, both for residents’ families and care home operators, really can’t be overstated. It represents a proactive, rather than reactive, approach to fire safety, moving from simply managing risk to actively mitigating it at source.
The Golden Thread: Information as a Lifeblood
Perhaps one of the most transformative elements stems from Regulation 38, which introduces stricter requirements for fire safety information. Principal contractors must now furnish detailed fire safety information to the relevant duty holder—typically the building owner or facilities manager—upon project completion or building occupation. This isn’t just a paperwork exercise; it’s about establishing what Dame Judith Hackitt famously termed the ‘golden thread’ of information.
Imagine moving into a new building. You need to know everything about its fire safety features: where the fire breaks are, the materials used in the walls and ceilings, the maintenance schedules for detection systems, and even the specific fire resistance ratings of key components. This information, often fragmented or lost in the past, now forms a continuous, accessible record. It empowers building managers to maintain safety standards effectively throughout the building’s lifespan. They can’t manage what they don’t know, can they?
This also means that during any future remediation or renovation work, the fire safety implications are clear from the outset, preventing dangerous oversights. The goal is to move away from relying on historical, often incomplete, paper trails to a dynamic, digital repository of critical safety data, ensuring accountability and transparency for years to come. It’s a huge leap forward for ongoing safety management.
Driving Sustainability: The Future Homes Standard and Beyond
Beyond fire safety, the UK government is clearly serious about tackling climate change, and the building sector holds a huge piece of that puzzle. The ambition is palpable, setting some truly demanding energy efficiency targets for new homes. You can feel the shift in the air; the days of simply bolting on a boiler are definitely numbered.
The Future Homes Standard: A Green Revolution for Residential Builds
Starting in 2027, the future of home heating in the UK will look dramatically different. The government’s ‘Future Homes Standard’ means most new homes will be required to incorporate electric heat pumps or other non-gas heating systems, essentially ushering in a ban on traditional gas boilers. This initiative isn’t just about hitting a target; it’s about radically cutting emissions, aiming for a staggering 75-80% reduction compared to current standards. That’s not a small step; it’s a giant leap.
While this policy has been discussed since 2019, the current administration seems intent on finalizing and legislating the guidance by May 2025. This gives the industry a few years to prepare, but it’s a tight turnaround for such a fundamental change. It’s not just about heat pumps either; the Future Homes Standard also implies much higher standards for fabric efficiency—think super-insulated walls, airtight construction, triple glazing, and efficient ventilation systems with heat recovery. The idea is to build homes that are so energy-efficient they require minimal heating in the first place.
Industry representatives, understandably, are calling for crystal-clear guidelines and adaptable transition arrangements. They need to know exactly what specifications they’re building to, what training is available for their workforce (we’ll need thousands of skilled heat pump installers, won’t we?), and crucially, how the supply chain for these new technologies will ramp up to meet demand. Without this clarity, we risk bottlenecks and delays in housing delivery. It’s a grand vision, but the practical implementation demands meticulous planning and robust infrastructure support. Imagine telling a builder on a site today that in just a few years, their entire heating system strategy is obsolete; that’s the scale of the challenge.
Easing the Burden? Balancing Regulation and Development
Interestingly, amidst these tightening regulations, the government is also exploring reforms to potentially ease some burdens on small and medium-sized builders (SMEs). Proposed changes include exemptions from certain environmental regulations and even the post-Grenfell safety levy. This isn’t about compromising safety, mind you, but rather about addressing the chronic housing affordability crisis and boosting home construction numbers, particularly from the smaller players who often find themselves bogged down in bureaucratic red tape.
SMEs are the backbone of local construction, but they often lack the resources of larger developers to navigate complex planning and regulatory hurdles. If these exemptions materialize, they could help these builders gain planning permission more easily and expedite project timelines. It’s a delicate balancing act, isn’t it? On one hand, we need stringent standards for safety and sustainability. On the other, we desperately need more homes, and anything that genuinely, safely, accelerates delivery is worth considering. The devil, as always, will be in the detail of how these exemptions are applied without inadvertently creating loopholes for less scrupulous developers.
Streamlining the Bureaucracy: The Building Safety Regulator’s Role
The construction industry has, at times, felt like it operates at two speeds: the rapid pace of physical construction versus the often glacial speed of regulatory approvals. Recognising this frustrating disparity, the Building Safety Regulator (BSR) is stepping up, aiming to grease the wheels of bureaucracy and make the approval process less of a headache.
Fast-Track Approvals: A Welcome Expedite for New Builds
The BSR has introduced a fast-track application process for new builds, including critically, self-build projects. This initiative directly responds to the significant, and frankly, often infuriating, delays in the current system. Can you believe that only about 15% of Gateway 2 submissions—a crucial stage for building control approval—are approved on time? That’s simply not sustainable for an industry trying to deliver homes at scale.
To combat this, the BSR is forming dedicated multi-disciplinary teams. These aren’t just a few new faces; we’re talking about regulatory leads, case officers, inspectors, and engineers, all working directly within the regulator. The goal? To slash review timelines from potentially months down to mere weeks. For a self-builder, imagine the relief of not having your dream home stalled for months just waiting for a sign-off. For developers, this means greater predictability and faster project commencement, which is invaluable in managing cash flow and deadlines. It’s a genuine attempt to make the system work for, rather than against, those who build.
Internal Expertise: Reducing Reliance on External Consultants
Part of this streamlining effort involves a significant expansion of the BSR’s internal workforce. They’re hiring over 100 new professionals, moving away from what was a heavy reliance on external consultants. This might seem like an internal management detail, but it has profound implications for the industry. An internal team fosters consistency in decision-making, develops deep institutional knowledge, and can react more nimbly to emerging issues. When you’re dealing with external consultants, there can often be a disconnect, a lack of cohesive strategy, or differing interpretations of regulations. By bringing that expertise in-house, the BSR aims to create a more unified, efficient, and responsive construction regulatory framework. It’s about building a better, more consistent service from the ground up.
Far-Reaching Implications for the Construction Industry
These regulatory changes aren’t happening in a vacuum; they ripple through every facet of the construction industry, impacting everything from profit margins to project timelines and workforce training. If you’re running a construction business, you’re undoubtedly feeling the tectonic plates shifting beneath your feet.
Pressure on Delivery and Market Dynamics
Major homebuilders, like Berkeley, have already voiced concerns about the intense pressure these reforms place on new home deliveries. The sector has, let’s be honest, been under constant scrutiny since Grenfell, enduring numerous reforms aimed at enhancing building safety and tackling systemic problems. This includes the Building Safety Levy, which we’ll discuss in a moment, funding the remediation of past safety defects and protecting leaseholders and taxpayers.
While Berkeley, a large and resilient player, has managed to maintain its earnings forecast (predicting a robust income of £525 million for the fiscal year ending April 30), that doesn’t mean the path is easy. Smaller and medium-sized developers will likely feel the pinch more acutely. Increased compliance costs, the need for new materials and technologies, and the potential for supply chain disruptions all add layers of complexity and risk. It’s a delicate dance between regulatory ambition and economic reality. Can the industry absorb these costs without significantly impacting housing affordability or simply slowing down construction altogether? That’s the multi-million-pound question.
The Building Safety Levy: Who Pays the Bill?
Then there’s the Building Safety Levy, set to come into force in autumn 2025. This isn’t a minor charge; it will apply to all new residential buildings in England requiring building control approval. The ambitious target? To raise £3.4 billion over at least ten years. And what’s it for? To pay for the remediation of building safety defects, effectively transferring some of the financial burden away from innocent leaseholders, who, through no fault of their own, found themselves trapped in unsafe homes with crippling bills. It’s a necessary intervention, but it’s still a significant new cost for developers.
This levy will inevitably be factored into project costs. While the intent is to protect leaseholders, you have to wonder how much of this cost will ultimately be passed on to the end consumer, pushing house prices ever higher. It adds another layer of financial complexity to development appraisals, forcing builders to reconsider the viability of certain projects, especially those with tighter margins.
Regional Nuances: The Welsh Example
It’s also crucial to remember that while many reforms are UK-wide, specific nations within the UK can introduce their own variations. Take Wales, for instance. The Building (Amendment) (Wales) Regulations 2025, effective from December 20, 2025, introduce similar, yet distinct, changes. A notable one is the outright ban on the use of ‘relevant metal composite material’ on the external walls of all buildings. This is another direct echo of Grenfell, where combustible cladding played such a devastating role. This regional nuance means that developers operating across the UK must navigate a patchwork of regulations, adding another layer of complexity to their operations. Consistency, while desirable, often gives way to localized policy decisions driven by specific risk assessments or political priorities.
The Road Ahead: Adaptation, Innovation, and Workforce Development
Ultimately, these developments underscore the government’s unwavering commitment to enhancing building safety and sustainability. The construction industry isn’t just reacting; it’s actively adjusting. This involves significant investment in new technologies, retraining existing workforces, and adapting supply chains. We’re talking about a demand for new skills: fire safety engineers intimately familiar with EN standards, heat pump installers, energy efficiency consultants, and digitally savvy professionals capable of managing the ‘golden thread’ of building information.
For businesses, it’s not just about compliance; it’s about competitive advantage. Those who embrace these changes early, investing in the necessary expertise and adopting innovative building methods, will undoubtedly be better positioned for success. It won’t be easy, and there will be bumps in the road, no doubt. But the outcome, a safer, more energy-efficient, and truly sustainable built environment for everyone, is surely worth the effort. It’s a challenging but exciting time to be in construction, isn’t it? The future isn’t just being planned; it’s being built, brick by regulatory brick.
The transition to BS EN 13501 for fire safety assessments highlights the increasing need for international standardization. How do you see this shift affecting cross-border collaborations and the potential for adopting best practices globally in construction?
That’s a great point! I think the move to BS EN 13501 will definitely encourage more collaboration. Standardized assessments make it easier to share knowledge and innovations across borders. Hopefully, we’ll see a faster adoption of best practices as a result. What are your thoughts on how smaller firms can best leverage these global standards?
Editor: FocusNews.Uk
Thank you to our Sponsor Focus 360 Energy
A “blueprint for a fundamentally transformed construction landscape” sounds ambitious! Is this transformation as seismic for small firms as it is for major players? Perhaps a few aftershocks are expected for the smaller firms?