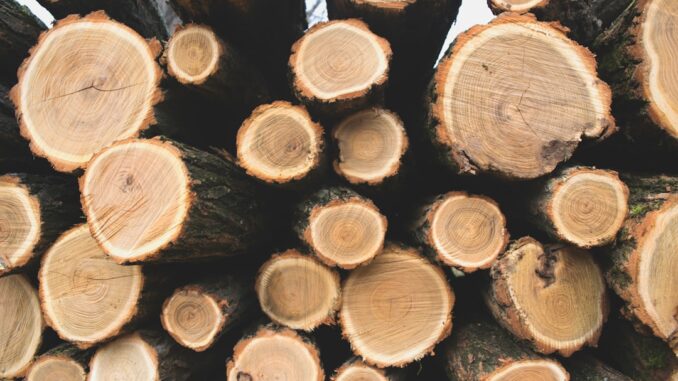
UK Homebuilders Brace for a Cost Surge: Navigating the New Construction Landscape
It’s a conversation that’s been bubbling beneath the surface for a while, isn’t it? That nagging feeling that the cost of building homes just keeps climbing. Well, now the numbers are really starting to crystalize. The UK’s homebuilding sector is staring down the barrel of a projected 12% increase in construction costs by 2030, according to the Building Cost Information Service (BCIS), a highly respected source of data and analysis for the industry. That’s a significant jump, and it’s not just a whisper; it’s a loud, clear warning sign for everyone involved, from small, local builders to national giants. This isn’t some abstract economic forecast; it translates directly into higher prices for you and me when we buy a new home, and tighter margins for those who build them. The drivers behind this surge are a potent cocktail of evolving regulations and relentless economic pressures that are fundamentally reshaping the entire construction landscape.
Successful low-energy building design hinges on careful planning. Focus360 Energy can help.
Think about it for a moment: A 12% rise over just seven years. If you’re a developer planning a project today, you’ve got to factor that into your projections, or you’ll be caught out. It means every brick laid, every beam erected, every hour of labour, will simply cost more. And honestly, it feels like we’re at an inflection point. The easy days, where perhaps costs were a bit more predictable, they’re gone. This new era demands a far more sophisticated approach to planning and execution.
The Squeeze on Labour: More Than Just Wages
When we talk about rising costs, labour is almost always at the top of the list, isn’t it? It’s the engine room of any construction project, and the BCIS Labour Cost Index predicts an eye-watering 18% rise by early 2030. That’s a huge figure, something that will undoubtedly send shivers down the spine of many a finance director. This isn’t just about headline wage increases, though those are certainly a factor. It’s a multifaceted problem, driven primarily by changes to National Insurance (NI) contributions and the steady, upward march of the National Living Wage (NLW).
Let’s unpack that a bit. From April, employer National Insurance contributions are set to tick up from 13.8% to 15%. Doesn’t sound like much, you might think, but when you multiply that across a substantial workforce, the pounds and pence really start to add up. What’s perhaps even more impactful is the concurrent drop in the contribution threshold, moving from £9,100 to a mere £5,000 per employee. This means employers will start paying NI on a much larger portion of each employee’s earnings. For a business with fifty or a hundred people on the payroll, this isn’t pocket change; it’s a direct hit to the bottom line, eroding those already slender profit margins.
But the labour challenge extends far beyond these direct tax and wage hikes. We’re facing a chronic skills gap in the UK construction industry, a problem that’s been brewing for years. Many experienced tradespeople are nearing retirement, and frankly, we haven’t brought enough new talent through the pipeline to replace them. It’s a demographic time bomb, really. Think about those highly skilled bricklayers, carpenters, and electricians; their expertise is invaluable, and their scarcity means they can command higher rates. Moreover, the impact of Brexit, while difficult to quantify precisely, has undeniably tightened the labour pool, particularly for certain roles that were historically filled by workers from the EU. It’s simple supply and demand: less supply of skilled labour means higher costs for what’s available.
So, what’s a builder to do? You can’t just conjure skilled workers out of thin air, can you? Companies are investing more in apprenticeships and in-house training programs, which is brilliant for the long term, but these come with their own upfront costs and don’t provide immediate relief. Retaining good staff has become paramount, leading to better benefits, more flexible working arrangements where possible, and competitive pay packets. The days of simply finding cheap labour are, for the most part, long gone. This shift necessitates a complete rethink of recruitment strategies and workforce planning. It’s a tough environment, and you’ll find many smaller firms, in particular, really struggling to compete for talent against the bigger players.
Materials Under Pressure: A Tangled Web of Costs
If labour is one side of the coin, material costs are definitely the other. And unfortunately, they’re not offering much respite. After a brief, almost misleading, period of decline in 2023–2024, the forecast predicts that prices for key commodities like timber, steel, and insulation will jump by 15% over the next five years. This reversal feels a bit like whiplash for an industry that hoped the worst of the post-pandemic supply chain chaos was behind it. But clearly, it isn’t.
The challenge here is incredibly complex. It’s not just about a few core materials; it’s the ripple effect across everything we use to build a home. Concrete, plasterboard, crucial electrical components, plumbing fixtures – they’re all tied into a global supply chain that remains surprisingly fragile. Remember the insane timber shortages during the pandemic lockdowns? I know a builder who had a couple of projects completely stalled for weeks because they simply couldn’t get hold of structural timber, no matter how much they were willing to pay. That kind of volatility wreaks havoc on project timelines and budgets.
Then there are the external shocks. Geopolitical events, like the conflict in Ukraine, might seem distant, but they directly impact energy prices, which in turn affect manufacturing costs for almost every material. High energy prices mean more expensive cement, more expensive steel production, and higher transportation costs. Speaking of which, the price of fuel, which impacts every lorry carrying materials to site, can fluctuate wildly. This adds another layer of unpredictability. It’s not just about the cost of the raw material itself, but the entire logistical chain that gets it to your site.
And let’s not forget the push towards more sustainable materials. While absolutely vital for our planet’s future, these alternatives often carry a premium. Recycled steel, sustainably sourced timber, innovative insulation made from natural fibres – they might be greener, but for now, they’re typically more expensive than their conventional counterparts. This puts builders in a tricky spot: meet regulatory requirements and consumer demand for eco-friendly homes, but at a higher cost. It’s a delicate balance, trying to factor in long-term environmental benefits against immediate financial outlays. So, while we all want to build greener, the immediate impact on the balance sheet is noticeable. Builders are increasingly looking at hedging strategies or long-term supply agreements to try and lock in prices, but it’s a high-stakes game.
Navigating the Green Transition: The Regulatory Imperative
Perhaps the most significant, and certainly the most transformative, cost driver on the horizon comes from the UK government’s ambitious push towards a greener future. New building regulations are not just minor tweaks; they represent a fundamental shift in how we conceive, design, and construct homes. It’s all about improving energy efficiency and drastically reducing carbon emissions, moving us closer to those elusive Net Zero targets. And frankly, this is an area where we really can’t afford to drag our feet. The planet demands it, and frankly, homeowners are increasingly expecting it.
Deciphering the Future Homes Standard: Beyond the Basics
The marquee piece of this legislative puzzle is the Future Homes Standard (FHS), set to take effect in 2025. This isn’t some gentle nudge towards better performance; it’s a seismic shift. New homes will need to produce at least 75% less CO₂ emissions than those built to the relatively lax 2013 standards. That’s not a typo; it’s three-quarters less carbon. This isn’t just about slapping on some solar panels; it’s a whole-house approach, a complete re-evaluation of building physics.
At its heart, the FHS champions a ‘fabric-first’ approach. What does that mean, exactly? It means focusing on the building’s thermal envelope before anything else. We’re talking about incredibly high levels of insulation in walls, roofs, and floors. Think about super-thick insulation boards, meticulously installed to eliminate gaps and cold spots. It’s about vastly improved U-values, which measure how effectively a material insulates, aiming for values that were almost unheard of in standard residential construction just a few years ago. We’ll also see stringent requirements for air tightness, minimising drafts and uncontrolled heat loss. This isn’t as simple as taping up a few cracks; it involves meticulous detailing around windows, doors, and service penetrations, often requiring specialist membrane systems and rigorous testing.
Furthermore, the FHS will drive the adoption of advanced low-carbon heating technologies. This primarily means heat pumps – both air source heat pumps (ASHPs) and ground source heat pumps (GSHPs). ASHPs, which extract heat from the outside air, are becoming increasingly common, but they require careful design, sufficient outdoor space, and often larger radiators or underfloor heating systems to operate efficiently. GSHPs, while incredibly efficient, involve significant upfront costs for drilling boreholes or laying ground loops, making them more suitable for certain developments.
Beyond heating, we’ll see an increasing integration of renewable energy generation on-site, primarily through photovoltaic (PV) solar panels. Homes will also need to be ‘future-proofed’ for battery storage, allowing homeowners to store excess solar energy and potentially participate in smart grid initiatives. Think about smart home systems managing energy use, optimising heating, and even potentially selling excess power back to the grid. It’s a brave new world, and it requires a different skillset from designers and installers.
The Heat Pump Revolution: Phasing Out Gas
Closely tied to the FHS, a new policy in England will outright ban the installation of gas heating systems in most new homes starting in 2027. This is a game-changer. For decades, gas boilers were the default, a simple, relatively inexpensive heating solution. But their carbon footprint is significant. So, from 2027, builders will have to specify electric heat pumps or other non-gas systems. There’s no getting around it. This policy is a crucial component of the ‘future homes standard’ and a major step towards decarbonising our housing stock.
This isn’t just a swap; it’s a fundamental change in how homes are heated. Heat pumps operate differently from boilers, providing lower, more consistent heat rather than intense bursts. This often necessitates changes to heating distribution systems within the home, favouring larger surface area emitters like underfloor heating or oversized radiators. And while heat pumps are incredibly efficient, their upfront installation costs are significantly higher than a conventional gas boiler. You’re looking at several thousand pounds more, just for the heating system alone. Then there are considerations like noise – some external heat pump units can be quite audible – and the space they require, both internally and externally.
Are we truly ready for this revolution? It requires a massive upskilling of installers, a robust supply chain for heat pump technology, and a national grid capable of handling the increased electrical demand. It’s not just about the individual home; it’s a systemic shift. Many smaller builders, who typically relied on conventional gas installations, are now facing a steep learning curve. They’ll need to forge relationships with new suppliers, train their workforce, and understand the intricacies of these new systems. It’s a lot to take on, isn’t it?
The Bottom Line Blues: Financial Realities for Developers
These regulatory changes, while absolutely necessary for our climate goals, are not without significant financial consequences for builders. Let’s be blunt: they add to the cost of building new homes. The ‘fabric-first’ approach championed by the Future Homes Standard, with its emphasis on superior insulation and airtightness, is estimated to add approximately £2,557 to the build cost of a typical new home. That’s for the basic compliance level. If a developer aims for the more ambitious 31% target outlined in Option 2 of the FHS – perhaps to gain a competitive edge or to align with higher sustainability goals – that figure jumps to a hefty £4,847 per home. And these figures don’t even fully capture the cost of the heat pump and associated electrical upgrades, which could add another several thousand pounds on top of that.
What does this mean for the developer? It means slimmer profit margins. In an industry where margins can already be tight, absorbing these extra costs is a real challenge. You can’t just pass every single penny of increased cost onto the homebuyer, at least not without risking affordability issues and slowing down sales. It forces developers to re-evaluate their entire business model, seeking efficiencies wherever possible.
This inevitably impacts affordability for the end consumer. With build costs rising, new home prices are likely to follow suit, exacerbating the existing housing affordability crisis. While energy-efficient homes offer lower running costs for the homeowner – a definite long-term benefit, one I personally value – the higher upfront purchase price can be a significant barrier. It’s a tricky balance: how do we build the greener homes we need without pricing out first-time buyers and families?
Financing also becomes a consideration. Lenders will be looking closely at development appraisals that factor in these higher build costs. Are the projected sales values realistic? Can the market absorb the increased price? These questions become even more pertinent, adding a layer of risk for both the developer and their financial partners. This isn’t just about putting up some bricks and mortar anymore; it’s about managing complex financial models in a rapidly evolving regulatory environment.
Strategies for Resilience: Building a Stronger Future
So, with all these challenges looming, what’s the path forward? For homebuilders, simply carrying on as before just won’t cut it. To navigate these turbulent waters and mitigate the financial impact of these rising costs, adaptation is absolutely key. It demands a proactive, forward-thinking approach.
1. Strategic Planning and Design Innovation: This is where it all begins. Builders need to adopt an integrated design process from day one. That means bringing together architects, structural engineers, mechanical and electrical specialists, and even material suppliers, right at the conceptual stage. Adopting Building Information Modelling (BIM) can be transformative here. BIM allows for a digital representation of the building, identifying clashes, optimising material use, and even simulating energy performance before a single brick is laid. This meticulous planning can prevent costly mistakes down the line and identify opportunities for efficiency.
2. Mastering Procurement and Supply Chain Resilience: Early procurement of materials is no longer a ‘nice to have’; it’s a necessity. Locking in prices through long-term contracts with key suppliers can provide some stability against volatile material costs. Exploring alternative, readily available materials, or even sourcing from new regions, can broaden options. Some larger firms are even considering bulk buying and stockpiling certain critical components, shifting from a ‘just-in-time’ to a more ‘just-in-case’ inventory strategy, though that carries its own financial implications.
3. Embracing Modern Methods of Construction (MMC): This is perhaps the biggest shift happening in the industry. Offsite manufacturing and modular construction – building significant parts of a home, or even entire modules, in a factory environment – offer immense potential. Imagine bathroom pods or entire wall sections being assembled in a controlled setting, then simply transported and installed on site. This can drastically reduce construction time, improve quality control, minimise waste, and, crucially, address labour shortages by shifting work from site to factory. While the upfront investment for MMC facilities can be substantial, the long-term benefits in efficiency and predictability are compelling. It also means fewer weather delays, less material waste, and often a higher quality product due to factory conditions. It’s definitely a future for the industry.
4. Investing in Skills and Training: If the labour market is tight, you’ve got to invest in your people. This means not just bringing in apprentices but upskilling your existing workforce. Training programs focused on new technologies – heat pump installation, smart home wiring, advanced insulation techniques – are vital. We need a new generation of skilled tradespeople who understand these modern systems, and businesses have a responsibility to provide that training. It’s an investment, yes, but one that pays dividends in productivity and quality.
5. Collaborative Partnerships: No one operates in a vacuum. Working closely with suppliers, fostering strong relationships, and even collaborating with clients to manage expectations about costs and timelines can be incredibly beneficial. Some builders are even exploring joint ventures or knowledge-sharing initiatives with competitors to collectively tackle industry-wide challenges, a rising tide lifts all boats, as they say.
6. Value Engineering and Innovation: This isn’t about cutting corners; it’s about smart design. How can you achieve the same or better performance using different, more cost-effective methods or materials? Can processes be streamlined? Are there new technologies or software solutions that can improve efficiency on site? This constant search for innovation is crucial to staying competitive.
As Dr. David Crosthwaite, chief economist at BCIS, rightly advises, ‘We expect slow growth in construction output in the next year, but it’s critical that homebuilders use this period of relative calm to strategically plan for the inevitable cost increases and regulatory changes coming down the line.’ He’s absolutely spot on. This isn’t a time for complacency. It’s a time for reflection, for adaptation, and for innovation.
The Path Forward: Opportunities Amidst the Challenges
It’s clear, isn’t it, that the UK homebuilding sector faces formidable challenges. The rising tide of labour costs, the unpredictable currents of material prices, and the seismic shifts demanded by new environmental regulations are collectively pushing up the cost of building homes. This isn’t just a blip; it’s a fundamental recalibration of the industry, a new normal where efficiency, sustainability, and technological adoption are no longer optional extras but core competencies.
Yet, within these challenges lie significant opportunities. For builders willing to innovate, to invest in new techniques like Modern Methods of Construction, and to prioritise skills development, there’s a chance to emerge stronger, more resilient, and more competitive. Homes that are truly energy-efficient aren’t just a regulatory necessity; they’re increasingly what consumers want. People are looking for properties with lower running costs, and they understand the long-term value of a home that’s built for the future. The initial higher build cost might be a hurdle, but the appeal of reduced energy bills, a warmer home, and a smaller carbon footprint is a powerful selling point.
Perhaps the biggest opportunity lies in shifting the narrative. Instead of viewing these increased costs purely as a burden, we can frame them as an investment in quality, sustainability, and long-term value. Building a home that’s fit for the future, one that actively contributes to our net-zero ambitions, is a compelling proposition, both economically and ethically. It’s going to be a tough few years, no doubt, but the industry has always shown a remarkable capacity for adaptation. I’m optimistic that with foresight and ingenuity, UK homebuilders won’t just weather this storm, but actually come out building better, more sustainable homes than ever before.
That 12% increase by 2030? Sounds like a bargain if you ask me! Has anyone considered building upwards? We could all be living in stylish towers, sipping tea, and laughing at ground-level cost increases. More seriously, how will these cost increases affect rural communities, particularly affordability?
Thanks for the comment! Building upwards is definitely part of the solution, especially in urban areas. I agree we need to think about affordability in rural communities. The cost increases could disproportionately affect them, potentially limiting access to new housing and impacting local economies. How can we ensure sustainable growth?
Editor: FocusNews.Uk
Thank you to our Sponsor Focus 360 Energy
The projection of a 12% cost increase underscores the need for innovative solutions. Modern Methods of Construction (MMC), particularly offsite manufacturing, could provide a pathway to mitigating rising costs through improved efficiency and reduced waste. How can we accelerate the adoption of MMC in the UK?
Absolutely! The 12% increase does put pressure on the industry to adapt. I’m with you on MMC playing a key role. What incentives do you think would encourage more homebuilders to invest in offsite manufacturing facilities or partner with existing MMC providers?
Editor: FocusNews.Uk
Thank you to our Sponsor Focus 360 Energy
The projected 15% increase in material costs over the next five years is concerning. How much of this increase is attributable to the rising demand for sustainable materials, and what measures can be implemented to make these options more financially accessible for builders?
That’s a great point! The shift to sustainable materials is a key factor. While it’s difficult to give a precise percentage, demand is certainly driving up prices. Government incentives like tax breaks or subsidies could make these materials more accessible. Perhaps grants could be awarded for builders using sustainable products. What are your thoughts?
Editor: FocusNews.Uk
Thank you to our Sponsor Focus 360 Energy
£2,557 extra for basic compliance with the Future Homes Standard? Does that include the cost of the existential dread knowing I’ll never afford a home with a garden big enough for a decent barbecue? Seriously though, are there grants to help with these initial expenses?
Thanks for raising the question about grants! It’s a worry for many. While there aren’t widespread grants *specifically* for FHS compliance right now, some local authorities offer funding for energy efficiency upgrades. Checking with them, or with organizations like the Energy Saving Trust, might be worthwhile to see if any support is available for new builds. It’s vital that these greener homes don’t become unaffordable.
Editor: FocusNews.Uk
Thank you to our Sponsor Focus 360 Energy
Given the predicted labour cost increases, what innovative workforce development strategies, beyond apprenticeships, might help to address the looming skills gap and mitigate the impact on construction timelines and overall project costs?
That’s a critical question! Beyond apprenticeships, encouraging experienced tradespeople to mentor new entrants through structured programs could be invaluable. Also, partnering with colleges to tailor courses to meet specific construction needs could ensure graduates have the practical skills required on site, closing the skills gap faster. What do you think?
Editor: FocusNews.Uk
Thank you to our Sponsor Focus 360 Energy
The emphasis on strategic planning and design innovation is vital. Integrating BIM from the outset allows for comprehensive clash detection and optimization, potentially mitigating rising material costs through efficient design and waste reduction.
Absolutely! The point about BIM integration is spot on. Early clash detection can save significant costs. Plus, advanced design software lets us explore alternative layouts and material choices virtually, optimizing for both budget and sustainability before a single brick is laid. It really is the future! What other tech can help?
Editor: FocusNews.Uk
Thank you to our Sponsor Focus 360 Energy
That 18% labour cost increase by 2030? Ouch! Makes you wonder if we’ll all be living in self-assembled, flat-pack houses ordered online. I’d like to know if any builders are offering courses on how to assemble these, for a discount, of course.
That’s a funny image! The flat-pack house concept is interesting and could address costs. Assembling these houses requires a different skillset. Builders teaching assembly could future-proof their businesses and offer a unique service. I wonder what specific skills are needed for this type of construction?
Editor: FocusNews.Uk
Thank you to our Sponsor Focus 360 Energy