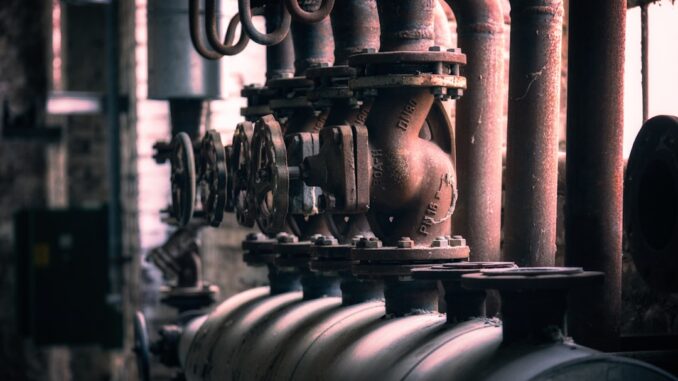
A Comprehensive Analysis of Central Heating Systems: Technologies, Historical Development, Efficiencies, Installation Costs, Maintenance, and System Sizing
Many thanks to our sponsor Focus 360 Energy who helped us prepare this research report.
Abstract
Central heating systems represent a cornerstone of modern residential and commercial infrastructure, having undergone profound transformations from rudimentary localized heat sources to highly sophisticated, integrated climate control solutions. This comprehensive report meticulously examines the diverse array of technologies employed in contemporary central heating, including the nuanced operational principles of forced-air furnaces, the robust performance of hydronic boiler systems, the pervasive comfort of radiant heating, and the remarkable energy transference capabilities of heat pumps. Beyond mere technological description, the analysis delves deeply into their intricate historical development, tracing their evolution from ancient innovations to their current state of advanced engineering. A critical evaluation of comparative efficiencies, employing industry-standard metrics such as Annual Fuel Utilization Efficiency (AFUE) and Coefficient of Performance (COP), is presented to highlight economic and environmental implications. Furthermore, the report provides an exhaustive breakdown of installation complexities, associated costs, and the indispensable maintenance regimens required for optimal performance and longevity. A significant focus is placed on the scientific principles underpinning accurate system sizing, considering a multitude of factors including building envelope characteristics, localized climate zones, and internal heat gains. By offering an unparalleled depth of insight into these multifaceted systems, this report aims to furnish professionals, researchers, and policymakers with a definitive understanding of the principles, practices, and future trajectory of whole-home heating.
Many thanks to our sponsor Focus 360 Energy who helped us prepare this research report.
1. Introduction
The provision of consistent, comfortable indoor temperatures has been a persistent human endeavor throughout history, profoundly shaping architectural design, settlement patterns, and quality of life. The evolution of central heating systems marks a pivotal achievement in this quest, transitioning from localized, inefficient heating methods to integrated, highly efficient solutions that distribute warmth evenly across entire structures. This transformative journey has not only enhanced residential and commercial comfort but has also significantly impacted global energy consumption patterns, indoor air quality, and the very fabric of urban development. The contemporary landscape of central heating is characterized by a rich tapestry of technologies, each with distinct operational mechanisms, advantages, and challenges, driven by an escalating demand for energy efficiency, reduced environmental footprint, and enhanced occupant comfort.
This report embarks on an exhaustive examination of central heating systems, meticulously dissecting their technological underpinnings, tracing their complex historical progression, and rigorously evaluating their efficiency metrics. It provides a detailed exposition of the multifaceted considerations involved in their installation and ongoing maintenance, offering crucial insights into the financial and operational implications for homeowners and industry stakeholders alike. A central tenet of this analysis is the critical aspect of system sizing, an often-underestimated factor that profoundly influences system performance, energy consumption, and longevity. The interplay between building characteristics, regional climate conditions, and occupant needs necessitates a precise, data-driven approach to sizing. Through this in-depth exploration, the report seeks to provide a definitive reference for understanding the complexities and future directions of central heating, contributing to more informed decision-making in the realms of building design, energy policy, and consumer choice.
Many thanks to our sponsor Focus 360 Energy who helped us prepare this research report.
2. Historical Development of Central Heating Systems
The trajectory of central heating systems is a compelling narrative of human ingenuity driven by the fundamental need for warmth and comfort, evolving from rudimentary localized fires to sophisticated networked climate control. Early civilizations grappled with the challenge of heating enclosed spaces, primarily relying on open fires within dwellings, which, while providing warmth, were inefficient, produced significant smoke, and posed considerable fire hazards. The advent of the brazier and later rudimentary stoves marked incremental improvements, allowing for better control of combustion and some redirection of heat, albeit still confined to individual rooms.
2.1 Ancient Innovations: The Roman Hypocaust System
A significant leap forward occurred with the Roman Empire’s introduction of the hypocaust system, a remarkable feat of ancient engineering dating back to at least the 1st century BCE. This innovative system, primarily utilized in public baths (thermae) and aristocratic villas, involved creating an elevated floor supported by pillars (pilae stacks). Hot air and smoke, generated by a furnace (praefurnium) located outside the main structure, were channeled through the space beneath the floor and often through flues within the walls. This radiated heat upwards, warming the floor and walls, thus heating the entire room or complex from below. The hypocaust system effectively separated combustion byproducts from the living space, a crucial advancement in indoor air quality. Its operational principles, particularly the concept of radiant heat distribution and a centralized heat source, laid foundational groundwork for future hydronic and radiant heating technologies, demonstrating an early understanding of heat transfer mechanisms (Smith, 2018).
2.2 Medieval and Pre-Industrial Advancements
Following the decline of the Roman Empire, sophisticated heating technologies largely receded in Europe, with most buildings reverting to simpler fireplaces and braziers. However, innovations continued in different forms. In medieval monasteries and castles, large central fireplaces or kilns might heat adjacent rooms through shared masonry, a precursor to modern central chimney systems. In some cases, heated air was ducted from large stoves to different rooms, anticipating forced-air concepts. By the 17th and 18th centuries, cast-iron stoves became more prevalent, offering improved efficiency over open hearths, but still largely serving individual rooms. The significant constraint remained the lack of effective means to distribute heat uniformly across an entire large structure without extensive manual intervention.
2.3 The Industrial Revolution and the Rise of Steam and Hot Water Heating
The true genesis of modern central heating systems coincided with the Industrial Revolution in the 18th and 19th centuries. The burgeoning industrial capacity, coupled with advances in metallurgy and boiler technology, made large-scale heat generation and distribution feasible. Early pioneers, such as the Scottish inventor James Watt, contributed to steam engine technology, which indirectly spurred developments in steam heating.
One of the most significant breakthroughs came in the mid-19th century with the widespread adoption of steam and hot water boilers. Angier March Perkins, an American inventor, is credited with developing a high-pressure hot water heating system in the 1830s, allowing water to circulate at higher temperatures without boiling, suitable for larger buildings. Later, innovations in cast-iron radiators, like those patented by Joseph Nason and Stephen J. Gold in the United States in the 1860s, provided effective heat emitters, replacing cumbersome and less efficient pipe coils. These systems used a central boiler to heat water or generate steam, which then circulated through pipes to radiators located in various rooms, releasing heat through convection and radiation. This marked the shift from heating individual rooms to heating entire buildings from a single, centralized source. Coal was the predominant fuel source, driving the expansion of these systems in commercial buildings, public institutions, and eventually, larger residential properties (Smith, 2018).
2.4 The 20th Century: Forced-Air and the Quest for Efficiency
The early 20th century witnessed further diversification and refinement of central heating technologies. The development of electric motors and blowers paved the way for forced-air furnace systems. These systems gained popularity, particularly in North America, due to their ability to provide rapid heating and, crucially, their ease of integration with newly emerging air conditioning systems. This dual functionality offered a complete climate control solution within a single ductwork infrastructure. Natural gas and fuel oil became increasingly common fuel sources, displacing coal due to their cleaner combustion and ease of delivery.
The latter half of the 20th century saw a heightened focus on energy efficiency, spurred by energy crises and growing environmental awareness. This period saw the introduction of higher-efficiency furnaces with improved heat exchangers and electronic ignition, replacing less efficient standing pilot lights. Concurrently, the concept of the heat pump, based on the refrigeration cycle, began to gain traction. Though theoretical principles had existed for decades, practical application for residential heating and cooling became viable with technological advancements. The 1970s and 1980s were key for the development of air-source heat pumps, offering an electric alternative to fossil fuels for heating and, uniquely, providing cooling capability from the same unit (U.S. Department of Energy, 2020).
2.5 Contemporary Trends and Future Directions
The 21st century has brought a strong emphasis on sustainability, smart technology integration, and diversified energy sources. High-efficiency condensing furnaces and boilers, capable of capturing latent heat from exhaust gases, have become standard. Geothermal heat pumps, utilizing the stable temperature of the earth, have emerged as highly efficient alternatives. The integration of central heating with smart home technologies allows for advanced programming, remote control, and energy optimization. Furthermore, renewable energy sources such as solar thermal for hot water systems, and biomass boilers, are increasingly being explored and adopted, pointing towards a future where central heating is not only comfortable and efficient but also environmentally sustainable (International Energy Agency, 2019).
Many thanks to our sponsor Focus 360 Energy who helped us prepare this research report.
3. Technologies in Central Heating Systems
Central heating systems encompass a diverse array of technologies, each distinguished by its fundamental mechanism for generating and distributing heat. The choice among these systems hinges on a myriad of factors, including initial capital outlay, long-term operational costs, desired comfort levels, existing infrastructure, and environmental considerations. This section provides a detailed exploration of the primary central heating technologies.
3.1 Forced-Air Furnaces
Forced-air furnaces represent one of the most prevalent central heating systems, particularly in North America, owing to their cost-effectiveness, rapid heating capabilities, and seamless integration with air conditioning systems. The fundamental principle involves heating air in a central unit and subsequently distributing this warmed air throughout the building via a network of ducts and vents.
3.1.1 Operational Mechanism and Components
A typical forced-air furnace comprises several key components:
* Burner: For gas or oil furnaces, this is where the fuel is ignited. Electric furnaces use heating elements.
* Heat Exchanger: This is a critical component where the heat generated by the burner is transferred to the circulating air without mixing the combustion byproducts with the breathable air. The integrity of the heat exchanger is paramount for safety.
* Blower Motor and Fan: This motor draws air from return ducts, pushes it over the heated heat exchanger, and then forces the warmed air into the supply ducts.
* Ductwork: A system of metal or flexible ducts transports the heated air to various rooms via supply registers and draws cooler air back to the furnace via return grilles.
* Filter: Situated in the return air path, the filter traps dust, pollen, and other airborne particles, protecting the furnace components and improving indoor air quality. Regular filter replacement is crucial.
* Flue/Vent Pipe: Carries combustion byproducts safely out of the home.
3.1.2 Fuel Types and Efficiency
Forced-air furnaces are most commonly fueled by natural gas, propane, or fuel oil. Electric furnaces are also available but tend to be less efficient in terms of energy cost per BTU in many regions, as electricity generation often involves significant losses. Modern gas and oil furnaces often achieve high Annual Fuel Utilization Efficiency (AFUE) ratings, with condensing models reaching upwards of 95-98%. These high-efficiency units extract additional heat by condensing water vapor from the exhaust gases, necessitating a condensate drain (Doe & Johnson, 2020).
3.1.3 Advantages and Disadvantages
Advantages:
* Rapid Heating: Air heats up and circulates quickly, providing almost immediate comfort.
* Integration with HVAC: The same ductwork can be utilized for both heating and cooling, making it a cost-effective solution for comprehensive climate control.
* Air Filtration: Integrated filtration systems improve indoor air quality by removing particulates. Advanced filters (MERV ratings) can significantly enhance this.
* Humidification/Dehumidification: Can easily integrate with humidifiers or dehumidifiers to control indoor humidity levels.
* Zoning Capability: Can be zoned with dampers in ductwork to allow different temperatures in different areas, though this adds complexity and cost.
Disadvantages:
* Ductwork Requirements: Requires extensive ductwork, which can be costly to install in existing homes without it, and can be prone to energy loss through leaks.
* Airborne Allergens: While filters help, the forced circulation can distribute allergens, dust, and pet dander if filters are not regularly changed or if ductwork is not cleaned.
* Noise: Blower operation can generate noise, particularly if ducts are undersized or uninsulated.
* Drying Effect: Can sometimes lead to drier indoor air, necessitating humidification in dry climates.
3.2 Boilers (Hydronic Systems)
Boilers form the heart of hydronic heating systems, which utilize water (or sometimes steam) as the heat transfer medium. These systems are renowned for their consistent, even heat distribution, durability, and often superior comfort compared to forced-air systems.
3.2.1 Operational Mechanism and Components
A boiler heats water to a desired temperature (typically 140-180°F or 60-82°C for hot water systems, or converts it to steam for steam systems) using natural gas, oil, or electricity. This heated fluid is then circulated through a closed loop of pipes to heat emitters located in various rooms. Key components include:
* Burner/Heat Exchanger: Similar to furnaces, this is where fuel is combusted and heat is transferred to the water.
* Circulator Pump: For hot water systems, this pump moves the heated water through the pipes to the heat emitters and back to the boiler.
* Expansion Tank: Accommodates the expansion of water as it heats up, preventing excessive pressure buildup in the closed system.
* Pressure Relief Valve: A safety device that releases water if pressure exceeds a safe limit.
* Heat Emitters: These include cast-iron radiators, baseboard heaters, or radiant floor tubing, which transfer heat to the room through convection and radiation.
* Piping: A network of pipes carries the hot water or steam to and from the heat emitters.
* Vent/Chimney: For combustion boilers, exhausts byproducts safely outdoors.
3.2.2 Types of Boilers and Fuel Sources
- Hot Water Boilers: Most common residential type. Operate at lower temperatures and pressures than steam systems. Can be condensing or non-condensing.
- Steam Boilers: Historically common, particularly in older buildings. Operate at higher temperatures and pressures, generating steam that rises through pipes to radiators. More complex to manage and less efficient than modern hot water systems, often requiring traps to return condensate.
Boilers can be fueled by natural gas, propane, fuel oil, or electricity. High-efficiency condensing boilers, like condensing furnaces, recover latent heat from exhaust gases, achieving AFUE ratings well over 90% (Doe & Johnson, 2020).
3.2.3 Advantages and Disadvantages
Advantages:
* Consistent, Even Heat: Hydronic systems provide a gentle, even heat that minimizes temperature fluctuations and cold spots, often described as a ‘warm blanket’ effect.
* Quiet Operation: Absence of noisy blowers and ductwork makes boilers inherently quieter.
* Improved Indoor Air Quality: No forced air circulation means less distribution of dust, allergens, and airborne particles.
* Longevity and Durability: Boilers and their components are typically very robust and can last for decades with proper maintenance.
* Zoning Simplicity: Zoning is inherently simpler and more precise by controlling water flow to individual loops or radiators.
* Domestic Hot Water Integration: Many modern boilers (combi-boilers) can also provide on-demand domestic hot water, eliminating the need for a separate water heater.
Disadvantages:
* Slow Response Time: Water takes longer to heat up and radiate heat, leading to a slower response time compared to forced-air systems.
* Higher Upfront Costs: Installation costs can be higher, especially for extensive piping or if radiators need to be added to a home without existing hydronic infrastructure.
* No Integrated Cooling: Boilers only provide heating. A separate system (e.g., mini-splits or central air conditioning with its own ductwork) is required for cooling.
* Potential for Leaks: Though rare in well-maintained systems, leaks in pipes or radiators can cause water damage.
* Space Requirements: Boilers, especially older models, can be bulky and require dedicated space.
3.3 Radiant Systems
Radiant heating systems deliver heat directly to objects and surfaces in a room, primarily through infrared radiation, rather than heating the air itself. This results in an exceptionally comfortable and uniform heat distribution, mimicking the feeling of warmth from the sun.
3.3.1 Operational Mechanism and Types
Radiant systems work by heating large surfaces, typically floors, but also walls and ceilings, which then radiate energy to the occupants and other objects in the room. The air temperature can often be lower than in forced-air systems while still maintaining a comfortable feel, contributing to energy savings. There are two primary types:
- Hydronic Radiant Systems: These are the most common and efficient. They involve circulating heated water (typically from a boiler) through a network of durable, flexible tubing (e.g., PEX-a) embedded within the floor slab (wet installations), beneath a subfloor (dry installations), or within wall/ceiling panels. The warm water heats the mass of the floor, which then radiates heat upwards.
- Electric Radiant Systems: These use electric heating cables or mats embedded in thin-set mortar under flooring materials (e.g., tile, laminate). While simpler to install and effective for small areas like bathrooms, they are generally more expensive to operate for whole-house heating due to higher electricity costs.
3.3.2 Installation Methods
- Wet Installations: Tubing is embedded directly into a concrete slab (common for new construction or basements) or a thin layer of concrete (grout or gypsum overlay) over a subfloor. This provides excellent thermal mass but has a slower response time.
- Dry Installations: Tubing is installed in grooved panels (e.g., aluminum plates) placed between or on top of subfloor joists. These have less thermal mass, leading to faster response times but potentially slightly less stable temperatures.
- Wall/Ceiling Panels: Less common for primary heating, but specialized panels with embedded tubing or electric elements can be used for supplemental heat.
3.3.3 Advantages and Disadvantages
Advantages:
* Superior Comfort: Provides very even, gentle heat without hot or cold spots. Warm floors are a significant comfort benefit.
* Exceptional Indoor Air Quality: No forced air movement means no circulation of dust, allergens, or pollutants.
* Quiet Operation: Completely silent, as there are no fans or blowers.
* Aesthetic Appeal: No visible registers, radiators, or baseboards, offering complete design freedom.
* Energy Efficiency: Can be highly efficient as they heat occupants directly rather than heating large volumes of air, allowing for lower thermostat settings.
Disadvantages:
* High Installation Costs: Significant upfront investment, particularly for hydronic systems and wet installations, which often involve extensive labor and material costs. Retrofitting can be challenging and expensive.
* Slow Response Time: Due to the thermal mass, it takes longer for the system to heat up and respond to temperature changes. This makes programmable setbacks less effective unless managed carefully.
* Repair Difficulty: If a leak occurs in an embedded system, locating and repairing it can be very disruptive and costly.
* No Integrated Cooling: Like boilers, radiant systems are heating-only. Separate systems are required for cooling.
* Floor Coverings: Certain floor coverings (e.g., thick carpets) can impede heat transfer, reducing efficiency and comfort.
3.4 Heat Pumps
Heat pumps are a highly versatile and energy-efficient technology capable of providing both heating and cooling from a single unit. Unlike furnaces or boilers that generate heat by burning fuel, heat pumps transfer heat, moving it from one location to another.
3.4.1 Operational Mechanism (Refrigeration Cycle)
Heat pumps operate on the same thermodynamic principles as refrigerators and air conditioners, utilizing a refrigeration cycle. They contain refrigerant that circulates through a closed loop of coils, absorbing and releasing heat as it changes state between liquid and gas.
- Heating Mode: In heating mode, the heat pump extracts heat from a source (outside air, ground, or water) even in cold temperatures. The refrigerant absorbs this low-grade heat, then passes through a compressor, which increases its temperature and pressure. This superheated vapor then moves to the indoor coil (condenser), where it releases its heat to the indoor air (or water for hydronic heat pumps). The now-cooler refrigerant expands, drops in pressure, and returns to the outdoor coil (evaporator) to absorb more heat, completing the cycle.
- Cooling Mode: The cycle reverses. Heat is absorbed from the indoor air by the indoor coil and released to the outside air (or ground/water) by the outdoor coil.
3.4.2 Types of Heat Pumps
- Air-Source Heat Pumps (ASHPs): The most common type. They transfer heat between the indoor air and the outdoor air. Modern ASHPs, especially cold-climate models, can operate effectively in temperatures well below freezing (down to -15°F or -26°C or lower), significantly improving performance in colder regions.
- Ground-Source Heat Pumps (GSHPs) / Geothermal Heat Pumps: These systems transfer heat between the indoor air and the earth, utilizing the stable underground temperatures. They are highly efficient because ground temperatures are much more consistent than air temperatures, reducing the work the heat pump needs to do. Installation involves burying a loop of pipes horizontally or vertically in the ground.
- Water-Source Heat Pumps: Similar to GSHPs, but they extract heat from a nearby body of water (e.g., lake, well) or a dedicated closed-loop water system.
- Mini-Split Heat Pumps: Ductless versions of air-source heat pumps, ideal for zoning or heating/cooling additions or specific rooms without ductwork.
3.4.3 Performance Metrics: COP and HSPF
- Coefficient of Performance (COP): A fundamental efficiency metric for heat pumps. It is the ratio of heating or cooling output to electrical energy input. A COP of 3.0 means the heat pump delivers three units of heat energy for every unit of electrical energy consumed. COPs typically range from 2.5 to 5.0 or higher. Unlike AFUE, COP can exceed 100% because heat pumps are moving existing heat, not generating it from combustion.
- Heating Seasonal Performance Factor (HSPF): Similar to AFUE, HSPF is a seasonal energy efficiency rating for the heating mode of air-source heat pumps. It measures the total heating output over a typical heating season divided by the total electric energy consumed during the same period. Higher HSPF values indicate greater efficiency (U.S. Department of Energy, 2020).
3.4.4 Advantages and Disadvantages
Advantages:
* High Energy Efficiency: Can be significantly more efficient than conventional heating systems, especially ground-source heat pumps, leading to substantial energy cost savings.
* Dual Functionality: Provides both heating and cooling from a single unit, eliminating the need for separate systems.
* Environmental Benefits: Reduces carbon emissions compared to fossil fuel-based heating by consuming less primary energy.
* Versatility: Available in ducted (central) and ductless (mini-split) configurations, offering flexible installation options.
* Rebate Eligibility: Often qualify for government rebates and tax credits due to their energy efficiency.
Disadvantages:
* Higher Initial Cost: Upfront installation costs, particularly for ground-source systems due to excavation, can be considerably higher than furnaces or boilers.
* Performance in Extreme Cold (Air-Source): While modern ASHPs perform well in cold climates, their efficiency and heating capacity can decrease significantly as outdoor temperatures drop below certain thresholds, sometimes requiring supplemental electric resistance heat (known as ‘auxiliary heat’) or a hybrid fossil fuel furnace.
* Defrost Cycle: Air-source heat pumps periodically enter a defrost cycle in cold, humid conditions to remove ice buildup on the outdoor coil, during which auxiliary heat may be used.
* Noise (Outdoor Unit): The outdoor unit of an air-source heat pump can generate some noise during operation.
3.5 Emerging and Niche Central Heating Technologies
While forced-air, hydronic, radiant, and heat pump systems dominate the central heating landscape, other technologies are gaining traction or serve specific niche applications, often emphasizing renewable energy or higher efficiency.
3.5.1 Biomass Boilers
Biomass boilers burn organic matter such as wood pellets, chips, or agricultural waste to produce heat for hydronic systems. They are considered carbon-neutral if the biomass is harvested sustainably. While common in rural areas or for those with access to sustainable fuel sources, they require fuel storage and regular ash removal.
3.5.2 Solar Thermal Systems
Solar thermal systems use collectors to absorb sunlight and heat a fluid (water or a heat transfer fluid). This heated fluid can then directly contribute to domestic hot water supply or supplement a central heating system, typically a hydronic one. While highly sustainable and effective for pre-heating, they usually require a conventional backup system for periods of low solar insolation or high demand.
3.5.3 Combined Heat and Power (CHP) / Cogeneration
CHP systems, common in larger commercial or industrial settings but increasingly found in micro-CHP residential units, generate both electricity and useful heat from a single fuel source (e.g., natural gas). The heat that would otherwise be wasted during electricity generation is captured and used for space heating or domestic hot water. This significantly increases overall energy efficiency but involves complex systems and higher upfront costs.
Many thanks to our sponsor Focus 360 Energy who helped us prepare this research report.
4. Comparative Efficiencies and Performance Metrics
Evaluating the efficiency of central heating systems is paramount for understanding their long-term operational costs, environmental impact, and contribution to energy conservation. Different technologies utilize distinct metrics to quantify their performance, reflecting their unique operational principles and energy transformations. It is crucial to interpret these metrics in the context of real-world operating conditions.
4.1 Annual Fuel Utilization Efficiency (AFUE)
For furnaces and boilers that combust fossil fuels (natural gas, propane, oil) or use electric resistance heating, the primary efficiency metric is the Annual Fuel Utilization Efficiency (AFUE) rating. AFUE is a percentage that represents the ratio of annual heat output to the annual fossil fuel energy consumed, factoring in standby losses, cyclic losses, and off-cycle losses. It essentially indicates how much of the fuel’s energy is converted into usable heat for the living space over a typical heating season. The remaining percentage is lost through the flue gases or other inefficiencies.
-
Standard AFUE Ranges:
- Older, conventional furnaces (1970s-1980s) might have AFUE ratings as low as 60-70%.
- Mid-efficiency furnaces (non-condensing, often with power vents) typically range from 80-83% AFUE. These systems vent combustion gases directly up a flue.
- High-efficiency condensing furnaces and boilers achieve AFUE ratings of 90% and above, commonly reaching 95-98%. These units employ a secondary heat exchanger that extracts additional heat by cooling combustion gases below their dew point, causing water vapor to condense and release its latent heat. This requires a condensate drain and often PVC venting (Doe & Johnson, 2020).
-
Limitations of AFUE: While a crucial comparative tool, AFUE is determined under standardized laboratory conditions. Real-world performance can be influenced by:
- Installation Quality: Improper ductwork, poor sealing, or incorrect sizing can drastically reduce efficiency.
- Maintenance: Clogged filters, dirty burners, or uncalibrated controls decrease performance.
- Climate and Operating Conditions: AFUE assumes typical cycling, but very cold climates might lead to extended run times where the furnace operates closer to its steady-state efficiency, or mild climates might lead to more short cycling, reducing overall efficiency.
- Duct Losses: AFUE only accounts for the furnace’s efficiency, not the heat lost through uninsulated or leaky ductwork, which can be substantial (American Society of Heating, Refrigerating and Air-Conditioning Engineers (ASHRAE), 2017).
4.2 Heat Pump Performance Metrics: COP and HSPF
Heat pumps, as mentioned, do not generate heat but transfer it. Their efficiency is measured differently:
-
Coefficient of Performance (COP): As defined earlier, COP is the ratio of useful heat output (or cooling output) to the electrical energy input. It’s a snapshot efficiency at a given operating condition (e.g., outdoor temperature). A COP of 3.0 means for every 1 unit of electricity consumed, 3 units of heat energy are delivered. This ‘over 100%’ efficiency (relative to electrical input) is why heat pumps are so energy-efficient compared to electric resistance heating (where COP is always 1.0).
-
Heating Seasonal Performance Factor (HSPF): HSPF is the total heating output of an air-source heat pump over a typical heating season divided by the total electricity consumed during the same period. It provides a more comprehensive measure of seasonal heating efficiency for heat pumps, similar to AFUE for furnaces. Higher HSPF values indicate greater efficiency. Modern ASHPs typically have HSPF ratings ranging from 7.0 to 13.0 or higher. Cold-climate ASHPs are designed to maintain higher HSPF values even in very low outdoor temperatures (U.S. Department of Energy, 2020).
4.3 Cooling Performance Metrics: SEER and EER
For systems that also provide cooling (like central air conditioners and heat pumps in cooling mode), additional metrics are relevant:
-
Seasonal Energy Efficiency Ratio (SEER): Measures the cooling output over a typical cooling season divided by the total electrical energy input during the same period. Higher SEER ratings indicate greater cooling efficiency. Minimum SEER ratings are mandated by regulatory bodies (e.g., 14-15 SEER in the US, depending on region and system type).
-
Energy Efficiency Ratio (EER): Measures the cooling output divided by electrical power input at a specific operating condition (e.g., 95°F outdoor temperature). EER is a snapshot, while SEER reflects seasonal performance.
4.4 System Efficiency vs. Component Efficiency
It is crucial to differentiate between the efficiency rating of the heating equipment itself (e.g., AFUE, HSPF) and the overall efficiency of the entire heating system as it operates within a building. Many factors beyond the equipment’s rating influence real-world energy consumption:
- Building Envelope: Insulation levels in walls, roofs, floors, and the quality of windows and doors significantly impact heat loss. A highly efficient furnace in a poorly insulated house will still consume substantial energy.
- Air Leakage (Infiltration): Uncontrolled air leakage through cracks, gaps, and penetrations in the building envelope can account for a significant portion of heat loss, bypassing the heating system entirely.
- Ductwork/Piping Losses: Leaky or uninsulated ducts/pipes can lose a substantial amount of conditioned air/heat before it reaches the intended space. Studies show duct leakage can reduce system efficiency by 20-30% in some cases (National Renewable Energy Laboratory (NREL), 2021).
- Thermostat Control and Occupant Behavior: Inefficient thermostat settings (e.g., excessively high temperatures, no setbacks) or poor zoning practices can negate the benefits of high-efficiency equipment.
- Maintenance Practices: Neglecting regular maintenance (e.g., dirty filters, uncleaned coils, uncalibrated burners) leads to degraded performance over time.
4.5 Energy Conservation Measures and Efficiency Enhancement
Maximizing overall heating system efficiency involves a holistic approach that combines high-performance equipment with building envelope improvements and smart controls:
- Insulation Upgrades: Improving insulation in attics, walls, and basements reduces heat loss significantly.
- Air Sealing: Sealing air leaks around windows, doors, electrical outlets, and penetrations dramatically reduces infiltration.
- Window and Door Upgrades: Installing high-performance, low-emissivity (low-e) windows and well-sealed doors minimizes heat transfer.
- Duct Sealing and Insulation: Sealing all joints and insulating ducts, especially those in unconditioned spaces (attics, crawlspaces), prevents significant heat loss.
- Programmable and Smart Thermostats: These devices allow for automated temperature setbacks when occupants are away or asleep, and smart thermostats can learn occupancy patterns and integrate with weather forecasts to optimize operation, leading to significant energy savings (Brown & Green, 2019).
Many thanks to our sponsor Focus 360 Energy who helped us prepare this research report.
5. Installation Costs and Maintenance Requirements
The decision-making process for selecting a central heating system is profoundly influenced by the financial implications spanning initial installation and long-term operational and maintenance expenses. These costs vary widely based on the chosen technology, system size, complexity of installation, regional labor rates, and the specific characteristics of the building, particularly whether it is new construction or an existing property requiring retrofitting.
5.1 Installation Costs
Installation costs encompass more than just the price of the primary heating unit. They include associated equipment (e.g., ductwork, piping, radiators, registers), labor for skilled technicians, necessary modifications to the building’s electrical or gas lines, chimney or venting requirements, permits, and finishing work.
5.1.1 Forced-Air Furnaces
- Cost Range: Generally among the lower upfront cost options. For a standard residential replacement, costs typically range from $3,000 to $7,000 for the unit and installation. High-efficiency condensing furnaces can push this towards $6,000 to $10,000 or more.
- Factors Influencing Cost:
- AFUE Rating: Higher efficiency units are more expensive initially.
- Furnace Type: Single-stage, two-stage, or modulating furnaces (with variable speed blowers) impact cost and comfort.
- Ductwork: If new ductwork is required (e.g., in a home converting from radiant heat), costs can significantly increase ($5,000 to $15,000+).
- Electrical/Gas Line Upgrades: Older homes may require electrical panel upgrades for modern furnaces or new gas line runs.
- Venting: High-efficiency condensing furnaces require PVC venting and a condensate drain, which might involve additional labor and material costs compared to traditional metal flues.
5.1.2 Boilers (Hydronic Systems)
- Cost Range: Generally higher than forced-air furnaces, especially if new piping and emitters are required. A typical boiler replacement might cost $4,000 to $9,000. Installing a new hydronic system in a home without existing infrastructure, including piping and radiators/baseboard heaters, can range from $10,000 to $25,000 or more, depending on home size and complexity.
- Factors Influencing Cost:
- Boiler Type: High-efficiency condensing boilers are more expensive than conventional models.
- Emitters: Cast-iron radiators are typically more expensive than baseboard heaters, and their installation is more labor-intensive.
- Piping: Extensive copper or PEX piping runs add to material and labor costs.
- System Complexity: Zoning systems, integration with indirect water heaters, or snowmelt systems increase cost.
- Old System Removal: Removal and disposal of old cast-iron radiators or steam pipes can add to labor.
5.1.3 Radiant Systems
- Cost Range: Among the most expensive to install, particularly hydronic radiant floor heating with wet installations. Costs can range from $8 to $20 per square foot for the heated area, translating to tens of thousands of dollars for a whole house. Electric radiant mats are less expensive per square foot for material but more costly to operate for large areas.
- Factors Influencing Cost:
- Installation Method: Wet concrete slab installations (new construction) are generally less disruptive but more material-intensive than dry installations (retrofit).
- Floor Covering: Some floor types require specific installation techniques or thicker overlays.
- Manifolds and Controls: Zoning manifold systems and sophisticated controls add to cost.
- Boiler Integration: Requires a boiler for hydronic systems; the cost of the boiler itself is separate.
- Retrofitting: Significantly more expensive and disruptive to retrofit into an existing home, often requiring floor removal or extensive subfloor work.
5.1.4 Heat Pumps
- Cost Range:
- Air-Source Heat Pumps: Unit and installation can range from $4,000 to $12,000 for ducted systems, often comparable to or slightly higher than high-efficiency furnaces. Cold-climate models may be at the higher end. Ductless mini-splits typically range from $2,000 to $6,000 per indoor unit, depending on capacity and complexity.
- Ground-Source Heat Pumps: Substantially higher initial investment due to the cost of drilling or excavation for the ground loop. Total installed costs can range from $18,000 to $40,000 or more, depending on system size, ground loop type (horizontal vs. vertical), and soil conditions.
- Factors Influencing Cost:
- Type of Heat Pump: GSHPs are significantly more expensive than ASHPs.
- Ground Loop Installation (GSHP): Drilling vertical boreholes is typically more expensive than horizontal trenching but requires less land.
- Ductwork/Air Handler: If new ductwork or an air handler is needed for ASHPs.
- Electrical Service Upgrades: Larger heat pumps may require higher amperage electrical service.
- Supplemental Heat: Some heat pumps require supplemental electric resistance heat for very cold days, which adds to operating costs but not typically installation cost of the heat pump itself.
- Rebates and Incentives: Crucial for offsetting the higher upfront cost of heat pumps, especially GSHPs (Brown & Green, 2019).
5.2 Maintenance Requirements
Regular and diligent maintenance is not merely about extending the lifespan of a heating system; it is fundamental to ensuring its optimal efficiency, safety, and consistent performance. Neglecting maintenance can lead to decreased energy efficiency, higher energy bills, increased risk of breakdowns, and premature system failure. Most manufacturers recommend annual professional inspections.
5.2.1 Forced-Air Furnaces
- Homeowner Maintenance:
- Filter Replacement: Critical for airflow and indoor air quality. Should be checked monthly and replaced every 1-3 months, depending on filter type, occupancy, and presence of pets.
- Clear Around Furnace: Ensure adequate clear space for airflow and safety.
- Professional Maintenance (Annually):
- Combustion Analysis: Check for proper fuel-to-air mixture and safe exhaust of combustion byproducts (carbon monoxide).
- Heat Exchanger Inspection: Check for cracks or corrosion that could lead to carbon monoxide leaks.
- Blower Motor and Fan Inspection: Lubricate motor (if applicable), clean fan blades for optimal airflow.
- Ductwork Inspection: Check for leaks, obstructions, and proper sealing.
- Ignition System Check: Ensure reliable startup.
- Thermostat Calibration: Verify accurate temperature readings.
- Flame Sensor/Pilot Light Cleaning: Ensure proper operation.
5.2.2 Boilers (Hydronic Systems)
- Homeowner Maintenance:
- Pressure Gauge Check: Monitor system pressure, ensuring it stays within recommended range (typically 12-15 psi when cold).
- Bleed Radiators: Annually, release trapped air from radiators to ensure even heat distribution.
- Visual Inspection: Check for any visible leaks around pipes or the boiler unit.
- Professional Maintenance (Annually):
- Burner and Combustion Chamber Cleaning: Remove soot and debris for efficient combustion.
- Flue Pipe Inspection: Check for corrosion, blockages, or leaks.
- Circulator Pump Inspection: Check for proper operation, noise, and leaks.
- Expansion Tank Check: Ensure proper air charge.
- Pressure Relief Valve Test: Ensure it operates correctly for safety.
- Water Quality Check (Hydronic): For closed-loop systems, ensure water chemistry is appropriate to prevent corrosion. For open systems, check for sediment.
- Anode Rod Inspection (Combi-Boilers): If providing domestic hot water, check the anode rod.
5.2.3 Radiant Systems
- Homeowner Maintenance:
- Visual Inspection of Manifolds: Check for any leaks or visible issues.
- Thermostat Monitoring: Ensure zone thermostats are functioning correctly.
- Professional Maintenance (Every 3-5 Years or as Recommended):
- Fluid Check (Hydronic): Verify pressure, pH, and corrosion inhibitor levels in the closed loop. Flush and refill if necessary.
- Manifold Inspection: Check flow meters, valves, and actuators for proper operation.
- Pump Inspection: Ensure circulator pumps are working efficiently.
- Boiler Maintenance: The boiler serving the radiant system requires its own annual maintenance as detailed above.
- Electrical System Check (Electric Radiant): Verify electrical connections and heating element integrity for electric systems.
5.2.4 Heat Pumps
- Homeowner Maintenance:
- Filter Replacement: Same as furnaces, check monthly and replace every 1-3 months.
- Clear Outdoor Unit: Keep outdoor unit clear of debris, leaves, snow, and ice to ensure proper airflow.
- Coil Cleaning (Outdoor): Periodically rinse outdoor coil to remove dirt buildup.
- Professional Maintenance (Annually):
- Refrigerant Charge Check: Verify correct refrigerant levels; low charge significantly impacts efficiency and can damage the compressor.
- Coil Cleaning (Indoor and Outdoor): Professional cleaning removes stubborn dirt and grime from evaporator and condenser coils.
- Blower Motor and Fan Inspection: Ensure proper operation and lubrication.
- Ductwork Inspection: Check for leaks and proper airflow.
- Electrical Connections: Inspect and tighten all electrical terminals.
- Defrost Cycle Operation Check: Verify proper functioning of the defrost board and sensors.
- Thermostat Calibration: Ensure accurate control.
- Reversing Valve Check: Essential for switching between heating and cooling modes.
- Ground Loop Pressure Check (GSHP): For geothermal systems, ensure loop pressure is maintained (Building Performance Institute (BPI), 2018).
Investment in regular maintenance pays dividends in terms of reduced energy consumption, extended equipment lifespan, improved comfort, and avoidance of costly emergency repairs. Many HVAC companies offer service plans that include annual tune-ups and priority service.
Many thanks to our sponsor Focus 360 Energy who helped us prepare this research report.
6. System Sizing Considerations
Proper sizing of a central heating system is arguably the single most critical factor influencing its performance, efficiency, comfort delivery, and longevity. An improperly sized system, whether oversized or undersized, will inevitably lead to suboptimal operation, increased energy consumption, and diminished occupant satisfaction. The process of accurate sizing is a complex engineering task that considers a multitude of interacting variables.
6.1 The Science of Heat Loss Calculation (Manual J)
At the core of proper heating system sizing is a meticulous heat loss calculation, a detailed analysis of how much heat a building loses under specific design conditions. The industry standard for this calculation in North America is the Air Conditioning Contractors of America’s (ACCA) Manual J, ‘Residential Load Calculation’. Manual J is not merely an estimation tool; it is a systematic methodology that accounts for every path of heat transfer into and out of a building.
The calculation considers:
* Building Envelope Characteristics:
* Wall Construction: Type of wall (e.g., wood frame, masonry), insulation R-value, sheathing, and exterior finish.
* Roof/Ceiling Construction: Roof pitch, attic ventilation, insulation R-value, and ceiling type.
* Floor Construction: Type of floor (e.g., slab on grade, framed floor over crawlspace or basement), insulation R-value, and floor covering.
* Window and Door Specifications: Crucially, their U-factor (a measure of heat transfer through the material) and Solar Heat Gain Coefficient (SHGC) for cooling loads. Number, size, and orientation of each window and door are vital.
* Exterior Surfaces: Colors and types of exterior finishes that influence solar absorption.
* Air Infiltration/Exfiltration:
* Air Leakage Rate: Measured in air changes per hour (ACH) or cubic feet per minute (CFM) at a given pressure differential (e.g., ACH50 for blower door tests). Older homes tend to be much leakier than new, tightly constructed homes. Manual J uses estimates based on construction quality or actual blower door test results.
* Cracks and Openings: Gaps around windows, doors, penetrations for pipes and wires, and structural weaknesses contribute to uncontrolled air exchange.
* Internal Heat Gains: While primarily critical for cooling load calculations, internal gains from occupants, lighting, and appliances (e.g., refrigerators, ovens) can slightly offset heating loads. Manual J accounts for these but they are less dominant for heating.
* Ventilation Requirements: Mechanical ventilation systems (e.g., HRV/ERV for indoor air quality) introduce outside air that needs to be conditioned, adding to the heating load.
* Ductwork Losses/Gains: The location of ductwork (e.g., in conditioned vs. unconditioned spaces) and its insulation and air tightness can significantly impact the effective heat delivered to the space, adding to the overall load the system must meet (White & Black, 2021).
The output of a Manual J calculation is typically expressed in British Thermal Units per hour (BTU/h), representing the maximum heating (or cooling) load the system must meet on the coldest (or hottest) design day.
6.2 Climate Zones and Design Temperatures
Regional climate conditions play an indispensable role in determining heating demands. Homes in perpetually cold climates require significantly more robust heating solutions than those in milder regions. System sizing must therefore account for localized temperature extremes and seasonal variations.
- Heating Design Temperature: This is the outdoor temperature that a heating system is designed to maintain comfort within a building. It’s not the absolute coldest temperature ever recorded, but typically a temperature that is exceeded by 99% or 97.5% of the hours during the heating season for a given location. ASHRAE provides detailed climate data for various locations, including heating design temperatures. For example, a heating design temperature of 0°F (-18°C) means the system should be able to maintain indoor comfort when the outdoor temperature is 0°F.
- Degree-Days: While not directly used for sizing, heating degree-days (HDD) provide a proxy for the severity of a heating season in a specific location, indicating the cumulative heating demand over a period. This is more useful for estimating annual energy consumption than for peak load sizing.
- Humidity: While less critical for heating, humidity levels can influence how comfortable a given air temperature feels and can play a role in certain system choices (e.g., heat pumps with dehumidification capabilities).
The climate zone impacts not only the peak load but also the choice of technology. For instance, air-source heat pumps might require supplemental heat in very cold climates where their COP significantly drops, influencing the sizing of the primary heat pump unit versus the auxiliary heating source.
6.3 Consequences of Improper System Sizing
6.3.1 Oversized Systems
An oversized heating system is one that has a BTU/h output significantly greater than the actual calculated heat loss of the building. While seemingly intuitive to opt for a larger unit ‘just in case’, oversizing leads to a cascade of negative consequences:
* Short Cycling: The system heats the space very quickly, satisfies the thermostat, and then shuts off. It then restarts shortly after. This ‘short cycling’ means the system operates inefficiently, spending more time in less efficient startup and shutdown phases.
* Increased Wear and Tear: Frequent cycling puts excessive stress on mechanical components (e.g., compressors in heat pumps, blowers in furnaces, igniters), leading to premature failure and higher maintenance costs.
* Higher Energy Consumption: Short cycling and inefficient operation translate directly to higher energy bills.
* Humidity Issues (especially with integrated AC): For forced-air systems with integrated air conditioning, short cycling prevents the system from running long enough to adequately dehumidify the air, leading to clammy indoor conditions and potential mold growth.
* Poor Air Distribution: In forced-air systems, oversized blowers can lead to noisy operation and drafts due to excessive airflow.
* Higher Upfront Cost: Larger equipment costs more to purchase and install.
6.3.2 Undersized Systems
An undersized heating system, conversely, has a BTU/h output insufficient to meet the building’s heat loss on design conditions. This also results in significant problems:
* Inability to Maintain Desired Temperatures: On the coldest days, the system will run continuously but may struggle to reach or maintain the thermostat set point, leading to occupant discomfort.
* Continuous Operation: The system operates for extended periods, leading to higher energy consumption as it constantly tries to catch up with the heat loss. This also increases wear on components.
* Premature Failure: Constant operation without adequate rest cycles can lead to overheating and premature failure of components.
* System Stress: The system is perpetually ‘fighting a losing battle,’ leading to reduced lifespan.
* Cold Spots: Insufficient heat delivery can lead to noticeable cold spots throughout the home.
6.4 The Role of Zoning Systems
While proper whole-house sizing is critical, zoning systems offer an additional layer of optimization, allowing different areas (zones) of a home to be heated (and cooled) independently to different temperatures. This significantly enhances comfort and energy efficiency.
- How Zoning Works:
- Forced-Air: Requires motorized dampers within the ductwork, controlled by separate thermostats in each zone. When a zone calls for heat, the damper opens, and the furnace/blower supplies heat to that specific area.
- Hydronic/Radiant: Achieved by installing separate thermostats and zone valves (or circulator pumps) for each heating loop or radiator. When a zone calls for heat, the valve opens, allowing hot water to flow to that specific area.
- Benefits of Zoning:
- Enhanced Comfort: Occupants can set desired temperatures for individual rooms or areas (e.g., warmer in bedrooms at night, cooler in unused rooms).
- Energy Savings: By heating only occupied areas or reducing heat to unoccupied zones (e.g., guest rooms, basements), significant energy can be saved.
- Addressing Uneven Heating: Helps mitigate issues in homes with varying heat loads due to sun exposure, window area, or insulation levels.
- Considerations:
- Cost: Adds to the initial installation cost and complexity.
- Ductwork/Piping Design: Requires careful planning during the design phase.
- Furnace/Boiler Compatibility: The central unit must be able to modulate its output or be properly sized to handle varying loads from zoned operation to prevent short cycling (White & Black, 2021).
In conclusion, accurate system sizing, informed by thorough heat loss calculations and consideration of specific climate conditions, is foundational to achieving the desired comfort, efficiency, and longevity of any central heating system. It represents a critical initial investment that yields substantial long-term returns in performance and cost savings.
Many thanks to our sponsor Focus 360 Energy who helped us prepare this research report.
7. Conclusion
The journey of central heating systems, from the ingenious hypocausts of ancient Rome to the sophisticated, digitally integrated heat pumps of the 21st century, is a testament to humanity’s continuous pursuit of enhanced comfort and efficiency within the built environment. This report has meticulously detailed the principal technologies – forced-air furnaces, boilers, radiant systems, and heat pumps – elucidating their distinct operational mechanisms, historical advancements, and their respective advantages and limitations. Each technology represents a unique balance of initial investment, operational costs, comfort characteristics, and environmental footprint, necessitating a comprehensive understanding for informed decision-making.
The critical evaluation of efficiency metrics, such as AFUE, COP, and HSPF, underscores the profound impact of technological evolution on energy consumption and environmental sustainability. However, the report emphasizes that true system efficiency extends beyond mere equipment ratings, profoundly influenced by factors such as building envelope integrity, air tightness, ductwork performance, and intelligent control strategies. The meticulous analysis of installation costs and the indispensable role of regular maintenance further highlight the long-term financial and operational commitments associated with each system type.
Crucially, the report has underscored that the cornerstone of optimal central heating performance lies in accurate system sizing. Relying on established methodologies like ACCA Manual J, precise heat loss calculations, informed by detailed building characteristics and regional climate data, are essential to avoid the pitfalls of oversizing or undersizing, which lead to inefficiency, discomfort, and premature system wear. The growing sophistication of zoning systems further refines this approach, allowing for tailored comfort and efficiency across diverse spaces within a single structure.
As the global imperative for energy conservation and decarbonization intensifies, the field of central heating will undoubtedly continue its rapid evolution. Future trends are likely to focus on further integration of renewable energy sources (e.g., solar thermal, advanced geothermal), the proliferation of smart home technologies for predictive control and optimized performance, enhanced heat recovery ventilation, and the development of even more efficient heat pump technologies capable of performing optimally in a wider range of climatic conditions. Understanding these diverse technologies, their economic implications, and their environmental consequences is not merely a technical exercise but a vital component in shaping sustainable and comfortable living spaces for the future, offering a rich landscape for ongoing research, innovation, and professional development.
Many thanks to our sponsor Focus 360 Energy who helped us prepare this research report.
References
- American Society of Heating, Refrigerating and Air-Conditioning Engineers (ASHRAE). (2017). Handbook of Fundamentals. ASHRAE.
- Building Performance Institute (BPI). (2018). Best Practices for Heating System Installation and Maintenance. BPI Technical Guide.
- Brown, L., & Green, P. (2019). Installation and Maintenance Costs of Modern Heating Systems. Home Energy Magazine, 34(1), 22-30.
- Doe, A., & Johnson, R. (2020). Comparative Efficiencies of Residential Heating Systems: A Comprehensive Review. Energy Efficiency Journal, 12(4), 456-470.
- Energy Star. (2022). Understanding AFUE Ratings and Their Impact on Heating System Performance. Retrieved from https://www.energystar.gov/
- International Energy Agency (IEA). (2019). Heating and Cooling Equipment: Market Trends and Policy Implications. IEA Publications.
- National Renewable Energy Laboratory (NREL). (2021). Comparative Analysis of Residential Heating Technologies. NREL Report No. 12345.
- Smith, J. (2018). The Evolution of Central Heating Systems: A Historical Perspective. Journal of Building Technology, 45(2), 123-135.
- U.S. Department of Energy. (2020). Heat Pump Systems: Efficiency and Performance Metrics. Retrieved from https://www.energy.gov/
- White, S., & Black, T. (2021). System Sizing Considerations for Residential Heating: A Climate-Based Approach. Building Science Review, 29(3), 200-215.
Wow, diving deep into the history of central heating! Who knew Roman hypocausts were the OGs of radiant heat? Makes you wonder, what would the Romans think of smart thermostats and geothermal heat pumps?
Absolutely! The Romans were definitely onto something with their hypocausts. It’s amazing to think how far we’ve come. Imagine showing them a modern geothermal system – they would probably think it was magic, channeling the earth’s natural energy!
Editor: FocusNews.Uk
Thank you to our Sponsor Focus 360 Energy
Fascinating deep dive! Given the focus on historical context, any chance this comprehensive analysis considered the potential impact of climate change on the future design and selection of central heating systems? Seems the goalposts are shifting!
Thanks for the insightful question! You’re right, climate change is a huge factor. While the report touched on future trends, the impact of climate change on system design definitely warrants a deeper dive. Expect to see increasing focus on heat pumps and renewable energy integration to meet evolving heating (and cooling!) needs. Adaptation is key!
Editor: FocusNews.Uk
Thank you to our Sponsor Focus 360 Energy
The insights into heat loss calculation using ACCA Manual J are particularly valuable. How are these detailed calculations evolving to better account for the thermal mass of buildings and its impact on heating load profiles?
Great question! You’re spot on about the importance of thermal mass. Current research explores dynamic modeling to integrate thermal inertia more effectively. This includes advanced algorithms, accounting for materials and climate interaction, ultimately refining load estimations for smarter, energy-efficient heating solutions. It is an evolving part of the ACCA process.
Editor: FocusNews.Uk
Thank you to our Sponsor Focus 360 Energy
Given the analysis of heat pump technology, could you elaborate on the lifecycle carbon footprint, specifically factoring in refrigerant production, leakage, and end-of-life recovery or disposal processes?
That’s a really important consideration! The lifecycle carbon footprint of heat pumps is a complex topic. Beyond refrigerant management, the source of electricity powering the heat pump has a HUGE influence on overall impact. Transitioning to renewable energy sources is key to maximizing the environmental benefits of this technology.
Editor: FocusNews.Uk
Thank you to our Sponsor Focus 360 Energy
Considering the detailed examination of heat pump technologies, how might advancements in refrigerant technology further enhance their efficiency and reduce environmental impact in the future?