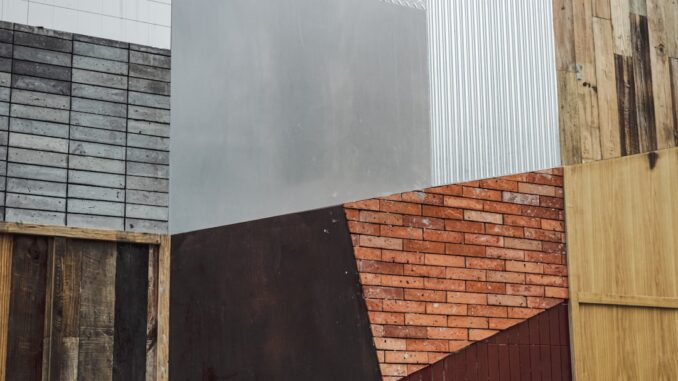
Abstract
The global construction industry stands at a critical juncture, facing increasing pressure to address its substantial environmental footprint and pivot towards truly sustainable practices. This paradigm shift necessitates a fundamental re-evaluation of material selection, moving beyond conventional choices to embrace innovative, environmentally responsible alternatives. Central to this transformation is the strategic adoption of sustainable materials characterized by principles such as minimal embodied carbon, maximal recycled content, rapid renewability, localized sourcing, inherent reusability, non-toxicity, and enhanced durability. This comprehensive report delves deeply into these foundational principles, elucidating their individual and collective significance in mitigating environmental impact. Furthermore, it provides an exhaustive exploration of the role of Environmental Product Declarations (EPDs) as critical tools for transparency and informed decision-making. The report also examines the cutting-edge innovations emerging in material science, from self-healing concretes to carbon-sequestering biomaterials, and discusses how these advancements, coupled with the rigorous application of circular economy principles, are reshaping construction methodologies towards a regenerative future. This detailed examination aims to provide a robust understanding of the multi-faceted approach required to foster a truly sustainable built environment.
Many thanks to our sponsor Focus 360 Energy who helped us prepare this research report.
1. Introduction
The construction sector is an undeniable cornerstone of global economic development and societal infrastructure. However, its expansive scale comes at a significant environmental cost, rendering it one of the largest contributors to global greenhouse gas (GHG) emissions, resource depletion, waste generation, and habitat degradation. Annually, the production and construction of buildings account for approximately 38% of global energy-related carbon dioxide emissions, with embodied carbon – the emissions associated with materials and construction processes – representing a substantial and growing proportion as operational energy efficiency improves across the sector (IEA, 2021). Furthermore, the industry consumes over 50% of all extracted raw materials globally and is responsible for a vast majority of solid waste generation (UNEP, 2020). This profound environmental impact necessitates a radical transformation towards sustainable construction practices.
Sustainable construction is a holistic approach that seeks to minimize the environmental footprint of buildings throughout their entire lifecycle, from design and material sourcing to construction, operation, maintenance, and eventual deconstruction or demolition. It integrates principles of ecological integrity, resource efficiency, economic viability, and social equity. Within this broader framework, the selection of materials plays a pivotal and arguably the most foundational role. Sustainable materials offer tangible solutions to mitigate ecological concerns, conserve finite natural resources, and reduce pollution, all while meeting the stringent functional, aesthetic, and structural requirements of modern architecture. The urgency of this shift is underscored by international agreements such as the Paris Agreement and the United Nations Sustainable Development Goals (SDGs), which call for urgent action to decarbonize economies and transition towards more resilient and equitable societies. This report focuses specifically on the critical role of material innovation and selection in achieving these ambitious sustainability targets, laying the groundwork for a more responsible and regenerative built environment.
Many thanks to our sponsor Focus 360 Energy who helped us prepare this research report.
2. Principles of Sustainable Materials
Sustainable materials are distinguished by a suite of interconnected principles that collectively contribute to a dramatically reduced environmental footprint throughout their lifecycle. Adherence to these principles guides architects, engineers, and developers in making choices that transcend mere compliance, moving towards genuine environmental stewardship and long-term resilience.
2.1 Low Embodied Carbon
Embodied carbon, or upfront carbon, refers to the total greenhouse gas emissions associated with the extraction, processing, manufacturing, transportation, construction, and initial maintenance of building materials, extending to their eventual disposal or recycling at the end-of-life. It encompasses the cradle-to-gate (A1-A3 manufacturing stages) and often includes cradle-to-site (A4-A5 construction stages) impacts, as well as operational repair/replacement (B4) and end-of-life (C1-C4) impacts within a comprehensive Life Cycle Assessment (LCA). As buildings become more energy-efficient in their operation, the embodied carbon component of their total lifecycle emissions becomes increasingly significant, often accounting for 30-50% or more of a building’s total carbon footprint over a 50-60 year lifespan (World Green Building Council, 2019). Therefore, selecting materials with demonstrably low embodied carbon is paramount for minimizing the overall carbon footprint of construction projects and achieving net-zero emissions goals.
Strategies for reducing embodied carbon include:
- Optimizing Material Efficiency: Designing structures to use less material overall, e.g., through efficient structural systems or prefabrication.
- Prioritizing Recycled Content: Utilizing materials with high percentages of post-consumer or post-industrial recycled content (discussed in Section 2.2) significantly reduces the energy and emissions associated with virgin material production.
- Specifying Low-Carbon Alternatives: Substituting high-carbon materials with lower-carbon options. For instance, traditional concrete, a major emitter due to cement production, can be replaced or supplemented with alternatives. Supplementary Cementitious Materials (SCMs) such as fly ash, blast furnace slag, and calcined clay can replace a significant portion of Portland cement, dramatically reducing the concrete’s embodied carbon. Emerging technologies like geopolymer concretes, which utilize industrial by-products activated by alkaline solutions, offer even lower carbon footprints by eliminating cement entirely. Another innovation involves injecting captured CO2 into concrete during curing, permanently sequestering the carbon within the material and enhancing its strength (CarbonCure Technologies, 2023).
- Leveraging Biomaterials: Timber, particularly from sustainably managed forests, is a prime example of a low embodied carbon material, as trees absorb and store carbon dioxide during their growth phase through photosynthesis. When used in construction, this sequestered carbon remains locked within the building material, effectively offsetting emissions from other materials. Mass timber products, such as Cross-Laminated Timber (CLT), Glued Laminated Timber (Glulam), and Laminated Veneer Lumber (LVL), offer structural performance comparable to steel and concrete, enabling multi-story and even high-rise timber buildings. Sweden’s commitment to timber cities, such as the ‘Wood City’ project in Stockholm, exemplifies this potential, showcasing how timber can be a sustainable choice for large-scale urban development while sequestering carbon (Time, 2023). Beyond timber, materials like straw, hemp, and bamboo (discussed in Section 2.3) also offer significant carbon sequestration potential.
- Minimizing Transportation: Local sourcing (discussed in Section 2.4) reduces the ‘transportation’ component of embodied carbon.
- Emphasizing Durability and Reusability: Materials with longer lifespans and those designed for reuse (discussed in Sections 2.7 and 2.5) reduce the need for new material production over time, thus lowering the overall embodied carbon of a building throughout its operational life cycle.
2.2 High Recycled Content
Incorporating materials with high recycled content is a cornerstone of circular economy principles in construction. It fundamentally reduces the demand for virgin resources, minimizes waste directed to landfills, and often results in significant energy savings compared to producing materials from scratch. Recycled content can be categorized as post-consumer (material that has served its intended purpose and been diverted from waste streams) or pre-consumer (material diverted from the waste stream during a manufacturing process).
Key examples and their benefits include:
- Recycled Aggregates: Crushed concrete, asphalt, bricks, and glass cullet can be repurposed as aggregates in new concrete mixes, road bases, or fill materials. This practice conserves natural sand and gravel reserves, reduces the environmental impact of quarrying, and diverts vast quantities of construction and demolition (C&D) waste from landfills. For instance, the use of recycled concrete aggregate (RCA) can reduce the need for virgin aggregates by up to 100% in certain applications, simultaneously reducing the carbon footprint of concrete production (Cemex Ventures, 2023).
- Recycled Steel: Steel is one of the most recycled materials globally, largely due to its magnetic properties that facilitate easy separation from waste streams. The use of electric arc furnaces (EAFs) allows for the production of new steel almost entirely from recycled scrap, consuming significantly less energy (up to 75% less) and emitting substantially less carbon than traditional blast furnace methods that rely on virgin iron ore. Recycled steel retains its inherent strength and durability, making it an excellent choice for structural components.
- Recycled Plastics: Post-consumer plastics (e.g., HDPE, PET, PVC) are increasingly being incorporated into various building products. Examples include plastic lumber for decking, fencing, and outdoor furniture; insulation materials made from recycled PET bottles; roofing tiles; pipes; and even composite building blocks or aggregates. While challenges remain regarding material sorting, contamination, and long-term performance, innovations are continually expanding the applicability of recycled plastics in construction.
- Recycled Glass: Beyond aggregate use, recycled glass can be transformed into countertops, tiles, insulation (e.g., fiberglass and foam glass insulation), and even translucent panels, offering aesthetic appeal and performance benefits.
- Recycled Gypsum: Gypsum wallboard scrap from construction sites or demolition can be recycled into new wallboard products or used as a soil amendment, reducing landfill waste and conserving natural gypsum reserves.
The widespread adoption of high recycled content materials requires robust collection and sorting infrastructure, clear performance standards for recycled products, and strong market demand to close the loop effectively.
2.3 Rapid Renewability
Rapidly renewable materials are those derived from plant or animal resources that can regenerate quickly, typically within a 10-year cycle or less, without depleting the natural resource base. Utilizing these materials supports sustainable practices by ensuring a continuous, replenishable supply, reducing reliance on finite resources, and often providing carbon sequestration benefits during their growth.
Prominent examples include:
- Bamboo: One of the fastest-growing plants on Earth, some species can grow several feet per day, reaching maturity in 3-5 years. Its rapid growth rate, combined with its impressive strength-to-weight ratio (often compared to steel and concrete), makes it an excellent choice for flooring, panels, structural components, scaffolding, and engineered composites. Bamboo forests also contribute to soil stability and carbon sequestration. (Mt Copeland, 2023).
- Hemp: Industrial hemp is a versatile and fast-growing crop that matures in approximately 4 months. Its fibers can be used for insulation, textiles, and composites, while its woody core (hurd or shiv) is a key component in hempcrete, a lightweight, insulating, and breathable building material (discussed further in Section 4.3).
- Cork: Harvested from the bark of the cork oak tree (Quercus suber) without felling the tree, cork is a rapidly renewable resource. The bark regrows every 9-12 years. Cork offers excellent thermal and acoustic insulation properties, making it ideal for flooring, wall coverings, and insulation boards. Its natural elasticity, durability, and resistance to moisture make it a valuable sustainable material.
- Straw Bales: A by-product of grain farming, straw bales are an abundant and rapidly renewable agricultural waste product. Used as infill in structural frames or load-bearing walls, straw bales provide exceptional insulation, acoustic properties, and are a significant carbon sink. Their low embodied energy and local availability make them a highly sustainable building option.
- Cotton: While cotton production can be water-intensive, recycled cotton fibers from textile waste can be processed into high-performance insulation, offering excellent thermal and acoustic properties while diverting waste from landfills.
- Linoleum: Made from natural materials like linseed oil, cork dust, wood flour, and natural resins, linoleum is a rapidly renewable flooring option known for its durability, natural anti-bacterial properties, and biodegradability.
2.4 Local Sourcing
Local sourcing, sometimes referred to as regional sourcing, involves procuring building materials from within a defined geographical radius of the construction site, typically 50-500 miles. This practice offers a multitude of environmental, economic, and social benefits:
- Reduced Transportation Emissions: A primary benefit is the significant reduction in greenhouse gas emissions associated with the transportation of materials from distant manufacturing facilities or raw material extraction sites. This directly lowers the embodied carbon footprint of the project.
- Support for Local Economies: Local sourcing strengthens regional industries, creates local jobs, and keeps capital within the community, fostering economic resilience. It can also encourage the development of local sustainable material production capacities.
- Reduced Supply Chain Risks: Shorter supply chains are generally more resilient to disruptions (e.g., natural disasters, geopolitical events) and can lead to more predictable material delivery times.
- Enhanced Regional Identity and Performance: Materials native to a specific region are often inherently well-suited to the local climate, geology, and environmental conditions. Utilizing local stone, timber, or earth (e.g., rammed earth, adobe) can result in buildings that are more climatically appropriate, perform better over time, and visually harmonize with their surroundings, fostering a sense of place and regional architectural identity.
- Reduced Packaging Waste: Local sourcing can sometimes facilitate bulk delivery or reusable packaging systems, further reducing waste.
- Greater Transparency and Accountability: Shorter supply chains can allow for easier verification of material origins, ethical labor practices, and environmental standards.
Challenges to local sourcing include the limited availability of certain specialized materials in all regions, the need for robust local manufacturing infrastructure, and the potential for increased costs if local production is not yet scaled. However, the growing emphasis on regional material palettes and the revival of traditional building techniques adapted for modern applications are making local sourcing an increasingly viable and desirable strategy.
2.5 Reusability and Design for Disassembly (DfD)
Promoting reusability and designing for disassembly (DfD) are fundamental tenets of the circular economy applied to the built environment. Rather than a linear ‘take-make-dispose’ model, this approach envisions buildings as ‘material banks’ where components can be easily deconstructed, reclaimed, and repurposed at the end of a building’s life, retaining their value and extending their useful lifespan. This drastically reduces the need for new material extraction and manufacturing, minimizes demolition waste, and preserves the embodied energy already invested in the materials.
Key aspects include:
- Design for Disassembly (DfD): This involves intentional design choices that facilitate the future deconstruction and reuse of building elements. Strategies include:
- Modular Construction: Utilizing pre-fabricated modules that can be easily assembled, disassembled, and reconfigured or relocated.
- Mechanical Fasteners: Preferring bolts, screws, and clamps over irreversible bonding agents like adhesives, welds, or chemical mortars, allowing for easy separation of components.
- Standardized Dimensions: Using standard sizes for components to simplify their reuse in other projects.
- Material Passports: Detailed documentation (often digital) of every material and component in a building, including its composition, source, environmental performance, and potential for reuse or recycling (discussed further in Section 5.2).
- Accessible Connections: Designing connections that are easy to access and undo without damaging adjacent materials.
- Separation of Layers: Designing building envelopes and systems with distinct, separable layers to allow for individual component replacement or reclamation.
- Reclaimed Materials: Utilizing materials salvaged from demolished or deconstructed buildings. Examples include:
- Reclaimed Wood: Timber beams, flooring, and siding salvaged from old barns, factories, or houses. Reclaimed wood often possesses a unique aesthetic character, exceptional durability due to its age and density, and a significantly lower embodied energy footprint than new timber (Billionbricks, 2023).
- Salvaged Bricks: Bricks from historic buildings can be cleaned and reused, retaining their unique patina and character, while avoiding the energy-intensive process of new brick manufacturing.
- Reused Steel: Structural steel components can be deconstructed, inspected, and re-erected in new projects, capitalizing on steel’s inherent recyclability and durability.
- Architectural Salvage: Doors, windows, light fixtures, plumbing fixtures, and decorative elements can be salvaged and incorporated into new designs, adding character and reducing waste.
Implementing DfD requires a shift in design philosophy, greater collaboration between designers, contractors, and material suppliers, and the development of robust ‘urban mining’ infrastructures to efficiently recover and process salvaged materials.
2.6 Non-Toxicity (Health and Well-being)
Non-toxic materials are crucial for creating healthier indoor environments for occupants and reducing the release of harmful pollutants into the environment throughout a material’s lifecycle. Traditional building materials often contain volatile organic compounds (VOCs), formaldehyde, heavy metals (e.g., lead, cadmium), phthalates, flame retardants, and other chemicals that can off-gas into the indoor air, leading to poor indoor air quality (IAQ). Poor IAQ is linked to a range of health issues, including respiratory problems, allergies, headaches, fatigue, and more severe conditions like cancer (‘sick building syndrome’).
Key aspects of non-toxicity include:
- Eliminating Harmful Chemicals: Selecting materials that are inherently free from hazardous substances. This includes paints, coatings, adhesives, sealants, flooring, insulation, and composite wood products.
- Low-VOC and No-VOC Products: Prioritizing paints, adhesives, and sealants labeled as low-VOC or no-VOC, which release fewer harmful airborne chemicals. Natural paints made from plant oils, resins, clay, or milk casein offer truly non-toxic alternatives.
- Formaldehyde-Free Materials: Opting for formaldehyde-free particleboard, MDF, and plywood, which often use formaldehyde-based resins as binders.
- Natural and Bio-based Materials: Many natural materials, such as solid wood, cork, natural linoleum, wool, cotton, and clay plasters, are inherently non-toxic and contribute to healthier indoor environments. They often regulate humidity naturally and do not off-gas synthetic chemicals.
- Material Transparency: Seeking products with transparent disclosure of their chemical ingredients through labels like Declare, Cradle to Cradle, or Health Product Declarations (HPDs). These certifications help designers identify and avoid ‘red list’ chemicals associated with significant health impacts.
- Reduced Emissions: Beyond off-gassing, non-toxic materials reduce pollution during manufacturing and disposal, protecting workers and ecosystems.
The focus on non-toxicity extends beyond individual materials to the holistic design of indoor spaces, ensuring adequate ventilation, moisture control, and thermal comfort to optimize occupant health and well-being. This is a core component of certifications like the Living Building Challenge and the WELL Building Standard.
2.7 Durability and Longevity
Durable materials are those that retain their intended performance characteristics over a long period, resisting degradation from environmental factors (weathering, UV radiation, moisture, temperature fluctuations), physical stresses (abrasion, impact), and chemical exposure. Selecting durable materials is a fundamental principle of sustainable construction because it directly contributes to:
- Reduced Resource Consumption: Longer-lasting materials mean fewer replacements, thereby reducing the demand for new material production, associated embodied energy, and raw material extraction.
- Minimized Waste Generation: Fewer replacements lead to less construction and demolition waste entering landfills.
- Lower Maintenance and Repair Costs: Durable materials typically require less frequent maintenance, repairs, or replacements, leading to cost savings over the building’s lifecycle and reducing the associated environmental impact of these activities.
- Enhanced Resilience: Buildings constructed with durable materials are more resilient to the impacts of climate change, such as extreme weather events, and can better withstand the test of time.
- Preservation of Embodied Energy: Every repair or replacement involves new embodied energy. By extending material life, the initial embodied energy investment is maximized.
Examples of inherently durable materials include:
- Stone: Natural stone (granite, limestone, slate, sandstone) has been used for millennia due to its exceptional strength, resistance to weathering, and longevity. Ancient structures built from stone stand as testament to its durability (Financial Times, 2023).
- Rammed Earth: A traditional building technique using compressed natural soils, rammed earth walls are incredibly durable, fire-resistant, and have excellent thermal mass properties, providing stable indoor temperatures for centuries if properly protected from erosion.
- High-Performance Concrete: While conventional concrete can have a high embodied carbon footprint, advancements in concrete technology have led to formulations that offer enhanced durability, reduced permeability, and resistance to chloride ingress or sulfate attack, significantly extending its service life and reducing the need for costly repairs.
- Copper and Zinc: These metals, when used for roofing or cladding, develop a protective patina that provides exceptional resistance to corrosion, leading to lifespans of 100 years or more with minimal maintenance.
- Properly Selected and Treated Wood: While often thought of as less durable than stone or steel, specific durable wood species (e.g., redwood, cedar, black locust) or engineered wood products (e.g., thermally modified timber, acetylation) can achieve remarkable longevity, especially when protected from moisture and UV degradation through good design practices (e.g., overhangs, proper detailing).
Designing for durability involves not only material selection but also robust structural engineering, appropriate detailing to prevent moisture ingress, and consideration of local climatic conditions and anticipated stresses over the building’s lifespan. It is a key aspect of creating sustainable, resilient infrastructure.
Many thanks to our sponsor Focus 360 Energy who helped us prepare this research report.
3. Environmental Product Declarations (EPDs)
Environmental Product Declarations (EPDs) are standardized, third-party verified documents that provide transparent and comprehensive information about the environmental performance of products throughout their lifecycle. They are increasingly becoming indispensable tools in the sustainable construction ecosystem, empowering stakeholders to make informed decisions based on quantifiable environmental data rather than generic claims. EPDs are built upon the robust methodology of Life Cycle Assessment (LCA) and adhere to international standards, primarily ISO 14040/14044 for LCA and ISO 14025 for Type III environmental declarations.
3.1 Life Cycle Assessment (LCA) Methodology
LCA is a systematic, quantitative methodology used to assess the environmental impacts associated with all stages of a product’s life, from raw material extraction (cradle) through material processing, manufacture, distribution, use, repair and maintenance, and disposal or recycling (grave, or cradle-to-cradle). The LCA process typically involves four phases:
- Goal and Scope Definition: Clearly defining the purpose of the study, the product system to be evaluated, and the functional unit (e.g., 1 m² of wall insulation for 60 years).
- Inventory Analysis (LCI): Collecting data on all energy and material inputs and environmental outputs (emissions, waste) associated with each stage of the product’s life cycle.
- Impact Assessment (LCIA): Translating the inventory data into environmental impact categories, such as:
- Global Warming Potential (GWP): Measured in CO2 equivalents (CO2e), representing contributions to climate change (e.g., embodied carbon).
- Acidification Potential (AP): Representing emissions that contribute to acid rain.
- Eutrophication Potential (EP): Representing nutrient enrichment in aquatic and terrestrial ecosystems.
- Ozone Depletion Potential (ODP): Representing chemicals that deplete the stratospheric ozone layer.
- Smog Formation Potential (SFP): Representing ground-level ozone formation.
- Primary Energy Demand: Total energy consumed from non-renewable and renewable sources.
- Resource Depletion: Impact on abiotic resource consumption.
- Interpretation: Evaluating the results of the inventory and impact assessment in relation to the defined goal and scope, drawing conclusions, and identifying opportunities for environmental improvement.
EPDs typically cover specific modules of the product’s life cycle. Most common are ‘cradle-to-gate’ EPDs, which include raw material supply (A1), transportation (A2), and manufacturing (A3). Increasingly, ‘cradle-to-grave’ EPDs, which extend to the use (B1-B7) and end-of-life (C1-C4) phases, or even ‘cradle-to-cradle’ EPDs that include the benefits and loads beyond the system boundary (Module D) from recycling or reuse, are available.
3.2 Structure and Verification of EPDs
EPDs are prepared according to specific Product Category Rules (PCRs), which are genre-specific guidelines that define how an LCA should be conducted for a particular product group (e.g., cement, insulation, windows) to ensure consistency and comparability. These PCRs are developed through a multi-stakeholder process and verified by a Program Operator.
Key characteristics of EPDs:
- Standardization: Adherence to ISO standards ensures a consistent framework for data collection and reporting.
- Transparency: EPDs provide a detailed breakdown of environmental impacts across different lifecycle stages, rather than a single ‘green’ label.
- Third-Party Verification: To ensure accuracy, reliability, and prevent greenwashing, EPDs are independently verified by accredited third parties. This verification confirms that the LCA methodology and data comply with relevant standards and PCRs (Wikipedia, 2023a).
- Quantitative Data: EPDs present quantifiable environmental impact indicators, allowing for objective comparison between similar products.
3.3 Role of EPDs in Construction
In the construction sector, EPDs are invaluable for several reasons:
- Informed Material Selection: Architects, designers, and specifiers can directly compare the environmental performance of different products that fulfill the same functional requirements. This enables them to select materials with lower environmental impacts, particularly concerning embodied carbon, thereby driving down a project’s overall carbon footprint.
- Green Building Certifications: EPDs are increasingly recognized and rewarded by leading green building rating systems such as LEED (Leadership in Energy and Environmental Design), BREEAM (Building Research Establishment Environmental Assessment Method), DGNB (German Sustainable Building Council), and Living Building Challenge. Projects utilizing materials with EPDs can earn credits towards these certifications, incentivizing manufacturers to produce them.
- Enhanced Transparency and Trust: For manufacturers, EPDs demonstrate commitment to environmental responsibility and provide a credible means of communicating product sustainability. For consumers and stakeholders, EPDs build trust by offering verified data.
- Supply Chain Optimization: EPDs can encourage manufacturers to improve their production processes, source more sustainably, and optimize logistics to reduce environmental impacts, as the data reveals hotspots for improvement.
- Policy and Regulation Support: Governments and municipalities are increasingly considering EPDs as tools for developing building codes and procurement policies that favor low-impact materials, such as the Buy Clean initiatives in some regions.
3.4 Limitations and Future of EPDs
Despite their benefits, EPDs face challenges. Data quality can vary, and the complexity of LCA means that comparability between products can sometimes be challenging if different PCRs or system boundaries are used. Furthermore, the sheer volume of products requiring EPDs necessitates scalable solutions.
The future of EPDs lies in greater digitalization and integration. Digital EPDs, machine-readable data, and their integration into Building Information Modeling (BIM) software will enable automated environmental performance calculations for entire projects, facilitating data-driven design decisions at an unprecedented scale. This will move beyond individual product comparisons to optimizing whole building environmental performance from the earliest design stages.
Many thanks to our sponsor Focus 360 Energy who helped us prepare this research report.
4. Innovations in Sustainable Materials
The urgent demand for more sustainable construction has spurred remarkable advancements in material science, leading to the development of innovative materials that offer enhanced performance, reduced environmental impact, and often entirely new functionalities. These innovations are critical for transitioning towards a regenerative built environment.
4.1 Self-Healing Concrete
Concrete is the most widely used man-made material globally, but its inherent brittleness makes it prone to cracking, which can compromise its structural integrity, allow ingress of water and corrosive agents (leading to rebar corrosion), and necessitate costly repairs or replacements. Self-healing concrete is an innovative material engineered to autonomously repair these cracks, significantly extending the lifespan of structures and dramatically reducing maintenance needs, resource consumption, and associated embodied carbon over time.
The mechanisms for self-healing concrete typically fall into a few categories:
- Bacterial-Based Healing: This approach involves incorporating dormant bacteria (e.g., Bacillus pasteurii or Sporosarcina pasteurii) and a calcium lactate nutrient into the concrete mix, often encapsulated in micro-capsules or lightweight aggregate. When a crack forms and water penetrates, the capsules break, activating the bacteria. The bacteria then convert the calcium lactate into calcium carbonate (limestone), which precipitates and fills the cracks. This bio-mineralization process effectively seals cracks up to several hundred micrometers wide (AP News, 2023).
- Polymer-Based Healing: Micro-capsules containing polymers or epoxy resins are embedded within the concrete. When a crack propagates through the material, it ruptures the capsules, releasing the healing agent, which then polymerizes or solidifies to fill the crack.
- Mineral-Based/Autogenous Healing Enhancement: This method relies on the un-hydrated cement particles within the concrete matrix. When cracks form and water enters, these particles can further hydrate and form calcium silicate hydrate (CSH) gel or calcium hydroxide, which can fill small cracks. Crystalline admixtures can be added to enhance this natural autogenous healing process, promoting the formation of insoluble crystals that block water pathways and seal cracks.
Benefits of self-healing concrete include:
- Extended Service Life: Reduces the need for repairs and replacements, translating to significant savings in materials, labor, and energy over the structure’s lifetime.
- Increased Durability and Resilience: Structures become more resistant to environmental degradation and less susceptible to the effects of water ingress and rebar corrosion.
- Reduced Maintenance Costs: Lower operational expenditures for infrastructure owners.
- Lower Embodied Carbon: By avoiding the production of new concrete for repairs or replacements, the overall embodied carbon footprint of the structure is reduced.
Challenges include the cost and scalability of current technologies, the long-term performance of healing agents in varied environmental conditions, and the need for standardized testing methods.
4.2 Bio-Fabricated Materials
Bio-fabricated materials represent a revolutionary class of sustainable building materials derived from or grown by living organisms, offering biodegradable, renewable, and often carbon-sequestering alternatives to conventional options. This field leverages principles from biology, biotechnology, and materials science.
- Mycelium-Based Products: Mycelium is the root-like structure of fungi. By growing mycelium on agricultural waste substrates (e.g., corn stalks, sawdust, hemp hurds) in molds, it binds the substrate together to form lightweight, robust, and custom-shaped composites. After growth, the material is heat-treated to stop further growth and enhance structural stability. Mycelium-based materials offer excellent thermal insulation, acoustic absorption, and inherent fire resistance. They are biodegradable, non-toxic, and can be grown with minimal energy input, making them highly sustainable. Applications include insulation panels, acoustic tiles, packaging, and even furniture components (GP Radar, 2023).
- Algae-Based Materials: Microalgae offer potential for various applications. They can be cultivated in bioreactors, absorbing CO2 and producing biomass. This biomass can then be processed into bioplastics, binders, pigments, or even serve as a raw material for producing bio-insulation. Algae bricks, for example, have been explored as self-sustaining, carbon-absorbing building blocks.
- Bacterial Cellulose: Produced by certain bacteria, bacterial cellulose is a high-purity form of cellulose with unique properties, including high strength, water retention, and biocompatibility. While currently more niche, it holds potential for advanced composites or coatings.
- Bio-bricks: Beyond mycelium, researchers are exploring ‘growing’ bricks using bacteria-induced mineralization processes (e.g., using urea and sand), offering an alternative to energy-intensive fired clay bricks.
These materials represent a significant departure from traditional extractive manufacturing, instead embracing biological processes for material creation. While many are still in early stages of commercialization, their potential for scalability and environmental benefits is immense.
4.3 Carbon-Negative and Carbon-Sequestering Materials
Carbon-negative (or carbon-sequestering) materials are those that remove more carbon dioxide from the atmosphere during their lifecycle than is emitted during their production, use, and disposal. These materials offer a critical pathway to achieving net-zero or even carbon-positive buildings.
- Hempcrete: A biocomposite material made from hemp hurds (the woody core of the hemp plant), a lime-based binder, and water. During the growth of the hemp plant, it sequesters significant amounts of atmospheric CO2. Further CO2 is absorbed during the carbonation (curing) process of the lime binder. Hempcrete is lightweight, provides excellent thermal insulation, regulates humidity, is vapor-permeable, and is naturally fire, mold, and pest resistant. It offers significant advantages as an infill insulation material for walls, roofs, and floors, contributing positively to a building’s carbon balance (Cemex Ventures, 2023).
- Mass Timber (CLT, Glulam, etc.): As discussed in Section 2.1, sustainably sourced timber products inherently sequester carbon. Advanced mass timber products like Cross-Laminated Timber (CLT), Glued Laminated Timber (Glulam), and Laminated Veneer Lumber (LVL) allow for the construction of multi-story buildings, effectively creating ‘carbon sinks’ that store CO2 for the lifetime of the structure. The rapid growth of sustainably managed forests ensures a continuous supply while maintaining the carbon sequestration cycle.
- Biochar in Construction: Biochar is a charcoal-like substance produced by heating biomass in the absence of oxygen (pyrolysis). When incorporated into building materials like concrete, insulation, or plaster, it can sequester carbon long-term. Biochar also offers potential benefits for material properties, such as enhanced thermal insulation and moisture regulation.
- Carbon Capture and Utilization (CCU) in Concrete: Technologies like CarbonCure inject captured industrial CO2 emissions directly into fresh concrete during the mixing process. This chemically converts the CO2 into a mineral, permanently sequestering it within the concrete and simultaneously increasing the concrete’s compressive strength, allowing for a reduction in cement content. This process directly transforms a climate pollutant into a valuable building material.
- Ferrock: An experimental material that uses recycled steel dust and silica, binding them with CO2. Ferrock behaves similarly to cement but actually absorbs carbon dioxide during its curing process, making it a carbon-negative material. Its properties, including hardness and durability, make it a promising alternative or additive to traditional concrete (Cemex Ventures, 2023).
These innovations are not only reducing the carbon footprint of construction but are actively contributing to atmospheric carbon removal, shifting buildings from being carbon emitters to carbon sinks.
4.4 Other Emerging Sustainable Materials
Beyond these categories, research continues to yield exciting possibilities:
- Transparent Wood: A composite material made by chemically removing lignin from wood and then impregnating it with a transparent polymer. It offers high optical transparency, excellent mechanical strength, and good thermal insulation, with potential applications in windows, facades, and solar cells.
- Aerogels: Extremely lightweight, porous materials derived from a gel in which the liquid component has been replaced with gas. Silica aerogels are super-insulating, offering thermal performance far superior to conventional insulation materials, with potential for ultra-efficient building envelopes.
- Phase Change Materials (PCMs): Substances that absorb and release large amounts of latent heat when they change phase (e.g., from solid to liquid and vice versa) within a specific temperature range. Integrated into building materials (e.g., drywall, insulation), PCMs can help regulate indoor temperatures, reducing the need for heating and cooling and thus lowering operational energy consumption.
- Recycled Plastic Bricks/Composites: Innovations in transforming mixed plastic waste into durable, lightweight, and insulating building blocks or panels, offering solutions for regions with limited access to traditional building materials and abundant plastic waste.
These emerging materials, alongside ongoing research into nanotechnology, smart materials, and biomimicry, promise to further transform the built environment, making it more resilient, energy-efficient, and environmentally benign.
Many thanks to our sponsor Focus 360 Energy who helped us prepare this research report.
5. Implementing Circular Economy Principles in Construction
The circular economy is an economic system aimed at eliminating waste and the continual use of resources. In construction, this translates into designing, constructing, and operating buildings and infrastructure in ways that keep materials, components, and products at their highest utility and value at all times, minimizing virgin resource extraction and waste generation. It’s a fundamental shift from the linear ‘take-make-dispose’ model.
5.1 Design for Disassembly (DfD) and Adaptability
As previously introduced (Section 2.5), Design for Disassembly (DfD) is a critical enabler of the circular economy. It involves intentional design decisions at the outset of a project to facilitate the easy deconstruction, rather than demolition, of buildings at the end of their useful life or when components need replacing. This ensures that valuable materials and components can be recovered, reused, or recycled with minimal waste and maximum preservation of embodied energy. Key strategies for DfD include:
- Material Selection for Reversibility: Prioritizing materials that can be easily separated and reused without damage. This includes favoring mechanical fasteners (bolts, screws, clips) over irreversible glues, welds, or chemical bonds.
- Standardization and Modularity: Designing with standardized dimensions and modular components allows for easier interchangeability, replacement, and reuse in other contexts. This supports prefabrication and off-site construction, which can further reduce waste and increase efficiency.
- Accessible Connections: Ensuring that connections between components are readily accessible for deconstruction, minimizing the need for destructive methods.
- Layered Design: Separating building elements into distinct layers (e.g., structure, enclosure, services, finishes) with different lifespans. This allows for individual layers or components to be updated, repaired, or replaced without affecting the entire building, extending the overall lifespan and adaptability of the structure.
- Future-Proofing and Adaptability: Designing buildings with inherent flexibility to accommodate future changes in use, technology, or occupant needs. This can involve clear spans, raised floors, flexible partitions, and easily modifiable service routes, thereby extending the building’s relevance and preventing premature demolition.
- Material Passports: A digital database of building materials is critical for enabling DfD.
5.2 Material Passports and Digital Twins
Material Passports are digital datasets that document the composition, characteristics, source, and potential for reuse or recycling of all materials and components used within a building. They act as a comprehensive inventory of the ‘material bank’ represented by the building. This information is crucial for enabling circularity at the end-of-life stage, allowing deconstruction companies to efficiently identify, sort, and recover valuable materials. Key data points in a material passport typically include:
- Material type and quantity.
- Manufacturer and product name.
- Chemical composition and any hazardous substances.
- Environmental performance data (e.g., EPDs).
- Certification information (e.g., Cradle to Cradle).
- Location within the building.
- Installation methods and fasteners used.
- Potential for reuse, recycling, or composting at end-of-life.
Material Passports are often integrated with Building Information Modeling (BIM). A BIM model serves as a ‘digital twin’ of the physical building, containing rich data about every element. By embedding material passport information directly into the BIM model, stakeholders gain unprecedented transparency and control over the building’s material assets. This integration facilitates:
- Enhanced Decision-Making: Designers can select materials with optimal end-of-life scenarios during the design phase.
- Efficient Deconstruction: Demolition companies can precisely locate and recover specific materials, optimizing the deconstruction process and maximizing material value.
- Urban Mining: Material passports underpin the concept of ‘urban mining,’ where buildings become sources of valuable raw materials for future construction.
- Regulatory Compliance: They can support compliance with future regulations requiring material circularity.
Challenges include the standardization of data formats, the effort required for data input, and ensuring the long-term maintenance and accessibility of these digital records.
5.3 Urban Mining and Deconstruction
Urban mining refers to the process of recovering raw materials from urban infrastructure, including buildings, rather than extracting new virgin resources from the earth. It is the direct antithesis of landfilling C&D waste. This concept shifts the focus from demolition, which is typically destructive and mixes materials, to deconstruction, which is a systematic and careful dismantling process aimed at preserving materials for reuse or high-value recycling.
- Deconstruction vs. Demolition: Demolition typically involves heavy machinery and aims for rapid breakdown, resulting in mixed waste streams that are difficult to separate and often end up in landfills or low-value recycling. Deconstruction, conversely, is a labor-intensive but value-adding process. It involves carefully salvaging components like timber beams, bricks, steel elements, doors, and windows for direct reuse. Materials that cannot be reused are then separated for high-quality recycling (e.g., concrete to aggregate, metal scrap).
- Economic Drivers: While deconstruction can have higher upfront labor costs than demolition, the sale of salvaged materials can offset these costs and even generate profit. The economic viability is improving as markets for reclaimed materials mature and as landfilling costs or carbon taxes increase.
- Policy Support: Some jurisdictions offer incentives for deconstruction or mandate diversion rates for C&D waste, further encouraging urban mining.
Urban mining and deconstruction are essential for closing material loops, reducing landfill burdens, and conserving resources, forming a crucial link in the circular economy chain.
5.4 Recycling and Upcycling Infrastructure
Effective recycling and upcycling are vital components of the circular economy. This requires robust infrastructure for collecting, sorting, processing, and reintroducing construction and demolition (C&D) waste materials back into the supply chain. While recycling typically refers to processing materials into similar products (e.g., concrete to aggregate), upcycling transforms waste materials into products of higher quality or value.
- Challenges: The C&D waste stream is often heterogeneous, containing a mix of materials (concrete, wood, metals, plastics, gypsum, etc.), often contaminated. Efficient sorting at scale is a significant challenge.
- Advancements: Automated sorting technologies, mobile recycling plants, and specialized processing facilities are improving the efficiency and purity of recycled materials. For example, advancements in concrete recycling now allow for the production of high-quality recycled concrete aggregate (RCA) suitable for structural applications.
- Upcycling Examples: Transforming waste plastics into durable building blocks or furniture; repurposing industrial by-products like fly ash and blast furnace slag into high-performance cementitious binders; using sawdust and wood chips to create engineered wood products or insulation.
- Industrial Symbiosis: This involves collaborations between industries where the waste product of one industry becomes the raw material for another. For example, excess heat from cement production might power a nearby facility, or waste gypsum from power plants might be used to produce plasterboard.
5.5 Product-as-a-Service and Reverse Logistics
Moving beyond material ownership, circular economy models are exploring ‘product-as-a-service’ (PaaS) for building components. Instead of purchasing materials outright, manufacturers lease components (e.g., lighting fixtures, HVAC systems, flooring) to building owners. The manufacturer retains ownership and responsibility for the product’s maintenance, upgrades, and end-of-life recovery. This incentivizes manufacturers to design durable, repairable, and reusable products, as their profitability is tied to the longevity and reusability of their assets.
- Benefits of PaaS: Shifts focus from sales volume to product performance and longevity; encourages eco-design; ensures materials are returned to the manufacturer for reuse/recycling; reduces waste for building owners.
- Reverse Logistics: PaaS models necessitate robust reverse logistics systems, which manage the collection, inspection, repair, and redistribution of products and materials back through the supply chain. This is a complex but crucial aspect of circularity, ensuring materials don’t just disappear into landfills.
These innovative business models, coupled with technological advancements and supportive policies, are crucial for achieving a truly circular and regenerative built environment.
Many thanks to our sponsor Focus 360 Energy who helped us prepare this research report.
6. Challenges and Considerations
While the imperative and benefits of adopting sustainable materials in construction are clear, several challenges and considerations must be addressed for their widespread and effective implementation.
6.1 Cost Implications and Economic Viability
One of the most frequently cited barriers to the widespread adoption of sustainable materials is the perception of higher upfront costs, often referred to as the ‘green premium’. While some innovative materials or certified sustainable products may indeed have higher initial purchase prices compared to their conventional counterparts, this perspective often overlooks the broader economic picture:
- Upfront vs. Lifecycle Costs (LCC): Sustainable materials often offer significant savings over the building’s entire lifecycle. For instance, highly insulative materials may reduce operational energy consumption for heating and cooling, leading to lower utility bills. Durable materials require less frequent maintenance and replacement, cutting down on long-term repair costs. Non-toxic materials can improve occupant health and productivity, reducing absenteeism and healthcare costs.
- Market Scale and Economies of Scale: Many sustainable materials are produced by nascent industries or niche manufacturers, meaning they have not yet achieved the economies of scale that drive down prices for conventional materials. As demand increases and production scales up, costs are expected to decrease.
- Policy and Incentives: Government policies, tax incentives, grants, carbon pricing mechanisms, and green financing options can help offset initial costs and make sustainable materials more competitive. For example, incentives for deconstruction can make salvaged materials more economically attractive.
- Valuation and Risk Mitigation: Sustainable buildings can command higher rental rates, have higher resale values, and may even qualify for lower insurance premiums due to enhanced resilience. Investors are increasingly considering ESG (Environmental, Social, and Governance) factors, making sustainable projects more appealing.
Educating clients and stakeholders about the long-term financial benefits and value proposition of sustainable materials is crucial to overcome this perception.
6.2 Supply Chain Limitations and Scalability
The availability and widespread distribution of certain sustainable materials can be a significant hurdle, particularly for large-scale projects:
- Niche Production: Many highly innovative sustainable materials, such as self-healing concrete or bio-fabricated panels, are still produced at a relatively small scale, limiting their immediate availability for major construction projects.
- Geographical Constraints for Local Sourcing: While local sourcing is a key principle, specific projects might require materials not readily available in the immediate vicinity, necessitating longer transportation routes and potentially negating some environmental benefits.
- Quality Control and Consistency: As new materials enter the market, ensuring consistent quality, reliable performance, and adherence to industry standards across different manufacturers can be a challenge. This is particularly true for recycled or bio-based materials where feedstock variability can impact product characteristics.
- Lack of Established Infrastructure: For materials like reclaimed timber or recycled aggregates, robust and efficient collection, sorting, processing, and distribution networks are still developing in many regions.
Addressing these limitations requires investment in scaling up production capacities, developing more efficient and regional supply chains, and fostering collaboration between material innovators, manufacturers, and logistics providers.
6.3 Performance Standards and Regulatory Frameworks
Ensuring that sustainable materials meet the necessary performance criteria for safety, structural integrity, fire resistance, durability, and health is paramount. Integrating novel materials into established building codes and regulatory frameworks can be a slow and complex process:
- Testing and Certification: New materials often require extensive testing to prove their long-term performance, durability, and safety characteristics under various conditions. This can be time-consuming and expensive.
- Building Code Integration: Building codes are designed to ensure public safety and typically rely on well-understood, conventional materials. Introducing new materials requires rigorous evaluation and often specific code amendments or alternative compliance pathways.
- Risk Aversion: The construction industry is inherently risk-averse, given the long lifespan of buildings and the potential for liability. Designers, engineers, and insurers may be hesitant to specify or approve novel materials without extensive proven track records and clear regulatory acceptance.
- Lack of Standardization: Without standardized performance metrics and testing protocols for certain sustainable materials, comparing products and ensuring their suitability for specific applications can be difficult.
Collaborative efforts among industry bodies, research institutions, regulatory authorities, and manufacturers are essential to develop robust performance standards, facilitate testing, and streamline the integration of sustainable materials into regulatory frameworks.
6.4 Skills Gap and Education
The widespread adoption of sustainable materials also faces a significant human capital challenge:
- Lack of Expertise: Architects, engineers, contractors, and tradespeople may lack the necessary knowledge and experience in specifying, designing with, installing, and maintaining novel sustainable materials and circular construction practices.
- Traditional Education Systems: Current academic and vocational training programs often lag behind the rapid pace of innovation in sustainable materials and construction techniques.
- Resistance to Change: Established industry practices and familiarity with conventional materials can create inertia and resistance to adopting new methods.
Addressing this requires comprehensive educational initiatives, professional development programs, hands-on training, and curriculum reform in educational institutions to equip the workforce with the skills needed for a sustainable built environment.
6.5 Market Acceptance and Perceptions
Beyond technical and economic considerations, the market’s acceptance of sustainable materials plays a crucial role:
- Aesthetics and Design Preferences: Some sustainable materials might have a different aesthetic or perceived finish compared to conventional ones, which may not align with established design trends or client preferences. Educating clients on the unique beauty and performance of these materials is important.
- Perception of Performance: There can be a misconception that ‘green’ materials compromise on performance, durability, or cost-effectiveness, which needs to be actively dispelled through data and successful case studies.
- Consumer Demand: While environmental awareness is growing, a strong and consistent consumer demand for sustainable buildings and materials is necessary to drive market transformation.
Overcoming these challenges requires a multi-pronged approach involving policy support, technological innovation, economic incentives, educational initiatives, and proactive communication to build trust and demonstrate the tangible benefits of sustainable materials.
Many thanks to our sponsor Focus 360 Energy who helped us prepare this research report.
7. Conclusion
The imperative to transition towards a sustainable built environment is no longer a niche concern but a global necessity. The construction industry, as a major consumer of resources and contributor to greenhouse gas emissions, holds a significant responsibility and immense potential for positive change. The strategic integration of sustainable materials into construction practices is undeniably vital for reducing the environmental impact of the built environment and fostering a more resilient, low-carbon future.
This report has demonstrated that sustainable materials are characterized by a set of interconnected and mutually reinforcing principles: minimizing embodied carbon, maximizing recycled content, leveraging rapid renewability, prioritizing local sourcing, enabling comprehensive reusability through design for disassembly, ensuring non-toxicity for occupant health, and guaranteeing robust durability for long-term performance. Each of these principles, when rigorously applied, contributes significantly to mitigating climate change, conserving finite resources, reducing waste, and enhancing human well-being.
Crucial tools like Environmental Product Declarations (EPDs) provide the necessary transparency and verifiable data, empowering architects, engineers, and developers to make truly informed decisions based on comprehensive lifecycle impacts. EPDs are the bedrock for moving beyond anecdotal ‘greenness’ to quantifiable environmental performance, aligning material selection with ambitious sustainability targets and enabling compliance with evolving green building standards.
Moreover, the rapid advancements in material science are continuously expanding the palette of sustainable options. Innovations such as self-healing concrete promise extended material lifespans, while bio-fabricated materials like mycelium-based composites offer novel, biodegradable, and low-energy solutions. Most significantly, carbon-negative and carbon-sequestering materials, including hempcrete, advanced mass timber, and carbon-captured concrete, are revolutionizing the industry by actively removing atmospheric carbon, turning buildings into critical components of climate solutions.
Beyond individual materials, the wholesale adoption of circular economy principles in construction is transforming the industry’s modus operandi. Designing for disassembly, leveraging material passports, engaging in urban mining, and developing robust recycling and upcycling infrastructures are foundational to closing material loops, eliminating waste, and retaining the value of resources over multiple lifecycles. Emerging models like product-as-a-service hint at a future where material ownership shifts, further incentivizing durability and reuse.
While challenges persist – including upfront cost perceptions, supply chain limitations, the need for evolving performance standards, and a persistent skills gap – these are not insurmountable. They require concerted effort, continued research and development, supportive policies, and cross-sector collaboration. The trajectory of innovation, coupled with increasing environmental awareness and regulatory pressure, suggests that these challenges will be systematically addressed as sustainable materials move from being an alternative to becoming the industry standard.
In essence, the future of the built environment is inextricably linked to the materials we choose and how we manage them throughout their entire lifecycle. By embracing these principles, leveraging technological innovations, and championing circularity, the construction industry can transform from a major environmental burden into a powerful force for global sustainability, creating buildings that are not only structurally sound and aesthetically pleasing but also profoundly regenerative and harmonious with the natural world.
Many thanks to our sponsor Focus 360 Energy who helped us prepare this research report.
References
- AP News. (2023). Scientists developing self-healing concrete that could last for centuries. Retrieved from https://apnews.com/article/f5799b0009acc8145805610ee1972ac9
- Billionbricks. (2023). 5 Examples of Sustainable Construction Materials Flourishing in the US. Retrieved from https://billionbricks.org/blog/5-examples-of-sustainable-construction-materials-flourishing-in-the-us/
- CarbonCure Technologies. (2023). CarbonCure Concrete Technology. Retrieved from https://www.carboncure.com/ (Accessed Nov 2023)
- Cemex Ventures. (2023). Sustainable Building Materials: What They Are & Why We Need Them. Retrieved from https://www.cemexventures.com/sustainable-building-materials/
- Financial Times. (2023). How to make buildings that last. Retrieved from https://www.ft.com/content/f2d8c127-da52-42f3-995e-93af364c3195
- GP Radar. (2023). Top Sustainable Construction Materials: What They Are & How to Use Them. Retrieved from https://www.gp-radar.com/article/top-sustainable-construction-materials-what-they-are-how-to-use-them
- IEA (International Energy Agency). (2021). Buildings – Tracking Clean Energy Progress. Retrieved from https://www.iea.org/reports/buildings (Accessed Nov 2023)
- Mt Copeland. (2023). A Guide to Sustainable Building Materials. Retrieved from https://mtcopeland.com/blog/a-guide-to-sustainable-building-materials/
- Time. (2023). Sweden is Building a New City Made Entirely of Wood. Retrieved from https://time.com/7207873/sweden-stockholm-wood-city-sustainability/
- UNEP (United Nations Environment Programme). (2020). Global Status Report for Buildings and Construction 2020. Retrieved from https://globalabc.org/resources/global-status-report-2020 (Accessed Nov 2023)
- Wikipedia. (2023a). Environmental Product Declaration. Retrieved from https://en.wikipedia.org/wiki/Environmental_Product_Declaration
- Wikipedia. (2023b). Sustainable habitat. Retrieved from https://en.wikipedia.org/wiki/Sustainable_habitat
- World Green Building Council. (2019). Bringing embodied carbon upfront: Whole life carbon in buildings. Retrieved from https://www.worldgbc.org/sites/default/files/WorldGBC_Bringing_Embodied_Carbon_Upfront_Report_2019.pdf (Accessed Nov 2023)
Self-healing concrete? Are we one step closer to Wolverine-inspired infrastructure? Let’s hope the healing process is faster than my internet connection. What about self-cleaning buildings, next? Imagine the possibilities!
That’s a great point about self-cleaning buildings! The advancements in self-healing materials really do open up a world of possibilities. Imagine the reduced maintenance costs and improved longevity of our infrastructure. It could revolutionize how we approach building design and upkeep.
Editor: FocusNews.Uk
Thank you to our Sponsor Focus 360 Energy
The report highlights exciting innovations like bio-fabricated materials. How do factors such as regional climate and building type influence the selection and performance of these materials compared to more conventional options?
That’s an insightful question about bio-fabricated materials! Regional climate definitely plays a huge role, influencing factors like moisture exposure and temperature fluctuations. Building type also matters immensely – a high-rise needs different properties than a single-family home. Exploring these interactions is key to successful, sustainable implementation and long term viability.
Editor: FocusNews.Uk
Thank you to our Sponsor Focus 360 Energy
The discussion of material passports as digital datasets is particularly compelling. How might blockchain technology enhance the transparency and security of these passports, ensuring data integrity throughout the material lifecycle and across various stakeholders?
That’s a fantastic question! Blockchain’s decentralized and immutable nature could really revolutionize material passports. Imagine a secure, transparent record of a material’s journey from cradle to grave, accessible to all stakeholders. This could build trust and streamline circular economy initiatives. I’d love to hear other thoughts on this application!
Editor: FocusNews.Uk
Thank you to our Sponsor Focus 360 Energy