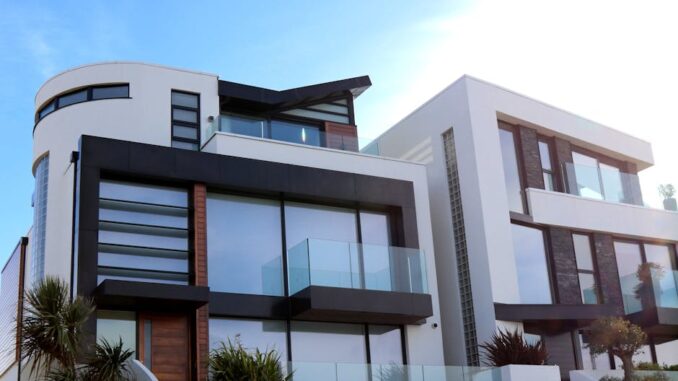
Abstract
The Passivhaus standard, originating in Germany, has emerged as a globally recognized benchmark for ultra-low energy building design. It prioritizes significantly reduced energy consumption for heating and cooling, alongside the provision of exceptional indoor comfort and air quality. This comprehensive report undertakes an exhaustive examination of the foundational principles underpinning Passivhaus design, meticulously detailing the rigorous certification process, critically evaluating the economic implications over a building’s lifecycle, and exploring its diverse practical applications in both new construction projects and challenging retrofits. By thoroughly analyzing these multifaceted aspects, this report aims to furnish a nuanced, in-depth understanding of Passivhaus’s pivotal role in advancing sustainable architecture and mitigating the environmental impact of the built environment.
Many thanks to our sponsor Focus 360 Energy who helped us prepare this research report.
1. Introduction
The accelerating global concerns pertaining to climate change, resource depletion, and the imperative for energy security have profoundly reshaped the discourse surrounding building design and construction. Traditional building practices often contribute substantially to global energy consumption and greenhouse gas emissions, necessitating a transformative shift towards more sustainable paradigms. In response to these pressing challenges, various advanced building standards and frameworks have been developed, prioritizing not only energy efficiency but also occupant health, well-being, and long-term environmental stewardship. Among these pioneering frameworks, the Passivhaus standard (often referred to as Passive House in English-speaking countries) has ascended to prominence as a leading, scientifically rigorous, and performance-based methodology.
Conceived in Germany in the late 1980s by Professors Bo Adamson and Wolfgang Feist, and formalized by the Passivhaus Institut (PHI) in Darmstadt, the standard’s genesis was rooted in the ambitious goal of constructing buildings that require minimal, if any, conventional heating or cooling. The core philosophy of Passivhaus is to achieve energy efficiency through passive means – primarily by optimizing the building’s fabric and form – rather than relying heavily on active mechanical systems. This ‘fabric-first’ approach inherently leads to buildings that are remarkably robust, comfortable, and resilient to external climate fluctuations. The standard sets exceptionally stringent criteria for energy performance, typically targeting a heating and cooling demand of no more than 15 kWh/(m²a) or a peak heating/cooling load of 10 W/m², alongside a primary energy renewable (PER) demand limit for all services (heating, cooling, domestic hot water, auxiliary electricity) of 60 kWh/(m²a) for the ‘Classic’ standard. Furthermore, it mandates superior indoor environmental quality, ensuring consistent temperatures, excellent air quality, and acoustic comfort.
This report embarks on a detailed exploration of the foundational principles that define the Passivhaus standard, dissecting each key element with technical precision. It meticulously outlines the multi-stage certification process, from initial design modeling using the Passive House Planning Package (PHPP) to final on-site verification. A significant portion of this analysis is dedicated to a comprehensive evaluation of the economic implications, moving beyond initial capital outlay to consider life-cycle costs, energy savings, market valuation, and return on investment. Finally, the report addresses the practical challenges and innovative solutions encountered during the implementation of Passivhaus designs in both new constructions, where flexibility is inherent, and in the more complex domain of retrofitting existing building stock, where unique constraints necessitate ingenious approaches. Through this detailed examination, the report seeks to underscore the profound and growing significance of Passivhaus as a cornerstone of sustainable and high-performance building practices worldwide.
Many thanks to our sponsor Focus 360 Energy who helped us prepare this research report.
2. Passivhaus Principles
The Passivhaus standard is predicated on a set of five core technical principles, which collectively ensure ultra-low energy consumption and superior indoor environmental quality. These principles are interdependent and must be holistically integrated into the building design from its earliest conceptual stages to achieve the demanding performance targets.
2.1 Super-Insulation
Super-insulation constitutes the bedrock of Passivhaus design, serving as the primary mechanism to drastically reduce heat transfer through the building envelope. The objective is to encase the conditioned space in a highly insulating thermal shell, minimizing heat loss in winter and heat gain in summer. This is achieved through the strategic application of robust layers of high-quality insulation materials across all opaque elements of the building envelope: walls, roof, floor slab, and foundation.
Unlike conventional construction, where insulation levels are often driven by minimum building code requirements, Passivhaus mandates significantly thicker and more effective insulation. The standard typically requires U-values (thermal transmittance, representing the rate of heat flow through a material or assembly per unit area and temperature difference) for opaque building elements to be below 0.15 W/(m²·K). In many colder climates, U-values as low as 0.10 W/(m²·K) or even lower are often achieved in practice. To contextualize, a typical non-Passivhaus wall in many regions might have a U-value of 0.25-0.35 W/(m²·K), demonstrating the substantial difference.
A diverse array of insulation materials can be employed to achieve these stringent U-values, each possessing distinct thermal, environmental, and structural properties. Common materials include:
- Mineral Wool (Rock Wool/Glass Wool): Known for excellent thermal and acoustic performance, fire resistance, and vapor permeability. It is often used in cavity walls and roof spaces.
- Expanded Polystyrene (EPS): Lightweight, cost-effective, and moisture-resistant, frequently used in external insulation systems (EIFS) and floor insulation.
- Extruded Polystyrene (XPS): Denser and more moisture-resistant than EPS, making it suitable for foundations, inverted roofs, and demanding applications.
- Polyisocyanurate (PIR) and Phenolic Foam: High-performance rigid foams offering superior thermal resistance per unit thickness, valuable where space is limited.
- Cellulose (Recycled Paper): An environmentally friendly option, often blown into cavities or open spaces, offering good thermal and acoustic properties.
- Wood Fiber Insulation: A sustainable, breathable insulation option derived from timber processing, providing good thermal mass and vapor permeability.
The application method is equally critical. Passivhaus design emphasizes continuous insulation layers, aiming to wrap the entire conditioned volume without breaks. This meticulous approach ensures uniform thermal performance across the envelope, mitigating localized cold spots and enhancing overall energy efficiency. The interplay between insulation thickness, material conductivity (Lambda value), and the overall assembly of the building element (including structural components and finishes) dictates the final U-value, which is precisely calculated during the design phase using tools like PHPP.
2.2 Thermal Bridge-Free Construction
Thermal bridges, also known as cold bridges or heat bridges, represent localized areas within a building’s envelope where the insulation layer is interrupted, compromised, or where materials with higher thermal conductivity create preferential paths for heat transfer. These discontinuities can arise from structural elements (e.g., concrete slabs penetrating insulation, steel beams), penetrations (e.g., window frames, service pipes), or even poorly executed construction joints. The consequences of thermal bridges are significant:
- Increased Heat Loss/Gain: They create ‘weak spots’ in the thermal envelope, leading to disproportionately higher energy losses (or gains) than the surrounding well-insulated areas.
- Reduced Surface Temperatures: Interior surface temperatures in the vicinity of thermal bridges can be significantly lower than the ambient room temperature. This discomfort for occupants can be perceived as draughts.
- Condensation and Mold Risk: Reduced surface temperatures can cause interstitial or surface condensation if the dew point is reached, leading to moisture accumulation, mold growth, and potential damage to building materials and adverse health effects for occupants.
- Compromised Airtightness: Thermal bridges often coincide with difficult-to-seal junctions, exacerbating air leakage.
Passivhaus design mandates ‘thermal bridge-free construction,’ meaning that the linear thermal transmittance (Ψ-value, measured in W/(m·K)) of all junctions and penetrations is minimized to negligible levels or explicitly accounted for. This necessitates an extremely meticulous approach to detailing during both design and construction. Strategies to achieve this include:
- Continuous Insulation: Ensuring that the insulation layer wraps continuously around the building, without interruptions by structural elements. This often involves innovative connection details for balconies, roof-wall junctions, and floor-wall junctions.
- Offset Connections: Designing structural connections (e.g., timber frame to foundation) to minimize direct thermal bridging paths.
- Insulated Structural Elements: Using specialized, thermally broken components for elements like window reveals, thresholds, and steel connections that penetrate the envelope.
- Careful Junction Detailing: Meticulous design of all interfaces between different building elements (e.g., wall-floor, wall-roof, window-wall) to eliminate or minimize thermal bypasses. This involves precise alignment of insulation layers and use of insulating materials for any necessary bridging elements.
- Thermal Bridge Calculation: Employing advanced calculation methods (e.g., finite element analysis) to predict and quantify thermal bridge performance at the design stage, enabling designers to refine details for optimal performance.
For Passivhaus certification, the effective U-value of components and the Ψ-values of junctions must be specifically calculated and verified within the PHPP, often aiming for Ψ-values close to zero (e.g., < 0.01 W/(m·K) for critical junctions). This rigorous attention to detail ensures that the building envelope performs as a monolithic, thermally consistent shell.
2.3 Airtightness
Airtightness is a critical, yet often underestimated, principle in high-performance building design. It refers to the sealing of the building envelope to prevent uncontrolled air infiltration (cold air entering in winter, hot air in summer) and exfiltration (conditioned air escaping). While often confused with ventilation, airtightness is distinct: it aims to stop unintended air movement, whereas ventilation provides controlled, purposeful air exchange.
The importance of achieving high airtightness in Passivhaus buildings stems from several factors:
- Prevention of Convective Heat Loss: Uncontrolled air leakage can account for a significant portion of heat loss in conventional buildings, as warm air escapes and cold air infiltrates. This process, known as convection, can be far more impactful than conductive heat loss through the building fabric.
- Moisture Management: Air leakage can carry moisture vapor into building cavities, where it can condense upon encountering colder surfaces. This can lead to interstitial condensation, mold growth, timber decay, and degradation of insulation materials, compromising both structural integrity and indoor air quality.
- Enhanced Thermal Comfort: Draughts caused by air leakage are a major source of discomfort for occupants, even if the overall room temperature is adequate. A high level of airtightness eliminates these cold spots.
- Improved Indoor Air Quality: A sealed envelope prevents the ingress of external pollutants, allergens, and dust, allowing the controlled mechanical ventilation system to effectively filter and condition incoming air.
- Acoustic Performance: Airtightness significantly contributes to reducing noise transmission from the exterior, improving acoustic comfort within the building.
- Optimized MVHR Performance: A highly airtight envelope is a prerequisite for the efficient and effective operation of the MVHR system, ensuring that all incoming fresh air passes through the heat exchanger.
Passivhaus buildings are required to achieve an exceptional level of airtightness, specifically n50 ≤ 0.6 h⁻¹
(air changes per hour at 50 Pascal pressure difference) as measured by a blower door test. This means that when the building is subjected to a pressure difference of 50 Pascals (roughly equivalent to a 20 mph wind), no more than 60% of the building’s internal air volume should leak out or in within one hour. To put this in perspective, conventional building codes often allow for 5 to 10 air changes per hour at 50 Pa, highlighting the significant difference.
The blower door test is a diagnostic and verification tool. A large fan is mounted in an exterior doorway, either pressurizing or depressurizing the building to 50 Pa. Sensors measure the airflow required to maintain this pressure difference, indicating the building’s leakage rate. Multiple tests are often conducted during construction (e.g., after the air barrier is installed but before finishes) to identify and rectify leakage paths proactively.
Achieving this stringent airtightness requires meticulous planning and execution. It involves:
- Continuous Air Barrier: Designing a continuous, uninterrupted air barrier layer around the entire conditioned volume of the building. This layer can be formed by various materials such as oriented strand board (OSB), plaster, concrete, specialized membranes, or intelligent vapor control layers.
- Tapes and Sealants: Using high-performance, durable, and flexible airtightness tapes, mastics, and sealants to connect and seal all joints, penetrations, and transitions in the air barrier (e.g., around windows, doors, pipe penetrations, electrical outlets).
- Careful Detailing: Designing and constructing complex junctions (e.g., roof-wall, wall-floor, foundation-wall) with specific airtightness strategies in mind, often involving pre-formed components or custom solutions.
- Skilled Labor and Quality Control: Requiring skilled tradespersons who understand airtightness principles and rigorous on-site quality assurance, including interim blower door tests and thermal imaging, to identify and rectify leaks before completion.
2.4 Mechanical Ventilation with Heat Recovery (MVHR)
Given the exceptional airtightness of Passivhaus buildings, a robust and balanced mechanical ventilation system is indispensable to ensure continuous supply of fresh, filtered air and effective removal of stale, polluted air, all while minimizing energy loss. This is the role of the Mechanical Ventilation with Heat Recovery (MVHR) system.
MVHR systems are sophisticated balanced ventilation units that simultaneously extract stale, moisture-laden air from ‘wet’ rooms (kitchens, bathrooms, utility rooms) and supply fresh, filtered air to ‘dry’ rooms (bedrooms, living rooms). The critical feature, however, is the integrated heat exchanger. As the warm, outgoing stale air passes through the heat exchanger, it transfers a significant portion of its thermal energy to the cooler, incoming fresh air, without the two air streams ever mixing. This process recovers heat that would otherwise be lost to the exterior, thereby substantially reducing the energy demand for heating the incoming fresh air.
Key aspects and benefits of MVHR systems in Passivhaus include:
- High Heat Recovery Efficiency: Passivhaus-certified MVHR units must achieve a heat recovery rate of over 75% (often exceeding 80-90% in practice) according to the Passivhaus Institut criteria. This means that, for example, if the extracted air is 20°C and the outside air is 0°C, the incoming fresh air might be pre-warmed to 16-18°C solely by the recovered heat.
- Superior Indoor Air Quality (IAQ): MVHR systems provide a continuous, controlled supply of filtered fresh air, removing pollutants, CO2, volatile organic compounds (VOCs), and excess humidity. High-efficiency filters (e.g., F7 for supply, G4 for extract) prevent pollen, dust, and particulate matter from entering the building, benefiting occupants, especially those with allergies or respiratory sensitivities. This leads to a consistently healthy and invigorating indoor environment.
- Moisture Control: By continuously exchanging air, MVHR systems effectively manage indoor humidity levels, preventing condensation and mold growth that can be problematic in highly airtight structures if not properly ventilated.
- Thermal Comfort: The pre-warmed fresh air supply eliminates cold draughts associated with uncontrolled infiltration or opening windows in cold weather, contributing to a stable and comfortable indoor temperature.
- Noise Reduction: Since windows typically remain closed for ventilation, external noise pollution is significantly reduced, enhancing acoustic comfort within the building.
- Energy Efficiency: By recovering heat, the MVHR system drastically reduces the energy required to heat or cool incoming fresh air, making it a cornerstone of the Passivhaus ultra-low energy strategy.
Design and installation of MVHR systems are crucial. This involves:
- Sizing and Balancing: Correctly sizing the MVHR unit for the building’s volume and occupancy, and precisely balancing the supply and extract airflows to ensure optimal ventilation rates and slight positive or negative pressure as needed.
- Ductwork Design: Designing an efficient, airtight ductwork system that minimizes pressure drop and noise, often utilizing radial ducting (individual ducts from manifold to each room) or rigid, smooth-bore circular ducts for better airflow and ease of cleaning.
- Commissioning: Professional commissioning of the MVHR system is mandatory for Passivhaus certification to ensure it operates at its designed flow rates and efficiencies.
- Maintenance: Regular filter changes and periodic cleaning of ducts are essential for maintaining optimal performance and indoor air quality.
2.5 High-Performance Windows and Doors
While often categorized implicitly under super-insulation, high-performance windows and doors warrant a dedicated discussion due to their critical role as potential weak points in the building envelope. In a Passivhaus, windows and doors are not mere openings but highly engineered components that contribute significantly to the building’s overall energy performance and comfort.
Passivhaus standard requirements for windows and glazed doors are exceptionally stringent, reflecting their large surface area and their inherent lower insulating properties compared to opaque walls. Typical requirements include:
- Triple Glazing: Mandatory for nearly all climates, triple-glazed units consist of three panes of glass separated by two cavities. These cavities are typically filled with inert gases like argon or krypton, which have lower thermal conductivity than air, further reducing heat transfer.
- Low-Emissivity (Low-E) Coatings: Applied to specific glass surfaces, these microscopic coatings reflect radiant heat, preventing it from escaping during winter and reducing solar heat gain during summer, depending on their spectral selectivity.
- Warm Edge Spacers: The spacers that separate the glass panes within the sealed unit are made of low-conductive materials (e.g., composite plastic or stainless steel) rather than aluminum, minimizing heat transfer at the edge of the glass and reducing condensation risk.
- Insulated Frames: The window and door frames themselves must be highly insulated, often incorporating multiple chambers or insulation inserts to minimize thermal bridging through the frame material. Frame U-values must be exceptionally low.
- Overall Window U-value: The combined U-value for the entire window unit (glass, frame, and spacer) must typically be ≤ 0.80 W/(m²·K). This is a significant improvement over standard double-glazed windows, which often have U-values ranging from 1.5 to 2.5 W/(m²·K).
- Airtight Installation: Beyond the window unit itself, the installation must be meticulously detailed to ensure a continuous airtight and weathertight seal with the surrounding wall structure, preventing air leakage around the frame.
The strategic placement and sizing of windows also play a vital role in optimizing passive solar gain. In colder climates, south-facing windows (in the Northern Hemisphere) are maximized to allow solar radiation to penetrate and warm the interior during winter. Conversely, in warmer climates or on east/west facades, careful consideration of shading (overhangs, external blinds, louvers) is essential to prevent overheating during summer months. This balance ensures year-round thermal comfort without relying on active heating or cooling systems.
2.6 Passive Solar Gain and Shading
Passive solar design is the strategic use of solar energy to heat a building in winter and reject it in summer, fundamentally reducing the need for mechanical heating and cooling. In Passivhaus, this principle is integrated with the high-performance envelope to optimize energy balance and thermal comfort.
- Orientation: Buildings are typically oriented to maximize south-facing glazing (in the Northern Hemisphere) to capture winter solar radiation. In hotter climates, or for specific facades, orientation might be adjusted to minimize direct solar exposure during peak heat periods.
- Window Sizing and Placement: Large, high-performance windows are strategically placed on the south facade to allow sunlight to penetrate deep into the building, warming thermal mass elements like concrete floors or internal walls. North-facing windows are minimized to reduce heat loss, while east and west windows require careful shading due to low-angle sun.
- Thermal Mass: Internal thermal mass (e.g., concrete slabs, masonry walls) can absorb and store solar heat during the day, slowly releasing it back into the space during the cooler evening, thus stabilizing internal temperatures. In hot climates, thermal mass can also be used for night purging, flushing out heat accumulated during the day.
- Shading: Effective shading is crucial to prevent overheating, especially in summer or in warmer climates. Shading strategies include:
- Overhangs/Eaves: Fixed horizontal projections above windows, sized to block high-angle summer sun while allowing low-angle winter sun to enter.
- Vertical Fins: Used on east and west facades to block low-angle sun.
- External Blinds/Shutters: Dynamic shading devices that can be adjusted based on solar intensity and occupant preference. These are highly effective at blocking solar heat before it enters the building.
- Vegetation: Deciduous trees can provide summer shade while allowing winter sun to pass through.
Balancing passive solar gain with the risk of overheating is a core design challenge, especially in moderate and warm climates. PHPP includes an overheating calculation that must demonstrate that the building does not exceed 25°C for more than 10% of the annual hours, even without active cooling, solely through passive measures. This ensures year-round comfort and energy efficiency.
2.7 Primary Energy Renewable (PER) Demand and Renewable Energy Integration
While the original Passivhaus standard primarily focused on minimizing heat loss, the evolving climate crisis and technological advancements have led to an increased emphasis on minimizing overall energy demand and integrating renewable energy sources. The Passivhaus Institut introduced the Primary Energy Renewable (PER) metric to account for the total energy consumed by the building (heating, cooling, domestic hot water, auxiliary electricity for appliances and lighting, and ventilation fans) and its source. The PER demand limit for a Passivhaus Classic building is 60 kWh/(m²a), ensuring that the energy consumed is derived from efficient, non-fossil sources.
Furthermore, the PHI has introduced advanced certification classes:
- Passivhaus Plus: This standard requires the building to meet the Passivhaus Classic energy demand criteria AND generate a minimum of 60 kWh/(m²a) of renewable energy on site from a projected building footprint area (or primary floor area if not applicable). This encourages the integration of technologies like solar photovoltaics (PV) or solar thermal systems.
- Passivhaus Premium: This is the most ambitious standard, requiring the building to meet the Classic criteria AND generate a minimum of 120 kWh/(m²a) of renewable energy on site. Premium buildings are essentially ‘energy positive’ over the course of a year, producing more renewable energy than they consume, significantly contributing to grid decarbonization.
The integration of renewable energy sources in a Passivhaus context is particularly effective because the building’s inherently low energy demand means that smaller, more cost-effective renewable energy systems can meet a significant, or even all, of its energy needs. Common renewable technologies integrated include:
- Solar Photovoltaics (PV): Panels that convert sunlight directly into electricity, typically mounted on roofs or integrated into facades.
- Solar Thermal Collectors: Systems that use sunlight to heat water for domestic use or supplementary space heating.
- Heat Pumps: Highly efficient electrical devices that extract heat from ambient air (air-source heat pumps), the ground (ground-source heat pumps), or exhaust air (exhaust air heat pumps) and transfer it into the building for heating, domestic hot water, and sometimes cooling. Given the low heating loads of Passivhaus buildings, very small output heat pumps are often sufficient, sometimes even integrated directly into MVHR units.
By minimizing demand first, and then meeting the remaining demand with renewables, Passivhaus buildings provide a robust model for achieving truly sustainable, low-carbon, and energy-independent structures. This ‘efficiency first’ approach ensures that precious renewable energy is not wasted and that the building is resilient against future energy price volatility.
Many thanks to our sponsor Focus 360 Energy who helped us prepare this research report.
3. Certification Process
Achieving Passivhaus certification is a rigorous, multi-stage process that ensures adherence to the demanding performance criteria set by the Passivhaus Institut. It is a quality assurance process that provides independent third-party verification, giving confidence to owners, occupants, and the market that the building genuinely performs as designed. The process typically involves design modeling, meticulous construction, and final performance verification.
3.1 Passive House Planning Package (PHPP)
The Passive House Planning Package (PHPP) is the central and indispensable software tool for Passivhaus design and certification. Developed by the Passivhaus Institut, PHPP is a sophisticated, spreadsheet-based energy modeling tool that allows designers to accurately predict a building’s energy performance based on a wide range of input parameters. Its use is mandatory for all Passivhaus and EnerPHit projects seeking certification.
PHPP calculates:
- Heating and Cooling Demand: The annual specific heating and cooling demand (kWh/(m²a)) of the conditioned living area.
- Primary Energy Renewable (PER) Demand: The total energy consumed for heating, cooling, domestic hot water, ventilation, and auxiliary electricity, considering the energy source.
- Overheating Frequency: The number of hours per year that the internal temperature exceeds 25°C, ensuring summer comfort.
- Thermal Bridge Losses: Quantifies heat loss through linear thermal bridges.
- Airtightness Performance: Integrates the results of the blower door test.
- Domestic Hot Water Demand: Calculates energy needed for hot water.
- Electricity Consumption: Models auxiliary electricity use for fans, pumps, lighting, and appliances.
Designers input comprehensive building data into PHPP, including:
- Climate Data: Specific local climate data (temperature, solar radiation, humidity) for the building’s location.
- Building Geometry: Detailed dimensions, orientations, and surface areas of all envelope components.
- Material Properties: U-values of opaque components, window U-values (Ug, Uf, Ψg) and g-values (solar heat gain coefficient), and thermal bridge Ψ-values.
- Ventilation System: MVHR unit efficiency, airflow rates, and fan electricity consumption.
- Occupancy and Internal Gains: Assumed internal heat gains from occupants, lighting, and appliances.
- Shading Elements: Details of external shading devices.
PHPP serves as both a design optimization tool and a verification tool. During the design phase, it enables iterative analysis, allowing designers to experiment with different specifications (e.g., thicker insulation, higher-performance windows) and immediately see the impact on predicted energy demand. This empowers informed decision-making to achieve the Passivhaus targets cost-effectively. For certification, the final PHPP model, along with supporting documentation, forms the core of the submission, demonstrating compliance with the numerical criteria. While PHPP is the primary tool, designPH, a 3D modeling plugin for SketchUp, can be used for conceptual design and visual integration with PHPP.
3.2 Design and Construction Phases
Following the conceptual design and initial PHPP modeling, the project progresses through detailed design and construction, both of which require meticulous adherence to Passivhaus principles and quality assurance.
Design Phase: This stage involves translating the PHPP-optimized concept into detailed architectural and engineering drawings. Key aspects include:
- Integrated Design: A truly interdisciplinary approach where architects, structural engineers, mechanical engineers (HVAC), electrical engineers, and Passivhaus consultants collaborate from the outset. This ensures that all components and systems are seamlessly integrated to achieve performance goals.
- Detailed Drawings: Production of highly detailed construction drawings that precisely specify insulation layers, thermal bridge details, airtightness strategies, and MVHR ducting layouts. Each junction must be carefully thought out to avoid performance gaps.
- Specification of Components: Careful selection of certified Passivhaus components (windows, doors, MVHR units) with documented performance data. Product data sheets for all relevant materials and systems are collected for later verification.
- Moisture Management: Designing strategies to manage moisture within the building fabric, including vapor control layers, breathable membranes, and appropriate material sequencing to prevent interstitial condensation, particularly critical in varying climates.
Construction Phase: This phase is where theoretical design meets practical execution, and quality control becomes paramount. The builder and all tradespersons must be knowledgeable in Passivhaus principles and accustomed to higher precision work. Key steps and considerations include:
- Builder Education: Engaging a contractor and site team with prior Passivhaus experience or providing them with specific training on airtightness detailing, thermal bridge mitigation, and MVHR installation protocols.
- Air Barrier Implementation: Meticulous installation of the continuous air barrier, including taping and sealing all joints, penetrations (e.g., electrical boxes, pipework), and transitions between different materials. This is often an iterative process requiring rigorous attention.
- Interim Airtightness Tests: Performing blower door tests at critical stages of construction (e.g., once the air barrier is complete but before internal finishes are applied) to identify and rectify leaks early, when they are easier and less costly to fix. This proactive approach significantly reduces the risk of failing the final test.
- Thermal Bridge Execution: Ensuring that all thermal bridge details designed on paper are correctly implemented on site, using specified thermally broken components and precise installation techniques.
- MVHR Installation and Commissioning: Proper installation of the MVHR unit and its ductwork, ensuring minimal bends, appropriate sizing, and airtight connections. Professional commissioning is essential to balance airflow rates in all rooms and verify heat recovery efficiency.
- Documentation: Maintaining a thorough record of construction details, photographs of critical junctions, and material delivery slips to support the final certification application.
3.3 Certification and Verification
The final stage is the independent third-party certification, which provides an impartial assessment that the built structure meets all Passivhaus criteria. This process is typically managed by a certified Passivhaus Certifier accredited by the Passivhaus Institut.
Steps in the certification and verification process typically include:
- Documentation Submission: The design team compiles and submits a comprehensive documentation package to the certifier. This package includes:
- The final PHPP file, demonstrating that all numerical performance criteria (heating demand, cooling demand, PER demand, overheating frequency, airtightness) are met.
- Detailed architectural and structural drawings, highlighting Passivhaus-specific details (e.g., insulation layers, thermal bridge details, window schedules).
- Product data sheets and certifications for all key components (e.g., windows, doors, MVHR unit, insulation materials).
- Photos from critical stages of construction, particularly showing air barrier installation and thermal bridge details.
- Blower door test reports.
- MVHR commissioning report.
- Certifier Review: The independent certifier thoroughly reviews the submitted documentation, cross-referencing drawings, specifications, and calculations to ensure consistency and compliance with the Passivhaus standard. They will scrutinize the PHPP model for accuracy and identify any potential discrepancies or areas of non-compliance.
- On-Site Verification (Optional but Recommended): While not always mandatory for all certifiers, many certifiers or consultants conduct site visits during construction to verify the correct implementation of details, especially the air barrier and thermal bridge components. A final site visit after completion is common.
- Final Blower Door Test: A mandatory final blower door test is conducted by an accredited tester to measure the as-built airtightness of the building. The result
n50
must be≤ 0.6 h⁻¹
for Passivhaus Classic or≤ 1.0 h⁻¹
for EnerPHit Retrofit. This is a pass/fail criterion. - MVHR Performance Check: The certifier reviews the MVHR commissioning report and may verify the installed system’s operational parameters.
- Issuance of Certificate: Upon successful review of all documentation and verification of on-site performance, the building is officially awarded Passivhaus certification by the Passivhaus Institut or an accredited certifier. This signifies that the building meets the most rigorous energy efficiency and comfort standard in the world. The certificate usually specifies the class (Classic, Plus, Premium).
This robust certification process provides assurance of genuine high performance and distinguishes Passivhaus buildings from others that might merely claim to be ‘energy efficient’ without independent verification.
Many thanks to our sponsor Focus 360 Energy who helped us prepare this research report.
4. Economic Implications
The economic implications of Passivhaus construction are a frequent point of discussion, often centered around the perception of higher initial costs. However, a comprehensive analysis reveals that while upfront investment may indeed be greater, the long-term economic benefits, including significant operational savings and enhanced asset value, often result in a favorable lifecycle cost and an attractive return on investment.
4.1 Initial Costs
The initial capital expenditure for a Passivhaus project typically ranges from 5% to 15% higher than that of a comparable conventional new build. This uplift is primarily attributable to the following factors:
- High-Quality Components: The requirement for triple-glazed windows and doors, specialized airtightness products (tapes, membranes), and thicker, higher-performance insulation materials inherently increases material costs. For example, a Passivhaus-certified window can cost 1.5 to 2 times more than a standard double-glazed unit.
- Mechanical Ventilation with Heat Recovery (MVHR) System: The installation of a high-efficiency MVHR unit and its associated ductwork is a significant additional cost not typically found in conventional homes.
- Increased Labor and Skill: Achieving the exacting standards of airtightness and thermal bridge-free construction demands higher precision, greater attention to detail, and often more specialized labor or dedicated training for the construction team. This can lead to increased labor hours and costs.
- Design and Certification Fees: Engaging a certified Passivhaus designer or consultant and paying for the independent certification process adds to the upfront project cost. These fees are essential for ensuring compliance and quality assurance.
- Complexity (especially for Retrofits): For EnerPHit retrofits, the complexity of working with existing structures, overcoming unforeseen conditions, and potentially having to address structural or moisture issues can add significant costs. Custom solutions may be required where standard components do not fit.
It is crucial to note that the cost premium is often decreasing as the supply chain for Passivhaus components matures, and as more builders gain experience in this type of construction. Early engagement of a Passivhaus consultant, integrated design processes, and careful procurement can help mitigate these initial cost uplifts.
4.2 Energy Savings and Payback Period
The most compelling economic benefit of Passivhaus is the dramatic reduction in operational energy consumption. Passivhaus buildings consistently achieve energy savings of up to 90% for space heating and cooling compared to typical existing buildings, and up to 75% compared to new buildings constructed to conventional building codes. This translates directly into substantially lower utility bills for heating, cooling, and sometimes domestic hot water.
- Quantifiable Savings: For a typical family home, this could mean annual heating bills reduced from hundreds or thousands to perhaps tens of pounds/dollars, with cooling often being entirely passive or requiring minimal active intervention. This significant reduction offers immediate and ongoing financial relief.
- Reduced Energy Price Volatility: With minimal energy demand, occupants are largely insulated from fluctuations and spikes in energy prices, providing long-term financial security.
- Smaller Mechanical Systems: Due to the extremely low heating and cooling loads, Passivhaus buildings can often forgo conventional large boilers, furnaces, or air conditioning units. Instead, much smaller, simpler, and less expensive systems (e.g., a small heating coil within the MVHR, or a small air-source heat pump) are sufficient. The savings from these downsized systems can partially offset the costs of the high-performance envelope.
The payback period for the additional upfront investment in a Passivhaus typically ranges from 5 to 15 years, depending on various factors such as:
- Local Energy Prices: Higher electricity and fuel prices accelerate the payback period.
- Climate Zone: Buildings in extreme climates (very cold winters or hot, humid summers) tend to see faster paybacks due to greater potential for energy savings.
- Cost Premium: Lower initial cost uplifts naturally lead to shorter payback periods.
- Government Incentives: Subsidies, grants, tax credits, or low-interest loans for energy-efficient construction or renewable energy integration can significantly reduce the effective payback period.
- Occupant Behavior: While Passivhaus design is forgiving, occupant energy usage habits (e.g., excessive hot water consumption, leaving lights on) can influence overall bill savings.
Over the typical 50-100 year lifespan of a building, the cumulative energy savings far outweigh the initial investment, making Passivhaus a financially prudent long-term decision. Beyond simple payback, it’s essential to consider the lifecycle cost (LCC) analysis, which accounts for initial costs, operational costs, maintenance, and eventual disposal/replacement over the entire life of the building. Passivhaus buildings consistently demonstrate superior LCC performance compared to conventional construction.
4.3 Market Value and Resale Potential
Passivhaus certification increasingly acts as a differentiator in the real estate market, contributing to higher market value and enhanced resale potential. This is driven by several factors:
- ‘Green Premium’: There is a growing recognition and demand for sustainable, energy-efficient homes and buildings. Studies in various markets (e.g., UK, USA, Australia) indicate that green-certified homes can command a sales premium of 5% to 20% or more compared to conventional homes, or sell more quickly.
- Reduced Running Costs: Prospective buyers are increasingly aware of the financial burden of high energy bills. The promise of significantly lower (or near-zero) utility costs is a powerful selling point that translates into higher affordability over the long term, even with a potentially higher mortgage.
- Superior Comfort and Health: The enhanced indoor air quality, consistent internal temperatures, absence of draughts, and quiet environment of a Passivhaus building are tangible benefits that improve occupant well-being. These comfort advantages are highly valued by buyers.
- Future-Proofing: As energy regulations tighten and energy prices likely continue to rise, Passivhaus buildings are inherently ‘future-proofed.’ They meet or exceed future energy performance requirements today, making them more resilient to legislative changes and market shifts.
- Environmental Credentials: For environmentally conscious buyers, owning a Passivhaus aligns with their values and offers a tangible way to reduce their carbon footprint.
- Durability and Low Maintenance: The robust, ‘fabric-first’ approach of Passivhaus often results in highly durable buildings with reduced maintenance needs over their lifespan, further contributing to their long-term value.
- Financing Benefits: In some regions, financial institutions offer ‘green mortgages’ or preferential loan rates for certified energy-efficient homes, further enhancing their attractiveness.
While the market for Passivhaus properties is still niche in some areas, it is rapidly expanding. As public awareness of climate change and energy efficiency grows, the market appeal and resale value of Passivhaus buildings are expected to strengthen considerably, solidifying their position as a premium, desirable asset.
Many thanks to our sponsor Focus 360 Energy who helped us prepare this research report.
5. Practical Applications and Challenges
The implementation of Passivhaus principles, whether in new constructions or retrofits, presents distinct practical applications and challenges that demand careful consideration and innovative solutions.
5.1 New Constructions
Implementing Passivhaus principles in new construction is generally more straightforward than in retrofits, primarily due to the inherent design flexibility and the ability to integrate all necessary components from the ground up. However, even in new builds, specific challenges and best practices emerge:
- Integrated Design Process: The most effective way to achieve Passivhaus in new builds is through an early, integrated design process involving all stakeholders – architect, structural engineer, mechanical engineer, and Passivhaus consultant. Decisions made early in conceptual design (e.g., building form, orientation, window placement) have a disproportionately large impact on energy performance and cost efficiency. Retrofitting Passivhaus principles onto a conventional design late in the process is often expensive and difficult.
- Design Complexity: While the principles are clear, the detailed execution requires a high level of precision. Designers must meticulously detail junctions to eliminate thermal bridges and ensure airtightness, which can be more involved than standard construction detailing.
- Skilled Labor and Education: A significant challenge can be finding contractors and tradespersons with sufficient experience or willingness to adopt the stringent quality control required for Passivhaus. Airtightness, in particular, demands a different mindset from typical construction, where small gaps are often overlooked. Education and hands-on training for the construction team are crucial.
- Supply Chain: While improving, sourcing high-performance Passivhaus components (certified windows, MVHR units, specialized tapes) can sometimes be a challenge, especially in regions where the market is less mature. Lead times and cost can be higher for these specialized items.
- Cost Management: As discussed, the initial cost premium requires careful cost management. This involves value engineering, smart material selection, and leveraging the ability to downsize or eliminate conventional heating/cooling systems to offset costs.
- Client Expectations: Educating the client about the nuances of Passivhaus (e.g., windows generally remaining closed, MVHR operation, minimal heating) is vital to manage expectations and ensure occupant satisfaction post-occupancy.
Best practices for new Passivhaus construction include engaging a certified Passivhaus consultant from the very beginning, conducting intermediate airtightness tests during construction (e.g., ‘shell’ test before finishes), and thorough commissioning of all mechanical systems, especially the MVHR.
5.2 Retrofitting Existing Buildings (EnerPHit)
Retrofitting existing buildings to meet Passivhaus standards, known as EnerPHit, presents a more complex set of challenges and often requires innovative, context-specific solutions. EnerPHit offers a slightly more flexible standard than full Passivhaus, recognizing the inherent limitations of working with existing structures. The primary energy demand for EnerPHit is 45 kWh/(m²a) and heating/cooling demand is 25 kWh/(m²a) or a component-by-component approach can be followed.
Key challenges and considerations for EnerPHit retrofits include:
- Structural Limitations: Existing building structures may not easily accommodate the thickness of insulation required or the loads imposed by new components like MVHR units. This can necessitate structural modifications or creative insulation solutions.
- Moisture Management: A critical and often complex issue in retrofits is managing moisture. Adding external or internal insulation can change the thermal and moisture profile of existing walls, potentially leading to condensation risks within the wall assembly if not meticulously designed. Vapor-open external insulation or intelligent vapor control layers are often employed.
- Aesthetic and Heritage Constraints: Many existing buildings, particularly those with architectural or historical significance, have strict aesthetic or heritage preservation requirements. This can limit options for external insulation or window replacement, requiring more subtle or internal solutions.
- Thermal Bridge Mitigation: Existing structural penetrations (e.g., concrete floor slabs, balconies) are incredibly difficult to insulate effectively without extensive and costly structural alterations. EnerPHit allows for some higher thermal bridge values than full Passivhaus, acknowledging these practical constraints, but designers must still minimize them as much as possible.
- Airtightness Challenges: Achieving the stringent airtightness target in an existing building with numerous penetrations, uneven surfaces, and historic settlement can be highly challenging. Identifying and sealing every leakage path requires exceptional diligence, and often involves stripping back interiors or exteriors to create a continuous air barrier.
- Space for MVHR: Integrating MVHR units and their extensive ductwork into existing building layouts can be difficult due to limited ceiling space, structural elements, or aesthetic concerns. Careful planning of duct routes to minimize turns and maximize efficiency is essential.
- Occupancy During Retrofit: If the building remains occupied during the retrofit, phasing the work and managing disruption to occupants adds another layer of complexity.
Despite these challenges, innovative solutions are continually emerging:
- ‘Box within a Box’ Construction: As seen in the Cre8 Barn retrofit, constructing a completely new, super-insulated, airtight inner shell within the existing structure can bypass many of the external constraints and achieve high performance while preserving the exterior (netmagmedia.co.uk).
- External vs. Internal Insulation: Decision to insulate externally or internally depends on façade aesthetics, planning restrictions, and moisture risk. External insulation provides a continuous thermal wrap, minimizing thermal bridges, but alters the façade. Internal insulation preserves the exterior but requires careful moisture detailing and reduces internal space.
- Component-by-Component Approach: For EnerPHit, the PHI offers a ‘component method’ where individual components (e.g., walls, roof, windows) meet specific U-value targets, providing more flexibility when a full performance target is unfeasible due to site constraints.
EnerPHit projects demonstrate that even challenging existing building stock can be transformed into highly energy-efficient and comfortable spaces, significantly reducing their carbon footprint and extending their useful life. The key is thorough diagnostics, meticulous planning, and a highly skilled construction team.
5.3 Integration of MVHR Systems
The Mechanical Ventilation with Heat Recovery (MVHR) system is a critical component in both new builds and retrofits, ensuring continuous fresh air supply in highly airtight envelopes. Successful integration is crucial for optimal performance, indoor air quality, and thermal comfort. However, challenges can arise:
- Noise: Poorly designed or installed MVHR systems can generate noise from the unit itself, fan noise, or air rushing through ducts. This is mitigated by:
- Selecting Passivhaus-certified units with low specific fan power and low noise levels.
- Using appropriately sized ducts to maintain low air velocities.
- Installing attenuators (silencers) on supply and extract ducts, especially near living spaces.
- Mounting the MVHR unit on anti-vibration pads and locating it away from sensitive areas (e.g., loft, utility room).
- Ductwork Design and Space: Designing efficient ductwork that minimizes pressure drop, avoids cross-contamination, and fits within structural limitations can be challenging. Radial ducting systems (individual insulated ducts from a central manifold to each room) are often preferred for ease of balancing, better airflow, and reduced noise compared to branched systems.
- Commissioning: A poorly commissioned MVHR system will not perform as designed. Professional commissioning is essential to measure and balance airflow rates in each room, ensuring adequate ventilation and preventing pressure imbalances.
- Maintenance and User Education: Filters must be changed regularly (typically every 3-6 months) to maintain air quality and system efficiency. Users need to be educated on the purpose and maintenance of the MVHR, as it is a less familiar system than traditional heating.
- Over-Sizing/Under-Sizing: An improperly sized unit will either be inefficient (oversized) or unable to provide adequate ventilation (undersized). Sizing is based on building volume and occupancy, with allowances for peak loads (e.g., cooking).
- Condensate Drainage: MVHR units produce condensate as warm, moist air is cooled in the heat exchanger. Proper drainage to a waste pipe is necessary, requiring a slight fall in the pipe and sometimes a condensate pump.
Case studies, such as the residential Passivhaus in Melbourne (passivehouseadelaide.com), demonstrate successful MVHR integration. In this project, strategic placement of the unit in a dedicated service space, careful routing of insulated ductwork to minimize bends, and professional commissioning ensured optimal air quality (monitored CO2 levels, humidity) and thermal comfort throughout the year, even in a relatively warm climate where cooling becomes a consideration. This example highlights that when correctly designed and installed, MVHR systems are unobtrusive and highly effective.
Many thanks to our sponsor Focus 360 Energy who helped us prepare this research report.
6. Case Studies
Examining real-world applications provides tangible evidence of Passivhaus principles in action and illustrates how challenges are overcome across diverse building types and climates.
6.1 Cre8 Barn, Yorkshire, UK (EnerPHit Retrofit)
The Cre8 Barn project in Slaithwaite, West Yorkshire, stands as a remarkable exemplar of an EnerPHit retrofit, showcasing the successful transformation of a dilapidated 19th-century agricultural barn into a high-performance, comfortable, and aesthetically preserved dwelling (netmagmedia.co.uk).
Background and Challenges: The barn, originally built of stone, presented significant challenges typical of heritage retrofits: maintaining its historical appearance, addressing a thermally leaky and non-airtight stone shell, and integrating modern building services without compromising the existing structure.
Solutions and Implementation: The project employed an innovative ‘box within a box’ strategy. Instead of insulating externally (which would have altered the stone facade) or internally by bonding insulation directly to the stone (risking moisture issues), a new, independent, super-insulated timber frame structure was constructed entirely within the existing stone shell. This inner structure formed the primary thermal envelope of the dwelling.
- Super-Insulation: The timber frame allowed for generous insulation depths. The walls were insulated with approximately 300mm of mineral wool, the roof with up to 500mm, and the floor slab with 200mm of rigid insulation, achieving U-values significantly below EnerPHit targets (e.g., walls below 0.15 W/(m²·K)).
- Thermal Bridge-Free Design: The ‘box within a box’ approach inherently minimized thermal bridges between the new inner structure and the old outer shell. Where connections were necessary (e.g., for windows), thermally broken elements were utilized.
- Airtightness: A continuous air barrier was meticulously formed around the entire new timber frame, utilizing intelligent vapor control membranes and high-performance airtightness tapes. Multiple blower door tests were conducted during construction to ensure the stringent EnerPHit airtightness target of n50 ≤ 1.0 h⁻¹ was achieved.
- High-Performance Windows and Doors: New, triple-glazed, Passivhaus-certified timber windows were installed within the new inner frame. These were carefully detailed to connect seamlessly with the air barrier and insulation layers.
- MVHR System: A high-efficiency MVHR unit was installed to provide continuous fresh, filtered air, recovering heat from the exhaust air. Ductwork was carefully routed within the new timber frame structure to maintain efficiency and minimize noise.
- Heating System: Due to the exceptionally low heat loss, the main heat source was a small air-source heat pump primarily serving domestic hot water, with minimal supplementary heating required.
Outcomes: The Cre8 Barn achieved EnerPHit certification, demonstrating a dramatic reduction in energy consumption for heating and a significant improvement in indoor comfort. The ‘box within a box’ solution successfully preserved the barn’s rural character while transforming it into a cutting-edge, sustainable dwelling. It stands as a powerful testament to the adaptability and effectiveness of Passivhaus principles in challenging retrofit scenarios.
6.2 Residential Passive House, Melbourne, Australia
This single-family residential Passivhaus project in Melbourne, Australia, serves as an excellent illustration of adapting Passivhaus principles to a warmer climate with significant cooling demands, highlighting the crucial role of MVHR and smart design for summer comfort (passivehouseadelaide.com).
Climate Context: Melbourne experiences a temperate climate with hot summers (often exceeding 35°C) and cool, sometimes damp, winters, necessitating both effective heating and cooling strategies.
Solutions and Implementation:
- Super-Insulation & Airtightness: The house features high levels of insulation in walls (e.g., R-values equivalent to U-values around 0.15 W/(m²·K)) and roof, coupled with an exceptionally airtight envelope, verified by a blower door test achieving n50 well below 0.6 h⁻¹.
- High-Performance Glazing: Triple-glazed windows were selected for superior thermal performance, but critically, their Solar Heat Gain Coefficient (g-value) was carefully specified. While typically higher g-values are preferred for winter solar gain in cold climates, in Melbourne, a balance was struck to allow some winter gain while limiting excessive summer heat ingress. Strategic external shading (e.g., fixed eaves and adjustable external blinds) was implemented on east, west, and some north-facing windows to mitigate summer solar gain.
- Thermal Bridge-Free Construction: All junctions were meticulously detailed to eliminate thermal bridges, ensuring consistent performance of the envelope.
- MVHR Integration: A central, high-efficiency MVHR unit was installed. Its strategic placement (often in a dedicated service cupboard or garage) minimized noise transmission to living areas. The ductwork was carefully designed with radial runs and insulated to maintain thermal performance. The MVHR continuously supplies fresh, filtered air, essential for maintaining high indoor air quality (low CO2 levels, controlled humidity) even when external temperatures are extreme or air quality is poor (e.g., during bushfire smoke events).
- Passive Cooling and Minimal Active Cooling: The robust thermal envelope, effective shading, and nightly natural ventilation (manual opening of windows for ‘night purging’ when outside temperatures drop) significantly reduce cooling loads. While a small, highly efficient split-system air conditioner might be present, it runs for minimal hours, primarily as a backup during prolonged heatwaves, demonstrating the effectiveness of passive strategies.
Outcomes: The Melbourne Passivhaus consistently maintains comfortable internal temperatures year-round with minimal energy input for heating or cooling. Indoor air quality is excellent, and external noise is significantly attenuated. This project illustrates that Passivhaus is not solely for cold climates but is a versatile standard that can be adapted to deliver high performance and comfort across a wide range of climatic conditions, with particular attention paid to shading and overheating prevention in warmer regions.
6.3 Muhlgraben Elementary School, Germany (Public/Commercial Scale)
This project, completed in 2011, showcases the scalability of the Passivhaus standard to larger, more complex public buildings, demonstrating its applicability beyond single-family homes.
Background: The Muhlgraben Elementary School in Hanover, Germany, was designed to accommodate 400 pupils across 16 classrooms. The key drivers were to provide a healthy, comfortable learning environment while achieving extremely low operational costs and a minimal environmental footprint.
Solutions and Implementation:
- Optimized Building Form and Envelope: The school building was designed with a compact form to minimize external surface area relative to its volume, reducing heat loss. The entire building envelope was constructed with exceptionally high levels of insulation (e.g., walls with U-values around 0.12 W/(m²·K)) and achieved exemplary airtightness.
- Large-Scale MVHR Systems: Given the high occupancy and large volume, multiple high-capacity MVHR units were integrated. These systems were meticulously designed to ensure adequate ventilation rates for all classrooms and common areas, managing CO2 levels effectively to maintain a conducive learning environment. The heat recovery significantly reduced the energy demand for heating the large volume of incoming fresh air.
- Daylighting and Shading: Large windows were strategically placed to maximize natural daylight, reducing the need for artificial lighting. However, to prevent overheating in classrooms, external automated shading devices (louvers/blinds) were installed, which adjust based on solar intensity and internal temperature.
- Minimal Heating System: The ultra-low heating demand meant that a conventional large boiler system was unnecessary. Instead, a small, highly efficient heat pump provided supplementary heating and domestic hot water, primarily serving small heating coils within the MVHR supply air ducts, ensuring comfortable incoming air temperatures.
Outcomes: The Muhlgraben School achieved Passivhaus certification, demonstrating heating energy consumption less than 15 kWh/(m²a), a fraction of typical school buildings. This resulted in significant operational cost savings for the municipality. Beyond energy performance, the school reported excellent indoor air quality, consistent thermal comfort, and a quiet learning environment, contributing positively to student concentration and well-being. This project proved that Passivhaus principles are not limited to residential buildings but are highly effective and scalable for large-volume public and commercial applications.
Many thanks to our sponsor Focus 360 Energy who helped us prepare this research report.
7. Future Outlook and Broader Impact
The Passivhaus standard has evolved from a niche concept to a globally recognized benchmark for high-performance building. Its future outlook is one of increasing adoption, further innovation, and a growing impact on broader sustainable building practices and policy.
Evolution of the Standard: The introduction of Passivhaus Plus and Premium certifications signifies a deliberate move towards ‘Net Zero Energy’ and ‘Energy Positive’ buildings. This evolution ensures the standard remains at the forefront of decarbonization efforts, encouraging on-site renewable energy generation in addition to extreme efficiency. This tiered approach provides a clear pathway for projects to aim for ever-higher levels of sustainability and energy independence.
Increasing Mainstream Adoption: As awareness of climate change intensifies and energy prices remain volatile, the demand for resilient, low-energy buildings is rising. Governments and municipalities are increasingly recognizing the value of Passivhaus. For instance, Brussels made Passivhaus the mandatory standard for all new buildings from 2015. Several other cities and countries are either adopting similar policies or offering strong incentives for Passivhaus construction. This governmental push, combined with growing consumer demand, is driving the mainstream adoption of the standard.
Addressing Misconceptions: Common misconceptions, such as Passivhaus buildings being ‘sealed boxes’ (ignoring MVHR’s role in providing fresh air) or being ‘too expensive’ (ignoring life-cycle cost benefits), are steadily being debunked as more projects are built and data becomes available. The increasing number of certified professionals and builders is also improving cost-effectiveness and buildability.
Technological Advancements: Ongoing research and development are leading to even more efficient components (e.g., MVHR units with higher heat recovery rates, thinner high-performance insulation materials, smart building controls integrated with MVHR). The use of advanced building information modeling (BIM) and simulation tools is streamlining the design process, making Passivhaus design more accessible and efficient.
Impact on Public Health and Well-being: Beyond energy savings, the focus on superior indoor air quality, consistent thermal comfort, and acoustic performance of Passivhaus buildings has a profound positive impact on occupant health and productivity. Reduced exposure to pollutants and allergens, stable temperatures, and quiet environments contribute to better sleep, fewer respiratory issues, and enhanced overall well-being. This human-centric benefit is a powerful driver for adoption.
Climate Resilience: Passivhaus buildings are inherently resilient to climate extremes. Their robust, super-insulated envelopes and airtightness mean they perform exceptionally well during heatwaves or cold snaps, maintaining comfortable internal temperatures even during power outages or grid stresses, offering a valuable layer of protection in an era of increasing climate unpredictability.
Contribution to Decarbonization: By drastically reducing operational energy demand, Passivhaus significantly lowers a building’s carbon footprint. When combined with renewable energy sources, it offers a pathway to truly carbon-neutral or carbon-positive built environments, playing a critical role in global efforts to achieve net-zero emissions targets. It demonstrates that deep energy reductions are achievable and practical for all building types and scales.
In conclusion, the Passivhaus standard offers a comprehensive and scientifically proven framework for designing and constructing energy-efficient buildings that deliver superior indoor comfort, health, and resilience. While the initial investment may be higher, the long-term benefits, including substantial energy savings, improved indoor air quality, increased property value, and reduced environmental impact, unequivocally position Passivhaus as a leading solution for sustainable construction. By adhering to its rigorous principles, embracing integrated design, and fostering skilled craftsmanship, stakeholders can achieve buildings that are not only sustainable and comfortable but also economically viable and future-proofed against the evolving challenges of energy and climate. Passivhaus is not merely a standard; it is a philosophy that drives innovation and sets a new paradigm for the built environment of tomorrow.
Many thanks to our sponsor Focus 360 Energy who helped us prepare this research report.
References
- netmagmedia.co.uk – Going for the Gold Standard: Cre8 Barn Retrofit
- passivehouseadelaide.com – Case Studies: Successful Implementation of MVHR in Passive House Buildings (Referenced for Melbourne)
- mdpi.com – Sustainability Journal – Recent Advances in Passive House Design (General)
- mdpi.com – International Journal of Environmental Research and Public Health – Indoor Air Quality in Passive House Buildings (General)
- sava.co.uk – The Fundamentals of Passivhaus (General Principles)
- rileycarter-architecture.com – Passive House Certification Requirements (Certification Process)
- mdpi.com – Buildings Journal – Thermal Bridge Free Design (General)
- iaskeding.com – Passive House Standards and their Role in Renewable Energy Efficiency (Renewable Energy)
- calctree.com – Passive House Energy (General Energy Metrics)
- thetwoarchitects.com – Passive House Benefits (General Benefits)
- Passivhaus Institut (PHI) Official Website. (Numerous resources on principles, certification, components, and case studies).
- International Passive House Association (IPHA). (Various publications and case studies on global adoption).
- Feist, W. (1993). Passive House Design: A Guide for Practitioners. Passivhaus Institut.
- Adamson, B., & Feist, W. (1998). ‘The Passive House – Minimum Energy Consumption and Highest Comfort.’ International Journal of Sustainable Energy, 18(2), 166-170.
- Schnieders, J. (2012). Passive House Explained: The Design and Construction Handbook. Earthscan.
- European Passive House Institute. (Various technical papers and reports on cost-effectiveness and climate adaptation).
The case studies highlight successful MVHR integration. Given the increasing focus on indoor air quality, how might future Passivhaus designs further optimize MVHR systems for enhanced filtration of pollutants, particularly in urban or industrial environments?
That’s a great question! Future MVHR systems could incorporate multi-stage filtration, including activated carbon filters for VOCs and specialized filters for particulate matter specific to urban or industrial pollutants. Real-time air quality monitoring integrated with the MVHR could also dynamically adjust filtration levels for optimal IAQ. It’s an exciting area of development!
Editor: FocusNews.Uk
Thank you to our Sponsor Focus 360 Energy
Impressive! Passivhaus seems like the gold standard. Wondering if these principles could be adapted for temporary structures, like disaster relief shelters, to provide immediate, efficient housing solutions in crisis situations?
That’s an incredibly insightful point! The adaptability of Passivhaus principles for temporary structures is an exciting area. Using modular, super-insulated panels coupled with efficient MVHR systems could create truly life-saving, comfortable disaster relief shelters. It would offer a significant improvement over conventional options. Thanks for sparking this idea!
Editor: FocusNews.Uk
Thank you to our Sponsor Focus 360 Energy
The report’s emphasis on minimizing operational energy consumption is a game changer. As building owners become more aware of life-cycle costs, Passivhaus design’s focus on superior insulation and airtightness makes it an increasingly attractive and sustainable investment.
Absolutely! You’re spot on. This growing understanding of life-cycle costing is really driving interest. It’s not just about the initial expense; it’s about the long-term value and resilience that Passivhaus provides. We’re seeing more owners factoring in reduced maintenance and increased asset value, making it a clear win-win.
Editor: FocusNews.Uk
Thank you to our Sponsor Focus 360 Energy
So, Passivhaus buildings are great at minimizing energy demand, but what about structures that *need* to use a lot of energy, like data centers or vertical farms? Could Passivhaus principles be modified to make those energy-intensive buildings more sustainable too?
That’s a fantastic question! It highlights a critical area for innovation. Absolutely, Passivhaus principles can be adapted! For energy-intensive buildings, focusing on waste heat recovery and optimized energy distribution, combined with a super-insulated envelope to minimize losses, offers a pathway to significant sustainability gains. It requires rethinking the energy flows, but the potential is huge! What are your thoughts?
Editor: FocusNews.Uk
Thank you to our Sponsor Focus 360 Energy
This report clearly articulates Passivhaus benefits beyond energy consumption, especially concerning occupant health and well-being. Further research into the correlation between IEQ in Passivhaus buildings and cognitive performance could strengthen the argument for wider adoption, particularly in educational and office environments.
Thank you for highlighting the occupant health and well-being aspect! Absolutely agree that further research on the correlation between IEQ and cognitive performance, especially in schools and offices, could be a game-changer for wider Passivhaus adoption. It could really emphasize the comprehensive benefits!
Editor: FocusNews.Uk
Thank you to our Sponsor Focus 360 Energy
Ultra-low energy, eh? Does this mean my phone battery will last longer if I’m inside a Passivhaus? Asking for a friend (who is me, constantly searching for outlets).
That’s a fun question! While a Passivhaus won’t directly charge your phone, the reduced energy consumption and stable grid load *could* mean fewer power outages overall. Perhaps fewer trips searching for outlets are on the horizon for your friend! This sparks an interesting discussion about energy resilience and the future of sustainable living.
Editor: FocusNews.Uk
Thank you to our Sponsor Focus 360 Energy
Fantastic report! But does Passivhaus design account for the energy used by my robot vacuum? I mean, keeping all that ultra-low energy dust at bay is a serious commitment to indoor air quality!
That’s such a great point! While the Passivhaus standard directly addresses building-related energy, the energy consumption of household appliances certainly adds to the overall picture. Optimizing appliance efficiency and considering renewable energy sources to power them are essential steps toward holistic sustainability. Does your robot vacuum have an energy star rating? What are your thoughts about appliances?
Editor: FocusNews.Uk
Thank you to our Sponsor Focus 360 Energy
Ultra-low energy and superior air quality, you say? What about the embodied carbon of the materials used in construction? Surely those super-insulated walls and fancy windows have a carbon footprint of their own. Is anyone measuring the long-term impact of material choices?
That’s an incredibly important point! Embodied carbon is absolutely crucial. We’re seeing growing interest in materials like wood fibre insulation and recycled content options to address this. Life Cycle Assessments (LCAs) are becoming more common to evaluate the full environmental impact. What other low embodied carbon materials do you find promising?
Editor: FocusNews.Uk
Thank you to our Sponsor Focus 360 Energy
The mention of heat pumps integrated into MVHR units is interesting! Combining these technologies could further reduce space requirements and installation costs, streamlining the path to Passivhaus certification and making it more accessible for diverse projects.
Great point about heat pump integration, it’s definitely a promising area! Thinking about the broader impact, more compact and cost-effective systems could open up Passivhaus to a wider range of building types and budgets. Hopefully this can assist in expanding the approach and making energy efficiency more accessible.
Editor: FocusNews.Uk
Thank you to our Sponsor Focus 360 Energy
The reference to Passivhaus Premium as energy positive is particularly compelling. It would be interesting to see more data on the long-term performance of these buildings, especially regarding battery storage and grid interaction to maximize the benefits of on-site renewable energy generation.
That’s a fantastic point! I agree, robust data on the long-term operation of Premium certified buildings is essential. Battery storage and smart grid integration will definitely be key to maximizing their positive energy contributions. It opens up a fascinating discussion on how buildings can become active participants in the energy grid.
Editor: FocusNews.Uk
Thank you to our Sponsor Focus 360 Energy
The discussion of Passivhaus Premium as energy positive is very interesting. The potential for these buildings to offset their embodied carbon over their lifespan through excess energy generation deserves further investigation. Perhaps future research can quantify this offset and compare it across different building typologies.
That’s an excellent point about embodied carbon offset! Quantifying this across different building types is a vital area for future research. Understanding the true lifecycle impact will strengthen the case for Passivhaus Premium as a pathway to carbon neutrality. Let’s hope more studies emerge! What specific building typologies do you think would be most impactful to study?
Editor: FocusNews.Uk
Thank you to our Sponsor Focus 360 Energy
The discussion of integrating renewable energy sources is key, particularly the transition to Passivhaus Premium. How can policy incentivize on-site renewable energy generation in urban areas where space is limited? Perhaps focusing on community-scale solutions alongside building-integrated renewables is required.
That’s a crucial point! Exploring policy incentives for on-site renewable energy generation in urban settings with limited space is vital for wider Passivhaus Premium adoption. Community-scale solutions combined with building-integrated renewables are a viable approach. Perhaps we can look at grants for shared renewable energy infrastructure?
Editor: FocusNews.Uk
Thank you to our Sponsor Focus 360 Energy