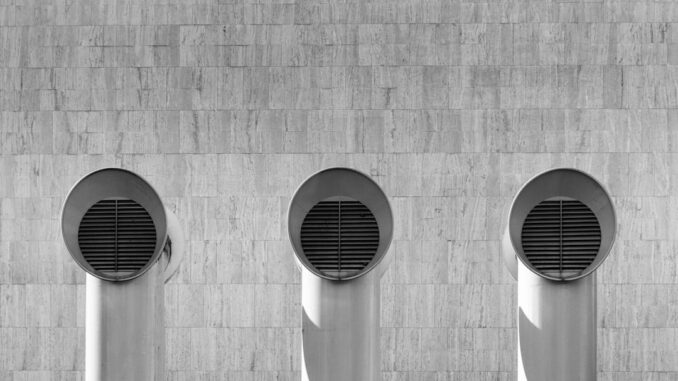
Abstract
Mechanical Ventilation with Heat Recovery (MVHR) systems are now an indispensable element in contemporary building design, serving as a cornerstone for achieving enhanced energy efficiency and superior indoor air quality. This comprehensive report meticulously examines MVHR systems, delving into their diverse types, fundamental design principles, critical installation best practices, profound health benefits, detailed operational costs, crucial noise considerations, systematic troubleshooting methodologies, and essential regulatory compliance. By synthesising current research, established industry standards, and best-practice guidelines, this report aims to furnish professionals with an exhaustive resource to facilitate the optimisation of MVHR system performance and seamless integration within diverse building typologies.
Many thanks to our sponsor Focus 360 Energy who helped us prepare this research report.
1. Introduction
The global imperative for energy conservation and the concurrent drive towards significantly improved airtightness in modern building construction have unequivocally elevated Mechanical Ventilation with Heat Recovery (MVHR) systems from a niche technology to a foundational building service. Historically, buildings relied on uncontrolled infiltration through natural leakages in the building envelope for ventilation. However, as energy prices escalated and environmental concerns grew, design strategies shifted towards creating highly insulated and airtight structures to minimise heating and cooling loads. While this approach dramatically reduced energy waste, it inadvertently trapped indoor pollutants and moisture, leading to compromised indoor air quality (IAQ) and potential structural degradation, often termed ‘sick building syndrome’.
MVHR systems emerged as the sophisticated solution to this paradox. These advanced systems are meticulously engineered to provide continuous, controlled ventilation by simultaneously supplying fresh, filtered outdoor air and extracting stale, polluted indoor air. Crucially, they incorporate a highly efficient heat exchanger that recovers a substantial portion of the thermal energy from the outgoing exhaust air and uses it to pre-condition the incoming fresh air. This innovative heat recovery mechanism significantly reduces the energy demand associated with heating or cooling ventilation air, making MVHR systems pivotal in achieving stringent energy performance targets, including those mandated by Passive House standards and Net Zero energy initiatives. This report systematically dissects the multifaceted aspects of MVHR systems, offering profound insights into their intricate design, precise installation, sophisticated performance optimisation, and unwavering compliance with evolving regulatory standards, thereby underscoring their critical role in fostering healthier, more energy-efficient, and sustainable built environments.
Many thanks to our sponsor Focus 360 Energy who helped us prepare this research report.
2. Types and Configurations of MVHR Systems
The efficacy and suitability of an MVHR system are intrinsically linked to its fundamental design, particularly its heat exchange mechanism and airflow configuration. A thorough understanding of these classifications is paramount for informed system selection and optimisation for specific building applications.
2.1 Heat Exchange Mechanisms
At the core of every MVHR unit lies its heat exchanger, the component responsible for transferring thermal energy between the two air streams without mixing them. The efficiency and characteristics of this transfer vary significantly among different types:
2.1.1 Thermal Wheel (Rotary Heat Exchanger)
Mechanism: A thermal wheel, also known as a rotary heat exchanger or enthalpy wheel, consists of a rotating cylindrical matrix, often made of corrugated aluminium or polymer, impregnated with a desiccant material. As the wheel slowly rotates, sections of it pass alternately through the warm exhaust air stream and the cool incoming fresh air stream. Sensible heat is transferred as the material absorbs heat from the warmer air and releases it into the cooler air. Latent heat (moisture) is transferred as the desiccant material absorbs water vapour from the more humid air stream and desorbs it into the drier air stream.
Advantages:
* High Efficiency: Capable of recovering both sensible and latent heat, leading to higher overall heat recovery efficiency (often exceeding 80% total energy recovery). This latent heat recovery is particularly beneficial in humid climates or applications requiring strict humidity control.
* Frost Protection: The rotation and heat transfer typically prevent frost build-up on the exhaust side, reducing the need for electric pre-heaters or bypass mechanisms.
* Compact Design: Often more compact for a given airflow capacity compared to plate heat exchangers.
Disadvantages:
* Cross-Contamination Potential: Due to the rotating nature and slight pressure differences, there is a small potential for exhaust air to be carried over into the supply air. High-quality wheels are designed to minimise this, often incorporating purge sectors.
* Moving Parts: Requires a motor to rotate the wheel, leading to increased maintenance requirements and potential for mechanical wear.
* Maintenance: Regular cleaning is necessary to maintain efficiency and prevent particulate build-up.
Typical Applications: Ideal for applications where high overall energy recovery, including humidity transfer, is desired, such as in highly insulated residential buildings, commercial offices, or buildings in climates with significant humidity variations.
2.1.2 Fixed Plate Heat Exchanger (Counterflow or Crossflow)
Mechanism: This type comprises a series of closely spaced, alternating layers of parallel plates, typically made of aluminium or plastic, that separate the incoming fresh air and outgoing exhaust air streams. Heat is transferred by conduction through the plate material from the warmer air stream to the cooler air stream. The most efficient design is ‘counterflow’, where the two air streams flow in opposite directions, maximising the temperature difference along the entire length of the plates. ‘Crossflow’ designs are simpler but less efficient.
Advantages:
* No Moving Parts: Simplicity of design means lower maintenance requirements and higher reliability.
* Zero Cross-Contamination: The physical separation of the air streams by the plates ensures no mixing of supply and exhaust air, making them suitable for applications where air purity is critical (e.g., hospitals, laboratories).
* Durability: Robust construction provides a long operational life.
Disadvantages:
* Sensible Heat Only: Primarily recovers sensible heat, meaning it does not transfer moisture. This can lead to drier indoor air in winter or require supplementary dehumidification in summer.
* Frost Risk: In cold climates, moisture in the exhaust air can freeze on the exhaust side of the heat exchanger, potentially blocking airflow and reducing efficiency. This necessitates frost protection strategies such as pre-heating, exhaust air bypass, or temporary cessation of supply air.
* Larger Footprint: Can be larger for equivalent capacity compared to thermal wheels.
Typical Applications: Widely used in residential and commercial buildings where sensible heat recovery is the primary goal and cross-contamination is a concern. Common in Passive House designs due to their high sensible efficiency and lack of cross-contamination.
2.1.3 Heat Pipe Heat Exchanger
Mechanism: A heat pipe consists of a sealed tube containing a working fluid (refrigerant) that undergoes a phase change cycle. One end of the pipe (evaporator) is placed in the warmer air stream, where the fluid absorbs heat and evaporates. The vapour then travels to the cooler end (condenser), releases its latent heat as it condenses, and returns to the evaporator via gravity or a wick structure. An MVHR system typically uses a bank of these pipes to transfer heat between two separated air streams.
Advantages:
* Compact: Relatively compact for their heat transfer capacity.
* No Moving Parts: Similar to plate exchangers, they offer high reliability and low maintenance.
* No Cross-Contamination: Air streams are completely separate.
Disadvantages:
* Sensible Heat Only: Primarily transfers sensible heat, similar to fixed plate exchangers.
* Positioning: Performance can be sensitive to orientation, particularly for gravity-assisted types.
* Cost: Can be more expensive than other options for some applications.
Typical Applications: Often found in commercial HVAC systems, where heat recovery between separate air streams is required, or where space is limited.
2.1.4 Run-Around Coil System
Mechanism: This system employs two separate finned coil heat exchangers—one positioned in the exhaust air stream and the other in the incoming fresh air stream. A closed-loop circulation pump continuously circulates a heat transfer fluid (e.g., water, glycol solution) between these two coils. The fluid absorbs heat from the warmer air stream in one coil and releases it to the cooler air stream in the other coil.
Advantages:
* Flexible Placement: The intake and exhaust air streams do not need to be adjacent, offering significant flexibility in architectural design and system layout.
* No Cross-Contamination: Air streams are entirely separate.
* Suitable for Multiple Streams: Can be used to recover heat from multiple exhaust air streams and transfer it to multiple supply air streams.
Disadvantages:
* Lower Efficiency: Typically less efficient than plate or rotary heat exchangers due to two heat transfer stages (air-to-fluid, fluid-to-air) and pump energy consumption.
* Higher Complexity: Involves more components (two coils, pump, piping, fluid) than static heat exchangers, potentially increasing installation and maintenance complexity.
* Pump Energy: The circulating pump consumes energy, which impacts overall system efficiency.
Typical Applications: Primarily used in situations where ducting constraints prevent the use of compact, single-unit heat exchangers, such as in retrofits or large commercial/industrial buildings with widely separated air handling units.
2.2 Airflow Configurations
Beyond heat exchange, the balance of supply and extract airflows dictates the pressure regime within the building envelope, which has significant implications for energy performance, comfort, and building integrity.
2.2.1 Balanced Systems
Description: In a balanced MVHR system, the volume of air supplied to the building is designed to be equal to the volume of air extracted from it. This maintains a near-neutral pressure differential between the inside and outside of the building.
Implications:
* Optimal Performance: Ensures that the heat recovery unit operates at its designed efficiency by maintaining steady airflow across the heat exchanger.
* Controlled Environment: Prevents uncontrolled air infiltration or exfiltration through the building fabric, which can lead to energy losses or moisture issues.
* Comfort: Minimises draughts, ensuring a comfortable indoor environment.
* Moisture Management: Reduces the risk of moisture-laden air being driven into the building structure, preventing condensation and mold growth within walls or cavities.
Typical Applications: The most common and recommended configuration for airtight, energy-efficient buildings, including Passive Houses, where precise control over the indoor environment is critical.
2.2.2 Positive Pressure Systems
Description: In a positive pressure system, the supply airflow rate is intentionally set to exceed the extract airflow rate, creating a slight positive pressure inside the building relative to the outside.
Implications:
* Pollutant Exclusion: This positive pressure helps to prevent the uncontrolled ingress of outdoor pollutants (e.g., dust, pollen, external odours) through cracks or gaps in the building envelope, as air is constantly being pushed outwards.
* Energy Consumption: May lead to higher energy consumption due to increased fan power for the supply fan or if conditioned air is forced out through unintended leakages.
* Moisture Risk: In cold climates, if warm, humid indoor air is pushed into cold wall cavities, it can condense, leading to interstitial condensation and potential mold or structural damage. This requires meticulous vapour control layer design.
Typical Applications: Sometimes used in specific industrial applications or cleanrooms where preventing the ingress of contaminants is paramount, or in very specific residential designs where a slight positive pressure is desired to minimise outdoor air intrusion, provided the building envelope is meticulously sealed and vapour control is assured.
2.2.3 Negative Pressure Systems
Description: Conversely, a negative pressure system operates with the extract airflow rate exceeding the supply airflow rate, resulting in a slight negative pressure inside the building.
Implications:
* Uncontrolled Infiltration: A negative pressure can draw unconditioned and unfiltered outdoor air into the building through any unintentional openings, bypassing the MVHR unit and negating its energy recovery and filtration benefits.
* Increased Energy Load: The uncontrolled infiltration can significantly increase heating or cooling loads.
* Discomfort: Can lead to uncomfortable drafts and uneven temperature distribution.
* Backdrafting: Potentially dangerous in buildings with combustion appliances (e.g., fireplaces, gas water heaters) that are not sealed combustion or direct-vented, as it can cause backdrafting of combustion gases into the living space.
Typical Applications: Rarely used in residential or commercial MVHR setups. More common in industrial processes where containing contaminants or odours within specific zones (e.g., fume hoods, paint booths) is the primary concern, requiring specific safety considerations for building occupants.
Many thanks to our sponsor Focus 360 Energy who helped us prepare this research report.
3. Design Principles for Optimal Performance
Achieving an MVHR system that not only meets but exceeds performance expectations requires meticulous attention to a hierarchy of design principles, ensuring a synergistic interplay between the unit, its distribution network, and the wider building physics.
3.1 System Sizing
Accurate system sizing is the bedrock of an efficient and effective MVHR installation. An incorrectly sized unit can lead to myriad problems, from insufficient ventilation and compromised indoor air quality to excessive noise and disproportionate energy consumption.
Calculation Methodologies: System sizing is primarily determined by calculating the required ventilation rates based on building occupancy, volume, and usage. Leading standards and regulations provide detailed methodologies:
- ASHRAE 62.1 (Commercial) and 62.2 (Residential): These standards specify minimum outdoor air ventilation rates per person and/or per unit area to ensure acceptable indoor air quality. For residential buildings, ASHRAE 62.2, ‘Ventilation and Acceptable Indoor Air Quality in Residential Buildings’, provides formulas considering dwelling size and number of bedrooms.
- Building Regulations (e.g., UK Approved Document F): These documents stipulate minimum extract rates for ‘wet’ rooms (kitchens, bathrooms, utility rooms) and minimum whole-house ventilation rates based on dwelling airtightness, number of bedrooms, and total volume. They often require ‘intermittent’ (boost) rates and ‘trickle’ (continuous) rates.
- Passive House Standard: Requires a continuous ventilation rate that ensures an air change rate of approximately 0.3 to 0.5 air changes per hour (ACH) in the entire dwelling, or based on occupant-driven CO2 levels. They also emphasise very low Specific Fan Power (SFP) values.
Impact of Undersizing: An undersized MVHR unit will perpetually struggle to meet the required airflow rates. This leads to:
* Compromised IAQ: Inadequate removal of pollutants (CO2, VOCs, moisture) and insufficient supply of fresh air.
* Increased Fan Speed and Noise: The unit’s fans will run at higher speeds to attempt to achieve target airflows, resulting in significantly increased noise levels and faster wear.
* Higher Specific Fan Power (SFP): Less efficient operation, consuming more electricity per litre per second of air moved.
* Reduced Heat Recovery Efficiency: Air may move too quickly through the heat exchanger, reducing the contact time and thus the efficiency of heat transfer.
Impact of Oversizing: While seemingly benign, an oversized unit also presents inefficiencies:
* Higher Capital Cost: Larger units are inherently more expensive to purchase.
* Reduced Efficiency at Part Load: Fans and heat exchangers are most efficient when operating near their design point, typically 50-70% of maximum capacity. An oversized unit running at a low percentage of its capacity often operates inefficiently, resulting in higher Specific Fan Power (SFP) than a correctly sized unit.
* Increased Standby Power: Larger units may have higher parasitic loads.
* Space Requirements: Physically larger units demand more installation space.
Optimal Operating Range: Industry best practice suggests sizing the MVHR unit such that it operates at approximately 50-70% of its maximum capacity during typical continuous (trickle) operation. This allows for headroom for boost ventilation (e.g., during cooking or showering) and ensures the fans operate within their most efficient and quietest performance curve.
3.2 Ductwork Design
The ductwork system is as critical as the MVHR unit itself, acting as the circulatory system of the building’s ventilation. Suboptimal ductwork design can negate the benefits of even the most efficient MVHR unit.
3.2.1 Duct Material
- Rigid Galvanised Steel (Spiro): This is the preferred material for main runs and longer sections due to its inherent advantages:
- Durability: Robust and long-lasting.
- Low Airflow Resistance: Smooth internal surface minimises friction losses, reducing static pressure and fan energy consumption.
- Acoustic Performance: Less prone to vibration noise compared to flexible ducts.
- Cleanliness: Less likely to harbour dust or microbial growth if properly maintained.
- Fire Resistance: Better fire performance than plastic ducts.
- Semi-Rigid Ducting (Radial Systems): Often used in radial systems where each supply/extract terminal has its own dedicated duct run back to a manifold connected to the MVHR unit. These are typically made of high-density polyethylene (HDPE).
- Flexibility: Easier to install in confined spaces and navigate around obstructions.
- Acoustic Attenuation: Some designs incorporate internal corrugations that can help attenuate noise.
- Ease of Sealing: Push-fit connections with rubber gaskets make sealing simpler and more reliable if installed correctly.
- Pressure Drop: Can have higher static pressure losses than smooth rigid ducting if not sized generously or if kinks occur.
- Flexible Ducting: Generally discouraged for MVHR systems due to:
- High Pressure Drop: Corrugated internal surfaces create significant friction, reducing airflow and increasing fan energy.
- Dust Traps: Prone to collecting dust and moisture, leading to poor IAQ and potential mold growth.
- Kinking: Easily kinked, further restricting airflow.
- Noise Transmission: Poor acoustic performance.
- Should only be used for very short connections (max 1-2m) to terminal units or silencers if absolutely unavoidable, and stretched taut to minimise corrugations.
3.2.2 Duct Insulation
Proper insulation of ductwork is non-negotiable for MVHR systems, particularly for ducts running through unheated or unconditioned spaces (e.g., lofts, crawl spaces, external walls).
* Heat Loss/Gain Prevention: Minimises thermal losses from conditioned air in winter and gains in summer, maintaining the effectiveness of heat recovery and reducing load on the main heating/cooling system.
* Condensation Prevention: Critical for preventing interstitial condensation within the ductwork, which can lead to:
* Mold and Bacterial Growth: A significant IAQ risk and source of unpleasant odours.
* Water Damage: Dripping water from ducts can damage finishes or building components.
* Corrosion: Of metallic ductwork.
* Acoustic Attenuation: External insulation can also contribute to reducing noise breakout from ducts.
* Vapour Barrier: Insulation materials should include a robust vapour barrier on the warm side of the insulation to prevent moisture migration and condensation within the insulation itself.
3.2.3 Duct Layout
An intelligently designed duct layout is fundamental to minimising pressure losses, reducing noise, and facilitating maintenance.
* Minimise Sharp Bends: Each 90-degree bend significantly increases pressure drop. Use sweeping, large-radius bends (e.g., two 45-degree bends instead of one 90-degree) or purpose-designed fittings to reduce turbulence and pressure loss. Ensure smooth transitions.
* Optimal Velocity: Design for appropriate air velocities. Main supply and extract ducts should typically aim for velocities of 2-3 m/s, while branch ducts can be slightly higher (3-4 m/s). Excessive velocity leads to higher pressure drop and airborne noise.
* Duct Sizing: Generously size ducts to achieve desired flow rates at low velocities. This means a larger cross-sectional area, which reduces friction and fan energy. Undersized ducts lead to higher velocities, increased pressure drop, noise, and energy consumption.
* Adequate Support: Ducts must be securely supported at regular intervals (e.g., every 1.5-2m for rigid ducts) to prevent sagging, which can create traps for condensate, restrict airflow, and increase noise. Use purpose-designed hangers and straps.
* Airtightness: All duct connections must be meticulously sealed to prevent air leakage. Even small leaks can significantly reduce system efficiency and compromise heat recovery. Techniques include mastic sealant, high-quality aluminium tape, and mechanical clamps for rigid ducting. Semi-rigid systems typically use push-fit connections with rubber gaskets, often reinforced with clips.
* Accessibility: Design duct runs with accessible points for inspection and cleaning, especially for longer runs or complex networks. Consider access hatches for filters or dampers.
* Cross-Talk Prevention: In multi-room systems, design duct routes and incorporate silencers to prevent sound transmission between rooms via the ductwork.
3.3 Filtration and Humidity Control
Beyond just moving air, MVHR systems are instrumental in purifying and conditioning it, with filtration and humidity control being key elements.
3.3.1 Filtration
High-efficiency filtration is paramount for improving indoor air quality and protecting the MVHR unit components. Filters are typically specified using EN ISO 16890 or old EN779 standards (e.g., G4, F7, F9).
* Pre-filters (e.g., G3/G4): Installed on both supply and extract air streams. Their primary role is to protect the heat exchanger and finer filters from larger particulate matter like dust, pollen, and insects. They reduce the frequency of cleaning for finer filters and the heat exchanger.
* Fine Filters (e.g., F7, F8, F9): Typically installed on the supply air stream after the pre-filter. These are critical for removing smaller, more harmful particulate matter (PM2.5, PM10), allergens, spores, and some bacteria. F7 is often considered the minimum standard for residential MVHR in urban environments.
* Activated Carbon Filters: In areas with significant outdoor gaseous pollution (e.g., proximity to busy roads), activated carbon filters can be added to the supply air stream to absorb volatile organic compounds (VOCs) and odours.
* Maintenance: Filters must be regularly inspected, cleaned, or replaced according to manufacturer guidelines and local air quality. Clogged filters dramatically increase static pressure, reducing airflow, increasing fan energy consumption (and SFP), and compromising IAQ. Filter changes are a primary ongoing operational cost and maintenance task.
3.3.2 Humidity Control
Managing indoor humidity is crucial for occupant comfort, preventing mould growth, and protecting building materials.
* Enthalpy Heat Exchangers (Thermal Wheels): As discussed, these transfer both sensible and latent heat, effectively recovering moisture from exhaust air in winter and transferring it to the dry supply air, or removing moisture from humid supply air in summer. This can significantly reduce the need for supplementary humidification/dehumidification.
* Sensible Heat Exchangers (Plate, Heat Pipe): These do not transfer latent heat. In winter, they can lead to very dry indoor air, which can cause discomfort (dry skin, respiratory irritation) and static electricity. In summer, they don’t assist with dehumidification. Supplementary humidifiers or dehumidifiers may be required.
* Condensate Drainage: In cold climates, sensible heat exchangers will produce condensate from the exhaust air as it cools. A properly sloped and trapped condensate drain must be installed to safely remove this water to a waste pipe, preventing blockages, odours, and water damage. The condensate trap must be correctly sized and maintained to prevent air ingress or egress.
* Bypass Functions: Most MVHR units incorporate a ‘summer bypass’ function. When outdoor temperatures are cooler than indoors (e.g., at night in summer), the bypass diverts the incoming fresh air around the heat exchanger, allowing cooler air to enter the building without picking up heat from the exhaust air. This aids in passive cooling. Some units also have frost protection bypasses for extremely cold conditions.
Many thanks to our sponsor Focus 360 Energy who helped us prepare this research report.
4. Installation Best Practices
Even the most meticulously designed MVHR system will underperform if not installed correctly. Adherence to best practices during installation is paramount for system efficiency, longevity, and compliance with regulatory frameworks.
4.1 Compliance with Regulations
Navigating the complex landscape of building codes and standards is a critical pre-requisite for any MVHR installation. Compliance is not merely a legal obligation but a guarantee of performance, safety, and energy efficiency.
- National Building Codes: Most countries have national building regulations that dictate minimum ventilation rates, energy efficiency targets, and safety standards. For example, in the UK, Approved Document F of the Building Regulations outlines requirements for ventilation in dwellings, while Approved Document L covers energy efficiency, both of which MVHR systems help address. In the US, ASHRAE Standard 62.1 (for commercial buildings) and 62.2 (for residential buildings) provide detailed guidelines on acceptable indoor air quality and ventilation rates.
- Energy Performance Standards: MVHR systems are key components in achieving higher energy performance certifications like Passive House, LEED (Leadership in Energy and Environmental Design), and BREEAM (Building Research Establishment Environmental Assessment Method). Compliance with these standards often requires specific SFP (Specific Fan Power) values, heat recovery efficiencies, and airtightness targets.
- Health and Safety Regulations: Installation must comply with general health and safety at work regulations, electrical safety standards (e.g., IEC standards), and fire safety regulations, especially concerning ductwork penetration through fire-rated compartments.
- Local Authority Planning and Building Control: Obtaining necessary planning permissions and building control approvals is essential. This often involves submitting design drawings, calculations, and product specifications for review.
- Manufacturer Guidelines: Strict adherence to the MVHR unit manufacturer’s installation manual is fundamental. Failure to do so can invalidate warranties and lead to operational issues.
- Industry Best Practices: Beyond minimum regulations, following industry-recognised best practices (e.g., those from the Heat Recovery Ventilation Association, Passive House Institute) ensures optimal performance and avoids common pitfalls.
4.2 Installation Procedures
Precision and attention to detail during the physical installation are critical to translating theoretical design into practical performance.
4.2.1 Ductwork Installation
The ductwork is arguably the most labour-intensive and critical part of the MVHR installation, often determining overall system performance.
* Material Selection and Sizing: As detailed in Section 3.2.1, prioritise rigid ducting for main runs and appropriately sized semi-rigid for branches. Ensure duct diameters are adequate to achieve low air velocities and minimise pressure drop.
* Airtightness: This is paramount. All duct connections must be mechanically secured (e.g., with clamps, screws) and then meticulously sealed. Use high-quality, long-lasting sealing compounds (mastic sealant) or specialist airtight tapes (e.g., aluminium foil tape with strong adhesive, butyl tape). Avoid standard cloth-backed duct tape, which degrades over time. Ductwork pressure testing (e.g., to Class C or D as per EN 12237 or DW/144) prior to commissioning is highly recommended to verify airtightness.
* Insulation Continuity: Ensure continuous and appropriate insulation of all ducts running through unheated or unconditioned spaces (e.g., cold lofts, unheated basements, outside walls). The insulation should be tightly fitted, joints sealed with vapour barrier tape, and free from compression. This prevents heat loss/gain and, crucially, condensation within the ducts.
* Routing and Support: Plan duct routes to be as direct as possible, minimising bends. Where bends are necessary, use long-radius elbows. Ensure all ducting is adequately supported at regular intervals with appropriate hangers to prevent sagging, kinking, or vibration transmission. Avoid crushing or distorting ductwork during installation, particularly semi-rigid types.
* Condensate Drainage from Ducts: If ducts pass through zones where the air temperature could drop below the dew point of the air inside the duct (e.g., supply air duct in a very cold attic), they may also require sloping and supplementary drainage points, in addition to the main unit’s condensate drain.
4.2.2 Unit Placement
The location and mounting of the MVHR unit significantly impact its operational performance, noise levels, and ease of maintenance.
* Solid, Stable Surface: The MVHR unit, often weighing a significant amount, must be securely mounted on a solid, level surface capable of bearing its weight and resisting vibration. Wall mounts should be robustly fixed to structural elements.
* Vibration Isolation: Use anti-vibration mounts (e.g., rubber pads, spring isolators) between the unit and the mounting surface to prevent mechanical vibration from transmitting through the building structure, which can be a major source of noise.
* Acoustic Separation: Locate the unit away from habitable spaces, especially bedrooms. Good locations include utility rooms, plant rooms, garages, or dedicated service voids. If placement in or near occupied areas is unavoidable, specify an acoustically attenuated unit and ensure robust sound insulation for the room it is in.
* Maintenance Access: Crucially, ensure sufficient clear space around the unit for future maintenance tasks, including filter changes, condensate trap cleaning, heat exchanger removal, and access to electrical components. Refer to manufacturer’s specified clearances.
* Proximity to External Vents: Position the unit as close as practically possible to the external intake and exhaust grilles to minimise long external duct runs, which are prone to heat loss and potential condensation or frost issues.
* Frost Protection: Ensure the unit is located in an area that does not drop below freezing, or if it must be, specify a unit with robust internal frost protection or incorporate an external pre-heater.
4.2.3 External Terminations
The positioning of external grilles is vital for system performance and preventing issues.
* Separation of Intake and Exhaust: Maintain adequate separation between the fresh air intake grille and the stale air exhaust grille (typically a minimum of 2-3 metres, or as per manufacturer/regulatory guidelines) to prevent short-circuiting or recirculation of exhaust air back into the building. Consider prevailing wind directions.
* Pest and Debris Protection: Grilles must be robust, weather-resistant, and incorporate fine mesh screens to prevent the ingress of insects, birds, and larger debris, while still allowing adequate airflow without excessive pressure drop.
* Location: Avoid placing intake grilles near potential sources of pollution (e.g., boiler flues, car parks, waste bins, dryer vents, openable windows). Position grilles where they are accessible for cleaning but not easily vandalised.
* Snow and Rain: Design external grilles to minimise snow ingestion in winter and rainwater ingress, often achieved with louvred designs and drip trays.
4.2.4 Electrical Wiring and Controls
- Dedicated Circuits: MVHR units should be wired to a dedicated electrical circuit with appropriate circuit protection.
- Sensor Integration: Connect and calibrate all associated sensors (e.g., CO2 sensors, humidity sensors, occupancy sensors) to enable demand-controlled ventilation (DCV) and optimise operation.
- User Interface: Install user controls (e.g., boost switches, mode selection) in convenient locations and ensure they are clearly labelled and easy to understand for occupants.
- Building Management System (BMS) Integration: For larger commercial or complex residential systems, integrate the MVHR controls with the central BMS for centralised monitoring, scheduling, and fault diagnosis.
4.2.5 Commissioning
Commissioning is the final, indispensable step that verifies the installed system operates according to the design specifications and regulatory requirements. It transforms an installation into a functional, optimised system.
* Visual Inspection: Thoroughly inspect all installed components, including ductwork, insulation, sealing, unit mounting, and electrical connections, ensuring they meet quality standards and design drawings.
* Ductwork Pressure Testing: If not done earlier, conduct a pressure test of the entire ductwork system to identify and rectify any leaks. This is crucial for achieving high system efficiency.
* Airflow Balancing: This is the most critical commissioning step. Using calibrated airflow measurement devices (e.g., balometers, hot-wire anemometers, pitot tubes), measure the airflow at each supply and extract terminal. Adjust dampers and fan speeds on the MVHR unit to achieve the design airflow rates for each room and ensure overall system balance (supply = extract).
* Control System Verification: Test all control functions, including fan speed settings (trickle, boost), summer bypass, frost protection, filter alarms, and any integrated sensors (CO2, humidity). Ensure they respond correctly and automatically.
* Noise Testing: Conduct subjective and, if specified, objective noise measurements at key locations to ensure the system operates within acceptable acoustic limits. Address any excessive noise sources.
* Handover Documentation: Provide the client with comprehensive documentation, including an operation and maintenance (O&M) manual, as-built drawings, commissioning reports, warranty information, and recommended maintenance schedules. Crucially, provide training to the building occupants or facility managers on how to operate and maintain the system correctly, particularly filter replacement.
Many thanks to our sponsor Focus 360 Energy who helped us prepare this research report.
5. Health Benefits
MVHR systems are not merely energy-saving devices; they are powerful tools for enhancing public health and well-being by creating superior indoor air environments. Their health benefits extend far beyond basic ventilation.
5.1 Comprehensive Indoor Air Quality (IAQ) Improvement
MVHR systems systematically address a wide spectrum of indoor air pollutants, thereby elevating overall IAQ.
5.1.1 Particulate Matter Reduction
- PM2.5 and PM10: These microscopic airborne particles, originating from outdoor sources (traffic, industrial emissions, pollen, dust storms) and indoor activities (cooking, burning candles, cleaning), are significant health hazards. PM2.5 (particles smaller than 2.5 micrometres) can penetrate deep into the lungs and even enter the bloodstream, leading to respiratory and cardiovascular diseases.
- MVHR Mitigation: High-efficiency filters (e.g., F7, F9, HEPA) within MVHR units are highly effective at capturing these fine particulates from the incoming fresh air, preventing their ingress into the living space. Simultaneously, continuous extraction removes internally generated particulates, significantly reducing occupant exposure.
5.1.2 Gaseous Pollutant Dilution and Removal
- Volatile Organic Compounds (VOCs): Emitted from building materials (paints, glues, carpets, furniture), cleaning products, personal care products, and cooking. Exposure to VOCs can cause headaches, dizziness, respiratory irritation, and long-term health effects.
- Carbon Dioxide (CO2): A primary indicator of human occupancy and insufficient ventilation. Elevated CO2 levels (above 1000-1500 ppm) can lead to reduced cognitive function, fatigue, and headaches.
- Other Gaseous Pollutants: Including nitrogen oxides (NOx) from combustion, radon (a naturally occurring radioactive gas), and odours from various sources.
- MVHR Mitigation: By providing a continuous supply of fresh outdoor air and extraction of stale indoor air, MVHR systems effectively dilute and remove these gaseous pollutants. Demand-controlled ventilation (DCV) strategies, integrating CO2 and VOC sensors, can modulate fan speeds to precisely meet ventilation demands, ensuring optimal dilution without excessive energy use.
5.1.3 Bioaerosol and Allergen Control
- Mold Spores and Dust Mites: These common indoor allergens and irritants thrive in humid conditions. Mold can cause respiratory problems, allergies, and asthma exacerbations. Dust mites are a major trigger for asthma and allergic reactions.
- Pollen and Pet Dander: Outdoor allergens like pollen and indoor allergens like pet dander can significantly impact individuals with sensitivities.
- MVHR Mitigation: MVHR systems actively manage indoor humidity levels, preventing the build-up of moisture that supports mold and dust mite proliferation. The filtration system captures pollen, pet dander, and other airborne allergens from the incoming air, providing relief for allergy and asthma sufferers.
- Virus Transmission: While not a standalone solution for airborne disease transmission, continuous ventilation with filtered air helps dilute airborne pathogens (including viruses), reducing their concentration and potential for spread within the indoor environment.
5.2 Thermal Comfort and Well-being
Beyond air quality, MVHR systems contribute to a superior thermal environment and overall occupant well-being.
* Consistent Temperature and Humidity: By recovering heat and potentially moisture, MVHR systems help maintain more stable indoor temperatures and humidity levels, preventing large fluctuations that can cause discomfort.
* Reduced Draughts: Unlike traditional ventilation methods (e.g., trickle vents, opening windows), MVHR supplies conditioned air in a controlled manner, preventing cold spots or draughts, which can be a significant source of discomfort.
* Enhanced Productivity and Cognitive Function: Studies have shown that improved IAQ and thermal comfort positively impact cognitive performance, concentration, and overall productivity in educational and office environments.
* Alleviation of Sick Building Syndrome (SBS): By addressing a multitude of indoor environmental factors (IAQ, thermal comfort, noise), MVHR systems play a crucial role in mitigating symptoms associated with SBS, such as headaches, fatigue, and respiratory irritation.
5.3 Noise Reduction
MVHR systems enable occupants to keep windows closed, providing a critical barrier against external noise pollution from traffic, neighbours, or urban environments. This allows for a quieter indoor environment, which is vital for sleep quality, concentration, and overall peace of mind. While the MVHR unit itself produces some noise (addressed in Section 7), a well-designed and installed system ensures that its internal noise is minimal and less disruptive than external sources.
Many thanks to our sponsor Focus 360 Energy who helped us prepare this research report.
6. Operational Costs and Energy Savings
The integration of an MVHR system represents a strategic investment in long-term building performance, yielding substantial energy savings and a favourable lifecycle cost profile, despite a higher initial capital outlay.
6.1 Detailed Energy Efficiency Mechanisms
MVHR systems are fundamentally designed to minimise energy waste associated with ventilation, a significant load in modern airtight buildings.
* Heat Recovery Efficiency: The core principle is the recovery of thermal energy that would otherwise be exhausted to the outside. Modern MVHR units boast heat recovery efficiencies typically ranging from 75% to over 90%. This means that for every 100 units of heat in the exhaust air, 75 to 90 units are transferred back to the incoming fresh air. This directly reduces the demand on conventional heating systems in winter and, for enthalpy wheels, on cooling systems in summer by recovering latent heat.
* Reduced Infiltration Losses: In traditional, leaky buildings, uncontrolled air infiltration and exfiltration lead to significant energy losses. MVHR systems, by providing controlled ventilation within an airtight envelope, eliminate these uncontrolled losses, ensuring that all incoming air is pre-conditioned.
* Optimised Fan Energy (Specific Fan Power – SFP): While fans consume electricity, the overall energy balance is highly favourable. The SFP (W/(L/s)) is a crucial metric, representing the electrical power consumed by the fans per unit of airflow. A lower SFP indicates a more energy-efficient fan and ductwork system. Building standards increasingly specify maximum SFP values for MVHR units (e.g., Passive House targets SFP values below 0.45 W/(L/s)). Good duct design (low resistance) and efficient fan motors are critical for achieving low SFP.
* Demand-Controlled Ventilation (DCV): Advanced MVHR systems incorporate sensors (CO2, humidity, VOCs) that monitor indoor air quality. When pollutant levels are low (e.g., when the building is unoccupied or during periods of low activity), the system automatically reduces fan speed, thereby reducing energy consumption. When levels rise, fan speed increases. This ‘on-demand’ approach prevents over-ventilation and unnecessary energy expenditure.
* Summer Bypass: During cooler periods in summer, particularly at night, the summer bypass feature allows incoming air to bypass the heat exchanger. This prevents warming of the cool night air by the warmer exhaust air, facilitating passive cooling and reducing reliance on active cooling systems.
* Frost Protection: In very cold climates, frost can build up on the heat exchanger. MVHR units employ various frost protection strategies (e.g., pre-heaters, temporary bypass of supply air, intermittent reduction of supply flow) that ensure continuous operation while minimising energy use for de-frosting.
6.2 Lifecycle Costs (LCC)
Evaluating MVHR systems purely on initial capital cost is short-sighted. A comprehensive lifecycle cost analysis reveals their true economic value.
* Initial Capital Investment: This includes the cost of the MVHR unit itself, the extensive ductwork (materials and labour), external grilles, controls, and commissioning. MVHR systems typically have a higher upfront cost than basic intermittent extract fans or natural ventilation systems due to the complexity and components involved.
* Operating Costs: The primary ongoing operating cost is electricity consumption for the fans. While the fans run continuously, their low SFP and the substantial heat recovery mean the energy savings from reduced heating/cooling loads far outweigh the fan energy consumption in an energy-efficient building. Filter replacement is another key operational cost, typically required quarterly to annually depending on filter type and air quality.
* Maintenance Costs: Routine maintenance, such as filter replacement (which can often be done by the occupant), heat exchanger cleaning (annually or bi-annually, often by a professional), and professional servicing (every 1-3 years for system checks, fan inspection, and calibration), are necessary to maintain efficiency and prolong system life.
* Energy Savings: These are the most significant long-term financial benefits. By drastically reducing heating and cooling demands, MVHR systems lead to lower energy bills year after year. The payback period for the initial investment varies significantly based on energy prices, building airtightness, climate, and system efficiency, but is typically estimated between 5-15 years for residential applications.
* Ancillary Benefits: While harder to quantify financially, improved indoor air quality can lead to reduced healthcare costs due to fewer respiratory illnesses, increased productivity and cognitive function, and enhanced comfort and well-being, all contributing to the overall value proposition.
* Property Value: Homes equipped with high-performance ventilation systems like MVHR are often seen as more desirable and can command higher property values.
* Government Incentives: In some regions, government grants, subsidies, or tax incentives are available for installing energy-efficient ventilation systems, further improving the financial viability.
6.3 Smart Controls and Optimization
The intelligence embedded within modern MVHR systems significantly contributes to their operational efficiency.
* Occupancy-Based Control: Integration with presence detectors can automatically adjust ventilation rates based on occupancy levels.
* Scheduling: Programmable timers allow for reduced ventilation rates during unoccupied periods (e.g., work hours, holidays) and increased rates when needed.
* Integration with BMS: For larger buildings, seamless integration with a central Building Management System (BMS) allows for sophisticated control strategies, remote monitoring, fault diagnostics, and energy performance analysis.
* Predictive Control: Emerging technologies are incorporating external weather data and internal sensor readings to predict ventilation needs and proactively adjust system operation for optimal efficiency.
Many thanks to our sponsor Focus 360 Energy who helped us prepare this research report.
7. Noise Considerations
While MVHR systems are designed to enhance indoor comfort, noise generation can be a significant concern if not properly addressed during design and installation. Unacceptable noise levels can undermine occupant satisfaction and negate the benefits of improved air quality.
7.1 Sources of Noise
Understanding the various origins of noise is the first step towards effective mitigation:
* Fan Noise (Aerodynamic and Mechanical): This is the primary source of noise. It comprises:
* Aerodynamic Noise: Generated by the movement of air over fan blades and internal components. Higher fan speeds (e.g., during boost mode) significantly increase aerodynamic noise.
* Mechanical Noise: Produced by the fan motor, bearings, and vibration of the fan casing. Poorly balanced fans or worn bearings exacerbate this.
* Airflow Noise (Duct-Borne): Generated by air moving through the ductwork.
* High Air Velocities: Excessive air speeds in ducts (due to undersizing or high fan settings) create turbulent flow, leading to whooshing or whistling sounds at grilles and bends.
* Turbulence: Sharp bends, sudden changes in duct cross-section, and obstructions within the ductwork create turbulence and increase noise.
* Grilles and Diffusers: Improperly selected or poorly installed supply and extract grilles can generate significant noise, especially if airflow is restricted.
* Breakout Noise: Sound generated inside the MVHR unit or ductwork that ‘breaks out’ through the casing or duct walls into the surrounding space. This is more likely with uninsulated or poorly insulated ducts.
* Vibration Transfer: Mechanical vibration from the MVHR unit or fans can transmit through the mounting structure (walls, floors) or directly through rigid duct connections, radiating noise into adjacent rooms.
7.2 Mitigation Strategies
Effective noise control requires a multi-faceted approach, integrated from the design phase through commissioning.
7.2.1 Unit Selection
- Low SFP Units: Prioritise MVHR units with very low Specific Fan Power (SFP) values. Lower SFP indicates more efficient fans that can achieve desired airflows at lower speeds, thereby reducing noise output.
- Acoustically Lined Casings: Many high-quality MVHR units incorporate internal acoustic insulation within their casings to absorb fan noise and prevent breakout noise.
- Certified Noise Data: Always request and compare manufacturers’ certified noise data (sound power levels at different fan speeds) during the selection process.
7.2.2 Placement and Mounting
- Strategic Location: Install the MVHR unit as far away as possible from noise-sensitive areas like bedrooms and living rooms. Ideal locations include utility rooms, plant rooms, garages, or dedicated, acoustically treated service voids.
- Anti-Vibration Mounts: Always mount the MVHR unit on purpose-designed anti-vibration pads or spring isolators. These prevent mechanical vibrations from the unit transmitting directly into the building structure.
- Flexible Duct Connections: Use short sections (e.g., 300-500mm) of flexible, acoustically lined ducting between the MVHR unit and the rigid ductwork. This isolates duct-borne vibration from the unit and prevents it from propagating through the ductwork.
7.2.3 Ductwork Design and Installation
- Generous Sizing: Design ductwork to ensure low air velocities. Larger duct diameters reduce air speed, resulting in less airflow noise and lower static pressure, which in turn allows fans to run at lower, quieter speeds.
- Minimise Bends and Obstructions: Use sweeping, large-radius bends instead of sharp 90-degree elbows. Avoid unnecessary changes in duct cross-section or restrictions that create turbulence.
- Internal Acoustic Lining: For particularly sensitive areas or long duct runs, ducts can be internally lined with acoustic insulation to absorb noise that travels through the ductwork. Alternatively, specify ducts with integral acoustic properties (e.g., certain semi-rigid systems).
- External Insulation: Proper external duct insulation (as discussed in Section 3.2.2) helps prevent noise from breaking out of the duct walls into adjacent spaces.
- Silencers/Attenuators: Install purpose-designed duct attenuators (silencers) immediately downstream of the MVHR unit on both supply and extract airflows, and optionally on individual branch lines leading to noise-sensitive rooms. These typically consist of acoustically lined baffles that absorb sound energy without significantly impeding airflow. Select attenuators sized for the specific duct diameter and required noise reduction.
- Airtightness: Ensure all duct connections are meticulously sealed. Air leaks can create whistling noises.
- Secure Support: Properly supporting ducts prevents rattling and vibration.
7.2.4 Terminal Devices (Grilles and Diffusers)
- Low-Noise Selection: Choose supply and extract grilles or diffusers that are designed for low noise operation at the calculated airflow rates. Manufacturers provide noise rating data for their terminal devices.
- Optimal Placement: Position grilles away from beds or seating areas where occupants spend long periods.
7.2.5 Commissioning and Maintenance
- Airflow Balancing: Proper commissioning and balancing of the airflow rates ensure that each terminal delivers the correct amount of air at the lowest possible fan speed and noise level. Over-ventilation or unbalanced flows can lead to noise.
- Regular Maintenance: Regular cleaning of filters prevents increased static pressure, which would force fans to work harder and noisier. Inspect fans for imbalance or debris, and lubricate bearings if required.
By implementing these comprehensive noise mitigation strategies, MVHR systems can deliver optimal indoor air quality and energy efficiency without compromising the acoustic comfort of the occupants.
Many thanks to our sponsor Focus 360 Energy who helped us prepare this research report.
8. Common Issues and Troubleshooting
While MVHR systems are robust and designed for continuous operation, like any mechanical system, they can encounter issues. Proactive identification and troubleshooting are essential to maintain performance and extend system lifespan.
8.1 Detailed Troubleshooting Steps
8.1.1 Inadequate Airflow
Symptoms: Reduced fresh air supply, stuffy indoor air, elevated CO2 levels, condensation on windows, persistent odours, fan running at unusually high speeds without achieving desired effect.
Possible Causes and Solutions:
* Clogged Filters: The most common cause. Solution: Inspect filters (supply and extract) monthly. Clean or replace them according to manufacturer recommendations (typically every 3-12 months, depending on filter type and air quality). A dirty filter light or alarm on the MVHR unit indicates this.
* Blocked Ducts: Can be caused by debris (e.g., construction dust, vermin nests if grilles are unprotected), kinks in flexible or semi-rigid ducting, or excessive dust build-up. Solution: Visually inspect accessible duct runs. For persistent issues, professional duct cleaning may be required. Ensure external grilles are clear of obstructions (leaves, snow, bird nests).
* Incorrect System Settings: Fan speeds may be set too low, or the system might be in a temporary ‘away’ mode. Solution: Check the MVHR unit’s control panel or associated app. Ensure fan speeds are set to ‘trickle’ for continuous ventilation and ‘boost’ is available when needed. Verify time schedules are correct.
* Duct Leaks: Air leaking from inadequately sealed ductwork reduces effective airflow at the terminals. Solution: Inspect all duct connections, particularly at joints, bends, and where ducts connect to the unit or grilles. Reseal with appropriate mastic or tape. A professional airtightness test of the ductwork can identify hidden leaks.
* Fan Motor Issues: A failing fan motor or capacitor can reduce fan speed. Solution: Listen for unusual sounds from the unit. If the fan seems to be struggling, a qualified technician should inspect and repair/replace the motor.
* Heat Exchanger Fouling: Over time, fine dust can build up on the heat exchanger plates or wheel, restricting airflow. Solution: Clean the heat exchanger periodically (usually annually or bi-annually during professional servicing) as per manufacturer instructions.
8.1.2 Unusual Noises
Symptoms: Whistling, rattling, humming, grinding, or excessive fan noise.
Possible Causes and Solutions:
* Loose Components: Panels, access doors, or internal components within the MVHR unit may vibrate. Solution: Secure all panels and check for loose parts. Ensure the unit is properly mounted on anti-vibration pads.
* Unbalanced Fans: Dirt build-up on fan blades or manufacturing defects can cause imbalance. Solution: Clean fan blades if accessible. If the noise persists, a technician may need to rebalance or replace the fan.
* Duct Vibration: Ducts not properly supported or touching building elements can transmit vibrations. Solution: Ensure ducts are securely supported at regular intervals and isolated from the building structure using suitable hangers and flexible connections. Check for obstructions within ducts.
* High Air Velocity at Grilles/Ducts: Often due to undersized ducts or excessive fan speed. Solution: Review duct design. Lower fan speed if possible. If terminal noise, consider replacing grilles with lower-noise models or adding duct attenuators.
* Motor Bearings: Worn motor bearings can produce a grinding or squealing noise. Solution: Requires professional repair or replacement of the motor.
* Air Leaks: Small gaps or holes in ductwork can create whistling sounds as air is forced through. Solution: Locate and seal leaks.
8.1.3 Energy Inefficiency
Symptoms: Higher than expected electricity bills, heating/cooling system running more frequently, poor heat recovery.
Possible Causes and Solutions:
* Dirty Filters: Increase fan energy consumption and reduce airflow. Solution: Regular filter replacement.
* Duct Leaks: Unconditioned air entering/exiting the system bypasses the heat exchanger. Solution: Identify and seal all duct leaks.
* Heat Exchanger Fouling: Reduces the efficiency of heat transfer. Solution: Periodic cleaning of the heat exchanger.
* Bypass Damper Stuck Open/Closed: If the summer bypass damper is stuck open in winter, heat recovery is circumvented. If stuck closed in summer, it prevents passive cooling. Solution: Inspect and lubricate the bypass damper mechanism. Check controls.
* Incorrect Temperature Setpoints: If an auxiliary heater is installed, its setpoint might be too high. Solution: Adjust setpoints on the control panel.
* Fan Motor Degradation: An aging or faulty fan motor may consume more power for the same output. Solution: Professional inspection and potential replacement.
* Improper Commissioning: System not balanced or optimised for design conditions. Solution: Re-commission the system by a qualified professional.
8.1.4 Condensation Issues
Symptoms: Water dripping from the MVHR unit or ducts, dampness around the unit.
Possible Causes and Solutions:
* Blocked Condensate Drain: The most common cause. Condensate from the heat exchanger cannot drain away. Solution: Regularly inspect and clean the condensate trap and drain line to prevent blockages from debris or biofilm. Ensure the trap is filled with water to prevent air ingress.
* Improperly Sloped Drain Line: The drain line must have a continuous downward slope to allow gravity drainage. Solution: Re-slope the drain line.
* Lack of Duct Insulation: Ducts running through cold spaces allow moist air inside to cool and condense. Solution: Ensure all unconditioned ductwork is thoroughly insulated with a continuous vapour barrier.
* Missing or Dry Condensate Trap: A dry trap can allow unconditioned air to enter, causing condensation or odours. Solution: Ensure the trap is filled with water. If it dries out frequently, investigate the cause (e.g., long periods of no operation, extreme dryness).
* Frost Protection Failure: In cold weather, if the frost protection system fails, the heat exchanger can freeze, potentially leading to ice build-up and water issues when it thaws. Solution: Check the unit’s frost protection settings and sensor functionality. Professional servicing required.
8.1.5 Odours
Symptoms: Musty, stale, or unpleasant odours from the supply or extract grilles.
Possible Causes and Solutions:
* Dirty Filters: Filters saturated with dust, mould spores, or pollutants can off-gas odours. Solution: Replace filters.
* Blocked Condensate Trap/Drain: Stagnant water in a blocked drain can become anaerobic and produce odours. Solution: Clean the condensate trap and drain line thoroughly.
* Mould Growth: In ducts or unit due to condensation or high humidity. Solution: Professional inspection and cleaning. Address root cause of moisture.
* External Air Contamination: Intake grille located too close to exhaust grille or other outdoor pollution sources (e.g., rubbish bins, flue vents). Solution: Relocate intake/exhaust grilles or extend ductwork to cleaner air zones.
* Internal Pollutant Source: Odour could be from an internal source not adequately being extracted. Solution: Identify and remove/mitigate internal pollutant source. Ensure extract points are in ‘wet’ or ‘dirty’ rooms.
8.2 Preventative Maintenance Schedule
Regular preventative maintenance is the most effective strategy to avoid issues, ensure optimal performance, and maximise the lifespan of an MVHR system.
- Monthly/Quarterly:
- User Check: Visually inspect external grilles for blockages (leaves, debris). Listen for unusual noises. Check control panel for warnings.
- Filter Inspection: For G3/G4 pre-filters, visually inspect and clean or replace as needed (often quarterly, more frequently in dusty environments).
- Bi-Annually:
- Filter Replacement: Replace F7/F9 fine filters (usually every 6-12 months, depending on air quality).
- Condensate Trap Check: Inspect and clean the condensate trap, ensure it’s filled with water and draining correctly.
- Annually:
- Professional Servicing Recommended: This should be carried out by a qualified MVHR technician.
- Heat Exchanger Cleaning: Clean the heat exchanger (plate or rotary wheel) as per manufacturer guidelines to maintain efficiency.
- Fan Inspection: Check fan blades for cleanliness and balance. Inspect bearings.
- Ductwork Visual Check: Inspect accessible duct runs for debris, kinks, or signs of leakage/condensation.
- Control System Check: Verify sensor calibration and control functions.
- Performance Verification: Basic airflow checks at terminals (can be done with simpler tools by homeowner).
- Every 3-5 Years (Professional):
- Deep Duct Cleaning: Depending on usage and internal air quality, professional internal duct cleaning may be recommended.
- Full System Audit: Comprehensive check of all components, electrical connections, and in-depth performance analysis.
By adhering to this maintenance schedule, building owners and facility managers can ensure their MVHR systems continue to deliver their intended benefits of superior indoor air quality and energy efficiency for many years.
Many thanks to our sponsor Focus 360 Energy who helped us prepare this research report.
9. Regulatory Compliance and Future Trends
MVHR systems are increasingly subject to stringent regulatory frameworks, reflecting their critical role in public health, energy efficiency, and environmental sustainability. Looking ahead, technological advancements and evolving societal priorities are shaping the next generation of ventilation solutions.
9.1 Detailed Regulatory Frameworks
The legislative landscape governing MVHR systems is multifaceted, encompassing various aspects of building performance.
9.1.1 Building Codes and Ventilation Standards
- Mandated Ventilation Rates: National and local building codes specify minimum ventilation rates required for different building types (residential, commercial, industrial) to ensure acceptable indoor air quality and occupant health. These are often expressed as air changes per hour (ACH), litres per second per person (L/s/person), or litres per second per square metre (L/s/m²). For example, in the UK, Approved Document F of the Building Regulations provides detailed guidance on ‘Means of Ventilation’, including continuous mechanical extract rates for wet rooms and whole-dwelling ventilation rates, with MVHR being a compliant solution for airtight dwellings. In the United States, ASHRAE Standard 62.1 (for non-residential buildings) and 62.2 (for residential buildings) are widely adopted benchmarks, setting performance-based criteria for ventilation design.
- Airtightness Requirements: Modern building codes increasingly mandate stringent airtightness targets (e.g., n50 value in Passive House, or air permeability rates in building regulations). MVHR systems are essential in these airtight envelopes, as natural infiltration is insufficient for proper ventilation.
- Specific Fan Power (SFP) Limits: To ensure energy efficiency, many regulations and voluntary standards (e.g., Passive House) set limits on the SFP of MVHR units, encouraging the use of highly efficient fans and low-resistance ductwork.
- Acoustic Requirements: Building codes may also include limits on internal noise levels from building services, which directly impacts MVHR unit selection and duct design.
9.1.2 Energy Performance Directives
- Nearly Zero-Energy Buildings (NZEB) / Net Zero Energy: European Union directives (e.g., EPBD – Energy Performance of Buildings Directive) have driven the transition towards NZEB, where buildings consume very little energy, largely covered by renewable sources. MVHR systems are fundamental to achieving these targets by drastically reducing ventilation heat losses.
- Energy Performance Certificates (EPCs): MVHR systems significantly improve a building’s energy rating on EPCs, reflecting lower energy consumption for heating and cooling. This can enhance property value and marketability.
- Certification Schemes: Green building certification schemes like LEED, BREEAM, and Passive House place a strong emphasis on energy recovery ventilation as a pathway to higher performance ratings. Compliance often requires documentation of MVHR performance data.
9.1.3 Environmental Regulations
- Refrigerant Management (F-Gas Regulation): While most MVHR units are refrigerant-free, some advanced units or those with integrated heat pumps may contain refrigerants. Regulations like the EU’s F-Gas Regulation control the use and emissions of fluorinated greenhouse gases, requiring proper handling, maintenance, and end-of-life disposal.
- Waste Electrical and Electronic Equipment (WEEE) Directive: This directive in the EU mandates the responsible collection, recycling, and recovery of electronic waste, including MVHR units, at the end of their lifespan.
- Embodied Carbon: There is a growing focus on the embodied carbon (carbon emissions associated with manufacturing, transport, and construction) of building materials and components, including MVHR units and ductwork. Future regulations or certifications may start to consider this aspect.
9.2 Evolving Standards and Technologies
The MVHR landscape is dynamic, with continuous innovation driven by demand for healthier, more efficient, and smarter buildings.
9.2.1 Smart Home and Building Management System (BMS) Integration
- Centralised Control: MVHR systems are increasingly integrated into comprehensive smart home ecosystems and commercial BMS platforms. This allows for centralised control, scheduling, remote monitoring via mobile apps, and interoperability with other building services like heating, cooling, and lighting.
- User Interfaces: Intuitive user interfaces with real-time IAQ data (CO2, humidity, PM2.5 levels) empower occupants to understand and control their environment more effectively.
9.2.2 Advanced Sensors and Demand-Controlled Ventilation (DCV)
- Multi-Sensor Integration: Beyond basic CO2 and humidity sensors, new MVHR systems are incorporating a wider array of IAQ sensors, including volatile organic compound (VOC) sensors, particulate matter (PM2.5) sensors, and even ozone or nitrogen dioxide sensors.
- Highly Responsive Systems: This allows for highly granular and responsive demand-controlled ventilation, where fan speeds are precisely adjusted in real-time based on actual indoor air quality needs, rather than fixed schedules. This maximises energy efficiency by preventing over-ventilation and enhances occupant comfort and health.
9.2.3 Artificial Intelligence (AI) and Machine Learning (ML)
- Predictive Control: AI and ML algorithms are being developed to analyse historical IAQ data, occupancy patterns, external weather forecasts, and energy prices to proactively optimise MVHR operation. This can include anticipating peak ventilation needs or optimising for off-peak electricity consumption.
- Fault Detection and Diagnostics: AI can identify subtle deviations from normal operation, flagging potential faults (e.g., clogged filters, fan issues) before they become significant problems, enabling predictive maintenance.
9.2.4 Decentralized MVHR Units
- Room-by-Room Solutions: While central MVHR systems remain dominant, decentralised, single-room MVHR units are gaining traction, particularly for retrofits or extensions where extensive ductwork installation is impractical. These units typically serve one room and often incorporate ceramic heat exchangers that alternate airflow direction.
- Pros: Easier and cheaper to install in existing buildings, no ductwork required, individual room control.
- Cons: Often lower heat recovery efficiency than central units, potential for multiple small units to generate more cumulative noise, less sophisticated filtration, and potential for unbalancing building pressure if not carefully designed.
9.2.5 Renewable Energy Integration
- PV Self-Consumption: MVHR units, with their continuous low power draw, are ideal loads for integration with rooftop photovoltaic (PV) systems, increasing the self-consumption of locally generated renewable electricity and reducing reliance on grid power.
- Heat Pump Integration: Some advanced MVHR units now incorporate small air-to-air heat pumps to provide supplementary heating or cooling, further enhancing their energy-saving capabilities.
9.2.6 Hybrid Ventilation Strategies
- Integrated Natural and Mechanical: Future designs may increasingly integrate MVHR with intelligent natural ventilation strategies. For instance, the MVHR might provide base ventilation, with automated windows or vents opening when external conditions are favourable (e.g., cool night air, low pollution) to augment ventilation or provide passive cooling.
9.2.7 Focus on Health and Well-being
- Beyond Energy: The industry is increasingly shifting its focus from solely energy efficiency to the holistic health and well-being of building occupants. MVHR systems, by providing continuous fresh, filtered air, are at the forefront of this movement, helping to create ‘health-positive’ buildings that actively contribute to occupant health and productivity.
Many thanks to our sponsor Focus 360 Energy who helped us prepare this research report.
10. Conclusion
Mechanical Ventilation with Heat Recovery (MVHR) systems represent a fundamental shift in how modern buildings manage indoor environments, moving beyond rudimentary air exchange to sophisticated control over air quality and energy consumption. As this report has thoroughly demonstrated, MVHR systems are indispensable tools in achieving contemporary building performance targets, particularly in the context of highly insulated and airtight construction.
A comprehensive understanding of the diverse types and configurations of MVHR units, from their intricate heat exchange mechanisms to their airflow balance strategies, is critical for informed selection. Moreover, meticulous adherence to robust design principles, encompassing precise system sizing, intelligent ductwork layout, advanced filtration, and strategic humidity control, directly translates into optimal performance and efficiency. The success of an MVHR system, however, is equally contingent upon rigorous installation best practices, including unwavering regulatory compliance, meticulous ductwork sealing, strategic unit placement, and, crucially, comprehensive commissioning. Neglecting any of these stages can significantly undermine a system’s efficacy, leading to compromised indoor air quality, excessive energy consumption, and unwanted noise.
The health benefits conferred by MVHR systems are profound, extending from the active removal of particulate matter, allergens, and gaseous pollutants to the maintenance of optimal indoor humidity, all contributing to superior indoor air quality and occupant well-being. Economically, while initial investment may be higher, the long-term energy savings, driven by highly efficient heat recovery and intelligent controls, deliver a compelling lifecycle cost proposition. Furthermore, proactive noise mitigation strategies, from unit selection to duct design, are essential to ensure that the enhanced indoor environment is also acoustically comfortable. Finally, a robust understanding of common issues and systematic troubleshooting, coupled with adherence to a consistent preventative maintenance schedule, guarantees system longevity and sustained high performance.
As regulatory frameworks continue to evolve towards more stringent energy and IAQ standards, and as technological advancements, including AI-driven controls, advanced sensing, and seamless smart home integration, reshape the built environment, MVHR systems will remain at the vanguard. They are not merely components of a building’s mechanical services; they are foundational elements of healthy, sustainable, and high-performance buildings, playing a pivotal role in shaping the future of indoor living and working environments. By embracing a holistic approach to their design, installation, operation, and ongoing maintenance, professionals can unlock the full potential of MVHR systems, ensuring they continue to enhance both the planet’s health and the well-being of its inhabitants.
Many thanks to our sponsor Focus 360 Energy who helped us prepare this research report.
References
- ASHRAE Standard 62.1-2019. (2019). ‘Ventilation for Acceptable Indoor Air Quality’. American Society of Heating, Refrigerating and Air-Conditioning Engineers.
- ASHRAE Standard 62.2-2019. (2019). ‘Ventilation and Acceptable Indoor Air Quality in Residential Buildings’. American Society of Heating, Refrigerating and Air-Conditioning Engineers.
- CIBSE Guide B: Ventilation and Air Conditioning. (2016). Chartered Institution of Building Services Engineers.
- EN 13779. (2007). ‘Ventilation for non-residential buildings – Performance requirements for ventilation and room-conditioning systems’. European Committee for Standardization.
- EN ISO 16890. (2016). ‘Air filters for general ventilation – Part 1: Technical specifications, requirements, and classification system based on particulate matter efficiency (ePM)’. International Organization for Standardization.
- Evolution Mechanics. (n.d.). ‘Ventilation System Design: Guide for Efficiency’. Retrieved from https://evolutionmechanical.net/blog/ventilation-system-design/ (Accessed October 26, 2023).
- Heat Recovery Ventilation Association (HRVA). (n.d.). ‘HRVA Good Practice Guide for the Installation of Residential Mechanical Ventilation with Heat Recovery Systems’.
- Loughborough Air Conditioning Ltd. (n.d.). ‘7 Considerations for MVHR Installation’. Retrieved from https://lacltd.uk.com/7-considerations-for-mvhr-installation (Accessed October 26, 2023).
- Passive House Adelaide. (n.d.). ‘Maintenance and Operation of MVHR Systems in Passive Houses’. Retrieved from https://passivehouseadelaide.com/maintenance-and-operation-of-mvhr-systems-in-passive-houses (Accessed October 26, 2023).
- Passive House Institute. (n.d.). ‘Component Certification: Heat Recovery Ventilation Units’. Retrieved from https://passiv.de/en/04_phpp/05_phpp_software_download/phpp_software_download.htm (Accessed October 26, 2023).
- The Building Regulations 2010. Approved Document F: ‘Ventilation’ (2021 edition incorporating amendments). HM Government, UK.
- Titon. (n.d.). ‘Maximising Air Quality and Efficiency: Advantages of Mechanical Ventilation Systems’. Retrieved from https://www.titon.com/blog-ventilation/mechanical-ventilation-system (Accessed October 26, 2023).
- Venti Group Ltd. (n.d.). ‘Ultimate Guide to Mechanical Ventilation with Heat Recovery Systems to Meet Approved Document F’. Retrieved from https://www.venti-group.com/ultimate-guide-to-mechanical-ventilation-with-heat-recovery-systems-to-meet-approved-document-f/ (Accessed October 26, 2023).
- Wikipedia. (n.d.). ‘Heat Recovery Ventilation’. Retrieved from https://en.wikipedia.org/wiki/Heat_recovery_ventilation (Accessed October 26, 2023).
Given that preventative maintenance is key, what strategies do you recommend for ensuring consistent adherence to maintenance schedules, especially in residential settings where the responsibility often falls to individual homeowners?