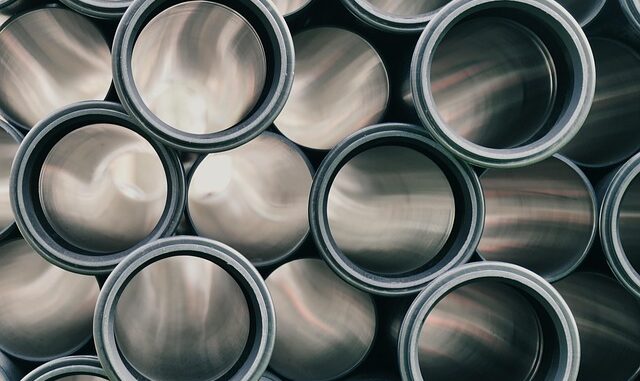
Quality Control in Complex Systems: From Construction to Bioengineering and Beyond
Many thanks to our sponsor Focus 360 Energy who helped us prepare this research report.
Abstract
Quality control (QC) is a cornerstone of success in any complex system, spanning domains as diverse as construction, manufacturing, and bioengineering. This research report provides a comprehensive overview of QC principles and methodologies, extending beyond the typical focus on construction to encompass a broader perspective of complex engineered systems. We examine traditional QC tools and techniques alongside more advanced methodologies such as Six Sigma, Lean principles, and statistical process control (SPC). The report explores the adaptation and implementation challenges of QC in dynamic environments and highlights the importance of risk-based approaches for effective QC implementation. Furthermore, we critically evaluate the role of emerging technologies like artificial intelligence (AI) and the Internet of Things (IoT) in revolutionizing QC processes, enabling real-time monitoring, predictive maintenance, and automated defect detection. The report argues that while domain-specific QC techniques are essential, a holistic, system-level understanding of QC principles is critical for achieving robust, reliable, and cost-effective performance in complex systems.
Many thanks to our sponsor Focus 360 Energy who helped us prepare this research report.
1. Introduction
Quality control (QC) is a systematic process designed to ensure that products or services meet specified quality standards and requirements. While the specific methods and tools used for QC vary significantly depending on the industry and application, the underlying principles remain constant: to prevent defects, reduce variability, and improve overall product or service quality. Historically, QC has been viewed as a reactive process, primarily focused on inspecting finished goods and identifying defects after production. However, modern QC practices emphasize a proactive approach, aiming to identify and address potential issues early in the design and production process to minimize the risk of defects.
This research report aims to provide a comprehensive overview of QC in complex systems, extending beyond the typical focus on construction. Complex systems are characterized by a high degree of interconnectedness, nonlinearity, and emergent behavior, making QC particularly challenging. These systems often involve multiple stakeholders, intricate supply chains, and complex interactions between various components and subsystems. Examples of complex systems include large-scale construction projects, manufacturing facilities, bioengineering processes, and software development projects. The effectiveness of QC in these systems depends not only on the application of appropriate tools and techniques but also on a deep understanding of the system’s dynamics and potential failure modes.
Many thanks to our sponsor Focus 360 Energy who helped us prepare this research report.
2. Core Principles of Quality Control
Several core principles underpin effective QC practices across different domains:
- Customer Focus: QC should be driven by the needs and expectations of the customer. Understanding customer requirements and translating them into measurable quality metrics is essential for ensuring customer satisfaction.
- Prevention over Detection: A proactive approach to QC is more effective and cost-efficient than relying solely on defect detection after production. By identifying and addressing potential issues early in the process, organizations can prevent defects from occurring in the first place.
- Continuous Improvement: QC is not a one-time effort but an ongoing process of continuous improvement. Organizations should regularly review their QC processes, identify areas for improvement, and implement changes to enhance quality and efficiency. This is often achieved through methodologies like Plan-Do-Check-Act (PDCA) cycle and Kaizen.
- Data-Driven Decision Making: QC decisions should be based on data and evidence rather than intuition or guesswork. Collecting and analyzing data on process performance, defect rates, and customer feedback is essential for identifying trends, understanding root causes, and making informed decisions.
- Employee Empowerment: Employees play a crucial role in QC. Empowering employees to identify and report potential quality issues, participate in problem-solving, and contribute to improvement efforts can significantly enhance QC effectiveness. In practice this looks like clear roles and responsibilities that are communicated effectively to the team.
- Systematic Approach: QC should be integrated into all aspects of the organization, from design and planning to production and delivery. A systematic approach ensures that quality is considered at every stage of the process.
Many thanks to our sponsor Focus 360 Energy who helped us prepare this research report.
3. Quality Control Methodologies
Numerous QC methodologies have been developed and implemented across different industries. Some of the most widely used methodologies include:
3.1. Statistical Process Control (SPC)
SPC is a powerful set of statistical techniques used to monitor and control processes. SPC involves collecting data on process variables, plotting the data on control charts, and analyzing the charts to identify trends, patterns, and deviations from expected behavior. Control charts help organizations distinguish between common cause variation (random variation inherent in the process) and special cause variation (variation caused by specific events or factors). By identifying and addressing special cause variation, organizations can improve process stability and reduce variability.
For example, in concrete pouring, SPC can be used to monitor the slump of the concrete mix, the ambient temperature, and the curing time. By tracking these variables on control charts, engineers can identify potential problems early on and take corrective action before the concrete sets.
3.2. Six Sigma
Six Sigma is a data-driven methodology focused on reducing defects and improving process performance. The core of Six Sigma is the DMAIC (Define, Measure, Analyze, Improve, Control) cycle, a structured approach to problem-solving and process improvement. Six Sigma projects typically involve cross-functional teams, rigorous data analysis, and the use of statistical tools to identify and eliminate the root causes of defects.
One critical aspect of Six Sigma that makes it a valuable QC methodology is its emphasis on minimizing variation in the processes. Lower variation leads to a more predictable and stable output, reducing the likelihood of defects and increasing the overall consistency of the final product or service.
3.3. Lean Construction
Lean construction is a production management approach that aims to minimize waste and maximize value in construction projects. Lean principles, such as just-in-time (JIT) delivery, pull scheduling, and continuous improvement, are applied to streamline construction processes, reduce inventory, and eliminate unnecessary delays. Lean construction emphasizes collaboration, communication, and teamwork among all project stakeholders.
In the context of QC, Lean Construction principles can significantly reduce the likelihood of defects by ensuring that materials and resources are available when and where they are needed, minimizing the risk of damage or spoilage. For instance, efficient inventory management and just-in-time delivery can prevent the storage of materials in suboptimal conditions, which can lead to material degradation and subsequent construction defects.
3.4. ISO 9000 Standards
ISO 9000 is a set of international standards for quality management systems (QMS). These standards provide a framework for organizations to establish and maintain a QMS that meets customer and regulatory requirements. ISO 9000 certification demonstrates an organization’s commitment to quality and provides a competitive advantage in the marketplace.
The ISO 9000 standards focus on several key elements, including customer focus, leadership, engagement of people, process approach, improvement, evidence-based decision-making, and relationship management. By adhering to these principles, organizations can build a robust QMS that supports consistent quality and continuous improvement.
Many thanks to our sponsor Focus 360 Energy who helped us prepare this research report.
4. Quality Control Techniques for Specific Processes
In addition to general QC methodologies, specific techniques are used for various construction processes. Examples include:
4.1. Concrete Pouring
QC techniques for concrete pouring include pre-pour inspections to ensure proper formwork and reinforcement placement, slump tests to verify concrete consistency, air content tests to measure air entrainment, and compression tests to assess concrete strength. Regular monitoring of temperature and humidity is also crucial to ensure proper curing.
4.2. Welding
Welding QC techniques include visual inspections to identify surface defects, non-destructive testing (NDT) methods such as ultrasonic testing and radiography to detect subsurface defects, and destructive testing methods such as tensile tests and bend tests to assess weld strength and ductility. Properly trained and certified welders are essential for ensuring weld quality.
4.3. Electrical Installations
QC techniques for electrical installations include visual inspections to verify proper wiring and component installation, continuity tests to check for open circuits, insulation resistance tests to ensure proper insulation, and ground resistance tests to verify grounding effectiveness. Compliance with electrical codes and standards is paramount.
4.4. Software Development
Software QC techniques encompass a broad range of methods, including code reviews to identify potential bugs and vulnerabilities, unit testing to verify individual components, integration testing to ensure seamless interaction between modules, and system testing to evaluate the entire software system. Performance testing and security testing are also critical for ensuring software reliability and security.
Many thanks to our sponsor Focus 360 Energy who helped us prepare this research report.
5. The Role of Technology in Quality Control
Emerging technologies are transforming QC processes across various industries. Artificial intelligence (AI) and machine learning (ML) are being used to automate defect detection, predict equipment failures, and optimize process parameters. The Internet of Things (IoT) enables real-time monitoring of process variables and equipment performance, providing valuable data for QC analysis.
5.1. AI-Powered Defect Detection
AI-powered defect detection systems use computer vision and machine learning algorithms to automatically identify defects in products or processes. These systems can be trained to recognize a wide range of defects, from surface scratches and cracks to internal anomalies. AI-powered defect detection can significantly improve the speed and accuracy of inspections, reducing the need for manual labor and improving overall QC efficiency. Deep learning models such as Convolutional Neural Networks (CNNs) are often employed for image-based defect detection due to their ability to learn complex patterns from visual data.
5.2. Predictive Maintenance
Predictive maintenance uses sensor data and machine learning algorithms to predict equipment failures before they occur. By analyzing data on vibration, temperature, pressure, and other parameters, predictive maintenance systems can identify early warning signs of potential failures and trigger maintenance interventions before breakdowns occur. Predictive maintenance can significantly reduce downtime, maintenance costs, and the risk of catastrophic failures.
5.3. Real-Time Monitoring with IoT
IoT sensors can be deployed to monitor process variables in real-time, providing valuable data for QC analysis. For example, in concrete production, IoT sensors can monitor the temperature, humidity, and moisture content of the concrete mix, providing real-time feedback to ensure that the concrete meets specified quality requirements. IoT data can also be integrated with other systems, such as building information modeling (BIM), to provide a comprehensive view of project status and quality.
5.4. Digital Twins for Quality Simulation and Prediction
Digital twins, virtual representations of physical assets or systems, can be used to simulate QC processes and predict potential defects. By creating a digital twin of a manufacturing process, engineers can experiment with different process parameters and identify optimal settings to minimize defects. Digital twins can also be used to simulate the impact of environmental factors, such as temperature and humidity, on product quality. This predictive capability allows for proactive adjustments, reducing the risk of non-conformance.
Many thanks to our sponsor Focus 360 Energy who helped us prepare this research report.
6. Risk-Based Quality Control
In complex systems, not all components or processes are equally critical to overall system performance. A risk-based approach to QC involves identifying and prioritizing potential risks based on their likelihood and impact. Resources are then allocated to QC activities based on the severity of the identified risks. This approach ensures that the most critical components and processes receive the most attention, maximizing the effectiveness of QC efforts.
6.1. Failure Mode and Effects Analysis (FMEA)
FMEA is a systematic technique used to identify potential failure modes in a system, assess the severity and probability of each failure mode, and identify appropriate mitigation measures. FMEA can be used to identify critical components and processes that require enhanced QC measures. The FMEA process involves assigning a Risk Priority Number (RPN) to each potential failure mode based on the severity, occurrence, and detection ratings. The RPN is then used to prioritize mitigation efforts.
6.2. Hazard Analysis and Critical Control Points (HACCP)
HACCP is a systematic preventive approach to food safety, but its principles can be applied to other industries as well. HACCP involves identifying critical control points (CCPs) in a process, establishing critical limits for each CCP, monitoring the CCPs to ensure that they are within critical limits, and taking corrective action when deviations occur. HACCP can be used to ensure that critical quality parameters are maintained throughout the production process.
Many thanks to our sponsor Focus 360 Energy who helped us prepare this research report.
7. Challenges and Future Directions
Implementing effective QC in complex systems presents several challenges. One major challenge is the increasing complexity of products and processes, which makes it more difficult to identify potential failure modes and develop effective QC measures. Another challenge is the need for collaboration and communication among multiple stakeholders, including designers, manufacturers, suppliers, and customers.
To overcome these challenges, organizations need to adopt a holistic, system-level approach to QC. This involves integrating QC into all aspects of the organization, from design and planning to production and delivery. Organizations also need to invest in training and development to ensure that employees have the skills and knowledge needed to implement effective QC practices. Furthermore, fostering a culture of quality, where all employees are committed to excellence and continuous improvement, is essential for long-term success.
Future directions in QC include the development of more advanced AI-powered defect detection systems, the integration of IoT data with machine learning algorithms to enable predictive maintenance, and the use of digital twins to simulate and optimize QC processes. As technologies continue to evolve, QC will become increasingly automated, data-driven, and predictive.
Another important trend is the increasing focus on sustainability and environmental responsibility. QC practices will need to incorporate environmental considerations, such as reducing waste, minimizing energy consumption, and using sustainable materials. This requires a shift towards a more circular economy, where products are designed for durability, reuse, and recyclability.
Finally, the globalization of supply chains poses new challenges for QC. Organizations need to ensure that their suppliers meet the same quality standards as their own operations. This requires robust supplier quality management programs, including supplier audits, inspections, and training. Technology can play a crucial role in enabling supply chain visibility and ensuring that quality standards are consistently maintained across geographically dispersed locations.
Many thanks to our sponsor Focus 360 Energy who helped us prepare this research report.
8. Conclusion
Quality control is a critical enabler of success in complex systems, extending far beyond traditional construction applications to encompass diverse fields like bioengineering, manufacturing, and software development. Effective QC requires a holistic, system-level approach that integrates core principles such as customer focus, prevention over detection, continuous improvement, data-driven decision-making, employee empowerment, and a systematic methodology. While established methodologies like SPC, Six Sigma, Lean Construction, and ISO 9000 remain essential, the adoption of emerging technologies like AI, IoT, and digital twins is revolutionizing QC processes, enabling real-time monitoring, predictive maintenance, and automated defect detection. Furthermore, the implementation of risk-based QC methodologies allows organizations to prioritize critical components and processes based on their likelihood and impact. By embracing these advancements and challenges, organizations can achieve robust, reliable, and cost-effective performance, ensuring consistent quality and customer satisfaction in an increasingly complex world.
Many thanks to our sponsor Focus 360 Energy who helped us prepare this research report.
References
- Montgomery, D. C. (2019). Statistical quality control: A modern approach. John Wiley & Sons.
- Pyzdek, T., & Keller, P. A. (2018). The Six Sigma Handbook. McGraw-Hill Education.
- Koskela, L. (2000). An Exploration Towards a Production Theory and its Application to Construction. VTT Publications.
- International Organization for Standardization. (2015). ISO 9000:2015 – Quality management systems — Fundamentals and vocabulary.
- Holzinger, A., Voraberger, A., & Mayer, C. (2020). Machine learning and knowledge extraction with complex data. Springer.
- Lee, J., Bagheri, B., & Kao, H. A. (2015). A cyber-physical systems architecture for industry 4.0-based manufacturing systems. Manufacturing Letters, 3(1), 15-23.
- Glaessgen, E. H., & Stargel, D. S. (2012). The digital twin paradigm for future NASA and US Air Force vehicles. 53rd AIAA/ASME/ASCE/AHS/ASC Structures, Structural Dynamics and Materials Conference 20th AIAA/ASME/AHS Adaptive Structures Conference 14th AIAA, 1818.
- Stamatis, D. H. (2003). Failure Mode and Effect Analysis: FMEA from Theory to Execution. ASQ Quality Press.
- FAO/WHO Codex Alimentarius Commission. (2020). Hazard Analysis and Critical Control Point (HACCP) System and Guidelines for its Application. CAC/RCP 1-1969, Rev. 5.
- Elkington, J. (2020). Green Swan: The Coming Boom in Regenerative Capitalism. Fast Company Press.
- Zsidisin, G. A., & Ritchie, B. (2009). Supply chain risk: A review and typology of supply chain risk studies. International Journal of Production Research, 47(20), 6275-6308.
Given the increasing focus on sustainability, how might QC methodologies adapt to better incorporate life cycle assessments and circular economy principles, particularly regarding material selection and waste reduction in complex systems?
That’s a fantastic point! Integrating life cycle assessments into QC is definitely the next frontier. Imagine using AI to predict the environmental impact of material choices *before* construction begins. This proactive approach could drive significant waste reduction and promote circularity in complex systems. What specific metrics would you prioritize in a life cycle assessment for QC?
Editor: FocusNews.Uk
Thank you to our Sponsor Focus 360 Energy
The emphasis on a systematic approach to QC is vital. How can organizations best foster cross-departmental collaboration to ensure quality considerations are embedded from the initial design phases through to final delivery, particularly in complex system development?