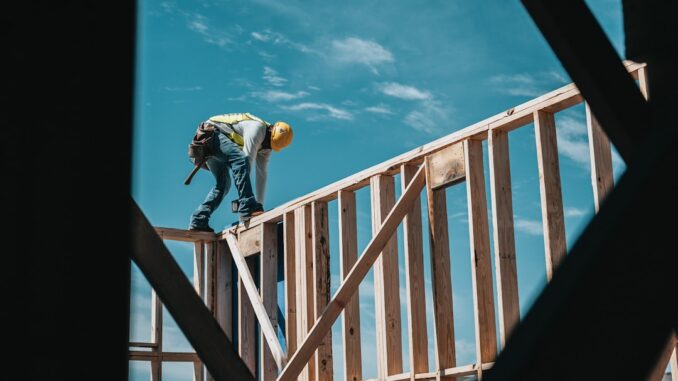
The Imperative of Sustainable Construction: Navigating Towards a Decarbonised Built Environment
Many thanks to our sponsor Focus 360 Energy who helped us prepare this research report.
Abstract
The global construction industry stands at a profound inflection point, confronted by an escalating imperative to integrate genuinely sustainable practices that not only mitigate its substantial environmental impact but also decisively align with ambitious global climate objectives. This comprehensive report meticulously examines the multifaceted dimensions underpinning sustainability within the contemporary construction sector. Its core focus encompasses the strategic integration of advanced low-carbon technologies, the rigorous adoption of pioneering building standards – exemplified by the United Kingdom’s transformative Future Homes Standard – and the industry’s proactive, collaborative measures aimed at significantly enhancing energy efficiency and drastically reducing lifecycle carbon emissions. Through an exhaustive and interdisciplinary analysis, this report illuminates the indispensable and interconnected roles of robust policy frameworks, relentless technological innovation, strategic financial instruments, and unwavering industry commitment in steering the construction sector towards an ecologically sound, economically viable, and socially responsible sustainable future. It delves into the granular details of regulatory evolution, material science advancements, and the critical socio-economic implications, including the pervasive skills gap, that define this ongoing paradigm shift.
Many thanks to our sponsor Focus 360 Energy who helped us prepare this research report.
1. Introduction: The Construction Industry’s Environmental Footprint and the Global Imperative for Change
The construction sector, a colossal engine of global economic activity and societal development, paradoxically bears an exceptionally heavy environmental burden. It is widely acknowledged as one of the largest contributors to global resource depletion, waste generation, and greenhouse gas emissions. Current estimates indicate that the built environment, encompassing both the construction and operational phases of buildings, is responsible for approximately 36% of global final energy use and a staggering 39% of energy-related carbon dioxide (CO2) emissions annually. This includes emissions from the manufacturing of building materials and products (often referred to as embodied carbon), as well as the energy consumed during a building’s operational lifetime (operational carbon) (en.wikipedia.org). Beyond carbon, the industry consumes vast quantities of virgin raw materials, accounts for a significant portion of potable water usage, and generates an immense volume of construction and demolition waste that often ends up in landfills, exacerbating land degradation and pollution issues.
This substantial ecological footprint has not only catalysed but intensified a global movement towards comprehensively sustainable construction practices. The core objectives of this movement are multi-dimensional: to drastically reduce energy consumption throughout a building’s lifecycle, to minimise the generation of waste through circular economy principles, to promote the widespread use of renewable resources and recycled content, and to foster healthier, more resilient indoor and outdoor environments. This paradigm shift is not merely an ethical imperative but a strategic necessity, driven by international agreements such as the Paris Agreement, which mandates signatories to pursue efforts to limit global temperature rise to 1.5 degrees Celsius above pre-industrial levels, and the United Nations Sustainable Development Goals (SDGs), particularly SDG 7 (Affordable and Clean Energy), SDG 9 (Industry, Innovation, and Infrastructure), SDG 11 (Sustainable Cities and Communities), and SDG 12 (Responsible Consumption and Production).
In response to these global pressures and national commitments, governments worldwide are enacting increasingly stringent building regulations and introducing proactive policies to accelerate the transition. The United Kingdom’s Future Homes Standard (FHS), slated for full implementation in 2025, stands as a prominent example of such a forward-looking initiative. Its ambitious mandate for low-carbon heating technologies and significantly enhanced fabric standards for new homes underscores a profound commitment to radically improve energy efficiency and reduce carbon emissions, setting a benchmark for future regulatory frameworks globally (at-eco.co.uk). This report will explore the intricacies of the FHS, the technological innovations it necessitates, the broader ecosystem of green building certifications, and the inherent challenges and opportunities that define the path towards a truly sustainable built environment.
Many thanks to our sponsor Focus 360 Energy who helped us prepare this research report.
2. The Future Homes Standard: A Paradigm Shift in UK Building Regulations
2.1 Overview and Evolution of the Future Homes Standard
The Future Homes Standard represents a monumental evolution in UK building regulations, designed to propel the nation towards its legally binding net-zero emissions target by 2050. The standard’s overarching aim is to ensure that new homes built from 2025 will produce 75-80% less carbon emissions compared to homes built under current (2013) standards. This significant reduction is to be achieved primarily through a ‘fabric first’ approach, drastically improving the energy efficiency of the building envelope, combined with a wholesale shift away from fossil fuel heating systems towards highly efficient low-carbon alternatives.
The journey towards the FHS began with the ‘uplift’ to Part L (Conservation of Fuel and Power) of the Building Regulations in June 2022. This interim step saw a 31% reduction in carbon emissions for new homes compared to previous standards, introducing higher fabric efficiency requirements and mandating the installation of low-carbon heating where feasible. This served as a crucial stepping stone, allowing the industry to adapt and prepare for the more radical changes of the FHS in 2025.
Key provisions of the Future Homes Standard include:
-
Enhanced Fabric Energy Efficiency: The FHS mandates significantly improved thermal performance of the building envelope. This means more rigorous U-value targets for walls (e.g., as low as 0.18 W/m²K), roofs (0.11 W/m²K), and floors (0.13 W/m²K), substantially exceeding current requirements. High-performance windows and doors with lower U-values (e.g., 1.2 W/m²K for double glazing, even lower for triple glazing) are essential. Crucially, the standard emphasizes exceptional airtightness, targeting air permeability rates as low as 3.0 m³/(h.m²) at 50 Pa, requiring meticulous construction detailing and robust quality control. The ‘fabric first’ principle dictates that reducing heat loss through the building envelope is the most cost-effective and enduring way to achieve energy efficiency, minimizing the reliance on heating systems (at-eco.co.uk).
-
Prohibition of Fossil Fuel Heating Systems: Perhaps the most transformative aspect of the FHS is the effective ban on the installation of natural gas boilers and other fossil fuel heating systems in new homes from 2025. This decisive move aims to decarbonise domestic heat by shifting entirely towards low-carbon heating solutions. The primary beneficiaries of this mandate are highly efficient heat pumps, including air-source heat pumps (ASHP) and ground-source heat pumps (GSHP), which extract latent heat from the ambient air or ground, respectively, and transfer it into the building for heating and hot water production. While wood-burning stoves have been granted a controversial allowance under specific conditions, the overarching policy direction is clear: an electrified, low-carbon heating future (at-eco.co.uk, homebuilding.co.uk).
-
Mandatory Integration of Renewable Energy: While not a primary focus for meeting compliance targets due to the emphasis on fabric and heat pumps, the FHS strongly encourages and, in many cases, makes mandatory the integration of on-site renewable energy sources. Solar photovoltaic (PV) systems, which convert sunlight directly into electricity, are becoming standard features on new residential developments, reducing reliance on grid electricity and lowering operational carbon emissions. Furthermore, the standard promotes battery storage solutions, enabling homeowners to store surplus renewable energy generated on-site for use during periods of high demand or low generation, thereby enhancing energy resilience and grid independence (at-eco.co.uk). The standard also accounts for Electric Vehicle (EV) charging infrastructure, aligning with broader decarbonisation efforts.
-
Improved Ventilation and Indoor Air Quality (IAQ): With significantly enhanced airtightness, traditional natural ventilation methods become insufficient and potentially problematic. The FHS therefore mandates the adoption of advanced mechanical ventilation systems to ensure optimal indoor air quality and prevent issues such as condensation and mould growth. Mechanical Ventilation with Heat Recovery (MVHR) systems are the preferred solution. MVHR units continuously extract stale, moist air from wet rooms (kitchens, bathrooms) and supply fresh, filtered air to habitable rooms, recovering up to 90% of the heat from the extracted air before it is expelled. This not only maintains excellent IAQ by removing pollutants and allergens but also prevents heat loss, directly contributing to the home’s energy efficiency. Other controlled mechanical ventilation systems may also be used, depending on specific building characteristics.
2.2 Implications for the Construction Industry
The implementation of the Future Homes Standard necessitates a comprehensive and profound paradigm shift across the entire construction value chain. Builders, developers, designers, and material suppliers must fundamentally re-evaluate and adapt their existing practices, processes, and business models to comply with the new requirements. This transition presents both significant challenges and unparalleled opportunities.
-
Increased Demand for Skilled Labor and Addressing the Skills Gap: The shift towards low-carbon construction technologies and high-performance building envelopes creates an urgent and substantial demand for new skills and expertise. The UK construction industry already faces a persistent skills gap, and the FHS will exacerbate this. There is a critical need for a greater number of professionals proficient in the design, installation, and maintenance of heat pumps, MVHR systems, and solar PV. Furthermore, meticulous attention to detail in thermal bridge reduction, airtightness, and advanced insulation techniques requires a highly skilled on-site workforce. Training and reskilling initiatives are paramount to equip existing workers and attract new talent into specialised roles. Without adequate investment in education and training, this skills deficit could severely impede the industry’s ability to meet the FHS deadlines and broader decarbonisation targets (reuters.com). Government-backed schemes, industry-led apprenticeships, and vocational training programs are crucial to bridge this gap.
-
Extensive Supply Chain Adjustments: The transition away from conventional materials and technologies to sustainable alternatives necessitates profound modifications across the entire supply chain. This involves identifying and establishing reliable sources for high-performance insulation, low-U-value windows, advanced heat pump systems, and MVHR units. Manufacturers must scale up production of these components, and distribution networks need to be optimized to ensure timely and cost-effective delivery. Furthermore, the emphasis on embodied carbon will drive demand for materials with lower lifecycle impacts, such as timber products, recycled content, and low-carbon concretes. This requires collaboration between designers, contractors, and material producers to foster innovation and develop new products. Challenges include potential cost volatility for new materials, increased lead times, and the need for greater transparency regarding material provenance and environmental attributes. However, this also presents an opportunity for the development of new manufacturing capabilities within the UK and the establishment of more localized, resilient supply chains that can reduce transport emissions and create new green jobs (reuters.com).
-
Financial Implications and Investment: While sustainable homes offer significant long-term operational savings for homeowners, the initial capital costs for compliance with the FHS can be higher than conventional builds. This upfront investment, particularly for heat pump systems and enhanced fabric, needs to be managed by developers. However, the long-term benefits, including lower energy bills, reduced carbon footprint, and enhanced asset value, are substantial. Government incentives, green mortgages, and innovative financing mechanisms will be crucial to de-risk investments and accelerate adoption. Furthermore, the FHS will drive innovation in off-site manufacturing (prefabrication and modular construction), which can enhance quality control, reduce on-site waste, and accelerate construction timelines, potentially mitigating some cost increases.
-
Integrated Design and Collaboration: Meeting the FHS requirements demands a far more integrated and collaborative design process. Architects, structural engineers, mechanical and electrical engineers, energy consultants, and contractors must work together from the earliest stages of a project. Early engagement of specialists in energy modelling, building physics, and sustainable materials is essential to optimise designs for performance, cost-effectiveness, and compliance. This shift away from traditional linear design processes towards a holistic, multi-disciplinary approach is fundamental for successful implementation of the standard.
Many thanks to our sponsor Focus 360 Energy who helped us prepare this research report.
3. Technological Innovations Driving Sustainable Construction
The mandate for sustainable construction, particularly exemplified by standards like the FHS, is a powerful catalyst for technological innovation. These innovations span heating solutions, renewable energy integration, and the development of advanced building materials, collectively shaping a more resource-efficient and low-carbon built environment.
3.1 Low-Carbon Heating Solutions
The effective prohibition of gas boilers in new builds has significantly accelerated the adoption and refinement of low-carbon heating technologies, with heat pumps leading the charge:
-
Heat Pumps: Air-source heat pumps (ASHPs) and ground-source heat pumps (GSHPs) are increasingly recognised as the cornerstone of future domestic heating. Unlike conventional boilers that generate heat by burning fossil fuels, heat pumps operate by extracting low-grade heat from external sources (air, ground, or water) and upgrading it to a higher temperature suitable for heating buildings and hot water. Their efficiency is measured by the Coefficient of Performance (COP) or Seasonal Coefficient of Performance (SCOP), typically ranging from 2.5 to 4.5, meaning they produce 2.5 to 4.5 units of heat energy for every unit of electricity consumed. This makes them significantly more efficient than electric resistance heating and, when powered by renewable electricity, virtually emission-free at the point of use.
- Air-Source Heat Pumps (ASHPs): The most common type, ASHPs extract heat from the outside air. They are relatively straightforward to install, requiring an outdoor unit similar to an air conditioning condenser. Modern ASHPs can operate effectively even in sub-zero temperatures, although their efficiency may decrease. They can be ‘air-to-water’ (heating radiators or underfloor heating) or ‘air-to-air’ (providing warm air directly).
- Ground-Source Heat Pumps (GSHPs): These systems extract heat from the ground via buried pipe loops (horizontal trenches or vertical boreholes). GSHPs benefit from the stable temperature of the ground, making them highly efficient year-round. While installation is more complex and costly due to the excavation required, their higher efficiency and longevity often provide a superior long-term return on investment.
- Hybrid Heat Pumps: These systems combine a heat pump with a conventional boiler, allowing the system to switch between sources depending on outside temperature and energy prices, offering flexibility during the transition phase.
- Challenges: Despite their benefits, challenges include high upfront costs, perceived noise levels (though much improved in modern units), appropriate sizing for older properties, and ensuring adequate thermal insulation within the building for optimal performance. Furthermore, the type of refrigerant used in heat pumps is a critical consideration due to the Global Warming Potential (GWP) of some HFC refrigerants, driving innovation towards low-GWP alternatives.
-
District Heating Networks (DHN): In urban and high-density areas, district heating systems offer a compelling centralized heating solution. A DHN distributes heat from a central source (e.g., combined heat and power (CHP) plants, large-scale heat pumps, waste heat from industrial processes, geothermal energy) to multiple buildings through an insulated pipe network. This approach offers significant advantages in terms of efficiency, fuel flexibility (allowing for a mix of low-carbon sources), and reduced individual carbon footprints. DHNs can achieve economies of scale and better manage peak demands. While requiring substantial initial infrastructure investment and complex planning, they are a vital component of urban decarbonisation strategies and are explicitly supported by policy frameworks as a preferred heat solution in certain zones (at-eco.co.uk).
3.2 Renewable Energy Integration
Integrating on-site renewable energy sources into building designs offers multiple benefits, reducing reliance on fossil fuels, lowering operational costs, and enhancing energy resilience.
-
Solar Photovoltaic (PV) Systems: These systems, comprising solar panels, an inverter, and potentially a battery, generate clean electricity directly from sunlight. They are increasingly prevalent on residential and commercial buildings, reducing grid reliance and lowering energy bills. Innovations include building-integrated photovoltaics (BIPV), where PV cells are integrated directly into building materials such as roofing tiles or facade elements, offering aesthetic benefits. Advances in cell efficiency (e.g., perovskite cells, bifacial modules) and module durability are continuously improving their performance and economic viability. Net metering policies or feed-in tariffs (where applicable) further enhance the financial attractiveness for homeowners and businesses (at-eco.co.uk).
-
Battery Storage Solutions: The intermittency of renewable energy generation (e.g., solar only produces during daylight hours) necessitates efficient energy storage. On-site battery storage systems, predominantly lithium-ion batteries, allow for the capture and storage of surplus renewable energy generated during off-peak times or high generation periods for use during peak demand, at night, or during grid outages. This enhances self-consumption of renewable energy, reduces reliance on grid electricity, and can contribute to grid stability through demand-side response programmes. Integration with smart home energy management systems allows for intelligent charging and discharging based on electricity prices and predicted generation/consumption patterns (at-eco.co.uk).
-
Solar Thermal Systems: Distinct from PV, solar thermal systems capture solar radiation to heat water directly, typically for domestic hot water supply. These systems can significantly reduce the energy demand for water heating, complementing other low-carbon heating strategies.
3.3 Advanced Building Materials and Construction Methods
The selection of sustainable materials is paramount for reducing the environmental impact of construction, particularly in addressing embodied carbon.
-
Mass Timber (e.g., Cross-Laminated Timber – CLT): Mass timber products, particularly Cross-Laminated Timber (CLT), are rapidly gaining popularity as a sustainable and efficient alternative to concrete and steel in structural applications. CLT panels are engineered wood products made by gluing together layers of solid-sawn timber, with each layer oriented perpendicular to the adjacent layers, enhancing structural stability and strength. Its advantages include:
- Carbon Sequestration: Wood naturally stores atmospheric carbon dioxide during its growth, effectively ‘locking’ it away for the lifespan of the building, making mass timber a carbon sink.
- Lower Embodied Carbon: The energy required to produce mass timber is significantly lower than that for steel or concrete, drastically reducing its embodied carbon footprint.
- Speed and Efficiency: Prefabricated CLT panels can be rapidly assembled on site, leading to shorter construction times, reduced labour costs, and less site waste.
- Lightweight: Mass timber structures are lighter than concrete, reducing foundation requirements and transport loads.
- Aesthetics and Well-being: Exposed timber surfaces create warm, aesthetically pleasing interiors, with research suggesting positive impacts on occupant well-being and productivity.
Projects like Stockholm Wood City exemplify the potential of mass timber, envisioning an entire urban district built predominantly from timber, showcasing its scalability and versatility (time.com).
-
Recycled Aggregates and Circular Economy Principles: The construction industry is a major consumer of virgin resources and a significant generator of waste. The adoption of circular economy principles aims to decouple economic growth from resource consumption by keeping materials in use for as long as possible. This includes:
- Recycled Aggregates: Utilizing recycled concrete, asphalt, and masonry as aggregates in new concrete and road bases significantly reduces the demand for virgin sand and gravel, conserves natural resources, and diverts waste from landfills. Innovation in processing and quality control ensures performance standards are met (reuters.com).
- Reclaimed Materials: Salvaging and reusing structural steel, bricks, timber, and other components from deconstructed buildings reduces embodied carbon and preserves the value of existing materials. Specialist demolition contractors are increasingly focused on deconstruction rather than demolition.
- Recycled Plastics and Composites: Research and development are focused on incorporating recycled plastics into building insulation, pipes, and composite materials, finding high-value applications for waste streams.
-
Novel and Bio-based Materials: The innovation landscape extends to entirely new material compositions or enhanced uses of natural materials:
- Low-Carbon Cements and Concretes: Developing alternatives to traditional Portland cement, which is highly carbon-intensive, through geopolymer concretes, alkali-activated materials, or carbon-capture technologies integrated into concrete production. These innovations significantly reduce the embodied carbon of concrete, a ubiquitous building material.
- Bio-based Insulation: Materials like hempcrete (hemp and lime binder), straw bales, sheep’s wool, and cork offer excellent thermal performance with negative or very low embodied carbon footprints, as they sequester carbon during their growth.
- Phase-Change Materials (PCMs): Integrated into building materials, PCMs can absorb and release thermal energy as they change phase (e.g., solid to liquid), helping to regulate indoor temperatures naturally and reduce reliance on active heating/cooling systems.
- Self-Healing Concrete: Research is ongoing into concrete that can autonomously repair cracks, extending its lifespan and reducing maintenance, often using embedded bacteria or microcapsules.
-
Prefabrication and Modular Construction: While not materials themselves, these construction methods significantly contribute to sustainability. By manufacturing building components or entire modules in a factory setting, waste is drastically reduced, quality control is enhanced (leading to better airtightness and thermal performance), and on-site construction time and disruption are minimised. This controlled environment also facilitates the precise integration of complex low-carbon technologies and materials.
Many thanks to our sponsor Focus 360 Energy who helped us prepare this research report.
4. Green Building Certifications and Standards: Benchmarking Performance
Green building certification systems serve as crucial frameworks for assessing, verifying, and promoting sustainable building practices across various dimensions of environmental performance. They provide a structured approach for designers, developers, and occupants to understand the sustainability credentials of a building, offering a credible benchmark beyond regulatory minimums.
4.1 Role and Scope of Certification Systems
Global and regional green building certifications play a vital role in formalizing and standardizing what constitutes a ‘green building’. They typically evaluate a project across multiple categories, including energy efficiency, water conservation, material selection, waste management, indoor environmental quality, land use, and innovation. Some of the most prominent systems include:
-
BREEAM (Building Research Establishment Environmental Assessment Method) – UK Origin: Launched in 1990, BREEAM is one of the world’s longest-established and most widely used environmental assessment methods for buildings. It provides a holistic assessment across various building types (new construction, in-use, refurbishment, communities). BREEAM assesses performance across nine key categories:
- Management: Project management and commissioning.
- Health and Wellbeing: Indoor air quality, thermal comfort, lighting, noise.
- Energy: Operational energy consumption and carbon emissions.
- Water: Water consumption and efficiency.
- Materials: Responsible sourcing, lifecycle impacts, recycled content.
- Waste: Waste reduction, reuse, recycling during construction and operation.
- Land Use and Ecology: Ecological value of the site, protection of biodiversity.
- Pollution: Emissions to air, land, and water.
- Transport: Access to sustainable transport, car parking.
Buildings are awarded ratings from ‘Pass’ to ‘Outstanding’, indicating their level of environmental performance (en.wikipedia.org).
-
LEED (Leadership in Energy and Environmental Design) – US Origin: Developed by the U.S. Green Building Council (USGBC), LEED is a globally recognized green building certification program. It offers a comprehensive rating system for design, construction, operations, and maintenance of green buildings. LEED projects earn points across several categories, and the sum of these points determines the certification level (Certified, Silver, Gold, Platinum). Key categories include:
- Location and Transportation: Sustainable site selection, access to public transport.
- Sustainable Sites: Site development, stormwater management, heat island effect.
- Water Efficiency: Indoor and outdoor water use reduction.
- **Energy and Atmosphere: Energy performance, renewable energy, refrigerant management.
- Materials and Resources: Waste reduction, material reuse, recycled content, regional materials.
- Indoor Environmental Quality: Air quality, lighting, thermal comfort, acoustics.
- Innovation: Exemplary performance, innovative strategies.
- Regional Priority: Credits addressing specific regional environmental priorities (en.wikipedia.org, en.wikipedia.org).
-
Passive House (Passivhaus) Standard – German Origin: While not a multi-criteria certification like BREEAM or LEED, Passive House is a rigorous, performance-based standard primarily focused on ultra-low energy consumption for heating and cooling. Its core principles involve: superior insulation, exceptionally airtight building envelopes, high-performance windows, thermal bridge-free construction, and mechanical ventilation with heat recovery. Buildings certified to Passive House standards demonstrate minimal energy demand, leading to significant operational cost savings and exceptional indoor comfort. It’s often seen as a practical pathway to achieving net-zero energy buildings due to its stringent focus on fabric efficiency.
-
WELL Building Standard: This standard focuses specifically on the impact of buildings on human health and well-being. It assesses factors such as air, water, nourishment, light, fitness, comfort, and mind, aiming to create environments that support and enhance the health of occupants.
-
Living Building Challenge (LBC): Considered one of the most stringent and holistic green building standards, the LBC aims for regenerative design. It defines seven performance areas, or ‘Petals’ (Place, Water, Energy, Health & Happiness, Materials, Equity, Beauty), with outcomes based on actual performance rather than predicted modelling. LBC projects are net-zero energy, net-zero water, and free of a ‘Red List’ of harmful chemicals.
4.2 Benefits of Green Building Certification
Achieving green building certification offers a multitude of tangible and intangible benefits for developers, occupants, and the wider community:
-
Enhanced Market Differentiation and Value: Certified green buildings often command higher occupancy rates, rental premiums, and resale values compared to conventional buildings. They attract environmentally conscious tenants and buyers, providing a clear competitive advantage in the market. Furthermore, adherence to green building standards can improve a developer’s ESG (Environmental, Social, and Governance) performance, making them more attractive to investors focused on sustainable portfolios.
-
Significant Operational Efficiency and Cost Savings: The rigorous requirements for energy and water efficiency embedded in certification systems directly translate into reduced utility bills over the building’s operational lifetime. Superior insulation, efficient HVAC systems, LED lighting, and water-saving fixtures dramatically lower energy and water consumption. Reduced maintenance costs due to higher quality materials and systems also contribute to long-term savings. For commercial properties, these savings directly impact the bottom line, enhancing profitability.
-
Improved Occupant Health, Productivity, and Comfort: Green buildings prioritize indoor environmental quality, leading to healthier and more comfortable spaces. Enhanced ventilation systems (like MVHR) improve air quality by reducing pollutants and allergens. Optimized natural daylighting, thermal comfort, and acoustic performance contribute to occupant well-being, reduce stress, and can lead to increased productivity in workplaces and better learning outcomes in schools. Studies have shown reduced absenteeism and improved cognitive function in certified green offices.
-
Risk Mitigation and Future-Proofing: Adhering to green building standards helps mitigate various risks. It future-proofs assets against increasingly stringent environmental regulations and carbon taxes. It reduces exposure to volatile energy prices. Moreover, resilient design principles often incorporated into certifications (e.g., stormwater management, passive survivability) enhance a building’s ability to withstand the impacts of climate change. For investors, green certifications signal responsible asset management and lower long-term liabilities.
-
Positive Brand Reputation and Corporate Social Responsibility (CSR): Achieving green building certification demonstrates a commitment to environmental stewardship and social responsibility. This enhances the brand image of developers, architects, and companies, fostering trust among stakeholders and attracting environmentally conscious talent. It positions them as leaders in sustainable development.
-
Access to Green Finance: A growing number of financial institutions offer preferential loan terms, ‘green mortgages’, and other financial incentives for certified sustainable buildings, recognizing their lower risk profile and higher long-term value. This can include lower interest rates or longer repayment periods.
In essence, green building certifications are not just about environmental compliance; they are comprehensive tools that drive innovation, enhance economic performance, and create healthier, more resilient spaces for people and the planet.
Many thanks to our sponsor Focus 360 Energy who helped us prepare this research report.
5. Challenges and Opportunities in Sustainable Construction
The transition to a fully sustainable construction industry, while indispensable, is not without its complexities. It presents a confluence of significant challenges, which, when strategically addressed, can unlock substantial opportunities for innovation, economic growth, and societal benefit.
5.1 Addressing the Pervasive Skills Gap
One of the most critical impediments to scaling sustainable construction practices is the pronounced skills gap within the workforce. The shift towards low-carbon technologies, advanced materials, and intricate building physics necessitates a new generation of highly skilled professionals and tradespeople. The existing workforce often lacks the requisite expertise, creating a bottleneck for the widespread adoption of technologies like heat pumps, MVHR systems, and integrated renewable energy solutions. A Reuters report highlighted this issue, noting the ‘long on ambition, short on people’ dilemma facing the UK’s decarbonisation efforts in buildings (reuters.com).
Challenges:
* Lack of Specialized Training: Traditional vocational and higher education curricula may not adequately cover the design, installation, and maintenance of modern sustainable technologies.
* Aging Workforce: Many experienced tradespeople are nearing retirement, taking with them valuable tacit knowledge, while younger generations are not entering the industry in sufficient numbers.
* Perception of the Industry: Construction is sometimes perceived as a low-tech or physically demanding industry, deterring new talent who might be attracted to greener, more technologically advanced roles.
* Capacity for Retraining: The sheer volume of existing workers needing retraining poses a significant logistical and financial challenge.
Opportunities & Solutions:
* Targeted Training and Education Programs: Development of specialized courses, certifications, and apprenticeships for specific green skills (e.g., Passive House designers, certified heat pump installers, energy assessors, BIM for sustainability specialists). Partnerships between educational institutions, industry bodies, and government are crucial.
* Upskilling and Reskilling Initiatives: Implementing comprehensive programs to retrain existing construction workers in areas such as airtightness detailing, thermal bridge mitigation, smart home system integration, and advanced insulation techniques.
* Attracting New Talent: Marketing the construction industry as a dynamic, technologically advanced, and environmentally critical sector to attract younger generations. Emphasizing career paths in green construction can resonate with those seeking purpose-driven work.
* Digital Tools and Automation: Leveraging digital tools, BIM, and potentially automation for aspects of construction can reduce reliance on manual labour for repetitive tasks, allowing the skilled workforce to focus on more complex, value-added activities.
5.2 Overcoming Supply Chain Barriers
The transition to sustainable construction demands fundamental shifts in how materials are sourced, produced, transported, and utilized. Existing supply chains are often optimized for conventional materials and linear production models, presenting significant barriers to the widespread adoption of sustainable alternatives.
Challenges:
* Availability and Scalability: Many advanced sustainable materials (e.g., low-carbon concrete, bio-based insulation) and technologies (e.g., specific heat pump models) may not yet be available at the required scale or in all geographic regions.
* Cost Volatility: Newer, less mature sustainable materials and technologies can have higher initial costs compared to their conventional counterparts, although life cycle costing often demonstrates superior long-term value.
* Lack of Standardization: Absence of common standards for green materials or components can hinder interoperability and efficient integration.
* Logistical Complexity: Sourcing materials from diverse, potentially new suppliers requires adjustments to procurement strategies, logistics, and inventory management.
* Transparency and Embodied Carbon Data: A lack of robust, standardized data on the embodied carbon and lifecycle impacts of materials makes informed decision-making challenging.
Opportunities & Solutions:
* Localized and Circular Sourcing: Prioritizing local suppliers reduces transportation emissions. Implementing circular economy principles through material reuse, recycling, and responsible waste management significantly lowers demand for virgin resources (reuters.com). This also enhances supply chain resilience.
* Supplier Collaboration and Innovation: Fostering partnerships with manufacturers to co-develop and scale up production of innovative, low-carbon materials and prefabricated solutions. Encouraging investment in green manufacturing processes.
* Digital Platforms and Data Management: Utilizing Building Information Modelling (BIM) and digital material passports to track the environmental performance of materials, facilitate material reuse, and optimize logistics.
* Incentivizing Green Production: Government policies, grants, and tax breaks for manufacturers developing sustainable building products can stimulate supply.
5.3 Policy and Regulatory Support
Government policies and robust regulatory frameworks are paramount in steering the construction industry towards sustainability. They provide the necessary impetus, direction, and level playing field for widespread adoption of sustainable practices.
Challenges:
* Regulatory Lag: Building codes can be slow to adapt to new technologies and scientific understanding of environmental impacts.
* Lack of Consistency: Variations in regulations across different regions or countries can create complexity for large developers.
* Insufficient Enforcement: Even well-intentioned regulations require robust enforcement mechanisms to be effective.
* Policy Uncertainty: Frequent changes or lack of long-term clarity in policy can deter investment in sustainable solutions.
Opportunities & Solutions:
* Strong, Ambitious Building Codes: Implementing progressive standards like the Future Homes Standard that set clear, ambitious targets for energy efficiency and carbon reduction. Regular reviews and updates are necessary to keep pace with technological advancements.
* Financial Incentives and Subsidies: Offering grants, tax credits, preferential loans, and rebates for adopting green technologies (e.g., heat pump grants, solar PV subsidies) can significantly de-risk investments for developers and homeowners, accelerating adoption (ft.com).
* Carbon Pricing Mechanisms: Implementing carbon taxes or cap-and-trade schemes can internalize the cost of emissions, making high-carbon materials and practices less economically viable.
* Public Procurement Policy: Governments can leverage their purchasing power by mandating green building standards for public projects, thereby creating market demand and driving innovation.
* Streamlined Planning and Permitting: Expediting approvals for sustainable developments and low-carbon technology installations can reduce lead times and administrative burdens.
5.4 Economic and Financial Considerations
The perception of higher upfront costs for sustainable construction often presents a significant barrier. However, a holistic financial perspective reveals substantial long-term economic benefits.
Challenges:
* Higher Upfront Capital Costs: Green materials and advanced technologies can have a higher initial price point than conventional options.
* Access to Green Finance: While growing, specialized green financing products might not be readily accessible or understood by all developers.
* Split Incentives: In rental properties, landlords bear the upfront cost of energy efficiency improvements, while tenants reap the benefits of lower bills, creating a disincentive for investment.
Opportunities & Solutions:
* Life Cycle Costing (LCC): Promoting the use of LCC, which accounts for initial capital, operational, maintenance, and end-of-life costs over a building’s entire lifespan. LCC consistently demonstrates that green buildings offer superior economic performance due to significantly lower operational costs (energy, water) and longer asset life.
* Green Finance Instruments: Expanding access to green bonds, sustainability-linked loans, green mortgages, and other financial products that incentivize sustainable development by offering more favourable terms.
* Increased Asset Value: Demonstrating that green buildings command higher property values and attract higher rental yields, thus providing a strong return on investment.
* Job Creation: The transition to a green construction industry is a significant driver of job creation across various sectors, from manufacturing to installation and maintenance of green technologies.
5.5 Data, Digitalization, and Innovation
The digital transformation of the construction industry offers unparalleled opportunities to enhance sustainability performance, efficiency, and data-driven decision-making.
Challenges:
* Data Silos: Information fragmentation across different project stages and stakeholders.
* Lack of Standardization in Data Collection: Inconsistent methodologies for measuring environmental performance.
* Resistance to Change: Traditional industry practices can be slow to adopt new digital tools and processes.
Opportunities & Solutions:
* Building Information Modelling (BIM): BIM is revolutionizing design and construction by creating a shared digital model of a building. For sustainability, BIM enables:
* Energy Performance Simulation: Early-stage modelling of energy use, daylighting, and ventilation to optimize design for efficiency.
* Embodied Carbon Calculation: Integration with material databases to assess the embodied carbon of different design options.
* Waste Reduction: Precise material take-offs and clash detection reduce material waste.
* Lifecycle Management: Facilitates asset management, maintenance, and eventual deconstruction/reuse of materials.
* Digital Twins and IoT: Creating real-time digital replicas of buildings (digital twins) integrated with Internet of Things (IoT) sensors allows for continuous monitoring and optimization of operational energy performance, indoor environmental quality, and predictive maintenance. This data-driven approach allows buildings to adapt to occupant behaviour and external conditions, maximizing efficiency (time.com).
* Artificial Intelligence (AI) and Machine Learning (ML): AI can optimize building design for energy efficiency, predict material performance, streamline supply chain logistics, and enhance operational control systems for smart buildings.
* Modular and Off-site Construction: Digital tools underpin the precision and efficiency of off-site manufacturing, leading to higher quality, less waste, and faster construction cycles for sustainable buildings.
By strategically navigating these challenges and leveraging the inherent opportunities, the construction industry can accelerate its transition towards a truly sustainable, resilient, and high-performing built environment.
Many thanks to our sponsor Focus 360 Energy who helped us prepare this research report.
6. Conclusion
The construction industry’s monumental shift towards sustainability is not merely an aspirational goal but an urgent imperative, driven by the undeniable necessity to dramatically reduce carbon emissions and align with global climate objectives. The trajectory of this transformation is profoundly shaped by progressive regulatory frameworks, exemplified by the UK’s ambitious Future Homes Standard, which serves as a powerful catalyst for change by setting stringent targets for energy efficiency and mandating the adoption of low-carbon technologies in new residential developments.
This comprehensive transition necessitates a holistic approach, encompassing a ‘fabric first’ design philosophy, the widespread integration of advanced heat pump systems and on-site renewable energy generation, and a fundamental re-evaluation of material choices towards those with lower embodied carbon and greater circularity. The emergence of mass timber, recycled aggregates, and novel bio-based materials underscores the vibrant innovation within the sector. Furthermore, the increasing prominence of green building certification systems like BREEAM and LEED provides essential benchmarks for performance, driving market differentiation, enhancing operational efficiency, and promoting occupant well-being.
While the path forward is marked by significant challenges—notably the pervasive skills gap, the need for extensive supply chain adjustments, and the complexities of initial capital investment—these obstacles simultaneously present unparalleled opportunities for growth, innovation, and long-term value creation. Addressing the skills gap through targeted training and education, fostering resilient and localized supply chains, and establishing supportive policy frameworks with clear incentives are critical enablers for widespread adoption.
The integration of digital technologies, including Building Information Modelling (BIM), digital twins, and artificial intelligence, promises to revolutionize how buildings are designed, constructed, and operated, unlocking unprecedented efficiencies and performance gains. Ultimately, the success of this transformation hinges on collaborative efforts across all stakeholders: governments enacting forward-looking policies, industry leaders investing in research and development and sustainable practices, financial institutions providing green capital, and educational bodies nurturing the workforce of the future.
By embracing this multifaceted transition with determination and foresight, the construction sector can not only mitigate its environmental impact but also deliver a built environment that is healthier, more resilient, economically viable, and intrinsically sustainable, contributing profoundly to global climate action and the well-being of future generations.
Many thanks to our sponsor Focus 360 Energy who helped us prepare this research report.
References
- Future Homes Standard 2025: UK Sustainability. (n.d.). AT-ECO. Retrieved from https://www.at-eco.co.uk/blog/future-homes-standard-2025.html
- Comment: Why circular built environment makes economic, environmental sense. (2024, February 23). Reuters. Retrieved from https://www.reuters.com/sustainability/climate-energy/comment-why-circular-built-environment-makes-economic-environmental-sense-2024-02-23/
- Sweden is Building the World’s Largest City Made Entirely From Timber. (2024, January 23). Time. Retrieved from https://time.com/7207873/sweden-stockholm-wood-city-sustainability/
- Materials Rethink Underpins Architecture’s Sustainability Push. (2024, June 15). Financial Times. Retrieved from https://www.ft.com/content/f2d8c127-da52-42f3-995e-93af364c3195
- The Design Firm Making Net-Zero Emissions Buildings a Reality. (2024, November 15). Time. Retrieved from https://time.com/7177539/cannondesign-net-zero-emissions-buildings/
- Government Caves in as Wood Burning Stoves Allowed in Future Homes Standard, Despite Health Warnings. (2024, May 10). Homebuilding & Renovating. Retrieved from https://www.homebuilding.co.uk/news/government-caves-in-as-wood-burning-stoves-allowed-in-future-homes-standard-despite-health-warnings
- Long on Ambition, Short on People: How the Skills Gap Could Scupper UK’s Bid to Decarbonise Buildings. (2024, November 28). Reuters. Retrieved from https://www.reuters.com/sustainability/climate-energy/long-ambition-short-people-how-skills-gap-could-scupper-uks-bid-decarbonise-2024-11-28/
- Green building certification systems. (n.d.). Wikipedia. Retrieved from https://en.wikipedia.org/wiki/Green_building_certification_systems
- World Green Building Council. (n.d.). Wikipedia. Retrieved from https://en.wikipedia.org/wiki/World_Green_Building_Council
- U.S. Green Building Council. (n.d.). Wikipedia. Retrieved from https://en.wikipedia.org/wiki/U.S._Green_Building_Council
This report highlights the critical role of policy frameworks like the Future Homes Standard. Exploring how these standards can be adapted and implemented across diverse international contexts could significantly accelerate global progress toward decarbonizing the built environment.
Thank you for your comment. I agree that exploring international adaptations is crucial! We’ve touched on the UK’s Future Homes Standard, but comparing its implementation and effectiveness against similar policies in other countries could offer valuable insights and best practices for global decarbonization efforts. What specific international examples are you most interested in?
Editor: FocusNews.Uk
Thank you to our Sponsor Focus 360 Energy
The emphasis on integrating digital technologies like BIM and digital twins is particularly compelling. How do you see smaller construction firms, who may lack resources for sophisticated tech, effectively participating in this data-driven future?