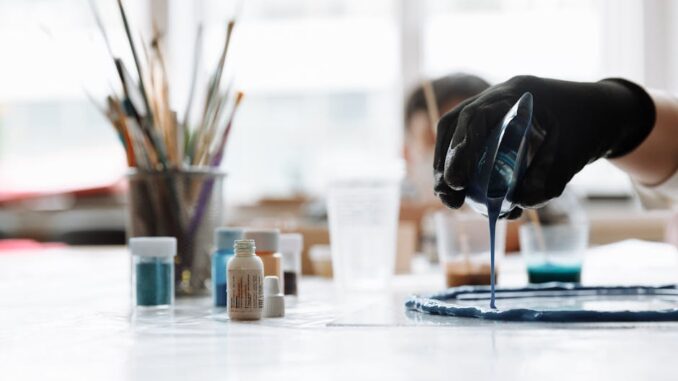
Abstract
This research report provides a comprehensive overview of sealants, with a particular emphasis on caulk as a prominent category. Moving beyond its simple application for sealing stationary cracks and gaps, we delve into the intricate details of sealant chemistry, application methodologies, and future technological advancements. This paper examines the evolution of sealants from rudimentary organic materials to sophisticated polymer-based formulations tailored for specific environments and substrates. The discussion encompasses the chemical composition of various sealant types (silicone, acrylic, polyurethane, etc.), explores the impact of environmental factors on sealant performance, analyzes advanced application techniques, and evaluates the latest innovations, including self-healing and environmentally friendly options. We will consider the challenges of sealant selection, application, and long-term performance, with a focus on optimizing these aspects for sustainable construction practices. This report aims to provide expert insights into the current state of sealant technology and offer a perspective on future directions, highlighting opportunities for innovation and improved performance.
Many thanks to our sponsor Focus 360 Energy who helped us prepare this research report.
1. Introduction
Sealants are indispensable components in modern construction and manufacturing, providing crucial barriers against the ingress of moisture, air, and other environmental elements. While the term ‘caulk’ is often used synonymously with sealants, it more accurately describes a specific subset used for filling cracks and gaps, particularly in stationary joints. The wider category of sealants includes a diverse range of materials designed for dynamic joints and specialized applications. The selection of an appropriate sealant is contingent upon a complex interplay of factors, including substrate material, environmental exposure, joint movement, and desired lifespan. Choosing the wrong sealant can lead to premature failure, resulting in costly repairs, structural damage, and potential health hazards. Therefore, a thorough understanding of sealant properties and application techniques is paramount.
Historically, sealants were primarily composed of rudimentary organic materials such as asphalt, pitch, and natural rubbers. These materials offered limited durability and resistance to environmental degradation. However, with the advent of polymer chemistry, a new era of high-performance sealants emerged. Silicone, acrylic, polyurethane, polysulfide, and hybrid polymer sealants now offer superior adhesion, elasticity, and resistance to UV radiation, temperature extremes, and chemical exposure. This evolution has enabled the construction of increasingly complex and durable structures.
This report will examine the chemical underpinnings of these advanced sealants, paying particular attention to the influence of molecular structure on macroscopic properties. We will further explore the latest advancements in sealant technology, including the development of self-healing polymers, bio-based formulations, and novel application methods. Finally, we will address the critical issue of sealant longevity and sustainability, considering both environmental impact and life-cycle cost.
Many thanks to our sponsor Focus 360 Energy who helped us prepare this research report.
2. Chemical Composition and Classification of Sealants
Sealants can be broadly categorized based on their chemical composition and curing mechanism. The most common types include:
-
Silicone Sealants: Silicone sealants are based on polymers containing repeating siloxane units (-Si-O-). They are known for their excellent flexibility, UV resistance, and temperature stability. Silicone sealants are often further classified as acetoxy (acetic acid byproduct), neutral cure (alcohol byproduct), or oxime cure (oxime byproduct). Acetoxy silicones are generally less expensive but can corrode certain metals. Neutral cure silicones offer broader substrate compatibility. However, the curing mechanism is not dependent on moisture, so may cure slower in some low humidity environments. Neutral cure silicones can be further subdivided based on the neutral by-product formed during cure, which can impact performance.
-
Acrylic Sealants: Acrylic sealants are water-based polymers that cure through evaporation of water. They are known for their paintability, low odor, and ease of application. However, acrylic sealants typically exhibit lower elasticity and chemical resistance compared to silicones and polyurethanes. Acrylic latex sealants can be modified with silicones, or urethanes to improve elasticity.
-
Polyurethane Sealants: Polyurethane sealants are based on polymers containing urethane linkages (-NH-CO-O-). They offer excellent adhesion, durability, and resistance to abrasion and chemicals. Polyurethane sealants are often used in demanding applications such as expansion joints in concrete structures and automotive body sealing. Polyurethane sealants may require primers to improve adhesion. Isocyanates, a component of polyurethanes, are known skin sensitisers. Moisture cure and two-part formulations are available.
-
Polysulfide Sealants: Polysulfide sealants are based on polymers containing sulfur-sulfur bonds (-S-S-). They are highly resistant to chemicals, solvents, and fuels, making them suitable for applications in the petrochemical industry and marine environments. Polysulfide sealants exhibit good elongation and recovery properties.
-
Hybrid Polymer Sealants (e.g., MS Polymers, Silyl-Modified Polymers): Hybrid polymer sealants combine the advantages of different polymer types. For example, MS Polymers (modified silane polymers) offer the flexibility and UV resistance of silicones with the paintability and adhesion of polyurethanes. Hybrid polymers can also be formulated with faster cure times and improved environmental friendliness.
The specific chemical composition of a sealant determines its key properties, including adhesion, elasticity, tensile strength, hardness, and resistance to environmental factors. Additives such as plasticizers, fillers, and UV stabilizers are often incorporated into sealant formulations to further enhance performance and tailor properties for specific applications. Fillers, such as calcium carbonate, silica, or talc, can influence the sealant’s viscosity, hardness, and cost. UV stabilizers protect the sealant from degradation caused by ultraviolet radiation, extending its lifespan in outdoor applications. The use of reactive silanes may improve adhesion to some surfaces.
Many thanks to our sponsor Focus 360 Energy who helped us prepare this research report.
3. Factors Influencing Sealant Performance
The performance of a sealant is influenced by a multitude of factors, which can be broadly categorized as:
-
Substrate Properties: The nature of the substrate material significantly impacts sealant adhesion. Surface energy, porosity, and cleanliness are crucial factors. Sealants adhere best to clean, dry, and properly prepared surfaces. Primers are often used to improve adhesion to difficult-to-bond substrates such as porous concrete or non-polar plastics. Compatibility between the sealant and substrate is also essential to prevent chemical reactions that could lead to bond failure.
-
Environmental Conditions: Exposure to environmental factors such as UV radiation, temperature fluctuations, humidity, and chemical pollutants can significantly degrade sealant performance. UV radiation can cause chain scission and crosslinking, leading to embrittlement and cracking. Temperature fluctuations induce expansion and contraction, placing stress on the sealant joint. Humidity can affect the curing process and promote the growth of mold and mildew. Chemical pollutants can react with the sealant, leading to degradation and loss of properties. Salt spray exposure accelerates sealant degradation on exposed marine applications.
-
Joint Design: The design of the joint plays a crucial role in sealant performance. Joint width, depth, and shape must be properly designed to accommodate anticipated movement. An improperly designed joint can lead to excessive stress on the sealant, resulting in premature failure. The correct aspect ratio is important to prevent cohesive failure or failure at the bondline.
-
Application Techniques: Proper application techniques are essential for achieving optimal sealant performance. This includes surface preparation, sealant application, tooling, and curing. Applying the sealant to a contaminated surface or using an incorrect application technique can lead to poor adhesion and premature failure. Tooling the sealant immediately after application ensures proper contact with the substrate and creates a smooth, aesthetically pleasing finish. It is essential to control the rate and temperature of cure to get optimal performance, for instance applying sealants at low temperatures will slow the cure and in some cases prevent it from curing properly.
-
Sealant Properties: The inherent properties of the sealant itself, such as elasticity, tensile strength, and chemical resistance, are critical determinants of its performance. Sealants with high elasticity can accommodate greater joint movement without failure. Sealants with high tensile strength can withstand greater stress. Sealants with good chemical resistance can resist degradation from exposure to harsh chemicals.
Addressing these factors requires a holistic approach, encompassing careful sealant selection, proper surface preparation, appropriate joint design, meticulous application techniques, and ongoing maintenance.
Many thanks to our sponsor Focus 360 Energy who helped us prepare this research report.
4. Advanced Application Techniques and Technologies
Advancements in application techniques and technologies are continually improving sealant performance and efficiency. Some notable developments include:
-
Automated Application Systems: Automated application systems offer precise and consistent sealant application, reducing labor costs and improving quality control. These systems are particularly valuable for large-scale construction projects and manufacturing processes. Robots can be programmed to apply sealants to complex geometries with high accuracy.
-
Primerless Sealants: Primerless sealants are formulated to adhere directly to a wide range of substrates without the need for a primer. This simplifies the application process and reduces the risk of errors. However, the substrate should still be cleaned appropriately.
-
Self-Leveling Sealants: Self-leveling sealants are designed to flow freely and create a smooth, level surface without the need for tooling. They are ideal for sealing horizontal joints and cracks in concrete and asphalt surfaces. These sealants typically have a low viscosity and are formulated to minimize air entrapment.
-
Sprayable Sealants: Sprayable sealants offer a fast and efficient way to apply sealant to large areas. They are particularly useful for roofing applications and sealing irregular surfaces. Sprayable sealants can be applied using airless spray equipment or aerosol cans.
-
Pre-Compressed Sealants: Pre-compressed sealants are designed to be compressed during installation and expand to fill the joint. They offer excellent sealing performance and can accommodate significant joint movement. Pre-compressed sealants are often used in expansion joints and bridge decks.
-
BIM Integration: Building Information Modeling (BIM) is increasingly being used to optimize sealant selection and application. BIM allows engineers to simulate joint movement and predict sealant performance under different environmental conditions. This helps to ensure that the correct sealant is selected for each application and that the joint is properly designed.
-
Digital Monitoring: Wireless sensors can be embedded in sealant joints to monitor performance and detect early signs of failure. These sensors can measure strain, temperature, and humidity, providing valuable data for maintenance and repair planning. Such predictive maintenance strategies are crucial for minimizing downtime and extending the lifespan of structures.
Many thanks to our sponsor Focus 360 Energy who helped us prepare this research report.
5. Longevity and Sustainability of Sealants
The longevity and sustainability of sealants are increasingly important considerations. Factors contributing to sealant longevity include:
-
Material Selection: Choosing the right sealant for the specific application is critical for maximizing lifespan. Factors to consider include substrate compatibility, environmental exposure, and joint movement. Using a sealant with inadequate UV resistance in an outdoor application will inevitably lead to premature failure.
-
Proper Application: Following proper application techniques is essential for ensuring optimal sealant performance and longevity. This includes surface preparation, sealant application, tooling, and curing.
-
Regular Maintenance: Regular inspection and maintenance can help to extend the lifespan of sealants. This includes cleaning, repairing minor damage, and reapplying sealant as needed.
-
Life-Cycle Cost Analysis: A life-cycle cost analysis can help to determine the most cost-effective sealant option over the long term. This analysis should consider the initial cost of the sealant, as well as the cost of maintenance, repair, and replacement. While a more expensive sealant may have a higher initial cost, it may offer lower life-cycle costs due to its longer lifespan and reduced maintenance requirements.
Sustainability considerations include:
-
Environmental Impact of Manufacturing: The manufacturing process of sealants can have a significant environmental impact, including the use of raw materials, energy consumption, and greenhouse gas emissions. Choosing sealants from manufacturers that prioritize sustainable practices can help to reduce this impact.
-
Volatile Organic Compounds (VOCs): Many sealants contain VOCs, which can contribute to air pollution and pose health risks. Low-VOC and VOC-free sealants are available and should be considered whenever possible. Regulations regarding VOC content in sealants are becoming increasingly stringent in many regions.
-
Recyclability: While most sealants are not currently recyclable, research is ongoing to develop recyclable sealant materials. Using sealants that can be recycled at the end of their lifespan would significantly reduce their environmental impact. The design of a recyclable sealant is a complex undertaking as performance requirements may make the materials too complex to separate and reuse.
-
Bio-Based Sealants: Bio-based sealants are made from renewable resources, such as plant oils and sugars. They offer a more sustainable alternative to traditional petroleum-based sealants. However, the performance of bio-based sealants must be carefully evaluated to ensure that they meet the requirements of the application.
Many thanks to our sponsor Focus 360 Energy who helped us prepare this research report.
6. Future Trends and Innovations
The field of sealant technology is constantly evolving, with new materials and application techniques being developed to address emerging challenges. Some key trends and innovations include:
-
Self-Healing Sealants: Self-healing sealants are designed to automatically repair minor damage, such as cracks and punctures. This extends the lifespan of the sealant and reduces the need for maintenance. Self-healing mechanisms can involve the release of encapsulated healing agents or the activation of reversible chemical bonds.
-
Smart Sealants: Smart sealants incorporate sensors and other technologies to monitor performance and provide real-time feedback. This information can be used to optimize maintenance and prevent failures. Smart sealants could also be used to detect leaks or other problems in buildings and infrastructure.
-
Nanomaterial-Enhanced Sealants: Nanomaterials, such as carbon nanotubes and graphene, can be incorporated into sealant formulations to enhance their properties. Nanomaterials can improve strength, durability, UV resistance, and other key performance characteristics.
-
3D-Printed Sealants: 3D printing technology is being used to create custom sealant solutions for complex geometries. This allows for greater design flexibility and can improve the efficiency of sealant application. 3D printing can also be used to create multi-material sealants with tailored properties.
-
Improved Weatherability: Improvements to polymer formulations are resulting in sealants with better resistance to ultraviolet light, weathering, and temperature extremes.
-
Advanced Adhesion Promoters: Novel adhesion promoters are being developed to improve the bond strength of sealants to a wider range of substrates. These promoters often involve the use of silane coupling agents or other reactive chemicals.
Many thanks to our sponsor Focus 360 Energy who helped us prepare this research report.
7. Conclusion
Sealants play a critical role in modern construction and manufacturing, providing essential barriers against environmental elements. The evolution of sealant technology from rudimentary organic materials to sophisticated polymer-based formulations has enabled the construction of increasingly complex and durable structures. Selecting the right sealant is critical and depends on various factors, including substrate material, environmental exposure, joint movement, and desired lifespan. Recent advancements in application techniques and technologies, such as automated application systems, primerless sealants, and self-leveling sealants, have improved sealant performance and efficiency. Furthermore, the rising demand for sustainability has propelled the development of environmentally friendly sealants with low VOC content, bio-based composition, and recyclability. Future trends and innovations, such as self-healing sealants, smart sealants, and nanomaterial-enhanced sealants, promise to further enhance sealant performance and longevity.
Continued research and development are essential for addressing the evolving challenges in sealant technology and optimizing the performance of sealants in diverse applications. By embracing innovation and adopting sustainable practices, we can ensure that sealants continue to play a vital role in creating durable, energy-efficient, and environmentally responsible structures.
Many thanks to our sponsor Focus 360 Energy who helped us prepare this research report.
References
- Brydson, J. A. (1999). Plastics Materials. Butterworth-Heinemann.
- Elias, H. G. (2005). An Introduction to Polymer Science. Wiley-VCH.
- Knapen, E., & van Gemert, D. (2009). Cement-based renders with high resistance to biogenic sulfuric acid corrosion. Building and Environment, 44(11), 2236-2244.
- Loh, G. H., Chua, K. J., Yeong, W. Y., & Song, J. (2020). 3D printing of concrete structures: A review. Virtual and Physical Prototyping, 15(6), 674-691.
- Oberndorfer, J. C., Lundgren, M. R., & Branch, G. M. (2007). Urban stormwater: Environmental science and engineering. John Wiley & Sons.
- Packham, D. E. (2005). Handbook of Adhesion. John Wiley & Sons.
- van Oss, C. J. (2006). Interfacial Forces in Aqueous Media. CRC press.
- ASTM International. (Various standards on sealants and adhesives).
- ISO Standards. (Various standards on sealants and adhesives).
- Technical Data Sheets from various sealant manufacturers (e.g., Dow, Sika, Bostik).
The discussion of hybrid polymer sealants is particularly interesting. Could you elaborate on the specific applications where MS Polymers or silyl-modified polymers outperform traditional sealants, particularly in terms of long-term durability and environmental resistance?
That’s a great question! MS Polymers really shine in applications demanding flexibility and strong adhesion, like sealing joints in prefabricated buildings or marine environments. Their superior UV and chemical resistance also make them ideal for demanding outdoor applications where traditional sealants might degrade quicker. Let’s delve more into specific case studies next time!
Editor: FocusNews.Uk
Thank you to our Sponsor Focus 360 Energy
Given the increasing stringency of VOC regulations, could you expand on the advancements in water-based sealant technologies and their performance trade-offs compared to solvent-based alternatives, especially concerning durability and application in demanding environments?