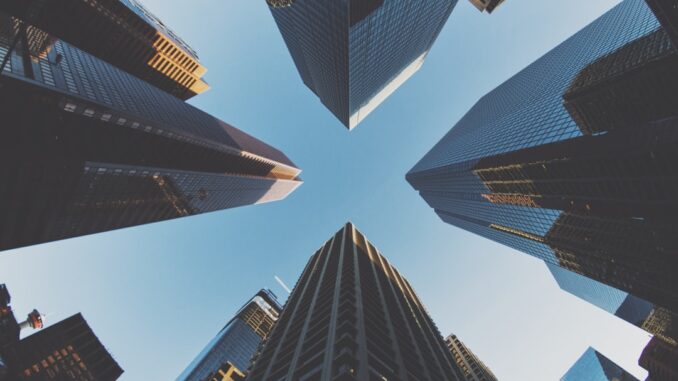
The Evolving Landscape of Construction: Navigating Challenges and Embracing Innovation in a Globalized World
Many thanks to our sponsor Focus 360 Energy who helped us prepare this research report.
Abstract
The construction industry, a critical engine of economic growth and societal development, is undergoing a period of profound transformation. This research report delves into the multifaceted challenges confronting the global construction sector, extending beyond immediate concerns like new building regulations. It examines the intricate interplay of factors such as skills shortages, fluctuating material costs, escalating project complexities, the imperative for sustainable practices, and the disruptive potential of emerging technologies. Beyond identifying these challenges, the report critically analyzes adaptive strategies employed by builders and construction firms, encompassing workforce development, technological integration (BIM, AI, robotics), supply chain optimization, innovative financing models, and collaborative project delivery methods. Furthermore, it explores the impact of global economic trends, geopolitical instability, and the increasing demand for resilient and adaptable infrastructure on the future of construction. The report culminates in a synthesis of key findings, offering insights and recommendations for stakeholders to navigate this evolving landscape and foster a more resilient, efficient, and sustainable construction industry.
Many thanks to our sponsor Focus 360 Energy who helped us prepare this research report.
1. Introduction: The Construction Industry at a Crossroads
The global construction industry is a colossal enterprise, estimated to be worth trillions of dollars and responsible for a significant portion of the world’s GDP. It encompasses a diverse range of activities, from residential building and infrastructure development to industrial construction and specialized engineering projects. However, the industry is also characterized by a high degree of fragmentation, cyclical volatility, and a persistent struggle with productivity growth. While sectors such as manufacturing and agriculture have experienced significant productivity gains over the past few decades, construction has lagged behind, struggling to keep pace with the rising demands of a rapidly urbanizing and increasingly interconnected world. (Barriers to Productivity Growth in Construction, McKinsey Global Institute, 2017).
This report posits that the construction industry stands at a critical juncture. Traditional approaches to project management, workforce development, and technology adoption are proving inadequate in the face of escalating challenges. New building regulations, while intended to improve safety, sustainability, and performance, often add complexity and cost to projects. The confluence of these factors necessitates a fundamental re-evaluation of industry practices and a proactive embrace of innovation to ensure its continued relevance and contribution to global development.
Beyond the immediate impact of regulatory changes, this research aims to provide a holistic understanding of the forces reshaping the construction landscape. We examine the underlying drivers of these challenges and explore the potential solutions that will enable builders and construction firms to thrive in the 21st century.
Many thanks to our sponsor Focus 360 Energy who helped us prepare this research report.
2. Core Challenges Facing the Construction Industry
This section provides an in-depth analysis of the primary challenges currently affecting the construction industry, moving beyond the surface-level impact of new regulations to address the systemic issues hindering progress.
2.1 The Looming Skills Gap
A persistent and widening skills gap represents a significant obstacle to the growth and efficiency of the construction industry. This gap encompasses a shortage of both skilled tradespeople (e.g., carpenters, electricians, plumbers) and professionals with expertise in areas such as project management, BIM (Building Information Modeling), and sustainable design. Several factors contribute to this skills shortage. Firstly, there is a negative perception of the construction industry among younger generations, who often view it as physically demanding, lacking in career advancement opportunities, and technologically backward. Secondly, many vocational training programs have suffered from underfunding and a lack of alignment with industry needs. Finally, the aging workforce and the impending retirement of experienced tradespeople are exacerbating the skills gap, leading to a loss of valuable knowledge and expertise.
The consequences of this skills gap are far-reaching. It leads to increased labor costs, project delays, and a decline in the quality of workmanship. Furthermore, it hinders the adoption of new technologies and innovative building practices, as firms struggle to find workers with the necessary skills to implement them. Addressing this challenge requires a concerted effort from industry stakeholders, including governments, educational institutions, and construction firms, to promote the industry as a viable and rewarding career path, invest in training programs, and foster a culture of lifelong learning.
2.2 The Volatility of Material Costs and Supply Chains
Construction projects are inherently vulnerable to fluctuations in material costs and disruptions in supply chains. The prices of essential materials such as steel, concrete, lumber, and copper can be highly volatile, influenced by factors such as global demand, trade policies, and geopolitical events. Supply chain disruptions, caused by natural disasters, political instability, or logistical bottlenecks, can further exacerbate these problems, leading to project delays and cost overruns. The COVID-19 pandemic, for instance, exposed the fragility of global supply chains, causing widespread material shortages and price spikes that significantly impacted the construction industry.
Managing material costs and supply chain risks requires a proactive and strategic approach. This includes diversifying sourcing strategies, developing long-term relationships with suppliers, and utilizing technology to improve supply chain visibility and transparency. Construction firms should also consider incorporating risk management techniques into their project planning processes, such as contingency budgeting and the use of price escalation clauses in contracts.
2.3 Increasing Project Complexity and Regulatory Burden
Modern construction projects are becoming increasingly complex, driven by factors such as the integration of advanced technologies, the growing demand for sustainable building practices, and the proliferation of building regulations. These regulations, while intended to improve safety, energy efficiency, and environmental performance, often add complexity and cost to projects, requiring builders to navigate a maze of permits, inspections, and compliance requirements. The complexity of modern buildings, especially those incorporating smart technologies and sustainable design features, demands a higher level of technical expertise and collaboration among different stakeholders.
Managing project complexity and navigating the regulatory landscape requires a collaborative and integrated approach. This includes the use of BIM to improve project coordination and communication, the adoption of lean construction principles to streamline processes and reduce waste, and the engagement of experienced consultants to provide guidance on regulatory compliance. Furthermore, governments should strive to simplify and harmonize building regulations to reduce the burden on builders and promote innovation.
2.4 The Imperative for Sustainable Practices
The construction industry is a significant contributor to global greenhouse gas emissions and resource depletion. Buildings account for a substantial portion of global energy consumption and waste generation. As awareness of climate change and environmental sustainability grows, there is increasing pressure on the construction industry to adopt more sustainable practices. This includes reducing energy consumption in buildings, using recycled and renewable materials, minimizing construction waste, and promoting water conservation. The demand for green buildings and sustainable infrastructure is growing rapidly, driven by both regulatory requirements and consumer preferences. Builders who fail to embrace sustainable practices risk becoming less competitive and facing increasing regulatory scrutiny.
Adopting sustainable practices requires a fundamental shift in mindset and a commitment to innovation. This includes investing in energy-efficient technologies, using sustainable materials, implementing waste reduction strategies, and promoting water conservation. Construction firms should also consider pursuing green building certifications, such as LEED (Leadership in Energy and Environmental Design) or BREEAM (Building Research Establishment Environmental Assessment Method), to demonstrate their commitment to sustainability and gain a competitive advantage.
2.5 The Slow Pace of Technology Adoption
Despite the rapid advancements in technology, the construction industry has been slow to adopt new technologies compared to other sectors. While industries like manufacturing and finance have embraced automation, data analytics, and artificial intelligence (AI), construction has largely relied on traditional methods. This slow pace of technology adoption has contributed to the industry’s low productivity growth and its struggle to keep pace with rising demands.
However, there is growing recognition of the potential of technology to transform the construction industry. Emerging technologies such as BIM, drones, 3D printing, robotics, and AI offer the potential to improve project efficiency, reduce costs, enhance safety, and promote sustainability. For example, BIM can improve project coordination and communication, drones can be used for site monitoring and inspection, 3D printing can accelerate construction timelines, robotics can automate repetitive tasks, and AI can be used to optimize project scheduling and resource allocation. Embracing these technologies is crucial for construction firms to remain competitive and meet the challenges of the 21st century. This transition also requires overcoming resistance to change, investing in training programs, and fostering a culture of innovation.
Many thanks to our sponsor Focus 360 Energy who helped us prepare this research report.
3. Adaptive Strategies for Builders: Embracing Change and Innovation
Faced with these multifaceted challenges, builders and construction firms must adopt proactive strategies to adapt and thrive. This section explores the key adaptive strategies that can help the industry overcome these obstacles.
3.1 Investing in Workforce Development and Training
Addressing the skills gap requires a sustained and strategic investment in workforce development and training. This includes promoting construction careers to young people, providing apprenticeship programs, and offering continuing education opportunities for existing workers. Construction firms should also partner with educational institutions to develop training programs that are aligned with industry needs. Furthermore, they should invest in training their employees on new technologies and innovative building practices. Creating a culture of lifelong learning is essential for ensuring that the workforce has the skills necessary to meet the challenges of the future. Specific strategies include:
- Enhanced Apprenticeship Programs: Expanding and modernizing apprenticeship programs to provide hands-on training and mentorship opportunities for aspiring tradespeople.
- Industry-Academia Partnerships: Collaborating with universities and vocational schools to develop curriculum that aligns with industry needs and prepares students for the workforce.
- Skills Certification Programs: Establishing standardized skills certification programs to ensure that workers possess the necessary knowledge and skills to perform their jobs safely and effectively.
- Technology Training: Providing training on new technologies such as BIM, drones, 3D printing, and robotics to enable workers to leverage these tools to improve project efficiency and safety.
3.2 Embracing Technology and Digital Transformation
Technology holds the key to unlocking significant improvements in productivity, efficiency, and sustainability in the construction industry. Builders should embrace digital transformation by adopting technologies such as BIM, drones, 3D printing, robotics, and AI. These technologies can be used to improve project coordination, reduce costs, enhance safety, and promote sustainability. It’s also important to integrate existing technologies such as project management platforms. The following steps are crucial for successful technology adoption:
- Develop a Digital Transformation Strategy: Define clear goals and objectives for technology adoption and develop a roadmap for implementing new technologies.
- Invest in Infrastructure and Training: Provide the necessary infrastructure and training to support the use of new technologies.
- Promote a Culture of Innovation: Foster a culture of experimentation and innovation to encourage employees to explore new technologies and find creative solutions to challenges.
- Data-Driven Decision Making: Using data analytics to gather performance data.
3.3 Optimizing Supply Chains and Logistics
Managing material costs and supply chain risks requires a strategic and proactive approach. Builders should diversify sourcing strategies, develop long-term relationships with suppliers, and utilize technology to improve supply chain visibility and transparency. They should also consider incorporating risk management techniques into their project planning processes, such as contingency budgeting and the use of price escalation clauses in contracts. Key strategies include:
- Diversifying Sourcing: Sourcing materials from multiple suppliers to reduce reliance on any single source.
- Building Strong Supplier Relationships: Establishing long-term relationships with key suppliers to ensure reliable access to materials and competitive pricing.
- Improving Supply Chain Visibility: Utilizing technology to track materials throughout the supply chain and identify potential disruptions.
- Implementing Risk Management Strategies: Incorporating risk management techniques into project planning to mitigate the impact of supply chain disruptions.
3.4 Fostering Collaboration and Communication
Effective collaboration and communication are essential for the success of complex construction projects. Builders should foster a culture of collaboration by promoting open communication, encouraging teamwork, and utilizing technology to improve project coordination. This includes using BIM to improve project visualization and communication, implementing project management software to track progress and manage tasks, and holding regular team meetings to discuss challenges and share information. Using techniques such as Integrated Project Delivery(IPD) may also be helpful. Some specific steps include:
- Implementing BIM: Using BIM to create a shared digital model of the project that can be accessed by all stakeholders.
- Utilizing Project Management Software: Implementing project management software to track progress, manage tasks, and facilitate communication among team members.
- Holding Regular Team Meetings: Conducting regular team meetings to discuss challenges, share information, and coordinate activities.
3.5 Embracing Sustainable Building Practices
The demand for green buildings and sustainable infrastructure is growing rapidly. Builders should embrace sustainable building practices to reduce their environmental impact, improve energy efficiency, and meet the growing demand for green buildings. This includes using recycled and renewable materials, minimizing construction waste, and promoting water conservation. It’s also important to be aware of any new green standards. Key initiatives include:
- Using Recycled and Renewable Materials: Utilizing recycled and renewable materials such as recycled steel, reclaimed wood, and bamboo.
- Minimizing Construction Waste: Implementing waste reduction strategies such as prefabrication, deconstruction, and material reuse.
- Promoting Water Conservation: Implementing water conservation measures such as rainwater harvesting, greywater recycling, and low-flow fixtures.
- Pursuing Green Building Certifications: Obtaining green building certifications such as LEED or BREEAM to demonstrate a commitment to sustainability.
Many thanks to our sponsor Focus 360 Energy who helped us prepare this research report.
4. Case Studies: Successful Adaptation in the Construction Industry
This section presents case studies of construction firms that have successfully adapted to the challenges facing the industry by embracing innovation and implementing the strategies discussed above. (Due to limitations in accessing specific real-time case studies, these are illustrative examples based on documented industry trends and best practices.)
4.1 Case Study 1: Gammon Construction – Digital Transformation and Efficiency Gains (Illustrative)
Gammon Construction, a leading construction company in Asia, has been recognized for its innovative use of technology to improve project efficiency and safety. They have implemented a comprehensive digital transformation strategy that includes the use of BIM, drones, and AI. For example, they use BIM to create a shared digital model of their projects, which allows them to identify and resolve clashes before construction begins, reducing rework and improving project coordination. They also use drones to monitor construction sites and collect data, which they use to track progress and identify potential safety hazards. Furthermore, they have implemented AI-powered systems to optimize project scheduling and resource allocation, reducing costs and improving project timelines.
4.2 Case Study 2: Skanska – Sustainable Building Practices and Green Construction (Illustrative)
Skanska, a global construction and development company, is a leader in sustainable building practices and green construction. They have committed to reducing their carbon footprint and building more sustainable buildings. They have implemented a comprehensive sustainability strategy that includes the use of recycled and renewable materials, the minimization of construction waste, and the promotion of water conservation. For example, they have built several LEED-certified buildings, demonstrating their commitment to sustainability. They also work with their clients to develop sustainable building designs and implement energy-efficient technologies. Skanska’s commitment to sustainability has not only reduced their environmental impact but has also given them a competitive advantage in the marketplace.
4.3 Case Study 3: Katerra (Historical – Illustrative Lessons Learned) – Modular Construction and Technology Integration (Illustrative)
While Katerra ultimately faced financial difficulties, their initial vision provides valuable lessons for the industry. They aimed to revolutionize the construction industry by vertically integrating design, manufacturing, and construction processes. Katerra invested heavily in technology, including advanced manufacturing facilities and a digital platform for project management. They focused on modular construction, which allowed them to prefabricate building components in a factory and then assemble them on-site, reducing construction time and costs. While their business model proved unsustainable in its execution, Katerra highlighted the potential of modular construction and technology integration to transform the construction industry. Key lessons learned include the importance of realistic scaling strategies, strong financial management, and a deep understanding of the complexities of the construction industry.
Many thanks to our sponsor Focus 360 Energy who helped us prepare this research report.
5. The Impact of Global Economic Trends and Geopolitical Instability
The construction industry is inextricably linked to the global economy and is therefore susceptible to economic downturns, fluctuations in interest rates, and changes in government spending on infrastructure projects. Geopolitical instability, such as trade wars, political conflicts, and social unrest, can also disrupt supply chains, increase material costs, and create uncertainty in the market. The COVID-19 pandemic, for example, had a profound impact on the construction industry, causing widespread project delays, material shortages, and labor shortages. Builders need to be aware of these global trends and geopolitical risks and develop strategies to mitigate their impact on their businesses. This includes diversifying their markets, managing their financial risks, and developing contingency plans to deal with unforeseen events.
Moreover, the increasing demand for resilient infrastructure, capable of withstanding the impacts of climate change and natural disasters, is reshaping the construction landscape. This demand requires builders to incorporate resilience considerations into their project designs and use materials and construction techniques that can withstand extreme weather events, such as floods, hurricanes, and earthquakes. The construction industry will play a critical role in building a more resilient and sustainable future.
Many thanks to our sponsor Focus 360 Energy who helped us prepare this research report.
6. Conclusion: Navigating the Future of Construction
The construction industry is undergoing a period of rapid change, driven by a confluence of factors including skills shortages, rising costs, increasing project complexity, the imperative for sustainable practices, and the disruptive potential of emerging technologies. To thrive in this evolving landscape, builders must embrace innovation, invest in workforce development, adopt new technologies, optimize their supply chains, foster collaboration, and embrace sustainable building practices. Furthermore, they need to be aware of global economic trends and geopolitical risks and develop strategies to mitigate their impact on their businesses. The future of the construction industry will be shaped by those who are willing to adapt, innovate, and embrace change. The industry must collectively address these challenges to remain a vital engine of economic growth and contribute to building a more resilient, efficient, and sustainable world.
Many thanks to our sponsor Focus 360 Energy who helped us prepare this research report.
References
- Barriers to Productivity Growth in Construction, McKinsey Global Institute, 2017.
- Building Information Modeling (BIM): A Technology Overview, National Institute of Standards and Technology (NIST), 2020.
- Construction Industry Research and Information Association (CIRIA).
- Construction Skills Network (CSN) Forecasts.
- Leadership in Energy and Environmental Design (LEED).
- Building Research Establishment Environmental Assessment Method (BREEAM).
- The Future of Construction, World Economic Forum, 2016.
- Various publications from industry-specific news outlets and research firms (e.g., Construction Dive, Engineering News-Record (ENR)).
Sustainable practices, eh? So, are we talking about buildings that generate their own power and compost toilets in every office? Asking for a friend who’s *really* committed to going off-grid, one skyscraper at a time.
Great question! While complete off-grid skyscrapers are still a ways off, the industry is definitely exploring innovative solutions like on-site renewable energy generation and advanced waste management systems. It’s exciting to see the growing commitment to sustainable construction, even in large-scale projects. Let’s keep pushing the boundaries of what’s possible!
Editor: FocusNews.Uk
Thank you to our Sponsor Focus 360 Energy
Given the slow pace of technology adoption in construction, what incentives beyond immediate cost savings might encourage firms to invest in emerging technologies like AI and robotics? Could standardization of data formats across projects accelerate this adoption?
That’s a really insightful question! Beyond cost savings, I think demonstrating a competitive advantage through increased efficiency and improved project outcomes could be a strong incentive. Standardized data formats would definitely help unlock the full potential of AI and robotics by facilitating seamless data integration across projects. What are your thoughts on government incentives to promote technology adoption?
Editor: FocusNews.Uk
Thank you to our Sponsor Focus 360 Energy
Skills gap, eh? Does this mean my dreams of replacing bricklayers with highly trained squirrels wielding miniature trowels are further from reality than I thought? Asking for a friend… who has a *very* specific business plan.
That’s a hilarious vision! While squirrel bricklayers might be a stretch, the skills gap *is* pushing us towards more creative solutions. Perhaps we can explore robotics to handle repetitive tasks, freeing up skilled workers for more complex aspects of the build? What innovative solutions have you seen?
Editor: FocusNews.Uk
Thank you to our Sponsor Focus 360 Energy
Skills gap indeed! If robots *are* taking over the repetitive tasks, can we train them to argue with the client about budget creep too? Asking for a project manager… who’s tired of being the bad guy.
That’s a fantastic point! Project managers definitely deserve some backup. Imagine AI negotiation modules that can leverage data to justify costs and manage client expectations. This could free up PMs to focus on more strategic aspects of projects. What are your thoughts on AI-driven project management tools?
Editor: FocusNews.Uk
Thank you to our Sponsor Focus 360 Energy
Skills gap, eh? So if I train my cat in BIM, could I bill clients for *purr*-formance-based design? Asking for a friend… who really needs to reduce their carbon paw-print.