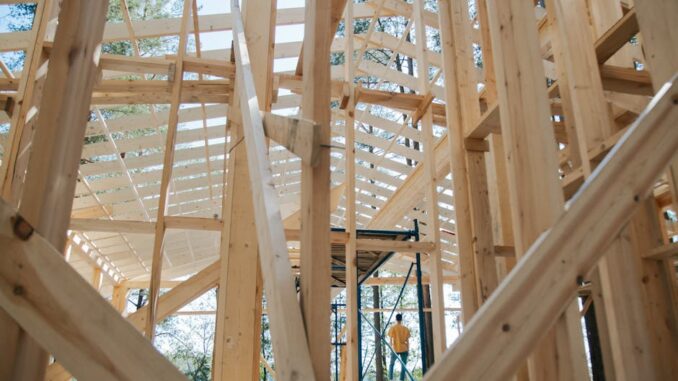
Navigating the UK’s Construction Landscape: A Deep Dive into Escalating Homebuilding Costs by 2030
The UK’s homebuilding sector, a cornerstone of its economy and social fabric, stands on the cusp of a significant — and potentially challenging — transformation. We’re looking at a projected 12% surge in building costs by the end of this decade, a forecast that really demands our immediate attention, doesn’t it? This isn’t just some abstract number; it’s a tangible threat to housing affordability and the viability of countless projects, casting a long shadow over the industry.
This isn’t just about a slight bump; it’s a fundamental shift, prompting serious discussions about strategic resilience. The Building Cost Information Service (BCIS) issued this stark warning, underscoring an imperative need for proactive, almost prescient, planning within the entire construction ecosystem. It’s a wake-up call, frankly, for everyone from major developers to independent builders, even those undertaking extensive home renovations.
Focus360 Energy: property compliance services – pre-planning to post-construction. Learn more.
The Dual Pressure Points: Labour and Material Costs
When we dissect this anticipated cost hike, two primary culprits emerge, exerting considerable upward pressure: labour and materials. BCIS projects labour costs alone will climb an eye-watering 18%, while material costs are set to jump 15% over the same period. This isn’t just inflation; it’s a complex interplay of systemic issues that demand closer scrutiny.
The Squeeze on Labour: Beyond Just Wages
Let’s talk about labour first because, honestly, it’s a multifaceted beast. The projected 18% increase is largely attributable to two main government policy levers: National Insurance (NI) contributions and the National Living Wage (NLW). Employers will soon face a higher National Insurance rate, moving from 13.8% to 15%, and, crucially, the contribution threshold is dropping. What does this mean in real terms? It means employers are paying more NI on a larger portion of their employees’ earnings. It’s a double whammy, further squeezing those already tight profit margins.
But it’s not just the government’s hand in your pocket. The NLW has seen consistent, significant increases over recent years, a laudable effort to ensure a fairer wage, no doubt, but one that directly impacts operational overheads. For a builder, this translates to higher wages for every bricklayer, carpenter, and electrician on site, not to mention administrative staff.
Think about it: even if your team is small, say five or six skilled tradespeople, these incremental increases compound. I remember chatting with a friend, Mark, who runs a small firm in Kent. He told me just last month, ‘Look, I want to pay my lads well, I really do. But when my NI bill goes up, and I’ve got to pay everyone more because of the NLW, it’s not just a few quid. It’s thousands over a year, and that comes directly out of my ability to invest in new kit or, heaven forbid, take a proper holiday.’ It’s a sentiment you hear echoed across the sector, especially among SMEs.
Beyond these direct financial impositions, there’s a deeper, more systemic issue at play: the widening skills gap. The UK construction industry has grappled with an aging workforce for years, and a perceived lack of new entrants into traditional trades has only exacerbated the problem. Brexit, too, played its part, impacting the free movement of skilled labour from Europe. When demand for skilled hands outstrips supply, guess what happens? Wages are bid up, naturally, making it even harder for firms to find and retain talent. Companies are investing more in apprenticeships and in-house training, which is fantastic for the long-term, but it’s an upfront cost that adds to the pressure now.
Material Meltdown: From Timber to Insulation
Then we turn to materials, slated for a 15% hike. This isn’t just a broad brushstroke; it’s specific commodities like timber, steel, and insulation that are driving this upward trajectory. We saw a brief, almost misleading, dip in material prices in 2023–2024, didn’t we? It felt like a moment of respite, a chance to catch our breath. Well, that seems to be firmly in the rearview mirror now, with prices reversing course sharply.
Why this volatility? It’s a confluence of global factors. Geopolitical tensions, like ongoing conflicts and trade disputes, disrupt supply chains. Energy prices, volatile as ever, directly impact manufacturing costs for everything from steel to cement. Raw material extraction and processing become more expensive. Plus, there’s renewed, if somewhat patchy, demand from large-scale infrastructure projects worldwide, which puts pressure on the availability and pricing of key materials. For instance, the cost of specific types of insulation, critical for meeting new energy efficiency standards, has become particularly unpredictable. You’re not just buying a product; you’re buying into a global risk matrix.
Imagine ordering a significant batch of structural timber, only to find the price has jumped 10% between your quote and the actual delivery date due to unexpected shipping container surcharges or a sudden increase in global demand. It happens. It forces builders to make tough choices, either absorbing the cost, which erodes profit, or passing it on, which makes homes less affordable.
The Double-Edged Sword of Growth: A Stagnation Warning
Here’s a particularly tricky paradox: these escalating costs are occurring against a backdrop of projected 19% growth in new work output. On the surface, growth sounds positive, right? But when costs are spiralling, this growth can actually lead to significant project delays and budget overruns. It’s like trying to run a marathon with weights strapped to your ankles; you’re moving forward, but it’s incredibly taxing.
Dr. David Crosthwaite, the chief economist at BCIS, nailed it when he highlighted the risk of ‘stagflation’ within the sector. Stagflation, for those less familiar, is that nasty economic cocktail of high inflation (rising costs) and stagnant economic growth (slow output). In construction, it means you’re building more, but you’re making less profit on each unit, and projects take longer, tying up capital for extended periods. It’s a recipe for cash flow nightmares and, ultimately, fewer homes being built or a significant increase in their final price.
His advice is clear, almost an industry mantra now: homebuilders and renovators must prepare strategically. What does that look like? It means moving beyond reactive problem-solving. It involves deep financial modeling, running multiple scenario analyses – best case, worst case, and everything in between. It’s about stress-testing your balance sheet against potential delays and cost surges. And critically, it means getting smart about procurement. ‘Lock in material prices early,’ he advises, and frankly, you’d be foolish not to if you have the capital and foresight. This often means forward contracts with suppliers, sometimes even buying and warehousing materials well in advance, which requires capital and space, of course. It’s a calculated risk, but often less risky than waiting for market price fluctuations to bite you.
Staying informed about market trends isn’t just good practice; it’s survival. It means subscribing to industry intelligence, having strong relationships with suppliers who can give you early warnings, and understanding global economic currents. Frankly, in this climate, relying on gut instinct alone isn’t going to cut it anymore.
The Green Imperative: Building Regulations and the Future Homes Standard
As if rising labour and material costs weren’t enough, the UK’s ambitious drive towards a greener, more sustainable future is adding another layer of complexity, and indeed cost, to construction. Recent changes in building regulations aren’t just minor tweaks; they represent a fundamental paradigm shift. The government’s push for ultra-energy-efficient buildings has led to significantly stricter requirements for insulation, heating systems, and overall building performance. And while we all champion the reduction of carbon emissions and improved sustainability, meeting these new standards certainly carries a price tag.
Firms aren’t just swapping out one material for another; they’re investing in more advanced, often more expensive, materials and entirely new technologies. Think about it: enhanced thermal bridging details, superior airtightness membranes, and significantly thicker insulation. These aren’t just minor upgrades; they often require a complete rethink of traditional building practices. For smaller builders, this can be a particular challenge. Do they have the capital to invest in retraining their workforce or buying new, specialised equipment? It’s a genuine concern, isn’t it?
The Future Homes Standard: A Game Changer
Perhaps the most significant regulatory change on the horizon is the Future Homes Standard, set to come into full effect from 2025. This isn’t just about making homes a bit more efficient; it mandates that new homes must be ‘future-proofed’ with low-carbon heating and achieve extraordinarily high levels of energy efficiency. We’re talking about new homes needing to have carbon emissions 75% to 80% lower than those built under current standards. That’s a staggering leap, when you stop to think about it.
What does ‘future-proofed’ actually mean on the ground? It means designing out reliance on fossil fuels. Say goodbye to traditional gas boilers in new builds. Instead, we’re seeing mandates for low-carbon heating solutions like air source heat pumps, ground source heat pumps, and even district heating systems where feasible. It also means exceptionally high levels of fabric efficiency – super-insulated walls, floors, and roofs, triple glazing as standard, and robust ventilation systems that recover heat. For a homeowner, this promises significantly lower energy bills, a huge long-term benefit, but for the builder, it’s an upfront cost that needs careful management.
This isn’t just about putting a heat pump in; it’s about redesigning the entire energy system of a home. It impacts everything from the size of radiator pipes to the electrical infrastructure. And then there’s the skills gap again: do we have enough qualified engineers and installers for these new systems? The manufacturing supply chain for these technologies also needs to scale up dramatically to meet demand, which could, paradoxically, drive prices even higher in the short term. It’s a classic chicken-and-egg scenario, really.
Navigating the Storm: Mitigation Strategies and Innovation
In the face of these formidable challenges, the construction industry isn’t just sitting idly by. Progressive firms are actively adopting sophisticated strategies, not just to mitigate costs, but to fundamentally reshape how homes are built. The goal? To deliver quality homes efficiently, even as the sands shift beneath their feet. It’s about working smarter, not necessarily harder, though frankly, it often involves both.
The Rise of Offsite Construction: Building Smarter, Not Just Faster
One of the most compelling approaches gaining significant traction is the increased use of offsite construction methods, particularly modular construction. Remember when ‘prefabs’ were often synonymous with temporary or lower quality? Well, that perception is rapidly changing. Today’s modular construction is a world away. It involves fabricating entire building components, or even full modules, in a highly controlled factory environment before transporting and assembling them on-site. You might see a crane lifting an entire floor or even a complete apartment module into place. It’s quite a sight, actually.
The benefits are multi-layered. First, there’s the obvious reduction in on-site labour costs. Much of the work shifts to the factory, where automation and streamlined processes are more feasible. Second, construction time dramatically shrinks. Because components are being built concurrently with site preparation, projects can be delivered significantly faster. This means quicker revenue recognition for developers and less exposure to fluctuating market conditions. Furthermore, quality control in a factory setting is far superior to an exposed construction site, leading to fewer defects and less waste. The impact of adverse weather becomes almost negligible, too. You don’t have rain stopping play or wind preventing a crane lift.
Of course, it’s not without its challenges. The initial capital investment for setting up a sophisticated modular factory can be substantial. Logistics become paramount – transporting large modules requires careful planning and specialized equipment. But the long-term benefits in predictability, cost control, and quality assurance are undeniable. We’re seeing more and more housing associations and private developers embracing this, and frankly, I think it’s the future for a significant portion of our housing stock.
Building Information Modelling (BIM): The Digital Blueprint for Efficiency
Another powerful tool in the arsenal of modern construction firms is Building Information Modelling (BIM). If you’re not already using it, you really should be looking into it. BIM isn’t just about 3D models; it’s a collaborative, information-rich process that allows for the creation and management of digital representations of physical and functional characteristics of places. Imagine constructing a building virtually, identifying every potential clash or inefficiency, long before the first shovel hits the ground. That’s BIM in action.
By leveraging BIM, firms can conduct incredibly detailed planning and simulation of construction projects. This helps to identify potential issues – say, a pipe clashing with a structural beam, or an electrical conduit running straight through a ventilation duct – before they morph into expensive, time-consuming problems on site. It reduces waste, minimizes rework, and allows for much more accurate material take-offs, so you’re not over-ordering or under-ordering. It essentially reduces the element of surprise, which, in construction, can often translate directly into budget overruns and delays. It’s a game-changer for project coordination and risk management, really.
Embracing Low-Carbon Heating Solutions: A Regulatory Push
As mentioned earlier, the regulatory push for sustainability means a wholesale shift towards low-carbon heating solutions. These aren’t just ‘nice-to-haves’ anymore; they’re becoming mandatory. The most prominent examples are air source and ground source heat pumps. Air source heat pumps extract heat from the outside air, even in cold temperatures, and transfer it into your home, while ground source systems utilize stable underground temperatures. Both significantly cut down on carbon emissions compared to traditional fossil fuel-based methods.
For builders, this means not only the upfront cost of the unit itself but also significant changes to design and installation practices. Heat pumps operate at lower flow temperatures than gas boilers, often requiring larger radiators or underfloor heating systems. They also need careful sizing and placement to be efficient. This demands new skill sets for plumbers and heating engineers. Similarly, solar thermal systems, which heat water using sunlight, are becoming more common, integrating renewable energy directly into the home’s energy profile. Government incentives, like the Boiler Upgrade Scheme, are designed to smooth this transition, but they don’t cover the full cost, leaving builders and ultimately homeowners, to bear a substantial portion of the investment.
Beyond Technology: The Human Element and Strategic Partnerships
While technology plays a crucial role, the human element remains paramount. Savvy firms are also focusing on:
- Value Engineering: Continuously scrutinizing designs and specifications to find cost efficiencies without compromising quality or performance. Sometimes, a different material or a slightly altered design can save thousands.
- Strategic Procurement: Building stronger, more collaborative relationships with suppliers. This isn’t just about getting the lowest price, but about securing reliable supply chains, negotiating favourable terms, and sometimes even engaging in bulk purchasing agreements or framework contracts to lock in prices over longer periods. You want your suppliers to be partners, not just vendors.
- Upskilling the Workforce: Investing heavily in training programs to equip existing staff with the skills needed for new technologies and methods. This helps alleviate the labour shortage and ensures competence in delivering energy-efficient homes. It’s an investment in your people, and honestly, you can’t put a price on that kind of loyalty and capability.
- Lean Construction Principles: Applying manufacturing principles to construction to reduce waste, optimize workflows, and improve productivity. This means focusing on value creation and eliminating non-value-adding activities on site.
The Road Ahead: Resilience and Innovation as Cornerstones
As the UK construction industry navigates this confluence of rising costs and transformative regulatory changes, early and meticulously strategic planning isn’t just good practice; it’s absolutely imperative for survival and sustained growth. The landscape is fundamentally shifting, and those who remain agile, adaptable, and forward-thinking will be the ones who thrive.
Embracing innovative construction methods like modular building, leveraging advanced technologies such as BIM, and staying relentlessly informed about evolving regulatory frameworks aren’t optional extras anymore. They are core tenets of a resilient business strategy. The industry is effectively being forced to innovate at an unprecedented pace, which, while challenging, also presents enormous opportunities for those willing to seize them. Will it be easy? No, certainly not. But will it forge a stronger, more sustainable, and ultimately more efficient homebuilding sector? I certainly think so, and I’m genuinely optimistic about the long-term prospects, provided we collectively commit to these changes. It’s a journey, not a destination, and we’re all on it together, aren’t we?
References
The projected increase in labour costs, especially considering the skills gap, highlights the urgent need for more robust apprenticeship programs and industry-education partnerships to cultivate the next generation of skilled tradespeople. How can we incentivize more young people to enter these vital professions?
That’s a great point about incentivizing young people! I think highlighting the potential for innovation and technology in construction is key. Many young people might not realize how much the industry is evolving. Showcasing the use of drones, BIM, and sustainable building practices could attract a new generation to these vital and rewarding careers. What other incentives could make a difference?
Editor: FocusNews.Uk
Thank you to our Sponsor Focus 360 Energy
That 12% jump in building costs by 2030? Sounds like a challenge, but also a prime opportunity for construction tech startups! Imagine the solutions we could build to drive costs down. Anyone else thinking ‘construction tech unicorn’ by 2035?
Absolutely! The potential for construction tech startups to address the rising costs is huge. I think AI-driven project management tools could significantly optimize resource allocation and reduce delays. What other innovative technologies do you think have the potential to transform the industry and create the next construction tech unicorn?
Editor: FocusNews.Uk
Thank you to our Sponsor Focus 360 Energy
The discussion on material costs is crucial. How might advancements in material science, such as self-healing concrete or sustainable alternatives to traditional materials, mitigate the projected 15% increase and contribute to a more resilient and eco-friendly construction sector?
That’s a great point about material science! Self-healing concrete and sustainable alternatives offer huge potential. Imagine the long-term cost savings and environmental benefits if we could integrate these into mainstream construction. What innovative material breakthroughs are you most excited about seeing adopted in the industry?
Editor: FocusNews.Uk
Thank you to our Sponsor Focus 360 Energy
That 18% jump in labour costs is a beast! If NI contributions and the NLW are squeezing firms, are we potentially pricing out smaller players? Could this unintentionally lead to a less diverse market, dominated by larger companies who can absorb those costs? Just curious.