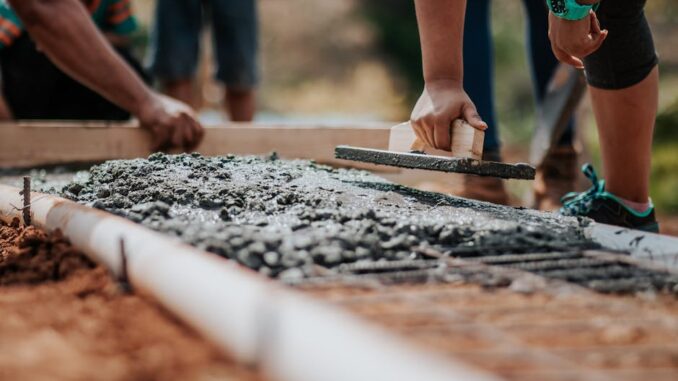
UK Construction: A Phoenix Rising, Yet Navigating a Minefield of Challenges
It’s been quite the rollercoaster for the UK construction sector lately, hasn’t it? If you’ve been following the industry, you’ll feel that undeniable buzz in the air, a sense of cautious optimism. Because, frankly, the numbers are speaking volumes. After a period that felt, at times, like slogging through quicksand, we’re seeing some truly remarkable shifts, a surge in activity that hints at a fundamental re-energising of developer and investor confidence.
Glenigan’s latest June Index, a bellwether for the sector, paints a rather compelling picture. Project starts, those vital first tremors of future building, have shot up by a staggering 49% over the second quarter. Think about that for a moment. Quarter-on-quarter, that’s almost a doubling, and when you stretch the lens out a bit, it represents a solid 25% increase year-on-year. This isn’t just a flicker; it’s a sustained ignition of activity.
Now, let’s unpack where this momentum is truly building. Private housing starts, in particular, are leading the charge, showing an impressive 76% surge quarter-on-quarter. That’s a dramatic rebound, isn’t it? Even more striking, it’s up a substantial 64% compared to June 2024 figures. We’re talking about significant, tangible developments here, like the expansive Sudbury Westlands Heath project, a sprawling undertaking that promises hundreds of new homes, along with a raft of major social housing initiatives popping up across the North West. These aren’t just isolated pockets of growth; they’re substantial anchors of future development, bringing much-needed housing stock to communities.
Focus360 Energy: property compliance services – pre-planning to post-construction. Learn more.
Geographically, some regions are really hitting their stride. The West Midlands, for instance, has reported an astonishing 78% quarterly growth in project starts. And just look at the North West, close behind with a 72% increase. What’s driving this regional dynamism, you might wonder? Often, it’s a confluence of factors: strategic investment in infrastructure, local authority commitment to housing targets, and perhaps a slightly less heated land market allowing for more viable projects. This uptick suggests a powerfully positive outlook for the industry, undoubtedly spurred by renewed demand from a slightly more confident consumer base, and crucially, a noticeable uptick in investor appetite. It’s almost as if the clouds are parting, allowing a bit more sunlight to hit the construction sites.
The Gnawing Ache: A Labour Shortage Crisis
However, and there always seems to be a ‘however’ in this business, doesn’t there? This burgeoning optimism, this palpable sense of forward motion, comes with a rather large asterisk attached. Because beneath the surface of soaring project starts, there’s a deep, gnawing anxiety that simply won’t dissipate: the acute labour shortage plaguing the sector. It’s a problem that feels less like a bump in the road and more like a chasm that needs bridging.
Reports from authoritative bodies like City & Guilds and the Construction Industry Training Board (CITB) paint a stark picture, don’t they? They tell us that a staggering 76% of construction firms are grappling daily with the monumental task of finding, let alone hiring, skilled workers. Think about that for a moment: three-quarters of businesses are actively struggling. And it’s not just a minor shortfall; the industry estimates we need an additional 252,000 workers by 2028 just to keep pace with projected demand. That’s a quarter of a million people, in less than five years. Where will they all come from?
It’s a perplexing paradox, isn’t it? The Office for National Statistics (ONS) might report a national unemployment rate of 4.7%, yet the construction sector continues to echo with the silence of unfilled vacancies. It’s as if the available workforce, for various reasons, simply isn’t equipped or inclined to fill these roles. This shortage isn’t a sudden phenomenon either; it’s a culmination of trends that have been building for years. We’re facing an aging workforce, a generation of highly skilled tradespeople – the master bricklayers, the experienced electricians, the meticulous carpenters – nearing retirement. And critically, there just aren’t enough younger professionals stepping up to fill their boots, let alone embrace the hard hats and hi-vis vests. The perception of construction, for too long, has been one of low-skill, physically demanding work, overlooking the immense innovation and career progression now available.
Sure, the government has pledged a substantial £600 million in skills funding, a promise aimed at training 60,000 workers by 2029. On paper, it sounds like a robust response. Yet, the implementation of these initiatives has, frustratingly, felt slow. One can’t help but wonder if the sheer pace of the industry’s need will outstrip the training pipeline’s capacity. Will these new recruits be ready, with the necessary skills, precisely when the industry needs them most? It’s a legitimate question, and one that keeps many a project manager awake at night.
We need more than just general funding. We need targeted interventions for specific, critical skills. Think about the demand for groundworkers, the absolute bedrock of any project, or the scarcity of experienced M&E engineers who bring a building to life. Digital modellers too, they’re becoming gold dust, as the industry embraces more sophisticated technologies. It’s a complex web of shortages, and it really demands a multi-pronged approach, not just a single, broad stroke of funding.
Easing the Burden: Government Reforms for SMEs
In a sector where giants often dominate the headlines, it’s easy to forget the immense contribution of small and medium-sized builders. They are, after all, the lifeblood of local economies, responsible for a huge proportion of the housing stock and often the most innovative in adapting to local needs. Recognizing their pivotal role, the UK government is thankfully now considering significant reforms aimed at easing the regulatory burden on these crucial players.
Proposed changes are quite specific, aiming to cut through some of the red tape that has historically stifled smaller firms. You’re looking at potential exemptions from certain environmental regulations, which, while vital for ecological protection, can become incredibly complex and costly for smaller developers with limited in-house expertise. Think about the myriad assessments, the lengthy consultations, the sheer volume of paperwork that can hold up a small development for months, even years. What’s more, there’s talk of exempting them from the post-Grenfell safety levy. While the levy is an essential mechanism for funding building safety remediation, its blanket application can disproportionately impact the financial viability of smaller projects, making it harder for them to get off the ground.
These measures are undoubtedly part of the government’s broader, ambitious goal: to construct a formidable 1.5 million homes in England by 2029. It’s a target that simply won’t be met without unlocking the latent capacity of the SME sector. The hope is that by streamlining the planning process and accelerating project timelines, these smaller builders can get on with what they do best: building homes, faster and more efficiently.
Industry groups like Propertymark have, quite rightly, voiced their support for these initiatives. They understand the mechanics of the market. However, and this is a critical point, they emphasize that these changes are just the beginning. The real transformative impact will only be felt if there are further, more comprehensive planning reforms. We’re talking about simplifying the entire planning system, making it more predictable, and less prone to costly delays. Crucially, there’s also an urgent need for significant investment in local authority resources. Because, let’s be honest, even with streamlined regulations, if local planning departments are understaffed, overwhelmed, and under-resourced, the bottlenecks will simply shift, won’t they? Smaller developers, who often lack the armies of consultants available to larger firms, rely heavily on efficient and accessible local planning services. Without that support, these proposed exemptions, while welcome, might not deliver their full intended benefit.
Bricks and Beyond: Navigating Material Constraints
Just when you thought the labour issue was enough to contend with, the construction industry continues to grapple with another persistent headache: material shortages. And, perhaps surprisingly for some, a primary culprit often highlighted in the current climate is the humble brick. It’s a foundational element of British housing, synonymous with tradition and durability, but its availability has become a significant choke point.
Our domestic UK brickmakers, for all their industrious efforts, currently possess the capacity to support only around 250,000 new homes per year. That’s a quarter of a million homes, which sounds impressive, I know. But when you stack it against the government’s ambitious 300,000-home annual target, you instantly spot the deficit. That’s a 50,000-home gap that bricks alone simply can’t fill. This isn’t just a minor inconvenience; it’s a fundamental supply-demand imbalance, exacerbated by increased energy costs for firing kilns, supply chain disruptions from global events, and a sudden surge in demand as the market reawakens.
So, what’s a developer to do when traditional materials are scarce or prohibitively expensive? Ingenuity, as ever, prevails. Developers are increasingly turning to alternative construction methods to bridge this gap. Timber-frame construction, for instance, is seeing a significant resurgence. It’s not a new concept by any means, but modern engineered timber products offer incredible strength, speed of construction, and a much lower carbon footprint than traditional masonry. Similarly, offsite construction methods, including modular and volumetric building, are gaining serious traction. Think about entire sections of a building, or even whole homes, being manufactured in controlled factory environments, then transported to site for rapid assembly. It’s almost like a giant LEGO set, but for houses.
These approaches aren’t just practical solutions to material shortages; they bring a host of other compelling benefits. For one, they can dramatically reduce construction waste. Factory settings allow for precision cutting and material optimization that’s difficult to achieve on a muddy, open site. This also contributes positively to the UK’s broader sustainability goals, pushing us closer to net-zero targets. Furthermore, the speed of construction is often phenomenal, shaving weeks, sometimes months, off project timelines. And, crucially, they offer enhanced quality control, as components are built in controlled environments, free from the vagaries of unpredictable British weather. You can’t argue with that, can you?
That said, it isn’t an entirely smooth transition. There are still hurdles: initial investment in new manufacturing facilities, overcoming traditional mindsets within the industry, and sometimes, navigating regulatory frameworks that haven’t quite caught up with these innovative methods. But the momentum is undeniable; these aren’t just stop-gap measures, they’re increasingly becoming preferred methodologies for forward-thinking developers.
The Digital Horizon: Tech as a Game Changer
If ever there was a time for technology to step up and deliver, it’s now. The construction industry, often seen as a laggard in digital adoption compared to manufacturing or finance, is finally, and with considerable gusto, embracing technological innovation. It’s playing a pivotal role, not just in addressing the gnawing labour shortages but also in fundamentally reshaping how projects are planned, executed, and managed for improved efficiency.
Building Information Modelling (BIM) technology, for example, isn’t just a buzzword anymore; it’s becoming the backbone of modern construction. We’re seeing its adoption on a grand scale, with a remarkable 73% of UK companies now utilizing BIM. And the sector is actively pushing towards Level 3 BIM compliance by 2025. What does that mean for you, the developer, the project manager? It means an integrated, collaborative, real-time digital representation of every aspect of a building’s lifecycle. Think fewer errors, better cost control, enhanced communication between disparate teams, and a smoother flow from design to construction to facility management. It’s a game-changer for reducing rework and improving predictability.
Beyond BIM, the entire construction technology, or ‘ConTech’, ecosystem is absolutely flourishing. We’re not talking about a handful of niche players; there are over 1,000 startups now populating this dynamic space, each bringing innovative solutions to the table. From AI-powered predictive analytics for risk management to sophisticated project management software, the landscape is incredibly vibrant. And the robotics market? That’s truly exploding. It’s expected to exceed £600 million by 2029 – a mind-boggling 360% increase over the decade. We’re witnessing a revolution in automation on site.
Artificial intelligence and automation are no longer futuristic concepts; they’re becoming mainstream solutions, deployed on major projects across the country. Remember those images of robots laying bricks? They’re real. We’re talking about advanced robotics like SAM (Semi-Automated Mason) bricklaying systems and Hadrian X robots, capable of building entire house shells in a mere three days. Imagine the productivity gains! But it’s not just about bricklaying. Drones are surveying sites, monitoring progress, and even identifying potential issues from the air with unprecedented speed and accuracy. AI algorithms are optimizing delivery schedules, predicting material needs, and even analysing complex data to prevent costly delays before they even occur. It’s quite something to behold, isn’t it?
These technologies aren’t just fascinating gadgets; they are fundamentally enhancing productivity, improving safety, and critically, mitigating the impact of the skilled labour shortage. They augment human capabilities, allowing the existing workforce to be more efficient and focus on higher-value tasks. While some worry about job displacement, the reality is more nuanced: these tools are creating new roles and demanding new skills, transforming the construction site into a smart, interconnected environment.
Shaping the Future: Policy and Sustainability Mandates
Perhaps the most profound forces shaping the construction landscape right now are not market whims, but robust, legally binding policy changes. The UK isn’t just gently nudging the industry towards sustainability; it’s mandating a radical transformation, particularly with the advent of the Future Homes Standard and the Future Buildings Standard.
Let’s talk about the Future Homes Standard, set to kick in with full force in 2025. This isn’t some minor tweak; it’s a seismic shift for residential development. It mandates a truly ambitious 75-80% reduction in carbon emissions compared to 2013 standards for all new homes. How will this be achieved? Primarily through the widespread adoption of low-carbon heating systems – think air source heat pumps and ground source heat pumps becoming the norm, rather than gas boilers – and significantly enhanced thermal performance. We’re talking about vastly improved insulation, perhaps even triple glazing becoming standard, and airtight building envelopes that retain heat like never before. For developers, this means a complete re-think of design, material sourcing, and construction methodologies. It’s a challenge, yes, but also an immense opportunity for innovation in sustainable building practices.
Simultaneously, the Future Buildings Standard mirrors this ambition for non-domestic buildings. The goal here is to achieve ‘zero-carbon ready’ status, with stringent requirements for a 27% carbon reduction. Again, this means a fundamental shift in how commercial, industrial, and public buildings are designed and constructed. Developers and architects must now integrate advanced energy efficiency measures, renewable energy generation systems, and low-carbon materials from the outset of any project. These standards are not just about compliance; they are a clear directive, influencing every stage of project planning and execution, pushing the industry towards a fundamentally more sustainable future.
These policy changes are the government’s answer to its legally binding net-zero targets. They’re part of a much larger, global movement to combat climate change, and the built environment, as a significant contributor to carbon emissions, simply has to play its part. The challenges these standards pose are considerable: the upfront costs of new technologies, the need to upskill the workforce in installing and maintaining these systems, and ensuring a robust supply chain for low-carbon components. But the opportunities are equally vast – driving innovation, creating new markets for sustainable products and services, and ultimately delivering homes and buildings that are cheaper to run for occupants and better for the planet in the long term. It’s a win-win, isn’t it, if we get it right?
Looking Ahead: A Path Paved with Potential and Pitfalls
So, there you have it. The UK construction industry, a vital engine of the national economy, finds itself at a fascinating crossroads. On one hand, we’re witnessing an undeniable surge in project starts, a vibrant reaffirmation of confidence that’s palpable across regions and segments. The sheer volume of new developments breaking ground is truly encouraging, indicating a robust rebound from previous market uncertainties. It’s almost as if the industry has taken a deep breath and is now exhaling a burst of activity.
Yet, this forward momentum is inextricably linked to, and indeed tempered by, a series of significant, stubborn challenges. The persistent labour shortages, the gnawing absence of skilled hands that echo across building sites, remain a critical bottleneck. And let’s not forget the material constraints, particularly that humble brick, which reveal underlying vulnerabilities in our supply chains. Then there’s the monumental task of adapting to stringent new building regulations, which, while absolutely necessary for our collective future, demand radical shifts in design, materials, and processes.
Can the government’s policy initiatives, coupled with the industry’s increasingly eager embrace of technological innovations, truly pave a smoother path forward? There’s certainly immense promise here. Targeted funding, regulatory easing for SMEs, and the transformative power of BIM, robotics, and AI, all point towards a future where construction is smarter, faster, and more sustainable. These aren’t just theoretical possibilities; they’re already being deployed, proving their worth on the ground.
However, the ultimate effectiveness of these measures will hinge on a few crucial elements. Timely implementation, for one, is paramount; we can’t afford to dither when the industry is moving at such a pace. Furthermore, the industry’s innate ability to adapt, to shed some of its more traditional skin and wholeheartedly embrace the evolving regulatory and market landscape, will be tested. It’s a demanding journey, no doubt, but one filled with immense potential. Will the UK construction sector not only meet its ambitious housing targets but also emerge as a global leader in sustainable, technologically advanced building? That, my friends, is the compelling question we’ll all be watching unfold. It’s going to be quite a ride.
The surge in private housing starts is certainly encouraging. Given the material constraints, particularly with brick availability, how do you see the increased adoption of alternative construction methods like timber-frame impacting long-term housing affordability and design aesthetics in the UK?
That’s a great point about timber-frame and aesthetics! It’s true, the design possibilities with modern timber are incredible. I think we’ll see some really innovative and beautiful housing coming through as architects and developers explore these options. Plus, the sustainability benefits can also add value in the long run!
Editor: FocusNews.Uk
Thank you to our Sponsor Focus 360 Energy
A 76% surge in private housing starts? Maybe I should finally invest in that LEGO set… I mean, modular home. Any recommendations for a good architect who specializes in snap-together construction? Just kidding… mostly.
That’s a great point! The modular home market is definitely gaining traction. While I can’t recommend a *snap-together* architect specifically, there are some fantastic firms specializing in modern methods of construction and modular design. They are embracing that Lego-esque approach to building! It’s exciting to see.
Editor: FocusNews.Uk
Thank you to our Sponsor Focus 360 Energy