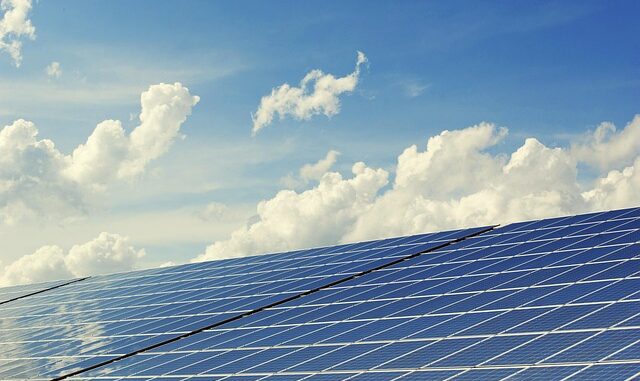
Abstract
The performance gap, a critical and pervasive challenge in the built environment, represents the significant and often disconcerting disparity between a building’s predicted energy consumption at the design stage and its actual energy usage once constructed and occupied. This extensive divergence profoundly impedes global efforts to achieve crucial energy efficiency targets, mitigate climate change, and realize broader sustainability objectives. This comprehensive research paper undertakes an in-depth, multifaceted examination of the root causes contributing to the performance gap. These include, but are not limited to, overly optimistic design assumptions, pervasive construction quality deficiencies, shortcomings in the commissioning process, and the often-unpredictable dynamics of occupant behavior. Furthermore, the paper thoroughly explores a range of advanced diagnostic tools, sophisticated continuous monitoring systems, robust post-occupancy evaluation (POE) methodologies, and strategic approaches for effective handover processes alongside proactive occupant engagement. By systematically dissecting these interdependent aspects, this paper aims to furnish a granular and holistic understanding of the performance gap, culminating in the proposition of actionable, integrated solutions designed to effectively bridge this persistent discrepancy and foster genuinely sustainable building performance.
Many thanks to our sponsor Focus 360 Energy who helped us prepare this research report.
1. Introduction
The phenomenon widely recognized as the performance gap in building energy consumption has emerged as a central concern within the architecture, engineering, and construction (AEC) industry and among policymakers focused on sustainability. It denotes a consistent and often substantial discrepancy where the operational energy use of a building significantly outstrips the energy consumption forecasts derived during its design phase. This pervasive issue is not merely an academic curiosity; it possesses profound practical implications, directly undermining the efficacy of strategies aimed at reducing overall energy demand and, consequently, mitigating greenhouse gas emissions associated with the built environment. As urban populations continue to swell and global energy demand escalates, the imperative to construct and operate buildings that are genuinely energy-efficient becomes increasingly critical. The persistent presence of the performance gap, however, complicates and often frustrates these endeavors, leading to higher operational costs, increased carbon footprints, and a diminished return on investment in green building initiatives. (buildpass.co.uk)
Historically, the focus within building design and construction was predominantly on structural integrity, functionality, and aesthetic appeal. Energy performance, while always a factor, gained prominence primarily in response to the energy crises of the 1970s and subsequent environmental awareness movements. The advent of sophisticated building energy modeling (BEM) tools in recent decades promised a new era of precision in predicting energy performance. These tools, however, largely operate on idealized assumptions, creating an inherent vulnerability to the realities of complex construction processes, intricate system operations, and highly variable human interactions. The journey from a conceptual design model to a functioning, occupied building is fraught with potential pitfalls where deviations from the original intent can accumulate, culminating in the observable performance gap. Understanding the intricate, interconnected underlying causes of this gap is not merely a theoretical exercise; it is an indispensable prerequisite for developing robust, pragmatic, and effective strategies to mitigate its impact and steer the built environment towards a truly sustainable future.
Many thanks to our sponsor Focus 360 Energy who helped us prepare this research report.
2. Causes of the Performance Gap
The performance gap is a multifaceted problem, rarely attributable to a single cause. Instead, it typically arises from a complex interplay of issues spanning the entire building lifecycle, from initial conceptualization through design, construction, commissioning, and ultimately, occupation and ongoing operation. Delving into each of these contributing factors provides a clearer pathway toward comprehensive solutions.
2.1 Optimistic Design Assumptions
During the initial design phase, the energy modeling process, while highly advanced, often relies upon a suite of idealized assumptions that, in practice, rarely align perfectly with real-world conditions. Building energy models (BEMs) are powerful computational tools, yet their outputs are intrinsically linked to the quality and realism of their inputs. These inputs frequently involve generalized or simplified representations of building characteristics, operational parameters, occupant behavior, and environmental conditions, leading to an inherent overestimation of anticipated energy efficiency. (frontiersin.org)
One significant area of optimism lies in the definition of internal loads. Design models often use averaged or static values for occupant density, lighting power density, and plug load density. In reality, these parameters fluctuate significantly based on actual occupancy patterns, individual user preferences for lighting levels, and the proliferation of various electronic devices. For instance, a design might assume a diversity factor for plug loads that is too low, or it might not account for personal heaters, fans, or multiple monitors per workstation. Similarly, assumptions about the optimal operation of heating, ventilation, and air conditioning (HVAC) systems are frequently made. These models typically presume that HVAC systems will operate precisely at their designed efficiencies, that control sequences will be flawlessly executed, and that setpoints will be maintained within tight tolerances without accounting for potential malfunctions, suboptimal settings due to user overrides, or a lack of dynamic response to varying loads. Furthermore, climate data used in models might be based on typical meteorological years (TMY) which, while representative, do not capture extreme weather events or microclimatic variations specific to a building’s precise location. Assumptions about material thermal properties and airtightness, too, often err on the side of optimism, assuming perfect installation and material integrity that may not be achieved on site.
2.2 Construction Quality Issues
The transition from design specifications to physical reality often introduces a critical source of the performance gap: deviations from design intent during construction. The quality of construction, encompassing both workmanship and adherence to specified materials and details, plays an indisputable role in determining a building’s actual energy performance. Even minor discrepancies or defects in the building envelope or system installations can cumulatively lead to substantial increases in energy consumption. (buildpass.co.uk)
Common issues include improper insulation installation, where batts may be compressed, gapped, or omitted entirely, leading to reduced effective R-values. Air leakage, or uncontrolled infiltration and exfiltration through cracks, gaps, and penetrations in the building envelope, is another pervasive problem. Even seemingly small unsealed gaps around windows, doors, electrical outlets, or pipe penetrations can result in significant heat loss or gain, compromising thermal performance and increasing heating and cooling loads. Thermal bridges, which are pathways of high heat transfer through the building envelope (e.g., steel beams penetrating an insulated wall, concrete slab edges, or poorly designed window frames), are particularly insidious. They bypass insulation layers, creating cold spots internally, increasing heat flow, and raising the risk of condensation and mold formation. The substitution of specified materials with cheaper, lower-performance alternatives without proper re-evaluation of energy implications is also a common occurrence. Furthermore, structural elements, façade systems, and window installations that deviate from precise alignment or sealing requirements can create chronic issues. Lack of rigorous quality control, insufficient site supervision, and inadequate training of construction personnel often contribute to these defects, ensuring that the ‘as-built’ condition significantly underperforms the ‘as-designed’ specifications.
2.3 Inadequate Commissioning
Commissioning (Cx) is a quality assurance process that ensures building systems are installed correctly, operate as intended by the design, and meet the owner’s project requirements. It is a systematic process extending throughout the project lifecycle, from initial design review to post-occupancy functional testing. However, inadequate or incomplete commissioning is a prevalent and substantial contributor to the performance gap, often rendering even perfectly designed and constructed systems inefficient. (frontiersin.org)
Failures in commissioning can manifest in several ways. Systems may be installed but never properly balanced, calibrated, or integrated, leading to inefficient operation. For instance, an HVAC system might have oversized fans or pumps operating at constant speed when variable speed drives are specified, or control sequences designed to optimize energy use might be bypassed or misconfigured. Sensors for temperature, humidity, or CO2 might be inaccurately calibrated or incorrectly placed, leading to erroneous readings and inappropriate system responses (e.g., over-cooling or over-heating zones). Lighting controls, such as occupancy sensors or daylight harvesting systems, might be incorrectly programmed or disabled, leading to lights remaining on when spaces are vacant or when sufficient daylight is available. Inadequate functional performance testing means that systems are not tested under a full range of operating conditions, including seasonal variations and peak loads, allowing subtle issues to remain undetected. Poor documentation of the commissioning process, including missing test reports, operational manuals, and as-built drawings, further exacerbates the problem, making troubleshooting and future maintenance challenging. Crucially, insufficient training of facility management staff on the proper operation and maintenance of complex building systems often means that even if a system is commissioned correctly, it will not be operated optimally over its lifespan. This leads to continuous energy waste and accelerated equipment degradation, turning initial design efficiency into a persistent operational deficit.
2.4 Occupant Behavior
Perhaps one of the most complex and least predictable factors influencing a building’s energy consumption is the behavior of its occupants. While building design and technology establish the potential for energy efficiency, it is the daily actions and choices of the people within the building that ultimately dictate actual energy usage. The human element introduces a significant degree of variability that energy models often struggle to capture accurately, leading to a substantial portion of the performance gap. (frontiersin.org)
Variations in how occupants interact with lighting, heating, cooling, and ventilation systems can lead to dramatic differences between predicted and actual energy use. For example, individuals may adjust thermostats outside of optimal setpoints for personal comfort, open windows while heating or air conditioning is active, leave lights on in unoccupied spaces, or plug in numerous personal electronic devices and appliances (e.g., mini-fridges, coffee makers, personal heaters) that contribute to un-modeled plug loads. The concept of ‘adaptive comfort’ suggests that people adapt to their thermal environment and prefer a wider range of indoor conditions than traditional comfort models predict; however, individual preferences can still lead to overrides of automated systems. Psychological factors, such as a lack of awareness regarding energy consumption, a perception that individual actions have negligible impact, or a prioritization of immediate comfort over long-term energy savings, play a significant role. Studies have indicated that occupant behavior can account for anywhere from 10% to 30% or more of the observed performance gap, highlighting the critical need for proactive strategies focused on occupant engagement, education, and behavioral nudges rather than merely relying on passive design or automated systems. Without active user participation and understanding, even the most advanced, energy-efficient building technologies may fail to deliver their full potential.
2.5 System Malfunctions and Maintenance Deficiencies
Beyond initial commissioning, the ongoing operational life of a building is subject to wear and tear, and complex mechanical, electrical, and plumbing (MEP) systems require continuous attention to maintain peak performance. System malfunctions, whether minor or significant, coupled with inadequate or deferred maintenance, constitute another substantial and often overlooked contributor to the performance gap.
Equipment degradation is an inevitable aspect of a building’s lifecycle. Components such as motors, pumps, fans, and chillers can lose efficiency over time due to dirt accumulation, bearing wear, or refrigerant leaks. Sensor drift, where environmental sensors (temperature, humidity, CO2, occupancy) gradually provide inaccurate readings, can lead to control systems operating inefficiently, initiating heating or cooling when not required, or failing to respond adequately to actual conditions. Control system overrides, sometimes performed by building operators lacking a full understanding of the optimized sequences or for the sake of perceived immediate comfort, can disable energy-saving strategies, leading to constant operation of variable air volume (VAV) boxes or leaving systems in manual mode. Lack of preventative maintenance schedules means filters become clogged, coils get fouled, and belts loosen, all of which restrict airflow, reduce heat exchange efficiency, and force equipment to work harder and consume more energy. Minor leaks in ductwork or piping can lead to significant energy losses over time. The cumulative effect of these seemingly small issues can result in substantial energy waste and accelerated equipment depreciation, directly widening the performance gap between ideal and actual energy consumption.
2.6 Operational and Management Issues
Even with well-designed and properly commissioned systems, the day-to-day management and operational practices of a facility can significantly impact energy performance. Inadequate training of facility management (FM) staff, poor operational scheduling, and siloed organizational structures often contribute to inefficient energy use.
Many building control systems (BMS/BEMS) are complex, requiring specialized knowledge to operate and optimize effectively. If FM personnel lack comprehensive training or are frequently replaced without proper handover, they may resort to simplistic or ‘safe’ operating modes that consume more energy, such as running systems continuously or overriding automated schedules. Poor scheduling practices, such as operating HVAC systems or lighting in unoccupied zones or during off-hours, are common and directly lead to wasted energy. This can be due to a lack of detailed occupancy schedules, a ‘set it and forget it’ mentality, or a disconnect between building management and tenant needs. Furthermore, budget constraints often lead to deferred maintenance, as mentioned previously, but also to an unwillingness to invest in software upgrades for BEMS, new sensors, or training programs that could improve efficiency. Organizational silos, where design, construction, and operations teams do not communicate effectively or share information, can lead to a fundamental misunderstanding of the building’s intended operational philosophy. This disconnect often prevents the feedback loop necessary for continuous improvement, ensuring that operational inefficiencies persist long-term. The lack of clear performance metrics or accountability for energy consumption within an organization can also mean that energy waste goes unnoticed or unaddressed.
Many thanks to our sponsor Focus 360 Energy who helped us prepare this research report.
3. Advanced Diagnostic Tools and Continuous Monitoring Systems
Bridging the performance gap necessitates a robust understanding of how a building truly operates post-occupancy. This requires moving beyond static energy audits to dynamic, real-time data acquisition and sophisticated analysis. Advanced diagnostic tools and continuous monitoring systems are indispensable for identifying inefficiencies, troubleshooting problems, and validating the effectiveness of energy-saving interventions.
3.1 Building Energy Management Systems (BEMS)
Building Energy Management Systems (BEMS), also commonly referred to as Building Management Systems (BMS), represent the central nervous system of modern buildings. They are integrated platforms designed to monitor, control, and manage various building services and systems, including HVAC, lighting, security, and access control. In the context of energy performance, BEMS are crucial for acquiring granular data on energy consumption and operational parameters. They collect data from a multitude of sensors and meters, providing real-time insights into energy flows and system performance.
Key capabilities of BEMS include:
* Granular Data Acquisition: BEMS can log data points at very short intervals (e.g., every minute or every 15 minutes) for parameters such as zone temperatures, relative humidity, CO2 levels, fan speeds, pump pressures, valve positions, and individual circuit power consumption. This high-resolution data is critical for understanding dynamic energy usage patterns.
* Trend Analysis: The historical data collected by BEMS allows facility managers to identify trends, compare performance against baselines or design targets, and pinpoint periods of abnormal energy consumption.
* Alarm Management: BEMS can be programmed to trigger alerts when system parameters deviate from predefined setpoints or when equipment malfunctions are detected (e.g., a pump operating outside its efficiency range, a temperature sensor reading inconsistently).
* Centralized Control: BEMS enable centralized control over building systems, allowing operators to adjust setpoints, modify schedules, and implement demand-response strategies from a single interface. This capability is essential for optimizing system operation in response to changing occupancy, external conditions, or energy tariffs.
* Integration with Sub-systems: Modern BEMS are designed to integrate disparate building systems, facilitating coordinated control and data exchange. For example, occupancy data from access control systems can inform HVAC scheduling, or lighting levels can adjust based on daylight sensors and occupancy status.
By providing this level of detailed operational insight, BEMS empower facility managers to proactively identify inefficiencies, diagnose problems, and implement corrective measures promptly, thereby reducing energy waste and improving overall building performance.
3.2 Internet of Things (IoT) Sensors
The proliferation of Internet of Things (IoT) sensors has revolutionized data collection in buildings, offering unprecedented granularity and flexibility in monitoring energy performance. IoT sensors are physical devices equipped with sensors, processing capabilities, and communication modules that allow them to collect and transmit data over a network, often wirelessly. (arxiv.org)
Key aspects and benefits of IoT sensors in building energy monitoring include:
* Diverse Data Types: IoT sensors can capture a wide array of environmental and operational data, including ambient temperature, relative humidity, CO2 concentrations, volatile organic compounds (VOCs), light levels, occupancy detection (using PIR, ultrasonic, or even camera-based sensors), equipment run-time, vibration, and granular electrical power consumption at the circuit or even individual appliance level.
* Granularity and Spatial Resolution: Unlike traditional building management systems that might rely on a few large sensors for an entire zone, IoT sensors can be deployed in large numbers, providing highly localized and granular data. This allows for precise identification of thermal discomfort zones, localized energy waste, or accurate occupancy patterns within specific areas.
* Wireless and Cost-Effective Deployment: Many IoT sensors are wireless, battery-powered, and relatively inexpensive, making them easy to deploy and reconfigure without extensive wiring infrastructure. This significantly reduces installation costs and allows for flexible data collection strategies.
* Enhanced Occupancy Monitoring: Beyond simple presence detection, advanced IoT sensors and related analytics can provide insights into actual occupant counts, movement patterns, and space utilization, which are critical inputs for truly optimized HVAC and lighting control strategies.
* Predictive Maintenance: Vibration sensors on mechanical equipment or current sensors on motors can detect early signs of impending failure, enabling predictive maintenance interventions before a complete breakdown occurs, thus preventing energy waste from malfunctioning equipment and extending asset life.
While IoT sensors offer immense potential, challenges include managing the vast volumes of data generated, ensuring seamless integration with existing BEMS and analytics platforms, and addressing cybersecurity concerns associated with networked devices. Nevertheless, their ability to provide rich, real-time data at an unprecedented level of detail significantly enhances the capacity for identifying energy waste and informing targeted interventions.
3.3 Data Analytics and Machine Learning
The sheer volume and velocity of data generated by BEMS and IoT sensors would be overwhelming without sophisticated tools for analysis. Data analytics and machine learning (ML) algorithms are increasingly crucial for extracting actionable insights from this raw data, transforming it into intelligence that can bridge the performance gap. (arxiv.org)
These tools move beyond simple trending to uncover hidden patterns, predict future energy use, identify anomalies, and even suggest optimization strategies:
* Descriptive Analytics: Summarizing historical data to understand past energy consumption patterns, e.g., weekly energy profiles, breakdown by end-use (lighting, HVAC, plug loads).
* Diagnostic Analytics: Investigating ‘why’ something happened. This involves comparing current performance against baselines, identifying deviations, and correlating energy spikes with specific events or system operations. For instance, diagnostic algorithms can quickly identify if a particular HVAC unit is operating continuously during unoccupied hours.
* Predictive Analytics: Using historical data and machine learning models (e.g., regression, time series models) to forecast future energy demand based on anticipated weather conditions, occupancy schedules, and historical consumption patterns. This enables proactive energy management and demand-side response.
* Prescriptive Analytics: Going a step further by recommending specific actions to optimize energy use. For example, an ML model might suggest optimal setpoint adjustments for a specific zone based on predicted occupancy and weather, or recommend a maintenance action based on detected equipment degradation.
* Fault Detection and Diagnostics (FDD): A highly specialized application of ML that automatically identifies and diagnoses operational faults in building systems. FDD algorithms can detect issues like stuck dampers, leaky valves, faulty sensors, or simultaneous heating and cooling conditions, often long before they become apparent to human operators. This minimizes energy waste from malfunctioning equipment and reduces maintenance costs.
* Anomaly Detection: Machine learning algorithms can learn normal operational baselines and flag any deviations as anomalies, indicating potential energy waste or equipment issues that require investigation.
* Optimal Control Strategies: Advanced ML techniques, such as reinforcement learning, are being explored to develop adaptive control algorithms that can dynamically adjust building systems in real-time to minimize energy consumption while maintaining occupant comfort, learning from past performance.
The integration of data analytics and machine learning with BEMS and IoT data streams enables a proactive and intelligent approach to building energy management. This shifts the paradigm from reactive troubleshooting to predictive optimization, significantly enhancing the accuracy of energy performance models and facilitating continuous improvements in operational efficiency.
3.4 Thermal Imaging and Air Tightness Testing
While continuous monitoring focuses on operational data, a crucial aspect of diagnosing construction quality issues, especially those related to the building envelope, involves specialized diagnostic tools like thermal imaging and air tightness testing. These tools provide visual and quantitative evidence of performance deficiencies that contribute significantly to the performance gap.
-
Thermal Imaging (Thermography): This non-destructive diagnostic technique uses infrared cameras to detect variations in surface temperature, which can reveal areas of heat loss or gain through the building envelope. Hotter areas on an exterior wall in winter, or colder areas on an interior wall, indicate areas where insulation is deficient, compromised, or where thermal bridging occurs. Common findings include:
- Missing or Gapped Insulation: Areas where insulation has been omitted or poorly installed show up as distinct warm or cold spots.
- Thermal Bridges: Structural elements (e.g., concrete slabs, steel beams) that penetrate the insulation layer appear as linear thermal paths.
- Air Leakage: Infiltrating cold air or exfiltrating warm air creates distinct temperature patterns that are visible with a thermal camera, especially around windows, doors, and building joints.
- Moisture Issues: Areas with moisture ingress often show up as cooler spots due to evaporative cooling.
Thermal imaging provides invaluable visual evidence that can pinpoint specific construction defects, allowing for targeted remediation rather than guesswork.
-
Air Tightness Testing (Blower Door Test): This quantitative method measures the uncontrolled air leakage rate of a building’s envelope. A large fan (blower door) is temporarily sealed into an exterior doorway and used to either pressurize or depressurize the building to a specific air pressure difference (e.g., 50 Pascals). The fan speed required to maintain this pressure difference directly correlates to the building’s air leakage rate, typically expressed as air changes per hour at 50 Pascals (ACH50) or cubic feet per minute per square foot of envelope (CFM/ft²).
A high air leakage rate indicates poor sealing of the building envelope, leading to significant energy loss due to uncontrolled ventilation. Combined with thermal imaging, a blower door test can make air leakage pathways more apparent, as the induced pressure difference accentuates air movement, making thermal patterns more visible. These tests are vital for identifying widespread issues stemming from poor sealing around windows, doors, and service penetrations, as well as general flaws in the continuity of the air barrier. Addressing these air leakage points through sealing and caulking can dramatically improve the thermal performance of a building and reduce heating and cooling loads, directly contributing to closing the performance gap.
Many thanks to our sponsor Focus 360 Energy who helped us prepare this research report.
4. Post-Occupancy Evaluation (POE) Methodologies
Post-Occupancy Evaluation (POE) is a systematic process of evaluating the performance of a building after it has been constructed and occupied. Unlike design-stage energy models or even initial commissioning checks, POE provides a critical feedback loop, assessing how well a building meets its original design intent, particularly regarding energy performance, and equally importantly, how effectively it supports the needs and satisfaction of its occupants. It bridges the gap between theoretical performance and real-world experience, offering invaluable insights for both current operations and future building projects. (en.wikipedia.org)
4.1 Purpose and Scope of POE
The primary purpose of POE is to gather comprehensive data and feedback on a building’s performance in use, compare it against established benchmarks and design goals, and identify discrepancies. Its scope is inherently multidisciplinary, encompassing more than just energy consumption, to provide a holistic view of building effectiveness. Key aspects of its scope include:
- Energy Performance Verification: Directly comparing actual energy consumption data (from utility bills, BEMS, sub-metering) against design predictions, operational benchmarks, and industry standards. This is where the ‘performance gap’ is definitively quantified.
- Indoor Environmental Quality (IEQ): Assessing factors critical to occupant comfort and health, such as thermal comfort (temperature, humidity, air movement), indoor air quality (CO2, VOCs, particulate matter), lighting levels (daylight and artificial), and acoustic comfort (noise levels, sound privacy).
- Functional Performance: Evaluating how well the building supports the activities and functions for which it was designed, including space utilization, layout efficiency, accessibility, and the functionality of specific areas (e.g., meeting rooms, laboratories).
- Technical Performance: Reviewing the performance of building systems (HVAC, lighting controls, renewable energy systems) in terms of reliability, efficiency, ease of maintenance, and adherence to operational parameters.
- Occupant Satisfaction and Productivity: Gathering subjective feedback from occupants regarding their comfort, perceived control over their environment, satisfaction with various building features, and how the building environment impacts their productivity and well-being.
- Operational and Maintenance Effectiveness: Assessing the efficiency and effectiveness of facility management practices, including maintenance schedules, responsiveness to issues, and operational costs.
POE serves not only as a diagnostic tool for existing buildings but also as a vital learning mechanism for the entire building industry. It helps to validate design hypotheses, expose common errors or misassumptions, and inform the development of more effective design strategies, construction practices, and operational protocols for future projects. By fostering a culture of accountability and continuous improvement, POE helps to close the knowledge gap between design intent and operational reality.
4.2 POE Process
The POE process is typically structured and methodical, involving several distinct phases to ensure thorough data collection, rigorous analysis, and effective reporting. While specific methodologies may vary, a common POE framework includes:
-
Pre-evaluation Planning:
- Define Objectives: Clearly articulate what aspects of the building are being evaluated (e.g., energy, IEQ, occupant satisfaction) and what questions the POE aims to answer.
- Scope Definition: Determine the specific areas or systems within the building to be evaluated.
- Stakeholder Identification: Identify all relevant parties, including building owners, occupants, facility managers, design team members, and contractors, and plan for their involvement.
- Methodology Selection: Choose appropriate data collection methods (surveys, interviews, monitoring) and define the timeline and resources required.
-
Data Collection: This phase involves a combination of qualitative and quantitative approaches:
- Surveys and Questionnaires: Administering standardized or custom surveys to a representative sample of occupants to gather subjective feedback on comfort, satisfaction, and perceptions of building performance. Methodologies like the Building Use Studies (BUS) methodology are widely used for this purpose.
- Interviews and Focus Groups: Conducting structured or semi-structured interviews with occupants, building management, and maintenance staff to delve deeper into specific issues, gather anecdotes, and understand operational challenges.
- Environmental Monitoring: Deploying sensors to continuously monitor objective IEQ parameters such as temperature, humidity, CO2 levels, light levels, and noise. This provides quantitative data to corroborate or contradict subjective occupant feedback.
- Energy Data Analysis: Collecting and analyzing utility bills, sub-metered data, and BEMS logs to track actual energy consumption, identify consumption patterns, and compare against benchmarks and predictions.
- Technical Performance Checks: Reviewing maintenance logs, conducting visual inspections, and performing functional tests on building systems to assess their operational status and efficiency. This may involve revisiting commissioning documentation.
-
Data Analysis: Once data is collected, it is meticulously analyzed:
- Quantitative Analysis: Statistical analysis of survey data, energy consumption figures, and environmental monitoring data to identify trends, correlations, and statistically significant deviations.
- Qualitative Analysis: Thematic analysis of interview transcripts and open-ended survey responses to identify recurring issues, perceptions, and suggestions.
- Benchmarking: Comparing the building’s performance against similar buildings, industry standards, and its own design targets to contextualize the findings.
-
Reporting and Dissemination: The final phase involves compiling findings into a comprehensive report and communicating them to relevant stakeholders:
- Findings Presentation: Clearly articulating the observed performance gaps, underlying causes, and their implications.
- Recommendations: Proposing actionable recommendations for immediate operational improvements, retrofits, policy changes, and lessons learned for future projects.
- Stakeholder Engagement: Presenting findings and recommendations to building owners, facility managers, occupants, and the design team to foster buy-in and facilitate implementation.
Engaging occupants actively throughout the POE process—from initial surveys to feedback on proposed solutions—is paramount for obtaining accurate, authentic, and actionable insights. Their lived experience provides a perspective that purely technical assessments cannot replicate.
4.3 Benefits of POE
Implementing comprehensive POE programs yields a multitude of benefits that extend far beyond simply identifying energy waste. It fosters a culture of continuous improvement, enhances stakeholder accountability, and ultimately contributes to the creation of more sustainable, comfortable, and efficient built environments.
Key benefits include:
- Improved Building Performance: Direct identification of operational inefficiencies and design flaws allows for targeted interventions, leading to quantifiable energy savings, reduced utility costs, and a smaller carbon footprint. This directly helps in bridging the performance gap.
- Enhanced Occupant Satisfaction and Well-being: By addressing issues related to thermal comfort, air quality, lighting, and acoustics based on occupant feedback, POE improves the indoor environmental quality (IEQ), leading to higher occupant satisfaction, fewer complaints, and potentially increased productivity in workplace settings.
- Valuable Lessons for Future Projects: POE provides a critical feedback loop to the design and construction communities. By understanding what worked well and what didn’t in completed projects, designers can refine their strategies, engineers can improve system specifications, and contractors can enhance construction practices. This institutional learning helps avoid repeating mistakes and promotes best practices in subsequent developments.
- Reduced Operational and Maintenance Costs: Identifying and rectifying system malfunctions, optimizing control strategies, and understanding user behavior patterns through POE can lead to more efficient maintenance schedules, extended equipment lifespan, and reduced need for reactive repairs.
- Accountability and Validation: POE provides objective data to validate whether design goals and performance targets have been met. This fosters greater accountability among all project stakeholders, from clients to designers and contractors.
- Evidence-Based Decision Making: Rather than relying on assumptions or anecdotal evidence, POE provides data-driven insights that inform strategic decisions regarding building operations, retrofits, and future investments.
- Certification and Compliance: For buildings seeking green building certifications (e.g., LEED, BREEAM), POE data can be crucial for demonstrating actual operational performance and achieving relevant credits or compliance requirements.
In essence, POE transforms buildings from static structures into dynamic learning laboratories. It helps to close the information gap that typically exists between the design and operational phases, creating more resilient, user-centric, and truly high-performing buildings.
Many thanks to our sponsor Focus 360 Energy who helped us prepare this research report.
5. Strategies for Effective Handover Processes and Occupant Engagement
The handover from the construction team to the operations team and the subsequent engagement of occupants are pivotal stages in determining a building’s long-term energy performance. A smooth transition and an informed, empowered occupant base are crucial for minimizing the performance gap and sustaining energy efficiency efforts.
5.1 Soft Landings Framework
The Soft Landings framework is a structured and collaborative approach designed to ensure a smooth, client-focused transition from a building’s construction phase into its operational life. It fundamentally redefines the relationship between the design/construction team and the client/occupants, extending the involvement of the project team beyond practical completion to include the early years of occupation. The core principle is to ensure that the building not only performs as designed but also meets the actual needs and expectations of its users, thereby directly addressing the performance gap. (uk.sfs.com)
Key principles and phases of Soft Landings include:
- Early Engagement and Continuity: Soft Landings advocates for the early involvement of the client’s operational team (facility managers, end-users) from the design stage. Critically, the design and construction teams maintain a level of involvement for an agreed period (typically 1-3 years) post-occupancy.
- Clear Objectives and Performance Targets: From the outset, clear and measurable energy performance targets and occupant satisfaction goals are established, understood, and agreed upon by all stakeholders.
- Operational Readiness Reviews: Throughout the design and construction phases, reviews are conducted with an operational lens, ensuring that systems are not only buildable but also maintainable, accessible, and user-friendly. This includes considerations for space for maintenance, access to equipment, and intuitive control interfaces.
- Enhanced Commissioning: Soft Landings emphasizes a rigorous and comprehensive commissioning process, extending beyond basic functional tests to include seasonal commissioning (testing systems under varying seasonal conditions) and performance verification against actual design targets.
- Building User Guides (BUGs): Development of user-friendly, non-technical guides for occupants and simplified operational manuals for facility managers. These guides go beyond traditional O&M manuals, providing practical advice on how to use the building’s systems efficiently and comfortably.
- Post-Occupancy Support: The design and construction teams provide ongoing support, advice, and training to the building operators and occupants during the initial occupation period. This allows for prompt identification and resolution of teething problems or operational inefficiencies.
- Feedback Loops and Review Meetings: Regular meetings are scheduled during the initial operational period to gather feedback from occupants and operators, discuss performance data, and collectively address emerging issues. This provides a formal mechanism for POE and continuous adjustment.
By ensuring that the design intent translates into actual performance and user satisfaction, Soft Landings significantly mitigates the factors contributing to the performance gap, promoting genuine operational excellence and sustainable outcomes.
5.2 Occupant Training and Education
Even the most technologically advanced and efficiently designed building can underperform if its occupants do not understand how to use its systems effectively. Providing comprehensive and ongoing training and education to occupants is a critical strategy for empowering them to contribute positively to a building’s energy performance.
Effective occupant training and education initiatives should consider:
- Content Tailored to User Needs: Training should cover essential aspects of the building’s energy-related systems that occupants interact with. This includes how to properly use thermostats and individual controls, operate automated window blinds or shading devices, understand and utilize lighting controls (e.g., occupancy sensors, dimming controls), and identify opportunities to reduce personal plug loads. It should also explain the reasoning behind certain energy-saving features, such as why windows should not be opened when HVAC is running.
- Accessible and Varied Delivery Methods: Information can be disseminated through multiple channels to cater to different learning styles and preferences:
- Workshops and Seminars: Interactive sessions conducted during the initial occupancy period, allowing occupants to ask questions and receive hands-on demonstrations.
- Informational Materials: Clear, concise, and visually appealing building user guides, leaflets, and posters distributed throughout the building, highlighting energy-saving tips and system functionalities.
- Digital Resources: Dedicated building websites, apps, or online portals providing access to user manuals, FAQs, energy dashboards, and video tutorials.
- Signage and Labels: Simple, intuitive labels on controls, light switches, and equipment to guide proper usage.
- Focus on Behavior Change, Not Just Information: Education should aim to foster energy-conscious behaviors and a sense of shared responsibility. This involves explaining the ‘why’ behind energy-saving measures, linking individual actions to broader sustainability goals, and showcasing the collective impact.
- Ongoing Reinforcement: Energy-conscious behavior is not a one-time training event. Regular reminders, seasonal tips (e.g., ‘Winter Heating Habits’), and updated information help to reinforce learned behaviors and adapt to changes in building operation or technology.
By investing in occupant education, building managers can transform occupants from passive consumers of energy into active participants in achieving energy efficiency, directly reducing the portion of the performance gap attributable to behavioral factors.
5.3 Feedback Mechanisms
Establishing clear, accessible, and responsive feedback mechanisms is essential for maintaining building performance and fostering a collaborative relationship between building management and occupants. These channels enable occupants to report issues, provide suggestions, and feel heard, which is critical for ongoing optimization and occupant satisfaction.
Effective feedback mechanisms include:
- Centralized Helpdesks or Service Desks: A primary point of contact for occupants to report immediate issues related to comfort (too hot/cold), lighting, air quality, or equipment malfunctions. Timely response and resolution are paramount for building trust.
- Dedicated Reporting Platforms (Apps/Portals): Digital platforms or mobile applications that allow occupants to submit service requests, provide detailed feedback, and track the status of their issues. These platforms can also provide information about energy performance or building news.
- Regular Occupant Surveys: Periodic surveys (e.g., annually or bi-annually) can gather broader feedback on overall satisfaction, comfort levels, and specific building features. These surveys can complement the objective data from environmental monitoring.
- Tenant Meetings or Committees: In multi-tenant buildings, establishing regular forums where occupants can meet with building management to discuss common issues, provide collective feedback, and participate in decision-making processes related to building operations.
- Suggestion Boxes (Physical and Digital): Simple, anonymous channels for occupants to submit ideas or concerns.
- Energy Performance Dashboards: Publicly displayed or accessible digital dashboards that show real-time energy consumption, comparisons to targets, or even peer comparisons. This provides transparent feedback to occupants about the collective impact of their actions and can serve as a motivational tool.
The effectiveness of these mechanisms hinges on timely responses and demonstrated action based on the feedback received. A robust feedback loop ensures that occupant concerns are addressed, operational issues are identified and rectified promptly, and there is continuous communication that reinforces a sense of shared responsibility for the building’s performance. This dynamic interaction helps to fine-tune building operations and close the performance gap by directly addressing occupant-related issues and preferences.
5.4 Behavioral Change Interventions
Beyond simply informing and training, more sophisticated behavioral change interventions leverage insights from psychology and economics to subtly or overtly encourage energy-saving behaviors among occupants. These strategies acknowledge that rational decision-making is only one part of human behavior, and often emotional, social, or habitual factors play a larger role.
Key behavioral change interventions include:
- Nudging: Subtle prompts or alterations to the environment that influence choices without restricting options. Examples include default settings for lighting or HVAC that are energy-efficient, placing waste bins prominently to encourage recycling, or making energy information easily visible at the point of decision (e.g., smart thermostats)..
- Gamification: Applying game-design elements and game principles in non-game contexts to engage users and solve problems. In buildings, this could involve creating competitions among departments or floors for energy reduction, offering rewards for reaching energy-saving targets, or displaying leaderboards showing comparative energy performance.
- Real-Time Energy Displays and Dashboards: Providing occupants with immediate and visible feedback on their energy consumption. A clear display in a common area showing the building’s current energy use or a personal dashboard showing individual plug load consumption can make energy tangible and encourage conscious reduction.
- Peer Comparison: Leveraging social norms by showing occupants how their energy consumption compares to that of their peers or similar buildings. If people know they are using more energy than their neighbors, they may be motivated to reduce consumption to conform to social norms.
- Goal Setting and Commitment: Encouraging individuals or groups to set specific, measurable energy reduction goals and publicly commit to them. The act of commitment can increase the likelihood of follow-through.
- Awareness Campaigns: Regular, engaging communications (e.g., newsletters, posters, emails) that highlight energy-saving opportunities, celebrate successes, and explain the environmental and financial benefits of reduced energy consumption. These campaigns help to build a culture of energy awareness.
- Feedback on Environmental Impacts: Connecting energy consumption directly to its environmental consequences (e.g., ‘your actions saved X kg of CO2 equivalent this month’) can provide a powerful motivator for environmentally conscious individuals.
By strategically implementing these behavioral interventions, building managers can tap into intrinsic and extrinsic motivators, making energy efficiency an easier, more appealing, or socially desirable choice for occupants, thereby significantly impacting the building’s overall energy performance.
Many thanks to our sponsor Focus 360 Energy who helped us prepare this research report.
6. Bridging the Performance Gap: Integrated Strategies
Addressing the performance gap is not a singular action but a continuous, integrated process that demands collaboration across all stages of a building’s lifecycle. A holistic approach that weaves together design excellence, rigorous construction, thorough commissioning, and proactive engagement with users and operators is essential for achieving and sustaining high-performance buildings. These integrated strategies aim to minimize deviations from design intent and ensure that operational realities align with performance aspirations.
6.1 Collaborative Design and Construction (Integrated Project Delivery – IPD)
Traditional design and construction processes often involve siloed teams working sequentially, leading to disconnects, missed opportunities, and blame when issues arise. Integrated Project Delivery (IPD) and similar collaborative approaches seek to overcome these challenges by fostering early, continuous, and intense collaboration among all key stakeholders from the project’s inception. This includes the client, architects, engineers (structural, mechanical, electrical), contractors, key subcontractors, and often, the future facility managers.
Key aspects of IPD and collaborative approaches include:
- Early Stakeholder Involvement: Bringing contractors and key subcontractors into the design process much earlier allows for constructability reviews, value engineering, and identification of potential issues before they become costly changes in the field. This ensures that designs are not only aesthetically pleasing and functional but also practical and efficient to build.
- Shared Risk and Reward: Unlike traditional contracts where risk is transferred, IPD frameworks often involve multi-party agreements that align the financial interests of all core team members. This incentivizes collective problem-solving and shared responsibility for project outcomes, including energy performance targets.
- Open Communication and Transparency: Regular, often co-located, meetings and shared digital platforms (like Building Information Modeling – BIM) facilitate real-time information exchange and decision-making. BIM, in particular, allows all disciplines to work on a common 3D model, identifying clashes and optimizing design details related to building envelope, HVAC routing, and lighting layout, all of which impact energy performance.
- Performance-Based Goals: Collaborative teams can jointly establish clear, measurable energy performance targets from the outset, moving beyond prescriptive requirements to focus on verifiable outcomes. This ensures that energy efficiency is an embedded objective rather than an afterthought.
- Lifecycle Costing: An integrated team is better positioned to conduct comprehensive lifecycle cost analyses, weighing initial capital costs against long-term operational costs, including energy consumption and maintenance, to make more informed decisions about material and system selections.
By breaking down traditional barriers and fostering a collective commitment to performance, collaborative design and construction significantly reduce the likelihood of design flaws or construction deviations that contribute to the performance gap.
6.2 Rigorous Quality Control and Assurance
Even the most meticulously designed building will fail to meet its energy performance potential if construction quality is compromised. Rigorous quality control (QC) and quality assurance (QA) measures throughout the construction phase are paramount to ensure that the ‘as-built’ condition faithfully executes the ‘as-designed’ specifications, particularly concerning the building envelope and MEP systems.
Key strategies for stringent QC/QA include:
- Detailed Specifications and Submittals: Clear, unambiguous specifications for materials, assemblies, and installation procedures, coupled with a thorough review of contractor submittals (shop drawings, product data, samples) to ensure compliance with design intent and energy performance requirements.
- Comprehensive Site Inspections: Regular and systematic site inspections by qualified personnel (design team, independent third-party consultants, commissioning agents) to verify that insulation is properly installed, air barriers are continuous, windows are correctly sealed, and HVAC ductwork and piping are installed according to specifications.
- Material Testing and Verification: Random or scheduled testing of materials (e.g., insulation R-value, concrete strength) to ensure they meet specified performance characteristics.
- Performance Mock-ups: For complex façade systems or critical envelope details, constructing full-scale mock-ups on-site or off-site to test airtightness, water penetration, and thermal performance before mass production and installation. This proactive approach identifies design or construction flaws early.
- Installer Training and Certification: Ensuring that contractors and their installers possess the necessary skills and certifications for installing critical energy-related components (e.g., air barrier systems, advanced glazing, complex HVAC equipment).
- Digital Tools for QC: Leveraging technologies like drones for aerial inspections, laser scanning for dimensional accuracy, and digital checklists/reporting apps to streamline QC processes and enhance traceability.
- Documentation and Traceability: Maintaining meticulous records of all inspections, tests, non-conformances, and corrective actions. This documentation is crucial for verifying compliance and for future troubleshooting.
By implementing these robust QC/QA measures, the gap between design aspiration and constructed reality can be significantly narrowed, laying a solid foundation for achieving the building’s intended energy performance.
6.3 Comprehensive and Continuous Commissioning
Commissioning (Cx) is the systematic process of ensuring that all building systems perform interactively according to the design intent and the owner’s operational needs. While often focused on the post-construction phase, a truly effective commissioning process begins at the project’s inception and extends throughout the building’s lifespan, evolving into ‘continuous commissioning’ or ‘recommissioning’. This comprehensive approach is vital for preventing and rectifying many of the operational inefficiencies that contribute to the performance gap. (frontiersin.org)
Key elements of comprehensive and continuous commissioning include:
- Design-Phase Commissioning: Reviewing design documents (schematic design, design development, construction documents) to ensure that energy performance goals are clearly defined, verifiable, and achievable. This includes reviewing control sequences, equipment selections, and maintainability.
- Construction-Phase Commissioning: Overseeing the installation of systems, verifying that equipment is correctly installed and wired, and conducting pre-functional checks before full system startup. This ensures that installation aligns with manufacturer specifications and design documents.
- Acceptance Testing (Functional Performance Testing): Rigorous testing of individual components and integrated systems under various operating conditions (e.g., partial load, full load, seasonal variations, failure scenarios). This includes testing sequences of operation, alarm functions, and interlocks between systems. For HVAC, this might involve verifying airflow rates, temperature control, and proper operation of economizers and heat recovery systems. For lighting, it means confirming correct sensor operation, dimming, and scheduling.
- Systems Manuals and Training: Developing comprehensive systems manuals that detail operational procedures, maintenance requirements, and troubleshooting guides. Crucially, extensive training for facility operators and maintenance staff on the proper use and optimization of all building systems is provided.
- Seasonal Commissioning: Conducting additional functional performance tests during different seasons (e.g., winter vs. summer) to ensure systems perform optimally under varying environmental conditions and loads. This helps uncover issues that might not appear during initial commissioning.
- Continuous Commissioning (Ongoing Commissioning): An ongoing process of optimizing building performance over time. This involves periodic re-evaluation of systems, analysis of operational data (often via BEMS), identification of operational drifts or new opportunities for efficiency, and implementation of corrective actions. It is a proactive approach to maintaining peak performance and adapting to changes in occupancy, use, or technology. Continuous commissioning leverages data analytics and FDD (Fault Detection and Diagnostics) tools to automatically identify deviations from optimal performance and flag them for investigation.
By embedding commissioning throughout the building lifecycle, owners can ensure that their significant investments in energy-efficient design and technologies translate into demonstrable energy savings and sustained high performance over the long term.
6.4 Continuous Monitoring and Performance Verification
Beyond initial commissioning, the sustained high performance of a building hinges on continuous monitoring of its operational data and regular verification against established performance benchmarks. This proactive approach allows building operators to move from reactive problem-solving to predictive optimization, significantly narrowing the performance gap over time.
Key aspects of continuous monitoring and performance verification include:
- Real-Time Data Acquisition: Leveraging Building Energy Management Systems (BEMS) and Internet of Things (IoT) sensors to collect granular, real-time data on energy consumption (electricity, gas, water), indoor environmental parameters (temperature, humidity, CO2), equipment status (run-times, setpoints, pressures), and occupancy patterns.
- Establishing Baselines and Targets: Developing a clear understanding of the building’s typical energy consumption profile and establishing realistic, data-driven performance targets. These baselines can be dynamic, adjusting for weather or occupancy variations.
- Automated Fault Detection and Diagnostics (FDD): Implementing software solutions, often integrated with BEMS, that use advanced algorithms and machine learning to automatically analyze operational data. FDD systems can identify common faults (e.g., simultaneous heating and cooling, oscillating controls, inefficient fan operation) and alert operators, often with proposed corrective actions, long before these issues become apparent through manual observation or lead to comfort complaints. This prevents energy waste from compounding over time.
- Measurement and Verification (M&V) Protocols: Applying standardized M&V methodologies (e.g., IPMVP – International Performance Measurement and Verification Protocol) to quantify the actual energy savings achieved from specific retrofits or operational changes. This provides credible data for evaluating energy performance contracts and demonstrating ROI.
- Performance Dashboards and Reporting: Visualizing key performance indicators (KPIs) through intuitive dashboards that provide actionable insights to building operators, facility managers, and even occupants. Regular reporting on energy performance trends, deviations from targets, and the impact of implemented changes helps maintain focus on efficiency.
- Feedback Loops for Operations and Maintenance: Integrating monitoring data into daily operational routines. This means using real-time data to adjust schedules, fine-tune setpoints, prioritize maintenance tasks based on detected inefficiencies, and inform future operational strategies.
Continuous monitoring and robust performance verification create a powerful feedback loop that allows building performance to be perpetually refined. By actively tracking, analyzing, and responding to operational data, facility managers can ensure that buildings not only meet but consistently exceed their energy performance expectations, thus systematically closing the performance gap throughout their operational lifespan.
6.5 Adaptive Management and Learning
The building performance gap underscores that buildings are not static entities but complex, dynamic systems that evolve over time in response to occupancy, external conditions, and technology. An effective strategy for bridging this gap is to adopt an adaptive management approach, treating the building as a living system that requires continuous learning, adjustment, and optimization.
Key principles of adaptive management and learning in the context of building performance include:
- Iterative Process: Recognizing that optimizing building performance is an ongoing, cyclical process of planning, implementing, monitoring, evaluating, and adjusting. It’s not a ‘set and forget’ approach but a commitment to continuous improvement.
- Data-Driven Decisions: Basing operational adjustments and capital expenditure decisions on real, verifiable performance data collected through continuous monitoring and POE. This moves away from assumptions or ‘rules of thumb’ to evidence-based optimization.
- Organizational Learning: Fostering a culture within the building owner and facility management teams that embraces learning from operational experience. This involves documenting lessons learned, sharing best practices, and incorporating insights from POE into future design guidelines and operational protocols.
- Flexibility and Responsiveness: Designing and operating buildings with an inherent degree of flexibility that allows for adaptation to changing occupant needs, technological advancements, and evolving climate conditions. This might involve modular systems, reconfigurable spaces, or control systems that can be easily reprogrammed.
- Feedback Integration Across Lifecycle: Ensuring that feedback from the operational phase (POE, continuous monitoring data) is systematically fed back to the design and construction teams for future projects. This closes the knowledge loop, preventing the recurrence of common design flaws or construction issues.
- Training and Upskilling: Investing in the continuous training and professional development of facility management staff, equipping them with the skills to utilize advanced BEMS, interpret data analytics, and implement sophisticated energy-saving strategies. Their expertise is crucial for truly ‘tuning’ the building.
- Collaboration Beyond Handover: Maintaining lines of communication and collaboration between the original design/construction team and the operations team long after the building is handed over. This ongoing dialogue can provide valuable insights for resolving persistent issues and optimizing performance.
By adopting an adaptive management philosophy, building stakeholders acknowledge the inherent uncertainty and complexity of building performance. They commit to a proactive, learning-oriented approach that continually seeks to understand, improve, and fine-tune the building’s energy consumption and overall functionality, thereby making significant strides in closing and keeping closed the performance gap.
Many thanks to our sponsor Focus 360 Energy who helped us prepare this research report.
7. Policy and Regulatory Frameworks
While technological advancements and improved industry practices are crucial for bridging the performance gap, supportive policy and regulatory frameworks play an indispensable role in incentivizing, standardizing, and ultimately mandating higher levels of operational energy performance. Without robust policy drivers, the adoption of best practices can remain sporadic and voluntary.
7.1 Performance-Based Building Codes vs. Prescriptive Codes
Historically, many building codes have been prescriptive, dictating specific materials, insulation levels, or equipment efficiencies. While these codes provide a baseline, they often do not guarantee actual operational performance. The trend is shifting towards performance-based codes, which set overall energy consumption targets for buildings, allowing designers and builders flexibility in how they achieve those targets, but placing greater emphasis on verified outcomes. For instance, requiring a building to meet a certain energy use intensity (EUI) or a percentage reduction in CO2 emissions shifts the focus from inputs to outputs. However, the challenge lies in the enforcement and verification of these performance targets post-occupancy, which is where the performance gap often emerges.
7.2 Energy Performance Certificates (EPCs) and Disclosure Requirements
Many countries have implemented Energy Performance Certificates (EPCs) or similar rating systems (e.g., LEED, BREEAM, Green Star) that rate a building’s energy efficiency. While these are valuable for raising awareness and providing a comparative metric, they often suffer from limitations: they typically assess ‘design energy’ or ‘asset rating’ based on standardized assumptions, rather than actual operational energy consumption. This means a building with a high EPC rating at design might still have a significant performance gap in reality. To address this, policies are evolving to include mandatory operational energy disclosure. For example, NABERS (National Australian Built Environment Rating System) in Australia and Display Energy Certificates (DECs) in the UK require buildings to disclose their actual measured energy consumption. Such policies create transparency, incentivize owners to manage their buildings more efficiently, and provide a clear metric against which to measure the performance gap.
7.3 Incentives for Performance and Retrofits
Governments and public bodies can provide financial and non-financial incentives to encourage bridging the performance gap. These may include:
- Tax Credits and Rebates: Offering tax credits, grants, or rebates for verifiable energy efficiency improvements, particularly those that address the operational performance gap through advanced BEMS, comprehensive commissioning, or deep retrofits.
- Performance-Based Grants: Tying financial incentives not just to the installation of energy-efficient technologies, but to the demonstrated achievement of actual energy savings over a period.
- Green Building Loan Programs: Providing favorable financing terms for projects that commit to and achieve high operational energy performance standards.
- Carbon Pricing and Emissions Trading Schemes: While broader in scope, these mechanisms create an economic incentive for buildings to reduce their energy consumption and associated emissions.
7.4 Mandates for Commissioning and POE
Some progressive building codes and green building standards are beginning to mandate not just initial commissioning but also ongoing commissioning and formal Post-Occupancy Evaluations for certain building types or sizes. Making these processes a regulatory requirement, rather than optional, ensures that buildings are systematically tuned and their performance regularly assessed, thereby embedding quality assurance throughout the lifecycle. Policies could also require documented occupant training and the provision of user-friendly operational guides as part of the building handover.
By implementing and strengthening these policy and regulatory frameworks, governments can create a market environment where bridging the performance gap is not just a best practice but a fundamental expectation and, increasingly, a legal requirement, driving widespread change across the built environment.
Many thanks to our sponsor Focus 360 Energy who helped us prepare this research report.
8. Conclusion
The performance gap, representing the persistent and often substantial disparity between a building’s predicted energy consumption and its actual operational energy use, stands as a critical impediment to global energy efficiency and sustainability ambitions. This comprehensive analysis has illuminated its multifaceted origins, stemming from optimistic design assumptions, deficiencies in construction quality, inadequate commissioning processes, and the inherent variability of occupant behavior, further compounded by systemic operational and maintenance challenges. The cumulative effect of these factors undermines the effectiveness of significant investments in energy-efficient design and technology, leading to elevated operational costs and a larger environmental footprint.
Addressing this complex phenomenon necessitates a holistic, integrated, and continuous approach that spans the entire building lifecycle. It begins with fostering genuine collaboration among all stakeholders – from architects and engineers to contractors, owners, and end-users – ensuring that energy performance targets are clearly defined, mutually understood, and rigorously pursued from the initial design phase. This collaborative ethos is best embodied through frameworks like Integrated Project Delivery and Soft Landings, which extend team involvement well into the post-occupancy period.
Rigorous quality control during construction, coupled with comprehensive and continuous commissioning, is paramount to translating design intent into built reality and maintaining optimal system performance over time. These processes ensure that building systems are installed correctly, operate as intended, and are consistently tuned for efficiency. Crucially, the deployment of advanced diagnostic tools, such as BEMS, IoT sensors, and sophisticated data analytics, provides the real-time, granular data necessary for identifying inefficiencies, diagnosing faults, and driving intelligent, adaptive operational adjustments. These technologies empower facility managers to proactively manage energy consumption and respond dynamically to changing conditions.
Recognizing the profound impact of human factors, effective occupant engagement is not merely an auxiliary consideration but a core strategy. This involves not only training and educating occupants on energy-efficient behaviors but also establishing robust feedback mechanisms and implementing nuanced behavioral change interventions. By empowering and involving occupants, their actions can shift from being a source of the performance gap to a vital component of its solution.
Finally, supportive policy and regulatory frameworks, evolving from prescriptive mandates to performance-based outcomes and mandatory operational disclosure, are essential for creating the market conditions that incentivize and enforce superior building performance. These policies drive accountability and accelerate the adoption of best practices across the industry.
In essence, bridging the performance gap is not a one-time fix but an ongoing journey of learning, adaptation, and continuous improvement. It demands a paradigm shift in how buildings are designed, constructed, operated, and managed, moving towards a truly performance-driven culture. By systematically implementing these integrated strategies, stakeholders can significantly enhance building performance, unlock the full potential of energy-efficient designs, achieve critical sustainability goals, and ultimately contribute to a more resilient, comfortable, and environmentally responsible built environment for generations to come.
Many thanks to our sponsor Focus 360 Energy who helped us prepare this research report.
The discussion of occupant behavior as a key factor is particularly insightful. Could exploring the impact of personalized environmental controls, allowing occupants to adjust lighting and temperature within defined parameters, further reduce the performance gap?
That’s a great point! Personalized environmental controls are a promising avenue. Giving occupants some agency, while maintaining overall efficiency, could lead to both energy savings and increased satisfaction. It would be interesting to research the sweet spot between individual control and building-wide optimization.
Editor: FocusNews.Uk
Thank you to our Sponsor Focus 360 Energy
So, construction quality is a huge piece of the puzzle! Ever wonder if those “minor discrepancies” in your building’s envelope are actually costing you a fortune? Time for some thermal imaging detective work!
Absolutely! The impact of seemingly small construction discrepancies is often underestimated. Thermal imaging is a powerful tool to uncover these hidden energy drains. It can reveal insulation gaps, air leaks, and thermal bridges that significantly impact building performance and energy costs. Thanks for highlighting the importance of diligent construction and diagnostic tools!
Editor: FocusNews.Uk
Thank you to our Sponsor Focus 360 Energy
This research highlights a vital point: occupant behaviour significantly impacts energy use. It would be interesting to explore strategies around real-time feedback systems, providing tailored, actionable insights to occupants to promote more energy-conscious decisions and reduce consumption.
That’s an excellent point! Real-time feedback is key. Imagine if building dashboards showed occupants their energy impact in relatable terms, like “You saved enough energy to power X homes today!” Making it personal and rewarding could drastically shift behavior. Let’s explore innovative feedback designs! What are your thoughts on gamification?
Editor: FocusNews.Uk
Thank you to our Sponsor Focus 360 Energy
Construction quality issues, eh? So, you’re saying my dreams of passive solar heating might be foiled by a rogue breeze whistling through a wall? Maybe I need to invest in some high-tech caulk! What are the craziest construction fails you’ve seen impacting energy use?
That’s a funny take on construction issues! High-tech caulk might be a good investment. One crazy thing I saw was a building where the insulation was installed *outside* the vapor barrier. It completely negated its effect! We need to ensure that best practices are adopted and adhered to.
Editor: FocusNews.Uk
Thank you to our Sponsor Focus 360 Energy
The emphasis on occupant behaviour is key. How can building design proactively encourage positive interactions, perhaps through intuitive interfaces or real-time feedback on energy use tied to specific actions?
That’s a fantastic question! Exploring intuitive interfaces is a game-changer. Imagine buildings with adaptive learning systems that respond to occupant preferences while optimizing energy use. We need to develop feedback loops that nudge towards sustainable choices and reward energy-conscious behaviour through positive reinforcement.
Editor: FocusNews.Uk
Thank you to our Sponsor Focus 360 Energy
Given the significance of occupant behavior, what specific design strategies could better facilitate intuitive system use and encourage greater awareness of energy consumption patterns within buildings?
That’s an important point! Design strategies that prioritize intuitive use are key. Imagine digital twins or augmented reality overlays that provide real-time feedback on energy consumption within a space, making it easier for occupants to understand their impact and adjust their behavior accordingly. Let’s discuss the potential of technology!
Editor: FocusNews.Uk
Thank you to our Sponsor Focus 360 Energy
So, if we’re pinning the performance gap on occupant behavior, are we suggesting buildings should come with a “How to be an energy-efficient human” manual? Maybe a mandatory course before getting the keys?
That’s a fun idea! While a mandatory course might be a bit much, it highlights a serious need for better user education. Perhaps interactive tutorials built into building interfaces or gamified energy-saving challenges would be a more engaging way to empower occupants and bridge the knowledge gap! What are your thoughts?
Editor: FocusNews.Uk
Thank you to our Sponsor Focus 360 Energy
A “building as a living system” requiring continuous learning? So, are we going to need to start offering buildings therapy sessions to deal with their performance anxieties? Perhaps a building-whisperer to help it communicate its needs more effectively?
That’s a hilarious analogy! It really emphasizes the need for adaptability and responsiveness in building management. Perhaps instead of therapy, we need better diagnostic tools and feedback mechanisms that help us understand the building’s ‘needs’ and optimize its performance in real time. Let’s innovate building “listening” devices!
Editor: FocusNews.Uk
Thank you to our Sponsor Focus 360 Energy
Given the research emphasis on occupant behaviour, how can designs promote intuitive interactions without compromising overall system efficiency, especially when balancing individual control with centralized optimization?
That’s a critical question! Designs could incorporate personalized dashboards providing real-time feedback on individual energy use versus building-wide averages. Gamification could play a role, rewarding collective energy savings while still allowing for individual preferences within set parameters. Further research could explore interfaces. Thanks for the prompt!
Editor: FocusNews.Uk
Thank you to our Sponsor Focus 360 Energy
So, you’re saying if my building is underperforming, I should give it a stern talking-to? Perhaps hold a building-wide intervention with all the pipes and wires? What happens if the building just gives me the cold shoulder (literally)?
Haha, love the image of a building ‘giving the cold shoulder’! It’s true, diagnosing building issues can feel like that sometimes. I think the key is to start with better communication – using data to ‘listen’ to what the building is telling us through its energy use and environmental conditions. That provides a factual basis on which to operate!
Editor: FocusNews.Uk
Thank you to our Sponsor Focus 360 Energy
The point about feedback loops is well-made. Exploring the use of AI to analyze POE data and suggest design improvements for future projects could be a key element. This would further integrate lessons learned and create a truly iterative design process.
That’s a great suggestion! Using AI to analyze POE data to improve future designs could be transformative. Imagine the potential for AI to identify patterns and correlations invisible to humans! This could lead to truly optimized, data-driven designs that anticipate and meet occupant needs while maximizing energy efficiency. It would be a real game-changer for creating sustainable buildings.
Editor: FocusNews.Uk
Thank you to our Sponsor Focus 360 Energy