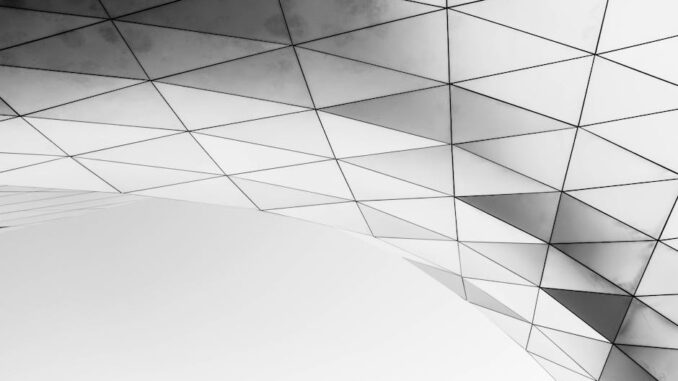
Digital Twins in Building Management: A Comprehensive Analysis
Many thanks to our sponsor Focus 360 Energy who helped us prepare this research report.
Abstract
Digital twin technology has emerged as a profoundly transformative tool in building management, extending beyond mere visualization to offer dynamic, virtual replicas of physical structures. These sophisticated models facilitate unparalleled real-time monitoring, intricate simulation, and in-depth analysis of diverse building systems, encompassing everything from foundational structural elements to complex operational parameters. This comprehensive research report delves into the multifaceted and evolving applications of digital twins within the realm of building management. It meticulously explores their intricate integration with Building Automation Systems (BAS) and pervasive Internet of Things (IoT) sensor networks, unveiling their advanced capabilities in predictive analytics for holistic energy optimization, precise identification and diagnosis of inefficiencies, and their pivotal role in comprehensively optimizing building performance across its entire lifecycle. From the initial conceptualization and rigorous design phases through construction, and into the long-term operational and maintenance stages, digital twins are reshaping the built environment. By thoroughly examining current cutting-edge practices, navigating the inherent technological and organizational challenges, and peering into the promising future prospects, this report provides an exhaustive understanding of how digital twins are not just enhancing, but fundamentally revolutionizing the planning, execution, and sustainment of modern buildings.
Many thanks to our sponsor Focus 360 Energy who helped us prepare this research report.
1. Introduction
The advent and rapid maturation of digital twin technology mark a significant paradigm shift across numerous industries, with the architecture, engineering, construction, and operations (AECO) sector, particularly building management, standing as a primary and highly impactful beneficiary. Fundamentally, a digital twin transcends a static digital model; it is a dynamic, virtual representation of a physical object, system, or process, meticulously engineered to mirror its real-world counterpart’s behavior, performance, and state in real-time. This sophisticated replication is achieved through a continuous, bidirectional data flow between the physical asset and its digital counterpart, enabling unprecedented levels of insight, prediction, and control. The concept, initially conceptualized by Dr. Michael Grieves in 2002 and later championed by NASA for spacecraft design and maintenance, has evolved rapidly, driven by advancements in computational power, sensor technology, and data analytics. (Wang et al., 2023)
In the intricate context of building management, a digital twin integrates vast streams of data from disparate sources, including comprehensive Building Information Modeling (BIM) data, live telemetry from Building Automation Systems (BAS), and a ubiquitous network of Internet of Things (IoT) sensors. This intricate aggregation coalesces into a holistic, dynamic, and interactive model of a building’s entire array of systems and operational nuances. Such profound integration empowers facility managers, building owners, and various stakeholders to not only monitor and analyze building performance in real-time but also to proactively optimize it. The resultant benefits are manifold, leading to significantly enhanced operational efficiency, substantial improvements in environmental sustainability, and ultimately, superior occupant comfort and well-being. The convergence of these technologies provides a powerful tool for navigating the increasing complexity of modern buildings, which are characterized by intricate mechanical, electrical, plumbing (MEP) systems, diverse occupancy patterns, and stringent energy efficiency demands.
The core value proposition of a digital twin in building management lies in its ability to bridge the gap between the physical and digital worlds. It creates a living, evolving replica that can be used for various purposes: simulating future scenarios, testing hypothetical changes without disrupting physical operations, diagnosing issues remotely, and predicting potential failures before they occur. This predictive and proactive capability is a significant leap forward from traditional reactive management approaches. The digital twin essentially becomes a ‘single source of truth’ for all building-related data, providing an unparalleled holistic view that fosters informed decision-making and strategic planning throughout the building’s entire lifecycle.
Many thanks to our sponsor Focus 360 Energy who helped us prepare this research report.
2. Integration with Building Automation Systems and IoT Sensors
The foundational strength and utility of a building’s digital twin are inherently dependent on its ability to ingest, process, and correlate vast quantities of real-time data from its physical counterpart. This crucial data stream is predominantly facilitated through deep integration with Building Automation Systems (BAS) and extensive networks of Internet of Things (IoT) sensors. These two pillars provide the constant pulse of information that animates the virtual model, transforming it from a static blueprint into a dynamic, responsive entity.
2.1. Building Automation Systems (BAS)
Building Automation Systems (BAS), often referred to as Building Management Systems (BMS), represent the nervous system of modern commercial and large residential buildings. They are centralized, computer-based control systems designed to monitor and manage a building’s mechanical, electrical, and plumbing (MEP) equipment. This includes, but is not limited to, sophisticated heating, ventilation, and air conditioning (HVAC) systems, intricate lighting controls, fire alarm systems, security access control, and increasingly, elevator operations and power management. The typical architecture of a BAS comprises field devices (sensors and actuators), controllers (which process data and send commands), and a central supervisory workstation or server that provides a user interface for monitoring and control.
Integrating digital twins with BAS establishes a profound synergy, creating a comprehensive and nuanced view of a building’s operational heartbeat. Real-time data from BAS, encompassing parameters such as air temperature, pressure differentials, fluid flow rates, fan speeds, damper positions, light levels, and equipment runtimes, is continuously streamed into the digital twin. This rich stream of operational data allows the digital twin to accurately reflect the current state and performance of the physical building’s core systems. For instance, by continuously analyzing data points from the HVAC system via the BAS, the digital twin can instantly identify deviations from optimal performance, detect anomalies (e.g., a pump drawing unusually high current, a valve failing to close fully), and even predict potential equipment failures based on performance degradation trends. This real-time diagnostic capability enables facility managers to initiate proactive corrective actions, significantly enhancing operational efficiency by preventing breakdowns, reducing unscheduled downtime, and optimizing resource allocation. The digital twin can also simulate the impact of proposed changes to BAS programming before they are implemented physically, mitigating risks and ensuring desired outcomes. Furthermore, the digital twin can act as a command center, sending optimized setpoints and operational directives back to the BAS controllers in a closed-loop feedback mechanism, thereby allowing for truly intelligent and adaptive building control.
Different BAS typically communicate using standardized protocols like BACnet (Building Automation and Control Network), LonWorks, and Modbus. The interoperability challenges of these diverse protocols often necessitate middleware or API layers to translate and normalize the data before it can be effectively consumed by the digital twin platform. Overcoming these integration hurdles is paramount for a fully functional and insightful digital twin.
2.2. Internet of Things (IoT) Sensors
While BAS provides critical operational data from core building systems, Internet of Things (IoT) sensors augment this data with granular, pervasive insights into a multitude of environmental and occupancy parameters. IoT sensors are physical devices embedded with sensors, processing capabilities, and communication modules that enable them to collect and transmit data over a network, often wirelessly. They play an exceptionally crucial role in enhancing the functionality and precision of digital twins by providing continuous, granular streams of data that would be impractical or impossible to collect solely through traditional BAS. This data encompasses a wide array of parameters, including but not limited to, highly localized temperature and humidity readings, indoor air quality metrics (such as CO2 levels, Volatile Organic Compounds (VOCs), particulate matter (PM2.5/PM10)), light intensity, acoustic levels, detailed occupancy patterns (presence, count, movement), water leak detection, vibration analysis for structural health, and even asset tracking.
The sheer volume, velocity, and variety of data generated by a dense network of IoT sensors feed continuously into the digital twin model. This continuous influx allows for extremely detailed analysis and sophisticated simulation of building systems and human-building interactions. The integration of IoT sensors with digital twins facilitates a paradigm shift towards truly proactive maintenance, highly granular energy optimization, and significantly improved occupant comfort and productivity. For example, precise occupancy sensors, deployed strategically throughout a building, can inform HVAC and lighting systems to dynamically adjust settings based on real-time usage patterns at a zone or even room level. This adaptive control can lead to substantial energy savings by preventing the conditioning or lighting of unoccupied spaces, while simultaneously ensuring optimal conditions for occupied areas. Similarly, air quality sensors can trigger ventilation adjustments to maintain healthy indoor environments, preventing the buildup of pollutants and enhancing occupant well-being.
The integration process often involves careful planning of sensor deployment, robust wireless network infrastructure (e.g., Wi-Fi, Bluetooth Low Energy (BLE), LoRaWAN, Zigbee, cellular 5G), and secure data ingestion pipelines. The concept of edge computing is also increasingly vital here, where some data processing occurs directly at the sensor or gateway level, reducing the volume of data sent to the cloud and decreasing latency for critical responses. This distributed intelligence enhances the real-time responsiveness of the digital twin.
By combining the macro-level operational data from BAS with the micro-level environmental and occupancy data from IoT sensors, the digital twin achieves an unprecedented level of situational awareness, enabling highly precise control, predictive capabilities, and a truly responsive built environment.
Many thanks to our sponsor Focus 360 Energy who helped us prepare this research report.
3. Predictive Analytics for Energy Optimization
Energy consumption is often the single largest operational cost in commercial buildings, and it also represents a significant portion of their environmental footprint. Digital twin technology, powered by advanced predictive analytics, offers a revolutionary approach to energy management, moving beyond historical analysis to proactive optimization and forecasting. This capability is pivotal for achieving sustainability goals, reducing operational expenditures, and enhancing building value.
3.1. Energy Consumption Modeling
Digital twins enable the creation of highly detailed and dynamic energy consumption models by aggregating and synthesizing vast datasets from various building systems, environmental sensors, and external data sources. These models are not merely static representations but sophisticated computational constructs that simulate energy usage patterns under a multitude of dynamic conditions. The precision of these models is derived from their ability to integrate granular data, including: real-time electricity, gas, and water consumption; operational data from HVAC systems (e.g., fan speeds, chiller loads, boiler efficiency); lighting system performance; building envelope properties (U-values, solar heat gain coefficients); occupancy schedules and real-time density; external weather conditions (temperature, humidity, solar radiation, wind speed); and even historical energy billing data.
Two primary methodologies underpin energy consumption modeling within digital twins: physics-based modeling and data-driven modeling, often combined in hybrid approaches. Physics-based models, frequently leveraging established energy simulation software like EnergyPlus or DOE-2 integrated with the digital twin platform, use detailed geometric and material properties of the building, along with thermodynamic principles, to predict energy flows. Data-driven models, on the other hand, employ advanced machine learning algorithms (e.g., regression analysis, neural networks, support vector machines) to learn complex relationships between building operational parameters, environmental conditions, and energy consumption from historical and real-time data. These models can identify intricate patterns and correlations that might not be immediately apparent through traditional analysis.
By analyzing these rich, multi-layered models, facility managers gain unparalleled insights into potential inefficiencies, sources of energy waste, and specific areas ripe for improvement. For example, the model might reveal that a particular HVAC zone experiences excessive heating or cooling demand due to suboptimal thermostat settings during low-occupancy periods, or that specific facade elements contribute disproportionately to heat gain. This granular insight allows for the implementation of highly targeted strategies to optimize energy consumption, such as dynamic adjustment of HVAC setpoints based on real-time occupancy and weather forecasts, intelligent scheduling of lighting and plug loads, or identifying optimal times for pre-cooling/pre-heating the building to leverage off-peak electricity tariffs. Furthermore, the digital twin can visualize these complex energy flows through intuitive dashboards, heatmaps, and 3D renderings, making otherwise abstract data actionable and understandable.
3.2. Scenario Simulation and Forecasting
One of the most powerful capabilities of digital twins in energy optimization is their ability to perform sophisticated scenario simulations and accurate energy forecasting. This moves beyond simply understanding current consumption to proactively predicting future energy needs and evaluating the impact of potential changes before any physical intervention is made. This ‘what-if’ analysis is critical for strategic decision-making and capital expenditure planning.
Digital twins allow facility managers and energy strategists to simulate a myriad of scenarios. Beyond evaluating the impact of energy-efficient lighting upgrades or new HVAC systems, these simulations can explore:
* The integration of renewable energy sources (e.g., assessing the optimal size and placement of rooftop solar photovoltaic panels or small wind turbines, and their contribution to reducing grid reliance).
* Participation in smart grid demand-response programs (simulating how shifting or shedding loads during peak periods affects energy bills and grid stability).
* The effect of changes in building occupancy patterns or operational schedules (e.g., adapting to hybrid work models or extended operating hours).
* The energy impact of building envelope improvements, such as upgrading insulation, replacing windows, or installing dynamic shading systems.
* Evaluating the financial implications and return on investment (ROI) for various energy conservation measures (ECMs) by projecting energy cost savings over the lifespan of the intervention.
These simulations are often driven by advanced optimization algorithms, including genetic algorithms, particle swarm optimization, or reinforcement learning, which can autonomously explore vast numbers of operational parameters to identify optimal control strategies for energy efficiency. For instance, a reinforcement learning agent within the digital twin could learn the most energy-efficient sequences for HVAC startup and shutdown, or the optimal setpoints to maintain comfort with minimal energy use under varying external conditions.
Energy forecasting, an integral part of this capability, leverages historical data and predictive models to anticipate future energy consumption. This helps in budget planning, identifying unusual consumption spikes, and optimizing energy procurement strategies. The accuracy of these forecasts is influenced by data quality, model complexity, and the precision of external data like weather predictions. By providing valuable insights into potential energy savings, carbon emission reductions, and financial returns, this capability supports informed, strategic planning for long-term energy management and contributes significantly to achieving corporate sustainability goals and complying with evolving environmental regulations.
Many thanks to our sponsor Focus 360 Energy who helped us prepare this research report.
4. Identification of Inefficiencies and Performance Optimization
Beyond energy management, digital twins are instrumental in the broader identification and rectification of inefficiencies across all facets of building performance, ultimately leading to holistic optimization. Their ability to fuse diverse data streams and apply advanced analytical techniques transforms raw data into actionable intelligence, enabling proactive management rather than reactive troubleshooting.
4.1. Anomaly Detection and Fault Diagnosis
Traditional building management often relies on manual inspections or reactive responses to alarms. Digital twins revolutionize this approach by continuously monitoring building systems in real-time, enabling sophisticated anomaly detection and precise fault diagnosis. This capability is paramount for preventing costly breakdowns, minimizing energy waste, and ensuring consistent operational efficiency.
By establishing a baseline of normal operating behavior for each system and component through historical data analysis, digital twins can immediately flag deviations. These deviations, or anomalies, can be subtle and indicative of nascent issues, far before they escalate into critical failures. For example, a digital twin can identify a slight but persistent increase in a pump’s vibration signature, a gradual rise in motor temperature, or an air-handling unit (AHU) consuming more power than usual for a given airflow. The example of a 33-story building cited in the original article, where a digital twin identified an AHU running continuously at night despite not being needed, perfectly illustrates this capability. This early detection allows for timely corrective actions, such as recalibrating sensors, performing preventative maintenance on a degrading component, or adjusting control sequences.
Advanced anomaly detection techniques employed by digital twins go beyond simple thresholding. They leverage statistical process control, machine learning algorithms (e.g., unsupervised learning for clustering normal vs. anomalous behavior, time-series anomaly detection), and rule-based expert systems to identify complex patterns indicative of faults. When an anomaly is detected, the digital twin’s integrated data model facilitates rapid root cause analysis. Instead of merely alerting to ‘HVAC inefficiency’, it can pinpoint the exact cause: a ‘stuck damper’ in zone 3, a ‘fouled coil’ in AHU-5, or a ‘miscalibrated temperature sensor’ in office B201. This level of precision significantly reduces the time and resources required for troubleshooting, allowing technicians to arrive on-site with a clear understanding of the problem and the necessary tools or parts.
The benefits extend to reduced energy waste (by fixing inefficiencies promptly), lower operational costs (by minimizing emergency repairs and optimizing maintenance schedules), increased equipment lifespan (through preventative interventions), and improved occupant comfort (by ensuring systems operate optimally without undetected faults). This proactive fault diagnosis shifts building management from a reactive ‘fix-when-broken’ model to a predictive ‘prevent-before-failure’ paradigm.
4.2. Space Utilization Analysis
Optimizing space utilization is a critical concern for building owners and facility managers, impacting operational costs, occupant comfort, productivity, and future planning. Digital twins provide unprecedented capabilities for analyzing space utilization patterns by integrating real-time data from various sources, offering dynamic insights into how spaces are actually being used.
The primary data sources for space utilization analysis include:
* Occupancy sensors: These can range from passive infrared (PIR) sensors detecting presence, to ultrasonic sensors, camera-based vision systems (often employing anonymized data for privacy), Wi-Fi triangulation, and Bluetooth Low Energy (BLE) beacons that track device density.
* Access control systems: Data on entry and exit times, and frequency of use for various zones.
* Desk booking systems: Information on scheduled workspace usage.
* Indoor positioning systems (IPS): More advanced systems that can track movement paths within a building.
By aggregating and analyzing this data, digital twins can generate key metrics and visualizations:
* Occupancy rates: Real-time and historical percentages of occupied vs. available space.
* Desk and meeting room utilization: Identifying underutilized desks or constantly booked meeting rooms.
* Peak vs. average utilization: Understanding demand fluctuations throughout the day, week, or season.
* Flow analysis: Mapping occupant movement patterns, identifying bottlenecks or underutilized pathways.
The applications of this analysis are extensive:
* Workspace Optimization: Businesses can optimize their office layouts, implement flexible seating arrangements (hot-desking or hybrid models), or reconfigure collaborative spaces based on actual usage. This can lead to significant reductions in real estate costs or allow for increased headcount within the same footprint.
* Facility Planning: Insights into underutilized floors or zones can inform decisions on whether to expand, consolidate, or repurpose spaces. It can guide capital investment in new amenities or renovations where demand is highest.
* Occupant Comfort and Productivity: By understanding real-time density, facility managers can adjust environmental controls (HVAC, lighting) to maintain optimal comfort levels per zone. For example, higher CO2 levels in a densely occupied meeting room can trigger increased ventilation.
* Operational Efficiency: Cleaning schedules can be dynamically adjusted based on actual usage, rather than fixed routines, leading to more efficient resource allocation. Security patrols can be optimized based on real-time activity levels.
* Wayfinding and Smart Navigation: Future integrations could use real-time occupancy data to guide occupants to available desks, meeting rooms, or less crowded routes within the building, enhancing overall user experience.
By moving beyond static design assumptions to dynamic, data-driven understanding of space usage, digital twins empower organizations to create more efficient, responsive, and occupant-centric environments that truly align with evolving business needs and occupant preferences.
Many thanks to our sponsor Focus 360 Energy who helped us prepare this research report.
5. Lifecycle Management: From Design to Operation and Maintenance
The true transformative power of digital twins in building management lies in their ability to provide continuous value throughout the entire lifecycle of a building, extending from its conceptualization and design through construction, and into its long-term operational and maintenance phases. This comprehensive oversight fosters greater efficiency, reduces costs, enhances sustainability, and ensures optimal performance at every stage.
5.1. Design and Construction Phases
During the initial design and subsequent construction phases, digital twins serve as powerful tools for advanced simulation, rigorous scenario testing, and meticulous validation, fundamentally transforming traditional building project workflows. The cornerstone of a construction-phase digital twin is often a highly detailed Building Information Model (BIM). BIM, itself a digital representation of a building’s physical and functional characteristics, provides the rich geometric, semantic, and relational data that forms the initial backbone of the digital twin. It includes information on architectural elements, structural components, MEP systems, materials, and their properties.
Architects and engineers leverage these foundational BIM models, which evolve into the nascent digital twin, to conduct a wide array of simulations and analyses before any physical construction begins. This proactive approach is critical for identifying and mitigating potential issues early, thereby preventing costly rework, delays, and design flaws later in the project lifecycle. Key simulation capabilities include:
- Energy Performance Optimization: Detailed energy simulations can assess daylighting strategies, thermal performance of different facade materials, and the efficiency of various HVAC system configurations. This ensures the building is designed from the ground up for optimal energy efficiency and sustainability targets.
- Structural Analysis: Simulating structural integrity under various loads (e.g., wind, seismic, occupancy) to ensure safety and material optimization.
- Daylighting and Occupant Comfort Analysis: Evaluating natural light penetration, glare potential, and thermal comfort zones to optimize window placement, shading devices, and internal layouts.
- Acoustic Modeling: Predicting sound propagation and reverberation to ensure optimal acoustic environments for different spaces.
- Egress and Fire Safety Simulation: Simulating occupant evacuation routes and fire spread scenarios to ensure compliance with safety codes and optimize emergency procedures.
- Constructability Analysis and Clash Detection: By integrating models from various disciplines (architectural, structural, MEP), the digital twin can automatically detect clashes or conflicts between different building systems (e.g., a pipe running through a structural beam). This prevents costly on-site rework and streamlines construction workflows.
- 4D and 5D Simulation: Integrating project schedule (4D) and cost (5D) data into the digital twin allows for visualization of construction progress over time, identification of potential schedule conflicts, and real-time cost tracking, improving project predictability and financial control.
Beyond simulation, digital twins facilitate enhanced collaboration among all project stakeholders – architects, engineers, contractors, subcontractors, and owners. The shared, integrated model acts as a single source of truth, improving communication, reducing misinterpretations, and accelerating decision-making. Virtual commissioning, where building systems are simulated to operate before physical installation, can identify control logic errors or operational inefficiencies, ensuring a smoother handover to the operational phase. For projects employing pre-fabrication or modular construction, the digital twin can optimize the assembly process, track module delivery, and manage installation sequences. Ultimately, by embedding performance parameters and operational data into the model from the earliest stages, digital twins ensure that the building is not only structurally sound and aesthetically pleasing but also optimized for long-term performance, efficiency, and user comfort upon completion.
5.2. Operational Phase
Once a building is constructed and occupied, the digital twin transforms into an indispensable, dynamic tool for day-to-day facility management and continuous performance optimization. This is the phase where the digital twin truly ‘comes alive’, leveraging its persistent connection to the physical asset to provide real-time intelligence and enable adaptive control.
In the operational phase, the digital twin acts as a central nervous system, integrating live data streams from BAS, an extensive network of IoT sensors, and potentially other enterprise systems (e.g., CMMS, occupant feedback platforms). This continuous influx of data allows for:
- Real-time Monitoring and Visualization: Facility managers gain access to comprehensive, intuitive dashboards that display key performance indicators (KPIs) for energy consumption, indoor air quality, occupancy levels, system status, and more. These dashboards often feature 3D models of the building, allowing users to drill down into specific zones, rooms, or even individual pieces of equipment, visualizing their real-time status and performance. This holistic view enables immediate identification of operational anomalies or suboptimal conditions.
- Adaptive Control and Optimization: Beyond simple monitoring, the digital twin can leverage predictive analytics and AI/ML algorithms to implement dynamic, adaptive control strategies. For instance, based on real-time occupancy data, predicted weather changes, and energy price forecasts, the digital twin can send optimized setpoints and operational commands back to the BAS. This might include pre-cooling a building during off-peak hours to reduce peak demand, adjusting ventilation rates based on actual CO2 levels, or dimming lights in unoccupied areas. This continuous optimization ensures the building operates at peak efficiency while maintaining desired comfort levels.
- Predictive Maintenance (detailed in next section): Proactively identifying potential equipment failures before they occur, reducing downtime and maintenance costs.
- Enhanced Occupant Experience: Digital twins can contribute significantly to occupant satisfaction. Through integrations with tenant experience platforms, occupants might personalize their comfort settings (temperature, lighting) within their zone, book meeting rooms based on real-time availability, or navigate the building more efficiently. The twin can also provide real-time information on air quality or crowded areas, enhancing well-being and safety.
- Regulatory Compliance and Reporting: Digital twins can automatically collect and consolidate data required for energy performance certificates, air quality regulations, and other compliance reporting, simplifying audit processes and ensuring adherence to standards.
- Security and Safety Management: Integrating with security systems allows for real-time monitoring of access points, alarm verification, and even simulation of emergency scenarios to optimize response plans.
By providing a comprehensive, dynamic, and integrated view of building operations, digital twins support highly informed decision-making, significantly enhance operational efficiency, reduce energy waste, extend asset lifespan, and ultimately improve the satisfaction and productivity of building occupants. They enable a shift from reactive problem-solving to proactive, intelligent building management.
5.3. Maintenance Phase
In the maintenance phase, digital twins elevate traditional maintenance practices from reactive and time-based approaches to sophisticated predictive and prescriptive strategies. This results in significant cost savings, reduced downtime, extended asset lifespan, and improved operational reliability.
-
Predictive Maintenance Strategies: This is where the digital twin truly shines. By continuously analyzing real-time operational data from BAS and IoT sensors (e.g., vibration, temperature, current draw, pressure, runtime hours) against historical performance trends and manufacturer specifications, the digital twin can predict when a component or system is likely to fail. Machine learning models (e.g., time-series forecasting, regression, classification models trained on failure patterns) are employed to identify subtle anomalies or gradual degradation that indicate impending failure. For example, a digital twin might detect a slight increase in vibration amplitude from a fan motor over several weeks, correlating it with an impending bearing failure, long before any audible signs or catastrophic breakdown occurs.
This predictive capability allows facility managers to shift from scheduled maintenance (which might occur too early or too late) or reactive breakdown maintenance (which is often costly and disruptive) to ‘just-in-time’ maintenance. This means maintenance can be scheduled precisely when it is needed, minimizing downtime and maximizing the useful life of assets.
-
Prescriptive Maintenance: Building on predictive insights, the digital twin can often go a step further to recommend the optimal course of action. This is known as prescriptive maintenance. For example, if a specific HVAC unit is predicted to fail in two months, the digital twin might suggest the most cost-effective solution (e.g., repair vs. replace), identify the necessary spare parts from inventory, and recommend the best time to schedule the maintenance to minimize disruption to building occupants and operations. It can even suggest the most qualified technician based on their skill set and availability.
-
Asset Management and Digital History: The digital twin acts as a comprehensive, living repository for all asset-related information. This includes detailed specifications, installation dates, warranty information, maintenance history (repairs, replacements, calibrations), service contracts, and performance logs. When a technician accesses a specific asset’s digital twin, they instantly have access to its complete history, enabling more informed troubleshooting and repair. This centralized and accessible information significantly streamlines maintenance workflows.
-
Augmented Reality (AR) for Technicians: An emerging and powerful application involves integrating the digital twin with Augmented Reality (AR) technologies. Field technicians can use AR-enabled tablets or smart glasses to overlay the digital twin’s data directly onto the physical equipment they are servicing. This means they can see real-time sensor readings, repair instructions, historical data, and even interactive 3D schematics projected onto the physical asset, significantly improving diagnostic speed, accuracy, and efficiency during maintenance tasks. It also aids in training new technicians.
-
Inventory Optimization: By accurately predicting maintenance needs, digital twins help optimize spare parts inventory management. This reduces the need for large, costly inventories while ensuring that critical parts are available when needed, minimizing delays in repairs. This precision also reduces capital tied up in inventory and avoids obsolescence.
In essence, digital twins transform maintenance from a necessary evil into a strategic advantage, ensuring building systems operate reliably, efficiently, and cost-effectively throughout their entire lifespan.
Many thanks to our sponsor Focus 360 Energy who helped us prepare this research report.
6. Challenges and Considerations
While the transformative potential of digital twins in building management is immense, their successful implementation and long-term viability are contingent upon addressing several significant challenges and considerations. These span technical, organizational, ethical, and economic dimensions, requiring careful planning and robust solutions.
6.1. Data Integration and Interoperability
Perhaps the most pervasive and complex challenge in establishing a fully functional digital twin for buildings is the monumental task of data integration and ensuring interoperability. Modern buildings generate vast amounts of data from a multitude of disparate sources, each often operating with its own proprietary format, communication protocol, and data structure. This includes:
- Building Information Modeling (BIM) data: Often in various software-specific formats (e.g., Revit, ArchiCAD) and typically static once exported.
- Building Automation System (BAS) data: Real-time operational data, often utilizing proprietary or specific industrial protocols (e.g., BACnet, LonWorks, Modbus, KNX). BAS data frequently comes with vendor-specific APIs or closed ecosystems.
- Internet of Things (IoT) sensor data: Generated by a wide array of devices from different manufacturers, using diverse wireless protocols (Wi-Fi, Bluetooth, LoRaWAN, Zigbee, cellular) and varying data payloads.
- Enterprise systems data: Information from Computerized Maintenance Management Systems (CMMS), Enterprise Resource Planning (ERP) systems, space management software, and security systems.
- External data: Weather forecasts, energy grid data, public transport schedules, etc.
Integrating this mosaic of data into a cohesive, synchronized, and actionable digital twin model is a formidable technical hurdle. The primary issues include:
- Data Silos: Information is often trapped in isolated systems, making it difficult to access and combine.
- Lack of Standardization: Different systems use varying naming conventions, units of measurement, and data models. A temperature reading from one sensor might be in Fahrenheit, another in Celsius, and a third might simply output a raw voltage value. This necessitates extensive data harmonization, cleaning, and transformation processes.
- Proprietary Systems: Many legacy BAS and equipment operate on closed, proprietary platforms, making it challenging to extract data or integrate with third-party solutions without specialized gateways or significant development effort.
- Data Quality: Inconsistent, missing, or erroneous data from sensors or systems can severely compromise the accuracy and reliability of the digital twin. Sensor drift, calibration issues, and communication errors are common problems that require robust data validation and cleaning pipelines.
- Semantic Interoperability: Beyond technical formats, ensuring that the meaning of data is consistent across systems is crucial. For example, ‘Occupancy’ might mean different things in a security system versus an HVAC control system.
Addressing these challenges requires a multifaceted approach:
- Standardization Efforts: Adopting and promoting industry standards such as IFC (Industry Foundation Classes) for BIM data, Brick Schema and Project Haystack for semantic tagging of building equipment and sensor data, and open APIs. These standards provide a common language for describing building assets and data points.
- Middleware and Integration Platforms: Utilizing robust middleware layers, integration platforms as a service (iPaaS), or dedicated digital twin platforms that specialize in connecting disparate systems, performing data normalization, and providing unified APIs.
- Data Governance: Establishing clear policies and procedures for data ownership, access, quality assurance, maintenance, and archiving. This ensures data integrity and reliability over the long term.
- Vendor Collaboration: Encouraging greater collaboration and open interfaces from BAS and IoT manufacturers to facilitate easier data access.
Without seamless and accurate data flow, the digital twin remains a static model rather than a dynamic, intelligent replica, severely limiting its value proposition. Achieving true data interoperability is the key to unlocking the full potential of digital twins in building management (Twinview Digital Twin, 2024).
6.2. Data Security and Privacy
The implementation of digital twins, with their extensive data collection and interconnectedness, inherently introduces significant privacy, security, and ethical concerns that must be proactively addressed. The sheer volume and granularity of data gathered about a building’s operations and its occupants make it a prime target for cyber threats and raises profound questions about individual privacy.
6.2.1. Cybersecurity Risks:
Digital twins aggregate data from numerous networked devices and systems, creating a vast attack surface. Potential cyber threats include:
- Data Breaches: Sensitive operational data (e.g., energy consumption patterns, security system configurations) or personal data (e.g., occupant movement patterns, comfort preferences) could be compromised, leading to competitive disadvantage, financial loss, or reputational damage.
- System Manipulation and Sabotage: A malicious actor could gain unauthorized access to the digital twin and, through its control over connected BAS, manipulate building systems. This could range from disrupting HVAC or lighting to disabling security systems, potentially causing physical damage, discomfort, or creating unsafe conditions. Examples include ransomware attacks disrupting operations or denial-of-service attacks rendering systems inoperable.
- Sensor Spoofing/Tampering: Falsifying sensor data to mislead the digital twin and consequently the BAS, leading to inefficient operation or even dangerous conditions.
- Supply Chain Attacks: Vulnerabilities introduced through third-party hardware or software components in the digital twin ecosystem.
To mitigate these risks, ‘security by design’ principles are crucial. This means integrating robust cybersecurity measures from the initial planning stages, including:
- End-to-End Encryption: Encrypting data in transit and at rest.
- Strong Authentication and Access Control: Implementing multi-factor authentication, role-based access control, and strict user permissions.
- Network Segmentation: Isolating critical building systems from less secure networks.
- Regular Security Audits and Penetration Testing: Proactively identifying and addressing vulnerabilities.
- Incident Response Plans: Developing clear protocols for detecting, responding to, and recovering from cyberattacks.
6.2.2. Privacy Concerns:
The extensive collection of data by digital twins raises significant privacy issues, particularly concerning occupant data:
- Granular Occupancy Data: Sensors tracking presence, movement, and even heat signatures can reveal highly personal information about individual occupants, including their working hours, breaks, meeting attendance, and even health-related patterns. This can be perceived as surveillance.
- Personalized Comfort Settings: While beneficial for individuals, storing and utilizing personalized temperature, lighting, or air quality preferences raises questions about data ownership and potential misuse.
- Data Minimization: The principle of only collecting the data that is absolutely necessary for the intended purpose should be strictly adhered to.
- Anonymization and Aggregation: Where possible, individual-level data should be anonymized or aggregated to protect privacy, especially for analytics that do not require individual identification.
- Consent: Clear mechanisms for obtaining informed consent from occupants regarding data collection and usage are essential, especially in residential or mixed-use buildings.
6.2.3. Ethical Considerations:
Beyond security and privacy, broader ethical questions emerge:
- Bias in Algorithms: If AI/ML algorithms used for optimization are trained on biased data, they could inadvertently lead to unequal treatment or comfort levels for different occupant groups. For example, an energy optimization algorithm might prioritize cost savings over the comfort of occupants in certain zones.
- Transparency and Accountability: The ‘black box’ nature of some advanced AI models can make it difficult to understand why certain decisions (e.g., energy adjustments) are made by the digital twin. Establishing clear lines of accountability for AI-driven outcomes is vital.
- Data Misuse: The potential for collected data to be used for purposes other than building management (e.g., marketing, employee monitoring) without explicit consent or knowledge is a serious concern.
- Digital Divide: Ensuring equitable access to the benefits of smart building technologies and preventing the creation of a ‘digital divide’ where some occupants or buildings are left behind.
Addressing these considerations is not only essential for fostering trust and acceptance but also for ensuring compliance with evolving privacy laws (e.g., GDPR, CCPA) and avoiding potential legal challenges (Reuters, 2024). A responsible approach mandates embedding privacy-by-design and ethical-by-design principles throughout the entire lifecycle of digital twin development and deployment.
6.3. Model Accuracy and Validation
The utility and reliability of a digital twin are fundamentally dependent on the accuracy and precision of its underlying virtual model and the data it receives. A ‘garbage in, garbage out’ principle applies rigorously; if the data feeding the twin is flawed or the model itself is not a true representation of the physical asset, the insights, simulations, and control commands generated by the digital twin will be unreliable, potentially leading to incorrect decisions, wasted resources, or even adverse operational outcomes.
Key challenges to model accuracy and validation include:
- Data Quality and Integrity: This is a critical factor. Sensors can drift over time, become miscalibrated, suffer from electrical interference, or simply fail. Data transmission errors, missing data points, and inconsistent data formats can all compromise data quality. The digital twin must incorporate robust data validation, cleaning, and imputation techniques to handle these issues.
- Sensor Calibration and Recalibration: Regular and accurate calibration of all connected sensors (temperature, pressure, flow, CO2, etc.) is paramount. If a sensor consistently provides erroneous readings, the digital twin will operate based on a false understanding of the physical environment. Establishing a routine calibration schedule and using self-calibrating sensors where possible are vital.
- Reality Gap (Model Drift): A building is a dynamic entity. Over its lifecycle, it undergoes changes due to wear and tear, renovations, equipment upgrades, changes in occupancy patterns, or even structural settling. If the digital twin model is not continuously updated to reflect these physical changes, a ‘reality gap’ emerges, where the virtual model no longer accurately mirrors the physical building. This model drift reduces the twin’s effectiveness.
- Computational Resources: Creating and maintaining highly accurate, real-time digital twins for large, complex buildings requires significant computational power for data processing, simulation, and running sophisticated AI/ML algorithms. This can necessitate substantial investment in cloud infrastructure, high-performance computing, and robust data storage solutions, posing a financial and technical challenge for some organizations.
- Complexity of Building Systems: Buildings are inherently complex, with interconnected systems where a change in one parameter can ripple through others. Accurately modeling these intricate interdependencies and dynamic behaviors (e.g., thermal dynamics of the building envelope interacting with HVAC system response) is a non-trivial task.
- Skill Gap: A significant challenge is the scarcity of professionals with the multidisciplinary expertise required to implement and manage digital twins effectively. This includes proficiency in BIM, IoT technologies, data science, cybersecurity, and traditional facility management. Bridging this skill gap through training and collaborative teams is essential for successful adoption.
To ensure model accuracy and ongoing validation:
- Continuous Feedback Loops: Implement mechanisms for real-time data from the physical asset to continuously update and refine the digital twin model. This could involve self-learning algorithms that adjust model parameters based on observed discrepancies.
- Validation against Ground Truth: Regularly compare the digital twin’s predictions and simulated outputs against actual measured performance data from the physical building. Discrepancies should trigger model refinement.
- Hybrid Modeling: Combining physics-based models (for foundational accuracy) with data-driven models (for adaptability and learning from real-world data) can often yield more robust and accurate digital twins.
- Version Control and Audit Trails: Maintaining clear version control for the digital twin model and an audit trail of all changes helps in understanding and troubleshooting model behavior.
- User Feedback Integration: Incorporating feedback from facility managers and occupants regarding perceived comfort or operational issues can help identify areas where the digital twin’s understanding or control needs refinement.
Maintaining a high level of model accuracy and ensuring continuous validation are ongoing processes crucial for deriving reliable insights and achieving the promised benefits of digital twin technology in building management.
Many thanks to our sponsor Focus 360 Energy who helped us prepare this research report.
7. Future Prospects
The trajectory of digital twin technology in building management is characterized by continuous innovation and increasing sophistication. As advancements in artificial intelligence (AI), machine learning (ML), Internet of Things (IoT), and other complementary technologies accelerate, digital twins are poised to play an increasingly integral and transformative role in shaping the smart, sustainable, and highly efficient built environments of tomorrow. The future prospects are expansive and exciting:
-
Advanced AI and Machine Learning Capabilities: Future digital twins will move beyond current predictive analytics to embrace more sophisticated AI paradigms. This includes reinforcement learning for truly autonomous building operations, where the twin can ‘learn’ optimal control strategies through continuous interaction with the physical environment, adapting to complex, changing conditions without human intervention. The concept of ‘cognitive digital twins’ may emerge, capable of reasoning, problem-solving, and even understanding human preferences and emotions to optimize environments for well-being and productivity. AI will also enhance the twin’s ability to self-diagnose and self-heal, recommending specific and immediate solutions to detected anomalies.
-
Broader Ecosystem Integration and Smart Cities: Digital twins of individual buildings will increasingly integrate into larger, interconnected ecosystems, forming the backbone of smart city initiatives. This will involve sharing anonymized data and insights with urban planning systems, smart grid management platforms (for demand-response and energy distribution optimization), public transportation networks, and even emergency services. This macro-level integration will enable holistic urban resource management, enhance urban resilience to climate change (Reuters, 2024), and create more livable and sustainable cities.
-
Blockchain for Data Trust and Security: The inherent distributed ledger technology of blockchain could be leveraged to enhance data security, transparency, and immutability within digital twin ecosystems. Blockchain could provide a trusted and auditable record of all data transactions, sensor readings, and system changes, addressing concerns around data integrity, provenance, and data ownership in a multi-stakeholder environment.
-
Enhanced User Interfaces and Immersive Interactions: The way facility managers and occupants interact with digital twins will become more intuitive and immersive. Augmented Reality (AR) and Virtual Reality (VR) technologies will allow for virtual walkthroughs of building models, real-time data overlays on physical assets for maintenance (as discussed), and collaborative virtual environments for design review and operational planning. This will make complex data more accessible and actionable for a broader range of users.
-
Hyper-Personalization and Human-Centric Design: Future digital twins will place an even greater emphasis on individual occupant well-being and productivity. By integrating with wearables and personal devices (with explicit consent and strong privacy safeguards), digital twins could offer hyper-personalized comfort control, dynamic lighting aligned with circadian rhythms, and optimized airflow, creating truly responsive and adaptive indoor environments tailored to individual preferences and health needs.
-
Integration with Renewable Energy and Circular Economy: Digital twins will play an even more critical role in achieving net-zero energy buildings and fostering circular economy principles. They will optimize the integration and management of on-site renewable energy sources, manage energy storage systems, and facilitate interactions with the grid for peak shaving and demand response. Furthermore, they can track the material composition of building elements, aiding in future deconstruction, recycling, and reuse strategies, thereby minimizing waste and promoting resource efficiency across the building’s entire lifecycle.
-
Decentralized Digital Twins and Edge Computing: The increasing power of edge computing devices will enable more localized intelligence and processing. This could lead to a decentralized approach to digital twins, where certain functions and data processing occur closer to the physical assets, reducing latency, enhancing responsiveness, and potentially improving data privacy.
-
Regulatory Support and Industry Standards Evolution: As the benefits of digital twins become more widely recognized, governments and industry bodies are likely to introduce policies, incentives, and evolving standards that encourage their adoption, further driving innovation and market growth. This will also help standardize data formats and interoperability, overcoming current challenges.
As digital twin technology continues its rapid evolution, it is not merely an incremental improvement but a fundamental paradigm shift. It is anticipated to become an increasingly indispensable tool, transforming how buildings are designed, constructed, operated, and maintained, ultimately leading to built environments that are smarter, more sustainable, resilient, and profoundly more responsive to human needs.
Many thanks to our sponsor Focus 360 Energy who helped us prepare this research report.
References
- Axios. (2025, June 18). How digital twin technology is transforming the enterprise. Retrieved from https://www.axios.com/sponsored/how-digital-twin-technology-is-transforming-the-enterprise
- Bosch Energy and Building Solutions Global. (n.d.). Digital Building Twins. Retrieved from https://www.boschbuildingsolutions.com/xc/en/news-and-stories/digital-building-twins/
- Buildings. (n.d.). The Real Value of Digital Twins in Smart Buildings. Retrieved from https://www.buildings.com/smart-buildings/article/55289925/the-real-value-of-digital-twins-in-smart-buildings
- CompanionLink. (2025, April 15). Digital Twins in Smart Buildings: What They Are and Why They Matter. Retrieved from https://www.companionlink.com/blog/2025/04/digital-twins-in-smart-buildings-what-they-are-and-why-they-matter/
- Joseph Engineering Services. (n.d.). Understanding Digital Twins in Construction. Retrieved from https://www.jesbim.com/services/what-are-digital-twins
- Pinnacle IIT. (n.d.). How can Digital Twins make any Building Smarter? Retrieved from https://pinnacleiit.com/blogs/bim/digital-twins/
- Reuters. (2024, May 23). How AI is arming cities in the battle for climate resilience. Retrieved from https://www.reuters.com/sustainability/climate-energy/how-ai-is-arming-cities-battle-climate-resilience-2024-05-23/
- Reuters. (2024, August 20). Avoiding growing pains in the development and use of digital twins. Retrieved from https://www.reuters.com/legal/legalindustry/avoiding-growing-pains-development-use-digital-twins-2024-08-20/
- Sensgreen. (n.d.). What is a Digital Twin in Building Management? Retrieved from https://sensgreen.com/what-is-a-digital-twin-and-how-is-it-revolutionizing-building-management/
- Toobler. (n.d.). Digital Twin for Buildings: Benefits & Best Practices. Retrieved from https://www.toobler.com/blog/digital-twin-for-buildings-benefits
- Twinview Digital Twin. (2024, July 10). Digital Twins: The Key to True Data Interoperability in Building Management. Retrieved from https://www.twinview.com/insights/digital-twins-the-key-to-true-data-interoperability-in-building-management
- Wang, Y., Su, Z., Guo, S., Dai, M., Luan, T. H., & Liu, Y. (2023). A Survey on Digital Twins: Architecture, Enabling Technologies, Security and Privacy, and Future Prospects. arXiv preprint arXiv:2301.13350. Retrieved from https://arxiv.org/abs/2301.13350
- Wikipedia. (n.d.). Digital twin. Retrieved from https://en.wikipedia.org/wiki/Digital_twin
So, buildings are getting their own doppelgangers now? I wonder if the digital twin of my house will finally fix that leaky faucet. If so, can I just pay the digital plumber?
That’s a great point! Imagine paying a ‘digital plumber’ – AI could diagnose the issue remotely using your home’s digital twin and even order the correct parts. Then a local plumber could fix it with all the information ready to go. Efficiency at its finest!
Editor: FocusNews.Uk
Thank you to our Sponsor Focus 360 Energy
The integration with IoT sensors for granular insights into occupancy patterns is particularly compelling. Imagine digital twins dynamically adjusting ventilation based on real-time density, optimizing air quality and energy use simultaneously.
I agree that IoT integration provides unparalleled opportunities. Taking it a step further, imagine the digital twin learning individual occupant preferences over time, then proactively adjusting environmental settings! We could have personalized comfort profiles for everyone in the building.
Editor: FocusNews.Uk
Thank you to our Sponsor Focus 360 Energy
So, a building’s digital twin can manage my comfort? Will it also argue with me about what temperature is *actually* comfortable, or just passively-aggressively adjust the thermostat? Asking for a friend… who may or may not be a building.