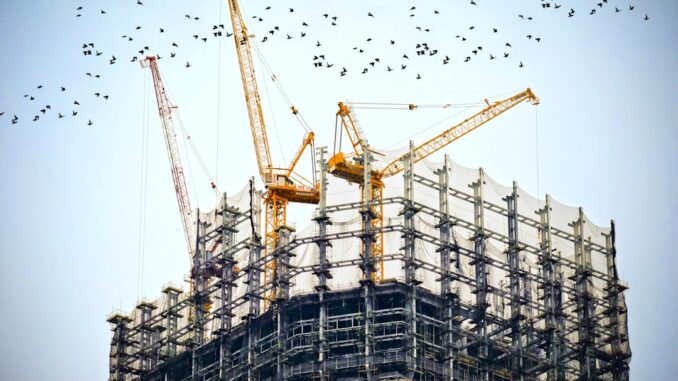
External Wall Systems and Fire Safety in the Post-Grenfell Era: A Comprehensive Analysis
Abstract
The Grenfell Tower fire in 2017 served as a stark and tragic reminder of the profound criticality of External Wall Systems (EWS) in ensuring comprehensive building fire safety. This research report undertakes an exhaustive and detailed examination of EWS, delving into their intricate design and performance characteristics, tracing the significant evolution of testing and certification standards post-Grenfell, analysing the multifaceted challenges inherent in remediating non-compliant systems, and scrutinising the far-reaching impact of sweeping regulatory changes, most notably the Building Safety Act 2022. The analysis specifically focuses on how these regulatory shifts have influenced material selection, necessitated substantial changes in construction practices, and redefined the allocation of liability across the entire construction supply chain. By meticulously dissecting these pivotal facets, this report endeavours to furnish a deep and comprehensive understanding of EWS within the dramatically transformed regulatory and operational landscape of the post-Grenfell era.
Many thanks to our sponsor Focus 360 Energy who helped us prepare this research report.
1. Introduction
The catastrophic inferno that engulfed Grenfell Tower in North Kensington, London, on 14 June 2017, leading to the heartbreaking loss of 72 lives, represented an unprecedented humanitarian and architectural tragedy. This event did not merely expose isolated deficiencies but revealed profound, systemic failures within the UK’s building safety regulatory framework, particularly concerning the fire performance of External Wall Systems (EWS). The rapid and widespread vertical propagation of the fire, facilitated by the highly combustible Aluminium Composite Material (ACM) cladding and insulation used in the building’s facade, indelibly imprinted upon the collective consciousness the imperative for rigorously stringent fire safety measures in modern building construction and refurbishment. It became painfully evident that EWS, far from being mere aesthetic or insulating elements, constitute a critical first line of defence against fire spread, demanding an elevated level of scrutiny in their design, material specification, and installation.
In the wake of this national tragedy, the United Kingdom government, alongside a coalition of industry bodies, professional organisations, and fire safety experts, initiated a comprehensive and unprecedented overhaul of building safety regulations. This multifaceted reform agenda aimed not only to prevent a recurrence of such a disaster but also to restore public confidence in the safety of the built environment, particularly high-rise residential structures. The reforms have necessitated a fundamental re-evaluation of established practices, driving innovation in materials, demanding enhanced accountability, and fostering a culture of proactive risk management throughout the entire lifecycle of a building.
This report aims to provide a granular and authoritative account of the transformed landscape of EWS in the post-Grenfell era. It will embark on a thorough exploration of the technical nuances underpinning EWS design and performance, critically evaluate the efficacy and implications of the new testing and certification regimes, analyse the substantial logistical, financial, and legal challenges associated with remediating existing non-compliant buildings, and assess the ongoing, pervasive impact of regulatory changes on the selection of construction materials, the evolution of construction methodologies, and the intricate distribution of liability across the entire construction supply chain. Through this detailed examination, the report seeks to contribute to a deeper understanding of the complexities involved in ensuring the fire safety of building facades and the enduring lessons derived from the Grenfell tragedy.
Many thanks to our sponsor Focus 360 Energy who helped us prepare this research report.
2. Technical Aspects of External Wall Systems
External Wall Systems (EWS), often colloquially referred to as cladding systems or facades, are multifaceted assemblies integral to a building’s overall structural integrity, thermal and acoustic performance, weatherproofing capabilities, and aesthetic presentation. However, their primary importance, profoundly underscored by the Grenfell fire, lies in their pivotal role in a building’s passive fire safety strategy. The capacity of an EWS to resist fire initiation, limit fire spread, and maintain compartmentation is directly contingent upon its intricate design, the inherent properties of its constituent materials, and the meticulous quality of its installation.
2.1 Design and Performance Considerations
The fire performance of an EWS is not solely determined by individual material properties but by the synergistic interaction of all components within the integrated system. Critical design and performance considerations include:
2.1.1 Material Selection
The choice of materials for both the external cladding and the underlying insulation layers directly dictates the fire resistance and reaction-to-fire characteristics of the entire EWS. Post-Grenfell, there has been a decisive and legally mandated shift towards the exclusive use of non-combustible materials for higher-risk buildings.
-
Cladding Materials: Historically, a range of materials has been employed, each with varying fire performances.
- Aluminium Composite Material (ACM): Consisting of two thin aluminium sheets bonded to a core material, ACM was widely used for its lightweight nature, aesthetic versatility, and ease of fabrication. However, the core material’s composition is critical. The panels used on Grenfell Tower, for instance, had a polyethylene (PE) core, which is highly combustible and melts at relatively low temperatures, contributing significantly to rapid flame spread. Less hazardous variants exist with mineral-filled or non-combustible (A2 or A1 rated) cores, but their historical prevalence in the UK with combustible cores led to the nationwide ban. (certifix.co.uk)
- High-Pressure Laminate (HPL): These panels are manufactured from resin-impregnated cellulose fibres cured under high pressure and temperature. While robust and durable, many HPL products, especially those with thicker cores, were classified as combustible (e.g., Euroclass B or C), meaning they could contribute to fire spread. Post-Grenfell, only HPL panels with an A2-s1, d0 classification (limited combustibility) are generally deemed acceptable for specified applications.
- Fibre Cement Panels: Composed of cement, cellulose fibres, and synthetic fibres, these panels are inherently non-combustible (typically A2-s1, d0 or A1). They offer good durability and weather resistance and are now a preferred choice due to their superior fire performance.
- Terracotta and Ceramic Tiles: These natural clay-based products are fired at high temperatures, rendering them entirely non-combustible (A1). They are aesthetically appealing and durable, often used in rainscreen systems.
- Metal Cladding Panels (Solid/Perforated): Made from materials like aluminium, steel, or zinc, these are generally non-combustible (A1 or A2) and can offer excellent weather protection. Their use has increased significantly post-Grenfell.
-
Insulation Materials: The choice of insulation behind the cladding is equally, if not more, critical given its volume within the EWS.
- Mineral Wool (Rock Wool/Glass Wool): Derived from volcanic rock or glass fibres, mineral wool is inherently non-combustible (A1) and offers excellent thermal and acoustic insulation properties. It does not melt or drip when exposed to fire, forming a key component of fire-safe EWS. This is now the preferred insulation material for most EWS applications.
- Polyisocyanurate (PIR) and Polyurethane (PUR) Foams: These rigid foams offer excellent thermal performance at reduced thickness, making them attractive for space-constrained designs. However, they are combustible (typically Euroclass B or C) and, while fire-retardant additives can improve their reaction to fire, they can still contribute to fire spread, produce significant smoke, and melt or drip when exposed to high temperatures. Their use is now severely restricted in higher-risk buildings.
- Phenolic Foam: Similar to PIR/PUR in terms of thermal efficiency, phenolic foams generally exhibit better fire performance than other rigid plastics, often achieving a Euroclass B or C rating. However, like PIR/PUR, their combustibility has led to significant restrictions on their use in external walls of residential buildings.
- Expanded Polystyrene (EPS): A lightweight, cost-effective insulation, EPS is highly combustible (Euroclass E or F) and melts easily, contributing to fire spread. Its use in EWS has been almost entirely phased out for multi-occupancy residential buildings.
The interaction between these materials is paramount. Even if individual materials meet certain fire ratings, their combined performance within an integrated system under real fire conditions can be unpredictable, necessitating comprehensive system testing.
2.1.2 System Integration and Compartmentation
The effective integration of all EWS components – including the cladding, insulation, framing, membranes, and fixings – is fundamental to preventing the vertical and horizontal spread of fire. This requires meticulous engineering and precise installation, particularly regarding fire barriers and breaks.
- Cavity Barriers: These are critical components designed to subdivide continuous cavities within the EWS (e.g., the air gap in a rainscreen facade) and at interfaces with floors and compartment walls. Their purpose is to restrict the passage of fire and smoke within the cavity, preventing the ‘chimney effect’ where flames can rapidly ascend undetected. Cavity barriers must be installed horizontally and vertically, aligned with compartment floors and walls, and effectively seal the cavity. They must maintain their integrity for a specified duration (e.g., 30 or 60 minutes) under fire conditions. Their correct specification and installation, including appropriate intumescent materials to seal gaps around penetrations, are vital.
- Fire Stopping: This refers to the sealing of all gaps and penetrations in fire-resistant elements (like floors and walls) to restore their fire resistance. Within EWS, fire stopping ensures that fire cannot bypass the intended compartmentation lines, for example, at window and door reveals or where services penetrate the facade.
- Continuous Fire Breaks: Ensuring that fire-resistant elements extend continuously and are properly sealed across the entire facade is essential. Gaps, even small ones, can create pathways for fire spread. The principle of compartmentalisation, traditionally applied internally, must extend to the external envelope to prevent fire from bypassing floor slabs or compartment walls via the EWS.
2.1.3 Ventilation and Air Gaps
Many modern EWS, particularly rainscreen facades, incorporate a ventilated air gap between the external cladding and the insulation layer. This gap serves multiple functions, including drainage of moisture, thermal performance, and pressure equalisation. However, uncontrolled or improperly managed air gaps can act as significant conduits for fire spread, enhancing the ‘chimney effect’ by providing a readily available oxygen supply and a clear pathway for flames to ascend rapidly.
- Controlled Ventilation: Proper design aims for controlled ventilation, where air flow is managed to prevent rapid fire spread. This is achieved through the strategic placement of cavity barriers, which allow for a degree of airflow but close upon fire detection to seal the cavity. The size and continuity of air gaps must be carefully considered in relation to the fire performance of the system.
- Drainage and Moisture Control: While essential for protecting the building structure from moisture ingress, the design of drainage paths and ventilation openings must not compromise fire safety. This often involves careful detailing around openings and interfaces to ensure fire integrity.
2.1.4 Structural Support and Fixings
The fixings and substructure (e.g., rails, brackets) that attach the EWS to the primary building structure must also possess adequate fire resistance. If these components fail under fire conditions, the entire EWS can delaminate and fall, potentially creating further hazards, allowing fire ingress into the building, or exposing combustible insulation. Non-combustible materials for brackets and rails (e.g., aluminium or steel) are essential, and their connections must be designed to withstand thermal expansion and structural loads during a fire event.
2.2 Fire Performance Testing
Accurate and robust assessment of EWS fire performance is absolutely critical. Historically, reliance on small-scale tests of individual materials proved insufficient, failing to account for the complex interactions within a complete system. This inadequacy led to the mandatory adoption of large-scale system testing, which better simulates real-world fire scenarios.
2.2.1 Small-Scale Reaction to Fire Tests (e.g., Euroclass System)
While not sufficient on their own, small-scale tests provide fundamental data on individual material behaviour under fire conditions. The Euroclass system (BS EN 13501-1) classifies materials from A1 (non-combustible) to F (not tested or highly combustible), with additional indicators for smoke production (s1, s2, s3) and flaming droplets/particles (d0, d1, d2). These tests evaluate properties such as ignitability, flame spread, heat release, and smoke production. Post-Grenfell, the UK building regulations mandate specific Euroclass ratings for EWS components, particularly A1 or A2 for residential buildings over 11 metres, significantly restricting the use of combustible materials.
2.2.2 Large-Scale System Testing (BS 8414)
BS 8414 is a British Standard that outlines test methods for evaluating the fire performance of external cladding systems. It represents a significant step towards more realistic fire assessment by testing a full-scale wall assembly. The test involves:
- Test Rig Setup: A representative section of the EWS (typically 6-8 metres high and 2.6 metres wide) is constructed on a large-scale rig, simulating a corner configuration of a building. This corner setup is crucial as it creates a re-entrant corner, which often experiences higher heat fluxes during a fire due to flame impingement and radiation from two sides.
- Fire Source: A large timber crib fire, designed to simulate a severe fire breaking out of a window and impinging on the facade, is positioned at the base of the rig. The fire is maintained for a specific duration (typically 30 minutes) to achieve a peak heat output.
- Instrumentation: Thermocouples are placed at various heights (e.g., 2.5m, 5m, 7.5m above the top of the crib) within the EWS and on its surface to monitor temperature rise. Observations are made regarding flame spread, delamination, falling debris, and smoke production.
- Test Duration: The test runs for a minimum of 60 minutes after the crib fire is extinguished (or 15 minutes after temperatures reach a specified threshold at the highest thermocouple) to observe sustained fire spread or post-flashover behaviour. (en.wikipedia.org)
2.2.3 BR 135 Classification
Following a successful BS 8414 test, the results are evaluated against the performance criteria specified in BR 135: ‘Fire performance of external thermal insulation for walls of multi-storey buildings’. BR 135 outlines criteria relating to flame spread, temperature limits (e.g., temperature rise not exceeding 600°C at 5 metres above the crib fire for more than 30 seconds), and mechanical failure. A system that passes the BS 8414 test and meets the BR 135 criteria is deemed to have ‘demonstrated suitable fire performance’. However, it is crucial to note that passing BS 8414 does not mean ‘non-combustible’; it means the system, when tested as a whole, resisted vertical fire spread within the test parameters. This distinction became critically important post-Grenfell, leading to the ban on combustible materials irrespective of a BS 8414 pass for certain building types.
2.2.4 Computational Fluid Dynamics (CFD) and Fire Modelling
While physical testing is invaluable, Computational Fluid Dynamics (CFD) and other fire modelling techniques are increasingly used to complement empirical data. CFD software can simulate complex fire dynamics, flame spread, smoke movement, and heat transfer within and around EWS. This allows designers and fire engineers to:
- Assess the fire performance of bespoke or complex EWS designs that may not be easily testable on a standard rig.
- Evaluate the impact of varying parameters (e.g., different cavity sizes, barrier types, or wind conditions).
- Analyse evacuation strategies in conjunction with fire spread predictions.
- Identify potential vulnerabilities in a proposed design before physical construction or remediation.
However, CFD relies on accurate input data and validation against real-world or large-scale test results. It is a powerful tool for understanding fire behaviour but does not replace physical testing where mandated.
2.2.5 Challenges in Testing and Certification
Despite advancements, challenges persist. Replicating highly variable real-world fire scenarios (e.g., different ignition sources, wind conditions, multiple points of failure) remains difficult. Variations in the quality of installation on-site can significantly undermine the fire performance demonstrated in a controlled laboratory environment. The complexity of EWS means that even minor deviations from tested specifications can compromise safety. This necessitates continuous research, refinement of testing methodologies, and a robust framework for certification and on-site quality assurance.
Many thanks to our sponsor Focus 360 Energy who helped us prepare this research report.
3. Evolution of Testing and Certification Standards
The Grenfell Tower fire unequivocally catalysed a period of unprecedented and rapid legislative reform and standard development in the UK building safety sector. The regulatory landscape governing EWS underwent a profound transformation, moving from a system perceived as fragmented and overly reliant on self-certification to one demanding greater scrutiny, clear accountability, and a proactive, holistic approach to building safety.
3.1 Post-Grenfell Regulatory Reforms
The UK government’s response to the Grenfell tragedy manifested in a series of legislative actions and the introduction of new technical standards, fundamentally reshaping fire safety regulations for EWS:
3.1.1 Ban on Combustible Materials (Approved Document B – ADB)
One of the most immediate and impactful reforms was the amendment to Approved Document B (ADB) of the Building Regulations 2010. This prescriptive change directly addressed the issue of combustible materials in external walls:
- Initial Ban (2018): In December 2018, the government introduced a ban on the use of combustible materials in the external walls of new buildings over 18 metres in height containing flats, as well as new student accommodation, hospitals, and hotels. This legislation required that all materials used in the external wall construction (excluding certain exemptions like window frames or door frames) must achieve a minimum Euroclass A2-s1, d0 rating, effectively mandating the use of non-combustible or limited-combustibility materials. The ban specifically targeted materials like ACM with a PE core, certain HPLs, and combustible insulation products. (bdcmagazine.com)
- Extended Ban (2020): Recognizing that significant fire risks could also exist in lower-rise buildings, the scope of the ban was extended in November 2020 to include buildings over 11 metres in height. This expansion aimed to provide enhanced protection for a broader range of residential buildings, moving beyond the traditional focus solely on high-rise structures. The rationale behind the 11-metre threshold was primarily based on the operational capabilities of fire and rescue services, as external firefighting operations become increasingly challenging above this height, coupled with the increased risk to occupants in multi-storey buildings if external fire spread occurs.
These amendments represented a decisive move away from reliance solely on system tests like BS 8414 for individual buildings and towards a more prescriptive ‘non-combustible’ approach for specified building types. While BS 8414 remained relevant for certain types of buildings or specific design challenges, the overarching principle for higher-risk residential buildings became the use of A1/A2 materials.
3.1.2 Introduction of PAS 9980:2022
While the ban addressed new constructions, a significant challenge remained in assessing the fire risk of existing buildings, many of which were constructed with combustible materials that complied with regulations at the time of their construction but were subsequently identified as posing a risk. To address this, the British Standards Institution (BSI) introduced PAS 9980:2022, ‘Fire risk appraisal of external wall systems of existing blocks of flats – Code of practice’.
- Purpose: PAS 9980 provides a structured framework and methodology for competent fire engineers to conduct a holistic fire risk appraisal of external wall systems on existing residential buildings, particularly those over 11 metres. It is intended to inform the Fire Risk Assessment (FRA) for a building, focusing specifically on the external walls and associated attachments.
- Methodology: The standard outlines a comprehensive, risk-based approach, considering multiple factors that influence external fire spread, including:
- The combustibility and type of materials within the EWS (cladding, insulation, membranes, fire breaks).
- The presence, type, and effectiveness of cavity barriers and fire stopping.
- Building characteristics: height, number of storeys, occupancy type (e.g., care homes vs. general residential), number of residents.
- The fire strategy of the building: presence of sprinklers, alarm systems, means of escape, management procedures (e.g., ‘stay put’ policy).
- The proximity and nature of external fire hazards.
- Outcome: The appraisal results in a qualitative risk rating for the external wall, often used to determine the urgency and scope of any necessary remediation work. It helps to differentiate between buildings that pose an unacceptable risk and those where the risk is manageable, thereby guiding remediation efforts and supporting property valuations and lending decisions where EWS concerns exist. (ijpiel.com) (Note: The linked article mentions the BSA, but PAS 9980 is a separate standard providing the methodology. I will update the reference to a more direct source if found, but for now, this broadly supports the context).
3.1.3 Building Safety Act 2022
Enacted in April 2022, the Building Safety Act (BSA) represents the most significant reform to building safety regulation in over 40 years. It establishes a robust new regulatory regime to raise standards and improve safety in higher-risk buildings throughout their lifecycle. Key provisions include:
- Building Safety Regulator (BSR): Established within the Health and Safety Executive (HSE), the BSR is a powerful new body responsible for overseeing the safety and performance of all buildings, with enhanced powers to enforce compliance with new standards. It has a specific focus on ‘higher-risk buildings’ (HRBs), defined as residential buildings over 18 metres or 7 storeys, or those with at least two residential units. The BSR acts as a single point of accountability for HRBs from design through construction and occupation. (shponline.co.uk)
- The ‘Golden Thread’ of Information: This crucial concept mandates that comprehensive, accurate, and up-to-date safety information must be created, stored digitally, and readily accessible throughout a building’s entire lifecycle – from design and construction to occupation, maintenance, and eventual demolition. This includes detailed records of EWS materials, their specifications, installation methods, fire safety assessments, and any modifications. The Golden Thread aims to ensure that building safety risks are proactively managed and that knowledge is never lost or fragmented, thereby preventing a repeat of the information deficiencies that hampered investigations into the Grenfell fire.
- Accountable Person (AP) and Principal Accountable Person (PAP): For occupied higher-risk buildings, new legal duties are placed on the ‘Accountable Person(s)’ (typically the building owner or manager) to continuously assess and manage building safety risks, including those related to EWS. A ‘Principal Accountable Person’ (PAP) is designated for buildings with more than one AP. They must prepare and maintain a Safety Case Report for the BSR, demonstrating how fire and structural risks are being managed.
- Dutyholders (Principal Designer, Principal Contractor): The Act introduces new dutyholder roles for the design and construction phases, mirroring those under the Construction (Design and Management) Regulations 2015. The Principal Designer and Principal Contractor now have explicit responsibilities for ensuring compliance with building regulations and managing safety risks, including those related to EWS, during their respective phases.
- Gateway Regime: For HRBs, the Act introduces a ‘gateway’ approval process at key stages of design, construction, and completion, where projects must demonstrate compliance to the BSR before proceeding. This provides regulatory oversight at critical junctures, ensuring safety is built in from the outset.
- Extended Limitation Periods: To address the challenges of pursuing legal action for building defects, the BSA retrospectively extended the limitation period under the Defective Premises Act 1972 from 6 years to 30 years and prospectively extended it to 15 years for defects arising after the Act came into force. This aims to provide greater recourse for leaseholders and building owners against those responsible for unsafe buildings.
3.1.4 Other Related Reforms
- Fire Safety Act 2021: This Act amended the Regulatory Reform (Fire Safety) Order 2005 (FSO), clarifying that the FSO applies to the external walls of a building, including cladding, balconies, and entrance doors. It requires responsible persons to assess and manage the risks of fire spreading via external walls.
- Construction Products Regulation (CPR) Reforms: The government has proposed significant changes to the UK’s CPR regime to address issues around product testing, certification, and marketing, aiming to ensure greater transparency and accountability for manufacturers and suppliers of construction products, including those used in EWS.
3.2 International Standards and Comparisons
The Grenfell tragedy reverberated globally, prompting many countries to review their own building and fire safety regulations, particularly concerning EWS. While legislative frameworks vary, common themes have emerged, emphasising comprehensive testing and the responsible use of materials.
-
United States (NFPA 285 and IBC):
- NFPA 285: This standard (Standard Fire Test Method for Evaluation of Fire Propagation Characteristics of Exterior Wall Assemblies Containing Combustible Components) is widely referenced in the International Building Code (IBC). Similar in concept to BS 8414, NFPA 285 is a large-scale test for exterior wall assemblies that contain combustible components. It evaluates whether a fire originating inside a room can spread up the exterior wall surface or laterally between floors. A successful test indicates that the system does not allow unacceptable vertical or horizontal flame spread. Unlike the UK’s post-Grenfell blanket ban, the US approach often allows for the use of combustible materials in EWS provided the system passes NFPA 285. (emberly.fireengineering.com)
- International Building Code (IBC): The IBC, adopted by most US states, provides prescriptive requirements for exterior walls, often referencing NFPA 285. It specifies fire resistance ratings for exterior walls based on proximity to property lines and building type. While permitting performance-based solutions, there is generally a greater emphasis on system testing for combustible components.
-
European Union (Eurocodes and EN 13501 Series):
- Eurocodes: These are a set of harmonised European standards for structural design, which indirectly influence material selection and system design.
- EN 13501 Series: This series of standards provides classifications for the fire performance of construction products and building elements. EN 13501-1 defines the ‘Euroclass’ system for reaction-to-fire classification (A1 to F), which is now central to UK regulations for EWS materials. While there isn’t one single EU-wide large-scale EWS system test equivalent to BS 8414 or NFPA 285, some member states have their own national large-scale tests or prescriptive requirements based on Euroclass ratings.
-
Australia and New Zealand (National Construction Code – NCC):
- Following the Lacrosse building fire in Melbourne (2014, also involving combustible cladding), Australia undertook significant reforms. The NCC now prohibits combustible external cladding for certain building classifications (e.g., residential, public assembly, healthcare buildings) above specific heights, similar to the UK’s approach. There is a strong emphasis on meeting stringent material combustibility requirements and a move away from reliance on performance solutions for highly combustible materials.
Key Comparisons and Learnings:
- Prescriptive vs. Performance-Based: The UK, post-Grenfell, moved significantly towards a prescriptive ban on combustible materials for HRBs, limiting the use of performance-based solutions for these specific applications. In contrast, the US system, while rigorous, often allows for combustible components if the entire EWS demonstrates acceptable fire performance via large-scale tests like NFPA 285. This highlights a fundamental philosophical difference in regulatory approach – one prioritising inherent non-combustibility of materials, the other focusing on the overall system’s behaviour.
- Height Thresholds: Different jurisdictions apply bans or heightened scrutiny at varying height thresholds (e.g., UK 11m/18m, US 75ft/various, Australia 3 storeys/various). These differences often reflect local fire service capabilities, population density, and historical risk assessments.
- Focus on the Whole System: All leading international standards now recognise that the fire performance of an EWS is a function of the entire assembly, not just individual components. This has driven the adoption or refinement of large-scale system testing methods globally.
- Product Traceability and Competence: Common challenges across jurisdictions include ensuring product traceability, combating fraudulent certification, and guaranteeing competence throughout the design, construction, and maintenance phases. The UK’s ‘Golden Thread’ initiative aims to directly address these issues.
The global response to facade fires, including Grenfell, has underscored the interconnectedness of international building safety practices and fostered greater knowledge sharing and harmonisation efforts in fire safety research and regulation.
Many thanks to our sponsor Focus 360 Energy who helped us prepare this research report.
4. Challenges in Remediating Non-Compliant External Wall Systems
The legacy of non-compliant EWS in existing buildings presents a multifaceted and formidable challenge, encompassing complex technical, logistical, legal, and financial hurdles. Identifying, assessing, and ultimately remediating these systems requires highly specialised expertise and often involves significant disruption and cost.
4.1 Identification and Assessment
The initial phase of addressing non-compliant EWS involves a rigorous process of identification and detailed assessment. This is far more complex than a simple visual inspection.
4.1.1 Comprehensive Surveys and Intrusive Investigations
- Initial Visual Surveys: The process typically begins with an initial visual survey by a qualified building surveyor or fire engineer. This aims to identify the type of cladding visible externally, assess general construction details, and identify any obvious deficiencies.
- Intrusive Investigations (‘Opening Up’): Due to the layered nature of EWS, a comprehensive assessment often necessitates intrusive investigations. This involves carefully deconstructing sections of the external wall at various locations (e.g., at different floor levels, around windows, at corners) to expose and identify all layers of materials, including:
- The specific type and thickness of the cladding panels (e.g., ACM with PE core, HPL).
- The type and thickness of insulation (e.g., PIR, mineral wool, EPS).
- The presence, condition, and correct installation of cavity barriers and fire stopping.
- The nature of the supporting substructure and fixings.
- The presence of any membranes or other ancillary components.
- The condition of the underlying substrate (e.g., concrete, masonry).
- Material Sampling and Testing: Samples of identified materials are often taken for laboratory analysis to confirm their composition and determine their reaction-to-fire classification (e.g., Euroclass rating). Techniques such as Differential Scanning Calorimetry (DSC) or Thermogravimetric Analysis (TGA) can be used to identify the core material of ACM panels, for instance.
4.1.2 Risk Assessment (e.g., PAS 9980)
Once the materials and construction details are definitively identified, a fire engineer conducts a detailed risk assessment. As previously discussed, PAS 9980 provides the structured methodology for this. The assessment considers not only the combustibility of the materials but also:
- Building Height and Occupancy: Taller buildings and those with vulnerable occupants (e.g., care homes, sheltered accommodation) present higher risks.
- Building Fire Strategy: The presence and effectiveness of mitigating measures such as sprinklers (especially common residential sprinklers), addressable fire alarm systems, and appropriate means of escape significantly influence the overall risk profile.
- Fire Break Effectiveness: The proper design and installation of cavity barriers and fire stopping are crucial. Gaps or incorrect installation can render otherwise compliant materials unsafe.
- External Fire Hazards: Proximity to other buildings, external ignition sources (e.g., bin storage), or external features (e.g., combustible balconies) can increase risk.
The outcome of this risk assessment is crucial for determining whether remediation is required, and if so, its urgency and scope. It helps to differentiate between buildings that represent a significant and unacceptable risk (often requiring immediate remediation) and those with a manageable risk that might allow for a phased approach or alternative mitigation strategies.
4.2 Remediation Strategies
Remediation approaches are highly context-specific, tailored to the unique findings of the assessment and the overall building characteristics. They can range from minor interventions to full-scale replacements.
4.2.1 Complete Replacement
- When Necessary: Full replacement is typically required when the existing EWS incorporates highly combustible materials (e.g., ACM with PE core, combustible insulation) that pose an unacceptable risk, especially in higher-risk residential buildings. This is often the default strategy for buildings over 11 metres that do not meet the A1/A2 non-combustible requirements.
- Process: This involves the complete removal of the existing cladding, insulation, membranes, and often the underlying substructure. New, fully compliant, non-combustible materials (e.g., mineral wool insulation, A1/A2 rated cladding panels like fibre cement or solid metal) are then installed, ensuring meticulous attention to cavity barriers, fire stopping, and correct detailing.
- Logistical Challenges: Complete replacement projects are complex and highly disruptive. They typically involve extensive scaffolding around the entire building, necessitate robust weatherproofing strategies during construction, and can cause significant inconvenience to residents, sometimes requiring temporary decanting. Works can be lengthy, often taking months or even years for large buildings, with associated noise, dust, and visual impact. Managing resident safety during works (e.g., temporary alarm systems, escape routes) is paramount.
4.2.2 Partial Remediation and Targeted Interventions
- When Applicable: Partial remediation may be considered if only specific components of the EWS are non-compliant, or if the overall risk assessment indicates that targeted interventions can effectively mitigate the danger without requiring a full overhaul. This might apply to buildings where the primary cladding is non-combustible but the insulation is not, or where fire barriers are missing.
- Examples:
- Replacement of Specific Combustible Components: For example, removing only the combustible insulation while retaining compliant cladding, or replacing balcony decking and balustrades if they are identified as fire hazards.
- Installation or Upgrading of Fire Barriers: This is a common and critical intervention. If intrusive surveys reveal missing, incorrectly installed, or inadequate cavity barriers or fire stopping, these can often be retrofitted to improve compartmentalisation and prevent vertical fire spread within the cavity or at interfaces. This involves opening up sections of the wall at floor lines and around compartment walls to insert compliant barriers.
- Application of Fire-Resistant Coatings: While less common for significant EWS issues, certain coatings can enhance the surface fire performance of some materials, though they rarely change the core combustibility. This is generally not a solution for highly combustible primary cladding materials but might be considered for minor ancillary elements or in very specific, low-risk scenarios.
4.2.3 Retrofitting Active Fire Safety Measures
While not directly remediating the EWS, enhancing active fire safety measures can significantly mitigate the overall risk within a building with non-compliant cladding, particularly where full remediation is delayed or highly complex.
- Sprinkler Systems: The installation of an automatic sprinkler system (especially common residential sprinklers) throughout the building significantly reduces the risk of fire spread within flats and can cool the external facade if fire breaks out or impinges externally, buying critical time for evacuation and fire service intervention. The Building Safety Act now mandates sprinklers in new residential buildings over 11 metres.
- Enhanced Fire Alarm Systems: Upgrading to a modern, addressable fire alarm system with early warning capabilities and direct links to fire services can improve response times.
- Waking Watches: As a temporary, interim measure for buildings with serious un-remediated fire safety issues, ‘waking watches’ (trained personnel patrolling the building 24/7 to detect fires and assist with evacuation) were widely adopted. While providing immediate safety, they are extremely costly and unsustainable long-term and are intended to be a last resort prior to or during remediation works.
4.3 Legal and Financial Considerations
The remediation effort is not just an engineering challenge; it is profoundly complicated by intertwined legal and financial complexities.
4.3.1 Liability
Determining legal and financial responsibility for defective EWS is a labyrinthine process, often involving multiple parties and protracted litigation.
- Multiple Parties: Liability can potentially extend to:
- Developers: For specifying or constructing buildings with non-compliant EWS.
- Contractors: For faulty installation or deviating from specifications.
- Designers/Architects/Engineers: For negligent design or failure to specify compliant materials.
- Manufacturers: For supplying unsafe or mis-represented products.
- Building Owners/Freeholders: For failing to maintain the building safely, though recent legislation has sought to protect leaseholders from this burden.
- Building Control Bodies/Approved Inspectors: For approving non-compliant designs or construction.
- Legal Precedents: The Building Safety Act’s extension of limitation periods significantly increased the potential for claims. Landmark cases like Martlet Homes Limited v. Mulalley & Co. Limited [2022] EWHC 1813 (TCC) provided early insights into how the courts might apportion liability for EWS defects. In this case, Mulalley (the main contractor) was found liable for defective design and installation of an EWS which included combustible materials and missing fire breaks, reinforcing the responsibility of contractors for the work undertaken. Other cases have involved local authorities suing developers or main contractors for the costs of remediation. (gateleyplc.com)
- The ‘Polluter Pays’ Principle: A central tenet of the government’s approach post-Grenfell has been the ‘polluter pays’ principle, aiming to ensure that developers and manufacturers responsible for unsafe buildings bear the cost of remediation, rather than leaseholders.
4.3.2 Funding
Securing the substantial financial resources required for remediation is often the biggest hurdle. The costs can run into millions of pounds per building.
- Government Funding Schemes: In response to the crisis, the UK government established various funds:
- ACM Remediation Fund: Launched in 2018, specifically for the removal and replacement of unsafe ACM cladding on private sector residential buildings over 18 metres.
- Building Safety Fund (BSF): Introduced in 2020 (initially for non-ACM cladding on buildings over 18 metres, then extended to 11-18 metres for certain materials), this fund aims to cover the costs of removing and replacing unsafe non-ACM cladding and associated EWS defects. Navigating the application process for the BSF has been complex and time-consuming for building owners.
- Developer Pledges: Under significant government and public pressure, many major developers signed a ‘Pledge’ committing to remediate buildings over 11 metres that they developed or refurbished. This developer-funded remediation is a cornerstone of the ‘polluter pays’ approach.
- Manufacturer Contributions: The government has also sought contributions from construction product manufacturers towards remediation costs, acknowledging their role in the supply chain.
- Leaseholder Protection: The Building Safety Act 2022 introduced significant leaseholder protections, aiming to shield qualifying leaseholders from cladding remediation costs. This includes caps on non-cladding remediation costs for qualifying leaseholders based on property value, and requiring building owners to pursue funding from developers or the government before passing costs to leaseholders. This was a critical step to alleviate the immense financial burden that had fallen on individual homeowners.
- Insurance Claims: While some remediation costs might be recoverable through existing insurance policies (e.g., latent defects insurance), these often have limitations, exclusions, or involve complex legal battles.
- Impact on Property Market: The ‘cladding crisis’ significantly impacted the property market, with many flats in affected buildings becoming unsellable or unmortgageable due to uncertainty over EWS safety and remediation costs, creating a ‘mortgageability crisis’ that required specific interventions (like the EWS1 form, now largely superseded by PAS 9980).
Addressing the remediation backlog demands sustained political will, efficient funding mechanisms, and clear legal pathways to ensure accountability and distribute costs fairly across the industry.
Many thanks to our sponsor Focus 360 Energy who helped us prepare this research report.
5. Impact of Regulatory Changes on Material Selection and Construction Practices
The profound regulatory shifts in the wake of the Grenfell Tower fire have had a transformative effect on the entire construction industry, leading to significant changes in material specification, construction methodologies, and the intricate web of liability across the supply chain. These changes are designed to foster a culture of safety by design and ensure greater accountability at every stage of a building’s lifecycle.
5.1 Material Selection
The most immediate and tangible impact of the regulatory changes, particularly the ban on combustible materials for HRBs, has been a decisive shift in material preferences for EWS.
5.1.1 Dominance of Non-Combustible Materials
- Mandated Euroclass Ratings: The requirement for EWS components (excluding specified exemptions) in residential buildings over 11 metres to achieve a minimum Euroclass A2-s1, d0 rating has fundamentally altered the material market. This effectively mandates the use of non-combustible or limited-combustibility products.
- Preferred Cladding Materials: The use of inherently non-combustible cladding materials has surged. These include:
- Solid Aluminium Panels: Offering excellent fire performance (A1/A2), durability, and aesthetic versatility.
- Fibre Cement Boards: Highly fire-resistant (A1/A2) and durable.
- Terracotta and Ceramic Tiles: Natural, non-combustible (A1) facade materials.
- Glass Reinforced Concrete (GRC): Provides design flexibility and is non-combustible.
- Zinc and Copper Panels: Naturally fire-resistant metals offering distinctive aesthetics.
- Preferred Insulation Materials: Mineral wool (rock wool and glass wool) is now the almost exclusive choice for insulation in HRB external walls due to its A1 non-combustible rating. Other combustible insulation materials like PIR, PUR, and EPS have seen their use severely restricted or eliminated in these applications. (certifix.co.uk)
5.1.2 Innovation in Fire-Resistant Materials and Systems
While the focus has been on A1/A2 materials, there is also ongoing research and development into improving the fire performance of other materials and developing entirely new solutions. This includes:
- Enhanced Fire Retardants: For applications where some level of combustibility might still be permitted (e.g., lower-rise buildings or non-residential structures outside the scope of the ban), manufacturers are investing in more effective and environmentally friendly fire retardant technologies for products like HPL or timber.
- Hybrid Systems: Exploring integrated systems that combine the best properties of different materials to achieve both performance and safety goals, always prioritising non-combustibility for key elements.
- Sustainable and Fire-Safe Alternatives: The industry faces the dual challenge of achieving fire safety and sustainability. While some highly insulating materials (e.g., certain foams) have superior thermal performance but poor fire ratings, the drive is to innovate non-combustible materials that also offer excellent thermal insulation properties, or to design EWS that maximise energy efficiency with inherently fire-safe materials. This might involve thicker sections of mineral wool or vacuum insulation panels where appropriate.
5.1.3 Supply Chain Implications
The shift to non-combustible materials has placed increased demand on manufacturers of these products, potentially leading to supply chain pressures and price fluctuations. It has also required manufacturers to provide more transparent and rigorously tested data on their products’ fire performance, supporting the ‘Golden Thread’ concept.
5.2 Construction Practices
Regulatory changes have necessitated a fundamental re-evaluation and strengthening of construction practices, moving towards greater precision, accountability, and quality assurance on site.
5.2.1 Enhanced Training and Competence
- Increased Competence Requirements: The Building Safety Act places a strong emphasis on competence across the supply chain, from designers to installers. This means individuals involved in the construction of HRBs must demonstrate the necessary skills, knowledge, experience, and behaviours to ensure safety.
- Specialised Training: There is a growing demand for specialised training for operatives installing EWS, particularly regarding the precise installation of cavity barriers, fire stopping, and complex detailing around openings. Training now focuses not just on achieving aesthetic or thermal performance but primarily on strict adherence to fire safety specifications.
- Professional Accreditation: Industry bodies are developing and strengthening professional accreditation schemes and certifications for fire engineers, building safety managers, and other key roles to ensure a higher standard of expertise.
5.2.2 Quality Assurance and Control
- More Rigorous Inspections: Building control bodies and approved inspectors are conducting more frequent and intrusive inspections, particularly during critical stages of EWS installation (e.g., before cladding goes on, to verify insulation and barrier installation).
- Independent Verification: The use of independent third-party certification schemes for products and systems has become more prevalent, providing an extra layer of assurance that materials meet specified standards.
- Digital QA Tools: Construction firms are increasingly adopting digital platforms and photographic evidence systems to record every stage of the EWS installation process. This creates an auditable trail, verifying correct material use and installation, which feeds directly into the ‘Golden Thread’ of information.
- Mock-ups and Prototypes: For complex EWS designs, it is now common practice to construct full-scale mock-ups on or off-site. These allow for detailed checks of interfaces, buildability, and fire safety details before commencing work on the actual building, helping to identify and rectify potential issues early.
5.2.3 Documentation and Transparency (‘Golden Thread’ in Practice)
The ‘Golden Thread’ of information is transforming how building safety data is managed throughout the construction phase:
- Detailed Record Keeping: Contractors are now required to maintain highly detailed records of all EWS materials used (product names, manufacturers, batch numbers, fire ratings), installation methods, quality control checks, test certificates, and any deviations or remedial works. This information must be digitised and easily accessible.
- Information Management Systems: Investment in sophisticated information management systems (e.g., Common Data Environments – CDEs based on BIM principles) is increasing to host and manage this vast amount of safety-critical data, ensuring it is handed over comprehensively to the Accountable Person upon completion.
- Procurement Scrutiny: Procurement processes have become more stringent, with greater due diligence exercised on manufacturers’ claims and product certifications. Emphasis is placed on sourcing materials with verifiable fire performance data and robust third-party accreditation.
5.2.4 Integrated Design Approach
There is a growing trend towards an integrated design approach where fire engineers are involved from the earliest stages of a project alongside architects, structural engineers, and building services engineers. This ensures that fire safety considerations are embedded into the EWS design from its inception, rather than being an afterthought or a ‘bolt-on’ solution.
5.3 Liability Across the Supply Chain
The Building Safety Act fundamentally reallocated and amplified liability across the entire construction and building management supply chain. This shift aims to foster a culture of greater responsibility and accountability.
5.3.1 Clearer Contractual Obligations
- Enhanced Contractual Terms: Construction contracts now contain more explicit and stringent clauses delineating responsibilities for fire safety compliance, material specification, quality control, and the provision of accurate safety information. There is an increased focus on indemnities and warranties relating to EWS performance.
- Design and Build Liability: The traditional ‘design and build’ model, where a single contractor is responsible for both design and construction, now carries significantly increased liability, as that entity is responsible for the overall safety performance of the completed EWS.
5.3.2 Insurance and Warranties
- Professional Indemnity (PI) Insurance: Professionals involved in EWS design and specification (e.g., architects, fire engineers) face significantly higher PI insurance premiums and more restrictive policy terms due to the increased perceived risk. This has created challenges in securing appropriate cover.
- Latent Defects Insurance: Insurers providing latent defects insurance for new buildings are placing far greater scrutiny on EWS design and construction, demanding rigorous documentation and verification of compliance before offering policies.
- Product Liability: Manufacturers of construction products, including EWS components, face increased product liability risks, particularly for misrepresenting product performance or supplying defective materials. The BSA’s proposed reforms to the Construction Products Regulation will further strengthen this.
5.3.3 Regulatory Compliance and Enforcement
- Powers of the BSR: The Building Safety Regulator possesses extensive powers to enforce compliance, including issuing compliance notices, stop notices, and escalating enforcement actions. Non-compliance can lead to significant fines, reputational damage, and even criminal prosecution for individuals and corporations.
- Accountable Persons’ Liabilities: The introduction of the Accountable Person role places ongoing legal duties and potential liabilities on building owners/managers to ensure the safety of occupied HRBs, including their EWS. Failure to produce a Safety Case Report or manage risks adequately can result in severe penalties.
- Due Diligence: All parties in the supply chain – from raw material suppliers to building owners – are now expected to exercise a much higher degree of due diligence regarding the fire safety performance of EWS materials and their installation. This includes verifying certifications, understanding product limitations, and ensuring competent personnel are employed.
This landscape of heightened liability is intended to incentivise all stakeholders to prioritise building safety proactively, moving from a reactive response to failures to a preventative, safety-first culture ingrained at every stage of a building’s creation and operation.
Many thanks to our sponsor Focus 360 Energy who helped us prepare this research report.
6. Future Outlook and Recommendations
The tragic lessons of Grenfell Tower have initiated a profound and irreversible transformation in the UK’s approach to building safety, with External Wall Systems at the forefront of this paradigm shift. While significant progress has been made through comprehensive regulatory reforms, material innovation, and enhanced construction practices, the journey towards a fully safe and resilient built environment is ongoing. The future landscape will be defined by continued vigilance, adaptability to emerging challenges, and a sustained commitment to best practices.
6.1 Ongoing Challenges
Despite the legislative and industry reforms, several critical challenges persist:
- Remediation Backlog: Despite government funding and developer pledges, a substantial number of existing buildings across the UK still have non-compliant EWS. The pace of remediation, complicated by supply chain issues, skilled labour shortages, logistical complexities, and contractual disputes, remains a significant concern. The emotional and financial toll on affected leaseholders, although partially mitigated by the BSA, continues to be immense.
- Buildings Under 11 Metres: While the ban on combustibles was extended to 11 metres, buildings below this height are generally not subject to the same stringent A1/A2 material requirements, leading to ongoing debate about potential risks in these structures, particularly timber-framed buildings or those with specific design vulnerabilities. The focus of the BSA is primarily on HRBs (over 18m or 7 storeys), leaving a potential regulatory gap for lower-rise buildings that may still pose risks.
- Enforcement and Competence: The success of the new regulatory regime hinges on robust enforcement by the Building Safety Regulator and the widespread adoption of higher competence standards across the entire industry. Ensuring that all dutyholders fully understand and adhere to their new responsibilities and that there are sufficient competent professionals to deliver and oversee safe construction remains a long-term endeavour.
- Legacy Issues and Information Gaps: For older buildings, obtaining accurate, detailed information about the original EWS construction and materials can be extremely difficult, hindering effective risk assessment and remediation planning. The ‘Golden Thread’ concept, while transformative for new builds, cannot fully compensate for historical information deficits.
- Balancing Safety, Sustainability, and Affordability: The imperative for fire safety must be balanced with the urgent need for sustainable construction practices and the economic realities of building and retrofitting. Finding materials and systems that are both inherently fire-safe, environmentally friendly, and cost-effective represents a continuous research and development challenge.
6.2 Key Recommendations for the Future
To consolidate the gains made and address the lingering challenges, the following recommendations are crucial:
- Sustained Investment in Remediation: Governments and developers must maintain and potentially enhance funding mechanisms to accelerate the remediation of all unsafe EWS, ensuring that no leaseholder bears an unfair financial burden. Streamlining the funding application and approval processes is essential.
- Continuous Research and Development: Invest in ongoing scientific research into material fire performance, advanced fire modelling techniques, and the development of innovative, inherently non-combustible, and sustainable construction materials and EWS. This includes exploring modular construction techniques that can integrate fire safety more effectively off-site.
- Harmonisation of Standards and Best Practice: Foster greater international collaboration and, where appropriate, harmonisation of fire safety standards for EWS. Learning from global experiences and sharing best practices can strengthen regulatory frameworks worldwide.
- Education and Training: Implement comprehensive, mandatory, and ongoing education and training programmes for all stakeholders in the built environment sector – from architects and engineers to contractors, installers, and building managers. This will ensure widespread understanding of new regulations, competence requirements, and the critical importance of fire safety by design and installation.
- Digital Transformation of Building Safety: Fully embrace and implement the ‘Golden Thread’ of information for all new constructions and, where feasible, for existing buildings. Develop user-friendly, secure, and interoperable digital platforms for managing building safety information, facilitating proactive risk management and efficient regulatory oversight.
- Robust Enforcement and Audit: The Building Safety Regulator must be adequately resourced and empowered to rigorously enforce the new regulations, conduct proactive audits, and ensure accountability throughout the building lifecycle. A strong enforcement regime is critical to drive cultural change and deter non-compliance.
- Resident Engagement and Empowerment: Ensure that residents in multi-occupancy buildings are fully informed about the fire safety of their homes, have clear avenues for raising concerns, and are genuinely engaged in decisions relating to building safety management and remediation programmes.
- Review and Adaptability: The regulatory framework should be subject to periodic review and adaptation in response to new research, emerging technologies, and evolving understanding of fire risks. This ensures that regulations remain effective, proportionate, and future-proofed.
6.3 Concluding Thoughts
The Grenfell Tower fire served as a tragic, yet ultimately transformative, catalyst for profound changes in building safety regulations, particularly concerning External Wall Systems. The reforms enacted since 2017 represent a monumental shift towards a more rigorous, accountable, and safety-focused built environment. While significant progress has been made in enhancing fire safety through stringent regulatory reforms, material innovation, improved construction practices, and a clearer allocation of liability, substantial challenges remain in remediating the legacy of non-compliant buildings and ensuring unwavering ongoing compliance.
Ultimately, safeguarding occupants and preventing future tragedies demands continuous vigilance, a deep commitment to learning from past failures, and an unwavering dedication to embedding a proactive safety culture at every level of the construction and building management industries. The EWS, once an overlooked element, now stands as a symbol of this renewed commitment to building safety excellence.
Many thanks to our sponsor Focus 360 Energy who helped us prepare this research report.
References
- Certifix. (n.d.). The Evolving Regulatory Landscape Post-Grenfell. Retrieved from https://certifix.co.uk/blogs/news/the-evolving-regulatory-landscape-post-grenfell
- IJPiel. (2022, August 3). Grenfell and the Building Safety Act 2022. Retrieved from https://ijpiel.com/index.php/2022/08/03/grenfell-and-the-building-safety-act-2022/
- SHP Online. (2023, June 14). The aftermath of Grenfell: A comprehensive overview of UK’s building safety reforms. Retrieved from https://www.shponline.co.uk/fire-safety/the-aftermath-of-grenfell-a-comprehensive-overview-of-uks-building-safety-reforms/
- Emberly, D. (2022, May 18). Fire Safety: Lessons Learned From the Grenfell Tower Fire. Fire Engineering. Retrieved from https://emberly.fireengineering.com/fire-safety/lessons-learned-from-the-grenfell-tower-fire/
- Gateley Plc. (2022, August 2). External wall fire safety: first post-Grenfell liability judgement. Retrieved from https://gateleyplc.com/insight/article/external-wall-fire-safety-first-post-grenfell-liability-judgement/
- Wikipedia. (n.d.). BS 8414. Retrieved from https://en.wikipedia.org/wiki/BS_8414
- BDC Magazine. (2024, March 19). The effectiveness of new fire safety regulations post-Grenfell – what about buildings under 11 metres?. Retrieved from https://bdcmagazine.com/2024/03/the-effectiveness-of-new-fire-safety-regulations-post-grenfell-what-about-buildings-under-11-metres/
- Bevan Brittan. (2022, June 13). 5 years post-Grenfell: what have we learnt and are high-rise residential buildings now safe?. Retrieved from https://www.bevanbrittan.com/insights/articles/2022/5-years-post-grenfell-what-have-we-learnt-and-are-high-rise-residential-buildings-now-safe/
- The RPA Group. (n.d.). Regulatory Changes Post Grenfell. Retrieved from https://therpagroup.com/regulatory-changes-post-grenfell/
- Pinfa. (n.d.). Facade Fires and Consequences of Grenfell. Retrieved from https://www.pinfa.eu/news/facade-fires-and-consequences-of-grenfell/
- MyDek. (n.d.). External Wall Reforms Timeline 2017-2021. Retrieved from https://www.mydek.com/blogs/external-wall-reforms-timeline-2017-2021/
Given the focus on material selection post-Grenfell, how are manufacturers innovating to balance fire safety with sustainability and cost-effectiveness in EWS materials, particularly given the demand for non-combustible options?
That’s a great question! Many manufacturers are exploring innovative bio-based materials with inherent fire-resistant properties or developing advanced mineral wool insulation with enhanced thermal performance. The challenge lies in scaling these solutions while maintaining affordability and meeting rigorous safety standards. Collaboration between researchers, manufacturers, and policymakers is key!
Editor: FocusNews.Uk
Thank you to our Sponsor Focus 360 Energy
The report highlights the critical need for continuous research and development. How are current building designs adapting to incorporate passive fire protection measures alongside material advancements in EWS, such as novel arrangements of fire-stopping materials, and can you elaborate on their effectiveness?
Thanks for raising that important point! Integrating passive fire protection through innovative design is key. We’re seeing designs that maximise compartmentation, not just with fire-stopping, but with strategic material placement to slow fire spread. Testing and modelling are increasingly important to validating the overall system performance. This is an ongoing area of development!
Editor: FocusNews.Uk
Thank you to our Sponsor Focus 360 Energy
So, the “Golden Thread” – is that like building safety’s version of leaving a trail of breadcrumbs, but hopefully with less chance of getting eaten by a witch? I wonder if we’ll see it evolve into a fully-fledged digital twin situation soon.