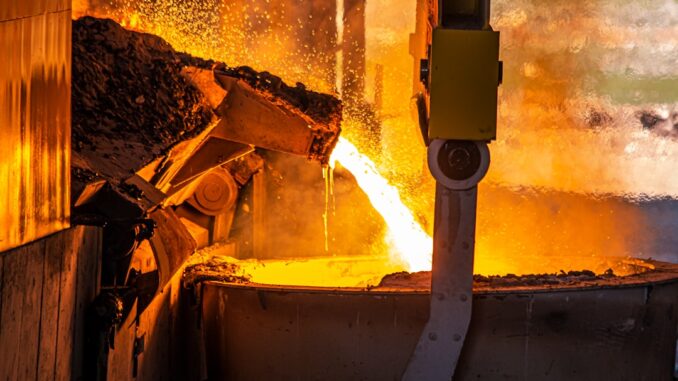
Abstract
The global steel industry stands as a colossal pillar of the modern economic and technological landscape, serving as the foundational material for virtually every sector from critical infrastructure and advanced manufacturing to groundbreaking technological advancements. This report undertakes an exhaustive and multi-dimensional analysis of the steel sector, meticulously detailing its intricate production processes, dissecting the geographical distribution of major producing nations, exploring the complex dynamics of its global markets, spotlighting the transformative impact of technological innovations, and critically assessing its profound environmental significance and the imperative for sustainable transformation. Through a rigorous examination of these interconnected facets, this comprehensive report endeavors to furnish stakeholders with an in-depth, nuanced, and forward-looking understanding of the industry’s current operational state, inherent challenges, and potential future trajectories, providing insights essential for strategic planning and sustainable development.
Many thanks to our sponsor Focus 360 Energy who helped us prepare this research report.
1. Introduction
Steel, primarily an alloy forged from iron and carbon, augmented by a diverse array of other elements to impart specific properties, has been an indispensable cornerstone of human civilization for millennia. From the rudimentary tools and weapons of antiquity to the towering skyscrapers and sophisticated machinery of the 21st century, its enduring versatility, unparalleled strength-to-weight ratio, and remarkable ductility have rendered it utterly indispensable across an astonishing spectrum of applications. The journey of steel from a nascent material in ancient metallurgy to a highly engineered product in the modern era mirrors the progression of human technological prowess and industrialization. Its inherent ability to be recycled without degradation further amplifies its long-term economic and environmental value.
Valued at well over $1 trillion annually, the global steel industry is far more than a simple manufacturing sector; it is an intricate web of complex global supply chains, characterized by profound capital intensity, a mosaic of diverse production methodologies, and a significant, pervasive influence on the global environment. The sheer scale of its operations and its pervasive integration into every facet of industrial and societal development underscore its strategic importance. Navigating the multifaceted nature of this colossal industry – from raw material extraction and processing to sophisticated steelmaking, global distribution, and end-of-life management – is paramount for all stakeholders. This includes governments shaping industrial policy, investors assessing market risks and opportunities, manufacturers relying on steel inputs, and environmental advocates pressing for sustainable practices. A deep, holistic understanding of the steel industry is not merely beneficial but unequivocally crucial for addressing its inherent challenges, capitalizing on its expansive opportunities, and steering it towards a resilient, efficient, and environmentally sustainable future.
Many thanks to our sponsor Focus 360 Energy who helped us prepare this research report.
2. Global Steel Production and Major Producing Countries
Global steel production, a benchmark of industrial might and economic activity, is primarily dominated by two fundamental processes, each with distinct characteristics and environmental footprints. The choice between these methods is often dictated by factors such as raw material availability, energy costs, existing infrastructure, and environmental regulations.
2.1 Production Processes
2.1.1 Blast Furnace-Basic Oxygen Furnace (BF-BOF) Process
The BF-BOF route, also known as the integrated steelmaking process, remains the predominant method globally, particularly for producing large volumes of virgin steel. This process is highly reliant on iron ore, coking coal, and limestone as primary raw materials. The journey begins with the beneficiation of iron ore, where raw ore is crushed, ground, and enriched to increase its iron content, often formed into pellets or sinter for optimal performance in the blast furnace.
The Blast Furnace (BF): This colossal structure acts as a counter-current reactor. Iron ore, coke (a carbon-rich fuel produced by heating coal in the absence of oxygen), and flux (limestone) are fed into the top of the furnace. Hot air, often enriched with oxygen, is blasted into the bottom. The coke serves multiple critical functions: it acts as a fuel, providing the intense heat necessary for the process, and as a reducing agent, reacting with iron oxides to reduce them to metallic iron. The limestone acts as a flux, combining with impurities in the ore and coke to form a molten slag, which floats atop the denser molten iron (often referred to as ‘hot metal’ or ‘pig iron’). The chemical reactions are complex, involving the reduction of iron oxides by carbon monoxide and direct carbon. The molten iron, typically containing 4-4.5% carbon and other impurities, is periodically tapped from the bottom of the furnace.
The Basic Oxygen Furnace (BOF): The hot metal from the blast furnace is transported in refractory-lined ladles to the BOF. Here, a high-purity oxygen lance is lowered into the molten metal, blowing oxygen at supersonic speeds onto the surface. This oxygen reacts violently with the carbon and other impurities (such as silicon, manganese, and phosphorus) present in the hot metal, oxidizing them. The oxidation generates immense heat, raising the temperature of the bath and melting scrap steel, which is often added for temperature control and to utilize recycled material. Fluxes (lime and dolomite) are added to form a slag that absorbs the oxidized impurities. The process is rapid, typically taking 15-20 minutes, and produces molten steel with a significantly lower carbon content (around 0.03-1.5% carbon, depending on grade) and reduced impurities.
Secondary Metallurgy and Continuous Casting: After the BOF, the molten steel undergoes secondary metallurgy in ladle furnaces, vacuum degassers, or other treatment stations. Here, precise alloying elements are added, and impurities like sulfur and phosphorus are further refined, and dissolved gases are removed, ensuring the steel meets specific metallurgical and quality requirements for its intended application. Finally, the refined molten steel is cast into semi-finished products such as slabs, blooms, or billets through a continuous casting process. These semi-finished products are then further processed (e.g., hot rolling, cold rolling) into finished steel products like sheets, plates, bars, or structural shapes.
2.1.2 Electric Arc Furnace (EAF) Process
In contrast to the BF-BOF route, the EAF process primarily relies on recycled steel scrap as its main raw material, making it inherently more energy-efficient and environmentally advantageous in terms of virgin material consumption and carbon emissions per tonne of steel. While some EAFs use a blend of scrap and direct reduced iron (DRI) or hot briquetted iron (HBI), scrap typically constitutes the vast majority of the charge.
Scrap Preparation: The quality and consistency of scrap are crucial for efficient EAF operation. Scrap undergoes various processing steps, including sorting, shredding, baling, and removing contaminants, to ensure a high-quality charge for the furnace.
Electric Arc Furnace Operation: The EAF itself is a large, refractory-lined vessel with a movable roof through which graphite electrodes are inserted. Scrap steel is loaded into the furnace, and high-current electric arcs are struck between the electrodes and the scrap, generating intense heat (up to 3,500 °C). This radiant heat melts the scrap. Oxygen is often injected to promote exothermic reactions that further melt the scrap and remove impurities like carbon and phosphorus. Fluxes (lime, dolomite) are added to form a slag that absorbs impurities. The EAF offers significant flexibility in terms of batch size and product mix. Unlike the continuous nature of a blast furnace, EAFs operate in batches, allowing for quick shifts in steel grades based on market demand.
Advantages and Disadvantages: The EAF process offers several key advantages: lower capital expenditure compared to BF-BOF, greater operational flexibility, significantly reduced energy consumption from virgin materials, and lower CO2 emissions per tonne of steel due to its reliance on recycled content. It typically produces steel with lower impurity levels, especially nitrogen. However, its major limitation is its reliance on high-quality scrap, the availability and price of which can be volatile. Producing certain ultra-low carbon or highly specialized steel grades requiring extremely pure iron units can also be more challenging with a 100% scrap charge.
2.1.3 Emerging Processes: Direct Reduced Iron (DRI) and Hydrogen-Based Steelmaking
Direct Reduced Iron (DRI) production involves reducing iron ore in its solid state using a reducing gas (typically natural gas, but increasingly hydrogen or syngas) in a shaft furnace or fluidized bed reactor, without melting. The resulting DRI can then be fed into an EAF, effectively providing a ‘virgin’ iron unit source that is less carbon-intensive than pig iron from a blast furnace. The ultimate evolution of this process is Hydrogen-based Direct Reduced Iron (H-DRI), where hydrogen replaces natural gas as the primary reductant. This method has the potential to virtually eliminate direct carbon emissions from the ironmaking step, as the primary by-product is water vapor. While still in early stages of commercialization for large-scale operations, significant pilot projects are underway globally, representing a critical pathway towards ‘green steel’ production. The adoption of these processes depends on the availability and cost of renewable energy and green hydrogen, as well as the necessary infrastructure.
2.2 Leading Steel Producers
As of 2024, the global steel landscape is heavily concentrated among a few dominant players, reflecting geopolitical influence, economic scale, and strategic resource endowments. The list of top steel-producing countries typically includes China, India, Japan, the United States, and Russia, alongside others like South Korea, Germany, Turkey, and Brazil. The World Steel Association consistently tracks and publishes these figures, highlighting the dynamic shifts in production.
China: China remains by far the world’s largest steel producer, consistently accounting for approximately 50% of global crude steel output, a position it has maintained for over a decade. This dominance is a direct result of its unprecedented economic growth, massive infrastructure development initiatives (such as the Belt and Road Initiative), rapid urbanization, and a robust manufacturing base. The Chinese steel industry is characterized by a mix of state-owned enterprises (SOEs) and large private companies, many of which are among the largest steel manufacturers globally (e.g., China Baowu Group). While its capacity has faced calls for rationalization due to oversupply concerns in the past, China’s domestic demand coupled with its export prowess continues to drive its production volumes.
India: India has rapidly ascended to become the second-largest steel producer globally, surpassing traditional giants like Japan and the United States. This surge is fueled by a rapidly expanding economy, significant infrastructure investments (e.g., national highway projects, smart cities), a burgeoning automotive sector, and a large domestic consumption base. India also possesses substantial domestic reserves of iron ore and coal, providing a cost advantage. The country’s steel sector is undergoing modernization and capacity expansion, aiming to meet future domestic demand and enhance its position in the global market.
Japan: Historically a powerhouse in steel production, Japan remains a significant player, renowned for its advanced steelmaking technologies, high-quality specialized steel products, and focus on innovation. Japanese steel companies (e.g., Nippon Steel) excel in producing high-performance steels for demanding applications in the automotive, shipbuilding, and electronics industries. While its absolute production volume might be overshadowed by China and India, Japan’s focus on value-added products and technological leadership ensures its continued global importance.
United States: The U.S. steel industry has undergone a significant transformation, largely pivoting towards the Electric Arc Furnace (EAF) route. The U.S. is a global leader in EAF steelmaking, relying heavily on abundant domestic scrap resources. This shift has made the U.S. industry more environmentally efficient and flexible. Key demand drivers include construction, automotive, and energy sectors. Trade policies, such as Section 232 tariffs, have also played a role in shaping the domestic market and protecting local producers from what is perceived as unfair competition.
Russia: Russia’s steel production is largely driven by its vast natural resources, including iron ore and natural gas (which supports DRI production), and its integrated metallurgical complexes. Its steel industry serves both domestic demand and is a major exporter, particularly to European and Asian markets. Geopolitical factors and international sanctions have, however, introduced significant volatility and challenges for its export-oriented steel sector.
Other notable producers include South Korea (highly efficient, export-oriented, specializing in shipbuilding and automotive steel), Germany (focus on high-quality, specialty steels for automotive and machinery, with strong emphasis on R&D), Turkey (a major EAF-based producer and a significant importer of scrap, serving construction and export markets), and Brazil (leveraging its vast iron ore reserves, producing both for domestic use and export).
Many thanks to our sponsor Focus 360 Energy who helped us prepare this research report.
3. Market Dynamics and Economic Significance
The global steel market is a complex interplay of demand-side drivers, supply-side capabilities, and external factors like trade policies, geopolitical events, and technological shifts. Its economic significance is profound, as steel serves as a foundational material for almost all industrial and infrastructure development.
3.1 Demand Drivers
The demand for steel is intrinsically linked to global economic growth, urbanization rates, and the pace of industrialization, making it a bellwether for the health of the world economy. Several key sectors consistently drive steel consumption:
Infrastructure Development: This is arguably the most significant and consistent demand driver. As economies grow, there is an inexorable need for robust infrastructure. This includes the construction of new roads, bridges, railways, ports, airports, and public utilities (water and sewage systems, power grids). In emerging economies, particularly across Asia and Africa, massive infrastructure projects are underway or planned, requiring vast quantities of rebar, structural shapes, pipes, and plates. Even in developed economies, maintenance, modernization, and expansion of aging infrastructure continue to generate substantial demand. For instance, the expansion of high-speed rail networks or the development of smart city infrastructure necessitates specialized steel grades for durability and performance.
Construction: Beyond public infrastructure, the residential and commercial building sectors are enormous consumers of steel. High-rise buildings, shopping malls, industrial complexes, and data centers all rely heavily on steel for their structural frameworks, reinforcement, roofing, and cladding. Architectural trends favoring open-plan designs and large spans often necessitate high-strength steel solutions. The shift towards modular construction and prefabrication also influences the types of steel products demanded.
Automotive Industry: The automotive sector is a critical consumer of steel, particularly advanced high-strength steels (AHSS) and ultra-high-strength steels (UHSS). These materials enable car manufacturers to produce lighter vehicles that meet stringent fuel efficiency and emission standards while simultaneously enhancing passenger safety through improved crashworthiness. The ongoing transition towards electric vehicles (EVs) is reshaping demand: while EVs may use less traditional body steel due to battery integration, they require specialized electrical steels (silicon steel) for electric motors and high-strength steels for battery enclosures and chassis components, presenting new opportunities and challenges for steelmakers.
Manufacturing and Machinery: Steel is the backbone of the manufacturing sector, forming the basis for a vast array of machinery and equipment, from heavy industrial machinery used in mining and agriculture to precision tools, consumer appliances (refrigerators, washing machines), and industrial robots. The resilience and malleability of steel make it ideal for components subjected to high stress and wear.
Energy Sector: The global energy transition is spurring new demand for specialized steel products. Renewable energy technologies, such as wind turbines (which require immense steel towers, nacelles, and foundations), solar panel frames, and geothermal power plants, are highly steel-intensive. The oil and gas sector, despite the transition, continues to demand high-grade steel for pipelines, drilling equipment, and offshore platforms. Additionally, the development of hydrogen infrastructure, including storage tanks and pipelines, will create demand for specific steel alloys capable of handling hydrogen.
Shipbuilding and Marine Applications: The maritime industry relies heavily on steel for the construction of cargo ships, tankers, passenger vessels, and offshore structures. High-tensile strength steels are crucial for reducing vessel weight and enhancing fuel efficiency.
General Economic Growth: Ultimately, steel demand correlates strongly with global GDP growth. A thriving global economy typically translates into increased investment in infrastructure, manufacturing, and consumer goods, all of which are steel-intensive. Urbanization, particularly in rapidly developing regions, fuels construction booms and necessitates expanded urban infrastructure, directly boosting steel consumption.
3.2 Trade and Tariffs
Global steel trade is a highly sensitive and often contentious arena, profoundly shaped by a confluence of economic, political, and geopolitical factors. The imposition of tariffs, quotas, and other trade barriers can significantly disrupt established supply chains, distort pricing mechanisms, and escalate into protracted trade disputes, impacting global market stability and profitability.
Global Trade Flows: Major steel exporters include China, Japan, South Korea, Russia, and the EU, while key importers include the United States, EU member states, and various developing nations. The volume and direction of these flows are influenced by domestic demand-supply balances, production costs, and exchange rates.
Overcapacity and Trade Remedies: A persistent challenge in the global steel industry has been the issue of overcapacity, particularly stemming from certain regions. When domestic demand cannot absorb production, excess steel is often exported, which can depress international prices and lead to allegations of unfair trade practices, such as dumping (selling goods below production cost or home market price) or the provision of unfair subsidies. To counteract these perceived injustices, countries frequently resort to trade remedies allowed under World Trade Organization (WTO) rules. These include:
- Anti-dumping (AD) duties: Imposed when imported goods are found to be sold at less than their normal value, causing material injury to a domestic industry.
- Countervailing duties (CVD): Applied to offset subsidies provided by foreign governments that distort trade.
- Safeguard measures: Temporary restrictions on imports imposed to protect a domestic industry seriously injured or threatened with serious injury by a surge in imports.
Case Study: U.S. Section 232 Tariffs: A prominent example of the impact of tariffs is the U.S. imposition of Section 232 tariffs on steel imports in 2018. Citing national security concerns, the U.S. applied a 25% tariff on steel imports from most countries. The stated aim was to protect and revitalize the domestic steel industry. This action led to retaliatory tariffs from affected trading partners (e.g., EU, Canada, Mexico, China), sparking trade disputes and disrupting global steel trade patterns. While proponents argued it bolstered domestic production and employment, critics pointed to increased input costs for downstream industries, reduced competitiveness for exporters using steel, and broader trade tensions.
Impacts of Trade Restrictions:
- Increased Domestic Prices: Tariffs tend to raise the price of imported steel, allowing domestic producers to increase their prices.
- Supply Chain Disruptions: Importers may scramble to find new suppliers or pay higher costs, leading to supply chain inefficiencies.
- Reduced Competitiveness for Downstream Industries: Manufacturers who use steel as an input may face higher costs, making their finished products less competitive globally.
- Retaliation and Trade Wars: Unilateral tariff actions often invite retaliatory measures, escalating trade tensions and negatively impacting global trade volumes.
- Diversion of Trade: Steel products may be diverted to other markets not subject to tariffs, creating price pressures elsewhere.
Role of WTO and Regional Agreements: The WTO provides a framework for international trade rules, aiming to ensure fair competition. However, the use of trade remedies often tests the limits of these rules. Regional trade agreements (e.g., USMCA, EU’s various agreements) also shape steel trade by offering preferential tariffs or establishing specific rules of origin, further fragmenting the global market into regional blocs.
Many thanks to our sponsor Focus 360 Energy who helped us prepare this research report.
4. Technological Innovations in Steel Production
The steel industry, traditionally perceived as conservative, is undergoing a profound technological transformation driven by the twin imperatives of efficiency and sustainability. The integration of advanced digital technologies and the pursuit of radically new production methodologies are reshaping its future.
4.1 Automation and Digitalization (Industry 4.0)
The advent of Industry 4.0 technologies has ushered in a new era for steel production, promising unprecedented levels of efficiency, productivity, and safety. The digital transformation encompasses the entire value chain, from raw material handling to finished product dispatch.
Artificial Intelligence (AI) and Machine Learning (ML): AI and ML algorithms are being deployed to optimize complex processes. For instance, predictive maintenance models, leveraging sensor data from machinery (vibration, temperature, current, acoustic signatures), can forecast equipment failures before they occur (Jakubowski et al., 2024). This proactive approach minimizes unscheduled downtime, reduces maintenance costs, and extends equipment lifespan. In quality control, AI-powered vision systems can detect surface defects on hot rolled steel coils with greater speed and accuracy than human inspection, ensuring consistent product quality. ML algorithms also optimize energy consumption in EAFs by predicting ideal power settings based on scrap composition and desired steel grade, or by optimizing the coking process in BF-BOF operations.
Internet of Things (IoT): The IoT involves deploying a vast network of interconnected sensors and devices throughout the steel plant. These sensors collect real-time data on parameters such as temperature, pressure, flow rates, chemical composition, and equipment performance. This deluge of data feeds into centralized control systems and analytical platforms, providing operators with comprehensive insights into the entire production process. Real-time monitoring allows for immediate adjustments to process parameters, preventing deviations and ensuring optimal performance. For example, IoT sensors in continuous casting can monitor mold levels and cooling rates to prevent defects, or track the composition of molten metal in secondary metallurgy to ensure precise alloying.
Digital Twins: A digital twin is a virtual replica of a physical asset, process, or system. In the steel industry, digital twins of blast furnaces, EAFs, rolling mills, or even entire production lines can be created. These twins are fed real-time data from IoT sensors, allowing for continuous simulation and analysis of the physical asset’s behavior. Operators can use digital twins to test different operational scenarios, predict outcomes, identify bottlenecks, and optimize processes in a virtual environment before implementing changes in the physical plant, thereby reducing risks and improving decision-making.
Robotics and Automation: Automation is increasingly prevalent in hazardous or repetitive tasks. Robotic systems are used for tasks like slag skimming, sampling, refractory repair, and material handling, significantly improving worker safety and consistency. Automated guided vehicles (AGVs) transport materials within the plant, optimizing logistics and reducing human error. Robotic ladle tending systems ensure precise and safe handling of molten metal.
Supply Chain Optimization: Digital platforms and AI are enhancing supply chain visibility and efficiency. This includes optimizing raw material procurement, managing inventory levels, scheduling production to meet demand, and streamlining logistics for product delivery. Blockchain technology is also being explored for its potential to enhance transparency and traceability within the steel supply chain, ensuring ethical sourcing and validating ‘green steel’ claims.
4.2 Sustainable Production Methods
The steel industry is under immense pressure to decarbonize, given its substantial carbon footprint. Innovations in sustainable production methods aim to significantly reduce greenhouse gas emissions and resource consumption, aligning with global climate targets.
Hydrogen-Based Direct Reduction (H-DR): This is one of the most promising pathways to ‘green steel’ (Souza Filho et al., 2022). Traditional direct reduction typically uses natural gas as a reductant, producing CO2. In H-DR, hydrogen (preferably ‘green hydrogen’ produced via electrolysis powered by renewable energy) replaces natural gas. The hydrogen reacts with iron ore (often in pellet form) at high temperatures in a shaft furnace to produce direct reduced iron (DRI) and water vapor (H2O), eliminating CO2 emissions from the ironmaking step. The resulting H-DRI can then be melted in an Electric Arc Furnace (EAF) powered by renewable electricity to produce steel with drastically lower emissions. While technically viable, the main challenges are the high cost and limited availability of green hydrogen, and the significant investment required for new H-DR plants or retrofitting existing DRI facilities.
Carbon Capture, Utilization, and Storage (CCUS): For existing BF-BOF plants, CCUS technologies offer a potential solution to mitigate emissions. This involves capturing CO2 emissions directly from the flue gases of steelmaking facilities. Once captured, the CO2 can either be stored permanently underground in geological formations (carbon storage) or utilized as a feedstock for other industrial processes (carbon utilization), such as producing synthetic fuels, chemicals, or building materials. While CCUS can significantly reduce emissions from conventional steelmaking, its deployment faces challenges related to high capital and operating costs, energy intensity of capture, and the availability of suitable storage sites (International Energy Agency, 2020).
Enhanced Electric Arc Furnace (EAF) Efficiency and Renewable Energy Integration: As EAFs inherently have lower emissions due to their reliance on scrap, improving their efficiency and powering them with renewable electricity is a key decarbonization strategy. Innovations include: preheating scrap before charging into the EAF to reduce energy consumption; optimizing slag foaming for better heat transfer; and utilizing smart control systems. Crucially, connecting EAFs to grids supplied predominantly by wind, solar, and hydropower significantly reduces the indirect (scope 2) emissions associated with electricity consumption.
Bio-based Reductants: Research is ongoing into using sustainable biomass (e.g., charcoal, agricultural waste) as a partial or full replacement for coal/coke in blast furnaces or as a reductant in other ironmaking processes. This can reduce the reliance on fossil fuels and potentially offer a more carbon-neutral alternative if the biomass is sourced sustainably.
Waste Heat Recovery: Steelmaking processes generate substantial amounts of waste heat. Technologies that capture and convert this heat into electricity or use it for other industrial purposes (e.g., district heating) improve overall energy efficiency and reduce the need for external energy sources, thereby lowering emissions.
Circular Economy Principles: Beyond direct production, the industry is increasingly embracing circular economy principles. This involves maximizing the recycling of steel scrap (as discussed below), but also finding innovative ways to reuse or reprocess steelmaking by-products such as slag (for cement or road construction), dust (for metal recovery), and gases (for energy generation or chemical feedstock). This reduces waste, conserves raw materials, and minimizes environmental impact.
These technological advancements are not merely incremental improvements but represent a paradigm shift towards a more sustainable and digitally integrated steel industry. However, their widespread adoption requires substantial investment, supportive policy frameworks, and collaborative efforts across the value chain.
Many thanks to our sponsor Focus 360 Energy who helped us prepare this research report.
5. Environmental Impact and Sustainability Challenges
The global steel industry faces an existential challenge in reconciling its economic indispensability with its significant environmental footprint. As a cornerstone of industrial society, its operations have pervasive effects on climate, natural resources, and local ecosystems.
5.1 Carbon Emissions
Steel production is one of the most carbon-intensive industrial sectors globally, accounting for approximately 7-9% of total anthropogenic greenhouse gas (GHG) emissions (International Energy Agency, 2020). The vast majority of these emissions originate from the traditional blast furnace-basic oxygen furnace (BF-BOF) route.
Sources of Emissions in BF-BOF:
- Coke Production: The coking process, where coal is heated to produce coke, releases significant CO2, methane, and other volatile organic compounds.
- Blast Furnace: The primary source of emissions is the reduction of iron ore using coke. Carbon from the coke acts as the reducing agent, reacting with oxygen in the iron ore to produce carbon monoxide (CO), which further reduces the iron oxides. This CO is then oxidized to CO2. Additionally, the combustion of fuels to heat the blast furnace contributes to emissions.
- Sintering and Pelleting: These pre-treatment processes for iron ore also require energy, often from fossil fuels, leading to emissions.
- Energy Consumption: The entire integrated process is highly energy-intensive, requiring large amounts of electricity and heat, often generated from fossil fuels, contributing to both direct (Scope 1) and indirect (Scope 2) emissions.
Emissions from EAF: While significantly lower than BF-BOF, EAFs still have a carbon footprint. Direct emissions come from electrodes (which oxidize to CO2), small amounts of carbon injection, and the combustion of natural gas for heating or oxygen injection. Indirect emissions arise from the electricity consumed. If the electricity grid relies heavily on fossil fuels, the EAF’s overall carbon footprint remains substantial. This highlights the critical importance of decarbonizing the electricity grid for truly ‘green’ EAF steel.
Global Climate Targets and the ‘Hard-to-Abate’ Challenge: Achieving the Paris Agreement goals of limiting global warming to well below 2°C, preferably to 1.5°C, necessitates drastic reductions in industrial emissions. The steel sector is classified as a ‘hard-to-abate’ sector due to the high temperatures and large quantities of carbon required for the chemical reduction of iron ore. Transitioning to greener technologies like hydrogen-based steelmaking or widespread CCUS deployment is capital-intensive, technologically complex, and requires significant infrastructure development for hydrogen production, transport, and CO2 storage. Many steel companies are ‘yet to prove their mettle’ in their commitment to net-zero targets, with a significant portion of planned capacity still relying on coal (Reuters, 2024; Global Energy Monitor, 2025).
Other Environmental Pollutants: Beyond GHG emissions, steel production is associated with other environmental impacts:
- Air Pollution: Emissions of sulfur oxides (SOx), nitrogen oxides (NOx), particulate matter (PM2.5, PM10), and heavy metals from various stages of production can contribute to acid rain, smog, and respiratory diseases.
- Water Pollution: Water is used extensively for cooling, cleaning, and material transport. Discharges can contain suspended solids, heavy metals, oil and grease, and other pollutants if not properly treated.
- Waste Generation: Slag (a by-product of both BF and EAF processes), dust, and sludge are generated in large quantities. While efforts are made to re-use these materials, their disposal can pose challenges.
- Land Use: Mining of iron ore, coal, and limestone, as well as waste disposal sites, requires significant land, leading to habitat disruption and ecosystem degradation.
5.2 Recycling and Circular Economy
Promoting a robust circular economy within the steel industry is not merely beneficial but essential for achieving its sustainability goals. Steel is unique among major industrial materials for its infinite recyclability without loss of intrinsic properties, making it a perfectly circular material if managed correctly.
Benefits of Steel Recycling:
- Resource Conservation: Recycling steel significantly reduces the need for virgin iron ore and coal extraction, conserving finite natural resources.
- Energy Savings: Producing steel from scrap via the EAF route consumes significantly less energy (up to 75% less) compared to producing it from virgin raw materials in a BF-BOF (Wikipedia, 2024). This directly translates to reduced energy costs and associated emissions.
- Emissions Reduction: The lower energy consumption and avoidance of carbon-intensive blast furnace operations mean that steel recycling drastically cuts CO2 emissions per tonne of steel produced.
- Waste Reduction: Recycling diverts steel scrap from landfills, reducing waste volume and preventing potential environmental contamination from discarded materials.
- Economic Benefits: The scrap industry creates jobs in collection, processing, and transportation. Recycled steel also offers a competitive input material for steelmakers.
Challenges in Steel Recycling:
- Scrap Quality and Contamination: The purity of recycled steel is a critical concern. Contaminants (such as copper, tin, nickel, chromium) in scrap can negatively impact the quality and properties of the new steel, limiting its application or requiring costly purification steps. Effective sorting and processing technologies are crucial to minimize contamination.
- Global Scrap Trade: Scrap is a globally traded commodity. The availability and price of high-quality scrap can fluctuate significantly based on regional supply and demand, geopolitical factors, and trade policies (e.g., export restrictions on scrap in some countries).
- Collection Infrastructure: Ensuring efficient collection and processing of end-of-life steel products from diverse sources (demolished buildings, scrapped vehicles, discarded appliances) requires robust collection infrastructure and consumer awareness.
- Life Cycle Management: While steel is highly recyclable, ensuring that steel products are designed for disassembly and ease of recycling at the end of their life cycle is important for maximizing circularity.
- Downcycling Risk: Without proper sorting and advanced processing, there’s a risk of ‘downcycling,’ where high-grade steel is recycled into lower-grade applications due to contamination.
Role of By-product Utilization: Beyond scrap, maximizing the utilization of steelmaking by-products, especially slag, is another facet of the circular economy. Steel slag can be used in cement production, road construction, and as an agricultural soil improver, reducing reliance on virgin materials in these sectors and minimizing waste. The recovery of valuable metals from dust and sludge further enhances resource efficiency.
Advancing a truly circular economy for steel requires concerted efforts from policymakers (to encourage collection and recycling), industry (to invest in advanced sorting and processing technologies, and to design for recyclability), and consumers (to participate in collection programs). It is a key enabler for the industry’s sustainable transformation.
Many thanks to our sponsor Focus 360 Energy who helped us prepare this research report.
6. Future Outlook and Strategic Considerations
The global steel industry is navigating a period of unprecedented transformation, driven by shifting market demands, technological breakthroughs, and an urgent mandate for environmental sustainability. Its future will be shaped by how it responds to these interwoven pressures.
6.1 Market Trends
The steel market’s future will be characterized by evolving demand patterns and regional growth disparities.
Growth in Emerging Markets: While mature economies may see stable or modest growth, the primary drivers of increased steel demand will continue to be emerging economies, particularly in Asia, Africa, and parts of Latin America (EOXS, 2024). Rapid urbanization, population growth, and ambitious infrastructure development plans in these regions will necessitate vast quantities of steel for housing, transportation networks, energy projects, and industrial expansion. Countries like India, Indonesia, Vietnam, and various African nations are poised for significant increases in steel consumption as their economies industrialize and their middle classes expand.
Electric Vehicles (EVs): The accelerating global transition to electric vehicles represents a nuanced demand shift for the steel industry. While some estimates suggest a slight reduction in overall steel per vehicle due to battery weight and design changes, the demand for specialized steel grades will intensify. This includes:
* Advanced High-Strength Steels (AHSS): Critical for lighter vehicle body structures that offset battery weight, improve crash safety, and extend range. AHSS and UHSS (Ultra High Strength Steels) enable thinner gauges without compromising strength.
* Electrical Steels (Silicon Steel): Essential for the electric motors of EVs, where high magnetic permeability and low core losses are crucial for efficiency.
* Battery Enclosures: Demand for steel to house and protect large battery packs, often requiring specific properties for thermal management and impact resistance.
* Charging Infrastructure: Steel will be needed for the expanding network of EV charging stations.
Renewable Energy Infrastructure: The global push towards decarbonization mandates a massive build-out of renewable energy capacity, all of which is highly steel-intensive:
* Wind Turbines: Require immense amounts of steel for towers, foundations, nacelles, and internal components, particularly for larger offshore turbines.
* Solar Power: Steel is used in the support structures for solar panels, mounting systems, and components for concentrated solar power (CSP) plants.
* Transmission and Distribution: Expanding and upgrading electricity grids to handle intermittent renewable sources will require significant quantities of steel for transmission towers and related infrastructure.
* Energy Storage: While batteries are often the focus, steel is also used in structural components for battery energy storage systems, and potentially in future hydrogen storage tanks and pipelines.
Digital Infrastructure: The expanding digital economy fuels demand for steel in data centers (for structural elements and racks), 5G network towers, and fiber optic cable protection.
Resource Nationalism and Supply Chain Resilience: Growing geopolitical tensions and the lessons from recent supply chain disruptions (e.g., COVID-19, geopolitical conflicts) are prompting countries and companies to prioritize supply chain resilience and, in some cases, resource nationalism. This could lead to a preference for domestic or regionally sourced steel, impacting global trade flows and potentially encouraging localized production or diversification of suppliers.
6.2 Policy and Regulatory Landscape
Government policies and international agreements will be pivotal in shaping the steel industry’s trajectory, particularly regarding its decarbonization efforts. The trend is towards stricter environmental regulations and economic incentives for sustainable practices.
Carbon Pricing Mechanisms:
* Carbon Taxes: Direct taxes on carbon emissions, making high-carbon production more expensive. This incentivizes companies to invest in cleaner technologies.
* Emissions Trading Systems (ETS): Cap-and-trade systems, like the European Union’s ETS, set a cap on total emissions and allow companies to buy or sell allowances. This creates a market price for carbon, rewarding efficient producers and penalizing polluters. The steel industry is often included in these schemes, facing increasing costs for their emissions.
Border Carbon Adjustment Mechanisms (CBAMs): To prevent ‘carbon leakage’ (where industries relocate to regions with less stringent climate policies), countries like the EU are implementing CBAMs. This mechanism applies a carbon cost to imported goods, including steel, based on their embedded emissions, aiming to level the playing field for domestic producers facing carbon costs. Such measures will profoundly influence global steel trade patterns and incentivize decarbonization across supply chains.
Green Steel Incentives: Governments are increasingly offering financial and regulatory support for green steel production:
* Subsidies and Grants: Direct financial aid for research, development, and deployment of innovative low-carbon steelmaking technologies (e.g., hydrogen-based DRI plants).
* Tax Breaks and Loan Guarantees: Incentives to reduce the financial burden of transitioning to greener processes.
* Public Procurement Policies: Governments can use their purchasing power to create demand for green steel by mandating its use in public infrastructure projects or requiring suppliers to demonstrate low-carbon credentials. This provides a crucial ‘pull factor’ for green steel market development.
* ResponsibleSteel and Other Standards: Industry-led initiatives like ResponsibleSteel provide certification schemes that verify sustainable production practices across environmental, social, and governance (ESG) criteria. These standards can influence procurement decisions and investor confidence.
International Collaboration: Global forums and agreements are crucial for harmonizing regulations, sharing best practices, and facilitating the cross-border transfer of green technologies. Multilateral efforts can help address the global nature of emissions and trade challenges.
6.3 Investment and Finance
Transitioning to green steel is incredibly capital-intensive, requiring trillions of dollars globally over the coming decades. Securing adequate financing is a major strategic consideration.
Challenges in Financing Green Steel:
* High Upfront Costs: Building new hydrogen-based DRI plants or retrofitting existing facilities is immensely expensive, often requiring multi-billion dollar investments.
* Technological Risk: While promising, some green steel technologies are still maturing, carrying inherent technological and operational risks that can deter traditional investors.
* Uncertainty of Returns: The market for green steel is still nascent, and premium prices for low-carbon products are not yet fully established, leading to uncertainty about returns on investment.
* Hydrogen Availability and Cost: The viability of hydrogen-based steelmaking is directly tied to the reliable and affordable supply of green hydrogen, which currently faces infrastructure and production scale-up challenges.
Role of Sustainable Finance:
* Green Bonds and Loans: Financial instruments specifically designed to fund environmentally sustainable projects are becoming increasingly important for steelmakers. These offer attractive terms for investors seeking ESG-aligned investments.
* Blended Finance: Combining public and private capital to de-risk projects and make them more attractive to private investors.
* Carbon Credits and Offsets: The revenue generated from carbon credit markets or the avoidance of carbon taxes can improve the financial viability of green steel projects.
* Venture Capital and Climate Funds: Specialized funds are emerging to support innovative climate technologies, including those applicable to steelmaking.
Investors are increasingly scrutinizing the ESG performance of steel companies. Those demonstrating clear decarbonization strategies and robust sustainability commitments are likely to attract more favorable financing and maintain a competitive edge in a carbon-constrained world. Conversely, companies perceived as lagging in their environmental transition may face higher capital costs and diminished access to finance.
Many thanks to our sponsor Focus 360 Energy who helped us prepare this research report.
7. Conclusion
The global steel industry finds itself at a truly pivotal juncture, confronting the dual imperatives of sustaining robust economic growth while simultaneously addressing the urgent demands of environmental sustainability. Its future success hinges on its ability to navigate this complex landscape, which is characterized by dynamic market shifts, the necessity for profound technological innovation, and an evolving regulatory environment.
Achieving significant decarbonization, particularly for the hard-to-abate steel sector, demands colossal investments in groundbreaking technologies such as hydrogen-based direct reduction and advanced carbon capture. These transitions are not merely technical challenges but also economic ones, requiring substantial capital, access to affordable renewable energy, and a supportive policy ecosystem that rewards early movers and penalizes inaction. The widespread adoption of Industry 4.0 technologies – encompassing AI, IoT, and digital twins – is essential for optimizing existing processes, enhancing efficiency, and improving safety, laying the digital groundwork for future sustainable operations.
Furthermore, the industry’s commitment to circular economy principles, especially through maximizing steel recycling and leveraging by-product utilization, is paramount for reducing resource consumption and waste. This circularity not only offers environmental benefits but also enhances resource security and cost efficiency.
Ultimately, fostering a resilient, efficient, and truly sustainable global steel sector necessitates profound and sustained collaboration among all stakeholders. This includes governments establishing clear, long-term policy frameworks and incentives; steel producers committing to ambitious decarbonization targets and investing in cutting-edge technologies; financial institutions providing the necessary capital for the green transition; and consumers recognizing and valuing the environmental benefits of green steel in their purchasing decisions. The challenges are formidable, but the opportunity to transform a cornerstone industry into a leader of the sustainable economy is equally immense, promising a future where steel continues to underpin global progress without compromising planetary health.
Many thanks to our sponsor Focus 360 Energy who helped us prepare this research report.
References
- EOXS. (2024). Global Steel Market Analysis | Emerging Trends and Future Directions. Retrieved from https://eoxs.com/new_blog/global-steel-market-analysis-emerging-trends-and-future-directions/
- EOXS. (2024). The Steel Industry is at a Pivotal Juncture as It Adapts to the Evolving Global Landscape. Retrieved from https://eoxs.com/new_blog/top-5-trends-shaping-the-global-steel-market-in-2024/
- Global Energy Monitor. (2025). Global Steel Sector Lagging on Green Transition as Coal-Powered Production Rises. Reuters. Retrieved from https://www.reuters.com/sustainability/cop/global-steel-sector-lagging-green-transition-coal-powered-production-rises-2025-05-20/
- International Energy Agency (IEA). (2020). Iron and Steel Technology Roadmap. Paris: IEA. https://www.iea.org/reports/iron-and-steel-technology-roadmap
- Jakubowski, J., Wojak-Strzelecka, N., Ribeiro, R. P., Pashami, S., Bobek, S., Gama, J., Nalepa, G. J. (2024). Artificial Intelligence Approaches for Predictive Maintenance in the Steel Industry: A Survey. arXiv. Retrieved from https://arxiv.org/abs/2405.12785
- Next Move Strategy Consulting. (2024). Steel Market Size and Share Analysis | Statistics – 2030. Retrieved from https://www.nextmsc.com/report/steel-market-mc3212
- PW Consulting. (2024). Steel Manufacturing Market. Retrieved from https://pmarketresearch.com/chemi/steel-manufacturing-market/
- Reuters. (2024). Green Steel is Possible and Even Affordable, but Still Unlikely. Retrieved from https://www.reuters.com/markets/commodities/green-steel-is-possible-even-affordable-still-unlikely-russell-2024-03-27/
- Reuters. (2025). Meet the Green Technologies Set to Transform the Geopolitics of Steelmaking. Retrieved from https://www.reuters.com/sustainability/decarbonizing-industries/meet-green-technologies-set-transform-geopolitics-steelmaking-2025-05-28/
- Reuters. (2024). Steel Companies ‘Yet to Prove Their Mettle’ in Race for Net Zero. Retrieved from https://www.reuters.com/sustainability/climate-energy/steel-companies-yet-prove-their-mettle-race-net-zero-2024-06-03/
- Souza Filho, I. R., Springer, H., Ma, Y., Mahajan, A., da Silva, C. C., Kulse, M., Raabe, D. (2022). Green Steel at Its Crossroads: Hybrid Hydrogen-Based Reduction of Iron Ores. arXiv. Retrieved from https://arxiv.org/abs/2201.13356
- Wikipedia. (2024). Steelmaking. Retrieved from https://en.wikipedia.org/wiki/Steelmaking
A trillion-dollar industry and we’re *still* figuring out how to make it sustainable? Should we just encase the entire planet in recycled steel and call it a day? I wonder if we could 3D print habitats from steel on other planets. Mars colony, clad in iron, anyone?
That’s a fantastic point about 3D printing with steel on other planets! The idea of creating habitats on Mars using locally sourced (or even transported) recycled steel is a really innovative way to approach space colonization. Exploring those possibilities further could revolutionize both steel production and space exploration!
Editor: FocusNews.Uk
Thank you to our Sponsor Focus 360 Energy
Considering the growing demand for specialized steel in EVs and renewable energy, how might the industry tailor its production processes to meet the specific needs of these sectors while maintaining sustainable practices?
That’s an excellent question! The move towards EVs and renewables necessitates a shift towards more flexible production processes. Investing in advanced metallurgy and process control technologies will be crucial for producing these specialized steels while minimizing waste and energy consumption. Collaboration across the supply chain will also be key. What are your thoughts on the role of government incentives in driving this transition?
Editor: FocusNews.Uk
Thank you to our Sponsor Focus 360 Energy
The report highlights the importance of transitioning to hydrogen-based direct reduction for “green steel.” The challenge lies in the availability and cost of green hydrogen. What innovative strategies or partnerships could accelerate the deployment of green hydrogen infrastructure for steel production?