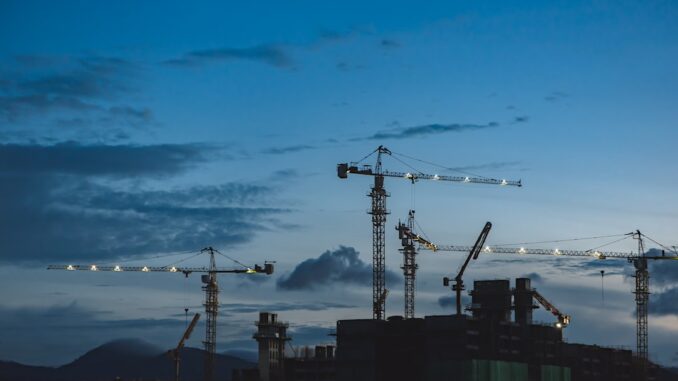
Abstract
Offsite construction, encompassing a spectrum of methodologies from prefabrication to advanced modular building, has solidified its position as a transformative solution addressing the multifaceted challenges confronting the global construction industry. These challenges include persistently escalating costs, a critical shortage of skilled labor, the imperative for enhanced productivity, and the undeniable urgency of transitioning towards more sustainable and environmentally responsible development practices. This comprehensive report provides an in-depth, rigorous examination of offsite construction. It meticulously explores its diverse methodologies, analyses the nuanced patterns and drivers of its global adoption, quantifies its profound economic advantages, delineates the pivotal role of concurrent technological advancements, scrutinises the substantial investment requirements, unpacks the complex logistical and regulatory challenges, and ultimately assesses its indispensable contribution to alleviating acute housing shortages and fostering genuinely sustainable building practices worldwide.
Many thanks to our sponsor Focus 360 Energy who helped us prepare this research report.
1. Introduction
The global construction industry stands at a critical juncture, grappling with a confluence of systemic challenges that threaten its long-term viability and capacity to meet escalating societal demands. Traditional, labour-intensive, and site-dependent construction methods are increasingly proving inadequate in the face of pressures such as rampant cost inflation, a pervasive and worsening skilled labour deficit, stagnant productivity growth compared to other sectors, and the urgent imperative to drastically reduce the sector’s substantial environmental footprint. The inherent inefficiencies of conventional construction, including exposure to unpredictable weather conditions, limited opportunities for quality control, significant material waste, and safety concerns on often chaotic construction sites, further exacerbate these issues.
In this context, offsite construction, often referred to interchangeably with Modern Methods of Construction (MMC) or Industrialised Construction, has emerged not merely as an alternative, but as a strategically vital paradigm shift. At its core, offsite construction is defined by the strategic relocation of significant portions of the building process—including planning, design, manufacture, and assembly of building components or entire modules—from the conventional, often challenging, final installed site to a controlled, factory-like environment. This fundamental shift is engineered to systematically enhance efficiency, elevate quality control, improve worker safety, accelerate project delivery, and significantly mitigate the environmental impact associated with the built environment. By leveraging the principles of manufacturing, offsite construction seeks to infuse the traditional construction process with the predictability, precision, and productivity characteristic of industrial production, thereby offering a robust and scalable solution to many of the industry’s most entrenched problems.
Historically, rudimentary forms of prefabrication have existed for centuries, often driven by expediency or necessity, such as the kit homes of the early 20th century or the post-war emergency housing initiatives. However, contemporary offsite construction represents a quantum leap in sophistication, underpinned by advanced technologies, refined design principles (such as Design for Manufacture and Assembly – DfMA), and increasingly integrated supply chains. This report delves into the intricate mechanisms and far-reaching implications of this modern offsite revolution.
Many thanks to our sponsor Focus 360 Energy who helped us prepare this research report.
2. Offsite Construction Methodologies
Offsite construction is not a monolithic concept but rather a broad umbrella term encompassing a sophisticated array of methodologies, each engineered for specific applications, scales, and levels of integration. These approaches vary in the degree to which components are manufactured offsite and the extent of their completion before transportation and final assembly.
2.1 Prefabrication
Prefabrication, at its fundamental level, involves the manufacturing of individual building components or sub-assemblies in a controlled factory environment. These components are then transported to the construction site for final assembly. This method represents a spectrum of complexity and scale:
2.1.1 Panelized Systems
Panelized systems involve the offsite manufacturing of two-dimensional wall panels, floor cassettes, and roof trusses or panels. These are typically fabricated with precision, often including openings for windows and doors, and sometimes integrating insulation, sheathing, and even initial wiring or plumbing. They are then transported to the site and assembled to form the building’s structural shell. Common materials include timber frames, light-gauge steel, and precast concrete panels. The benefits include:
- Speed of Erection: Once on site, panels can be rapidly erected, enclosing the structure much faster than traditional stick-built methods.
- Material Efficiency: Factory cutting minimises waste, and offcuts can often be recycled within the plant.
- Quality Control: Manufacturing in a controlled environment ensures consistent quality, dimensional accuracy, and optimal thermal performance of the building envelope.
2.1.2 Component Manufacturing
This refers to the prefabrication of individual components such as roof trusses, floor joists, staircases, and sometimes even pre-hung doors or window assemblies. These are often standard components used across numerous projects, benefiting from economies of scale. Utility walls or ‘MEP (Mechanical, Electrical, Plumbing) risers’ – where complex plumbing and electrical systems are assembled into a single unit offsite – are another increasingly common form of component prefabrication, significantly reducing complex onsite labour.
2.1.3 Cut-to-Length Systems
In this approach, raw materials like timber, steel, or even drywall are cut to precise dimensions offsite using automated machinery. These pre-cut elements are then bundled and shipped to the site for assembly. While not fully pre-assembled, this method reduces onsite cutting, waste, and labour, improving efficiency and material utilisation.
2.2 Modular Construction
Modular construction, often considered the most advanced form of offsite construction, involves the fabrication of entire three-dimensional sections or ‘modules’ of a building in a factory. These modules are often fully fitted out, including internal finishes, fixtures, and services, before being transported to the site and connected to form the complete structure. There are several variations:
2.2.1 Volumetric Modular Construction
This is the most common and visible form, where entire rooms, apartments, or building sections (e.g., bathroom pods, hotel rooms, or even entire floors) are constructed as complete 3D units. These modules are typically between 60% and 90% complete when they leave the factory, including electrical wiring, plumbing, HVAC, interior finishes, and even furniture. They are then stacked, connected, and weather-sealed on site. Key advantages include:
- Maximum Offsite Completion: Minimal onsite work required, reducing site-related risks and delays.
- Simultaneous Operations: Site preparation (foundations, utilities) can occur concurrently with module fabrication in the factory, dramatically compressing project timelines.
- Exceptional Quality: The controlled factory environment allows for superior quality control, tighter tolerances, and consistent finishes.
2.2.2 Flat-Pack Modular Construction
While less common for entire buildings, this involves the pre-manufacture of structural elements and panels that are then shipped flat-packed and assembled on site into modules or entire structures. This approach optimises transport volume but requires more complex onsite assembly than volumetric modules.
2.2.3 Chassis-Based Systems
Some modular approaches utilise a common structural ‘chassis’ or frame onto which different configurations of walls, floors, and roofs can be rapidly assembled. This offers a degree of customisation within a standardised framework, allowing for various building typologies to be derived from a common manufacturing platform.
2.3 Hybrid Systems
Hybrid systems strategically combine elements of offsite construction with traditional onsite methods, offering a flexible approach that leverages the efficiencies of prefabrication while allowing for greater design customisation or adapting to site-specific constraints. This approach is often adopted for complex or larger-scale projects where full modularisation might be impractical due to transport limitations, site access, or unique architectural requirements. Examples include:
- Precast Concrete Structures with Modular Infill: A traditional or precast concrete frame is erected on site, and then prefabricated wall panels or even volumetric modules (e.g., bathroom pods) are inserted to complete the building envelope and internal fit-out.
- Modular Cores with Traditional Wings: High-density elements like stairwells, elevator shafts, or service risers are constructed as modular units, while the main residential or office wings are built using conventional or panelised methods.
- Foundation and Groundworks Onsite: While superstructure is offsite, all foundation and groundworks typically remain traditional onsite activities, requiring careful coordination between the two processes.
The rationale behind hybrid systems is to achieve an optimal balance between factory-controlled quality and speed, and the flexibility often required for unique architectural expressions or challenging urban sites. This approach allows developers and contractors to strategically select which elements benefit most from offsite production, mitigating some of the inherent challenges of fully modular builds, such as transportation logistics for exceptionally large modules.
Many thanks to our sponsor Focus 360 Energy who helped us prepare this research report.
3. Global Adoption and Success Stories
The global adoption of offsite construction methodologies presents a diverse landscape, influenced by a complex interplay of economic imperatives, cultural perceptions, regulatory frameworks, technological readiness, and national priorities. While the fundamental benefits of offsite construction are universal, the pace and scale of its integration vary significantly across different regions.
3.1 Adoption Rates and Regional Drivers
-
Sweden: A recognised global leader, Sweden boasts an exceptionally high adoption rate, with estimates suggesting that up to 85% of its annual residential buildings incorporate significant offsite construction techniques, particularly timber-based prefabrication. This widespread adoption is rooted in a long history of industrialisation, dating back to the post-war era, and has been consistently supported by proactive government policies, a highly skilled workforce, and a cultural acceptance of pre-manufactured housing as high-quality and sustainable. The concentration of a few large, highly integrated construction companies also facilitates investment in advanced manufacturing facilities.
-
Netherlands and Belgium: These European nations also demonstrate significant integration of offsite methods, with adoption rates estimated at 47% and 46% respectively. Their drivers include high population density, a strong focus on sustainability and energy efficiency targets (which offsite methods excel at meeting), and a need for efficient construction processes in urban environments. The scarcity of land and the pressure to deliver housing rapidly have further accelerated the embrace of industrialised building techniques.
-
United Kingdom: Approximately 16% of construction projects in the UK currently utilise offsite techniques, a figure that is steadily growing. The UK’s push for offsite adoption is largely driven by a severe housing crisis, chronic labour shortages (exacerbated by Brexit), a persistent productivity gap in the construction sector, and ambitious government targets for carbon reduction. Government initiatives, such as the Construction 2025 strategy and the focus on Modern Methods of Construction (MMC) by Homes England, are actively promoting increased offsite uptake, particularly in affordable housing and public sector projects.
-
United States: With an adoption rate of around 5% of the overall construction market, the United States presents a substantial untapped potential for offsite growth. The lower adoption rate can be attributed to several factors, including a fragmented construction industry, a vast and diverse geographic landscape leading to complex logistics, and a highly localised and inconsistent regulatory and building code environment. However, increasing labour costs, a growing housing affordability crisis, and the need for rapid reconstruction in disaster-prone areas are accelerating interest and investment in offsite construction across various states.
-
Asia (Japan, Singapore, China): Asia has emerged as a significant hub for offsite construction, driven by rapid urbanisation, land scarcity, and governmental initiatives to enhance productivity and quality.
- Japan has a long-standing tradition of high-quality prefabricated homes, particularly robust in earthquake-prone regions. Large manufacturers like Sekisui House and Toyota Housing have perfected industrialised homebuilding, focusing on precision, quality, and speed.
- Singapore has aggressively championed Design for Manufacture and Assembly (DfMA) due to severe land and labour constraints. Government mandates and incentives have led to a significant increase in the adoption of prefabricated volumetric construction (PPVC) for high-rise residential and commercial buildings, achieving impressive productivity gains.
- China utilises offsite construction on an enormous scale, particularly for large-scale infrastructure projects and rapid urban development. While quality can vary, the sheer volume and speed achieved through prefabrication are unparalleled globally, often driven by top-down government policy to improve construction quality and reduce pollution.
3.2 Success Stories and Transformative Projects
The impact of offsite construction is best illustrated through numerous successful implementations worldwide, demonstrating its capacity to deliver high-quality, cost-effective, and sustainable projects.
-
Sweden’s Million Homes Programme (1965-1974): This ambitious initiative aimed to construct one million high-quality homes within a decade to address a severe housing shortage. By 1974, the goal was achieved, with substantial reliance on prefabricated construction methods, particularly timber-based systems. This programme not only provided much-needed housing but also fundamentally transformed the Swedish construction industry, leading to the development of highly efficient factory production lines and fostering a culture of industrialised building. It set a precedent for large-scale, quality-controlled offsite construction and continues to influence Swedish building practices today.
-
United Kingdom’s Post-War Housing (1940s-1950s): Following World War II, the UK faced an unprecedented housing crisis compounded by immense labour and material shortages. The government and industry explored various prefabricated housing solutions, leading to the rapid construction of numerous homes using offsite methods to meet urgent demand. While many of these ‘prefabs’ were initially intended as temporary solutions, their deployment highlighted the speed and efficiency benefits of offsite production under extreme pressure. Modern UK offsite initiatives build upon these lessons, focusing on high-quality, permanent structures for social housing, build-to-rent, and healthcare sectors.
-
Cross Laminated Timber (CLT) Buildings (Global): The rise of mass timber products, particularly CLT, has revolutionised prefabrication. Buildings like the Brock Commons Tallwood House at the University of British Columbia (Canada) and numerous multi-story residential and commercial buildings across Europe and Australia showcase how large-format, pre-cut CLT panels can be rapidly assembled on site, significantly reducing construction time, site disruption, and embodied carbon. CLT panels are prefabricated with precise openings and connections, arriving on site ready for assembly, akin to a large-scale flat-pack system.
-
Rapid Hospital Construction (Global, e.g., China, UK during COVID-19): The COVID-19 pandemic dramatically demonstrated the agility of offsite construction. In Wuhan, China, the Huoshenshan Hospital (1,000 beds) was constructed in approximately 10 days using extensive prefabrication and modular techniques. Similarly, in the UK, modular healthcare units were deployed rapidly to expand critical care capacity, underscoring offsite’s capability for emergency response and urgent infrastructure delivery.
-
Affordable Housing Initiatives (e.g., California, USA): In regions facing severe housing affordability crises, modular construction is increasingly being leveraged to deliver housing rapidly and cost-effectively. Projects ranging from permanent supportive housing for the homeless to multi-family affordable housing developments utilise modular units to compress timelines and control costs, demonstrating a scalable solution to critical social issues.
These success stories underscore that offsite construction is a proven methodology capable of delivering high-quality outcomes across diverse building types and under varied economic and social pressures. Their continued growth is indicative of a maturing industry poised for broader adoption.
Many thanks to our sponsor Focus 360 Energy who helped us prepare this research report.
4. Economic and Operational Benefits
Offsite construction offers a compelling suite of economic and operational advantages that directly address many of the inefficiencies inherent in traditional building methods. These benefits cumulatively lead to significant cost reductions, enhanced financial predictability, improved quality, and a more streamlined project delivery process.
4.1 Cost Reduction and Financial Predictability
One of the most attractive propositions of offsite construction is its potential for substantial cost savings across various project phases. These savings are realised through a combination of direct and indirect efficiencies:
4.1.1 Labor Savings
- Reduced On-Site Labor Requirements: By shifting labour-intensive activities to a factory setting, the demand for highly skilled trades on the construction site is significantly diminished. This is crucial in an era of acute skilled labour shortages. Factory environments allow for a more efficient deployment of specialist labour, reducing unproductive time (e.g., waiting for materials, weather delays) and travel to multiple sites.
- Improved Labor Productivity: Factory work environments are inherently more controlled, ergonomic, and conducive to sustained productivity. Workers are shielded from adverse weather, and tasks can be standardised and repeated, leading to higher output per person. Studies suggest that productivity in a factory setting can be 2-3 times higher than on a traditional site. This also contributes to attracting and retaining a more stable workforce, as factory conditions are often safer and offer more predictable hours.
- Reduced Labor Overhead: Lower onsite headcount means reduced costs associated with site supervision, temporary facilities, security, and benefits for a fluctuating workforce.
4.1.2 Shorter Construction Timelines
- Accelerated Project Completion: The ability to conduct site preparation (foundations, utility connections) concurrently with the manufacturing of building components or modules in the factory is a cornerstone of offsite efficiency. This parallel processing can dramatically compress overall project schedules by 30-50% compared to traditional construction. For instance, while a 10-story modular building’s modules are being fabricated, its foundations are being poured onsite, leading to a much faster structural completion.
- Reduced Financing Costs: A shorter construction period directly translates into lower interest payments on construction loans. Every month saved on the project timeline can mean significant financial savings for developers and investors.
- Earlier Revenue Generation: For commercial projects, hotels, student accommodation, or rental housing, faster completion means earlier occupancy and quicker revenue generation (e.g., rental income, sales revenue). This accelerates the return on investment and improves project viability.
- Mitigated Risk of Delays: Factory production is largely immune to weather disruptions, vandalism, and many site-specific logistical bottlenecks, making project timelines more predictable and reliable.
4.2 Waste Minimization and Environmental Efficiency
Offsite construction inherently promotes a more sustainable approach to material management, leading to significant reductions in waste and overall environmental impact:
- Material Efficiency and Optimization: In a controlled factory environment, precise cutting techniques and optimised nesting patterns for materials (e.g., timber, drywall, steel) minimise waste. Large-volume purchasing power also allows for bulk deliveries, reducing packaging waste. Furthermore, offcuts and excess materials can be collected and recycled efficiently within the factory, rather than being sent to landfill from dispersed construction sites.
- Reduced Site Waste: With a greater proportion of the building assembled offsite, the amount of waste generated on the final construction site is drastically reduced. This leads to cleaner sites, fewer skip movements, and less disruption to surrounding communities.
- Recyclability and Reusability: Offsite construction often lends itself to the use of standardised components and modular design, which can facilitate easier deconstruction and potential reuse of modules or components at the end of a building’s lifecycle, contributing to circular economy principles. Materials chosen for offsite construction are often selected for their longevity and recyclability.
4.3 Enhanced Quality Control and Safety
Building in a factory environment provides unparalleled opportunities for rigorous quality control and vastly improved safety conditions, leading to higher-quality outputs and reduced operational risks:
- Standardization and Precision: Manufacturing components and modules in a controlled, indoor setting allows for consistent processes, adherence to tight tolerances, and the use of automated machinery. This results in superior dimensional accuracy, higher structural integrity, and better overall build quality compared to traditional methods where quality can vary significantly due to site conditions, weather, and differing skill levels of onsite labour. This consistency leads to fewer structural defects and enhanced performance over the building’s lifespan.
- Reduced Defects and Rework: The controlled environment and systematic quality checks at various stages of the manufacturing process significantly reduce the incidence of construction defects. This means less rework on site, which is a major source of cost overruns and delays in traditional construction. Fewer defects also translate into lower maintenance costs post-occupancy and higher client satisfaction.
- Superior Performance: The precision afforded by offsite construction often translates into superior building performance, particularly in terms of thermal insulation, airtightness, and acoustic performance. This can lead to lower operational energy consumption for heating and cooling, contributing to long-term energy savings for occupants and reduced carbon emissions.
- Improved Safety Records: Construction is one of the most hazardous industries globally. By moving a significant portion of work into a factory, many of the inherent risks of onsite construction are mitigated. These include falls from height, exposure to adverse weather, vehicle movements, noise, dust, and working with heavy machinery in uncontrolled environments. Factory settings allow for safer working conditions, ergonomic workstations, consistent lighting, and structured safety protocols, leading to a significant reduction in accidents and injuries. This not only protects workers but also reduces insurance premiums and legal liabilities for contractors.
In essence, the economic and operational benefits of offsite construction paint a compelling picture of a more efficient, predictable, higher-quality, and safer way to build, directly addressing many of the historical pain points of the construction industry.
Many thanks to our sponsor Focus 360 Energy who helped us prepare this research report.
5. Technological Advancements Driving Offsite Construction
The resurgence and sophistication of offsite construction in the 21st century are inextricably linked to profound technological advancements. These innovations have not only streamlined design and manufacturing processes but have also enhanced precision, efficiency, and quality, making offsite methods increasingly viable and competitive.
5.1 Building Information Modeling (BIM)
BIM is perhaps the single most critical technological enabler for modern offsite construction. It is not merely a 3D design tool but a comprehensive digital representation of a building’s physical and functional characteristics, facilitating collaboration and information exchange across the entire project lifecycle.
- Integrated Design and Collaboration: BIM allows all stakeholders—architects, engineers, manufacturers, and contractors—to work from a single, shared, and intelligent model. This fosters unprecedented coordination, enabling early clash detection (identifying conflicts between structural, architectural, and MEP systems) long before physical construction begins. For offsite, this means designing components or modules that fit together seamlessly on site, virtually eliminating costly errors and rework.
- Design for Manufacture and Assembly (DfMA): BIM models are instrumental in implementing DfMA principles. Designs are optimised from the outset for factory fabrication and efficient onsite assembly. The level of detail (LOD) in BIM models for offsite projects is exceptionally high, allowing for precise material take-offs, fabrication instructions, and assembly sequences. This direct link between design and manufacturing reduces interpretation errors and improves predictability.
- Simulation and Analysis: BIM enables virtual simulations of the construction process (4D BIM – incorporating time) and cost estimations (5D BIM – incorporating cost), allowing project teams to visualise sequences, identify potential bottlenecks, and optimise schedules. Performance simulations (e.g., energy modelling, daylight analysis) can also be conducted early in the design phase, leading to more sustainable and efficient building designs that are then precisely replicated in the factory.
- Digital Fabrication Linkage: BIM models can directly feed information to Computer Numerical Control (CNC) machines, robotic fabrication systems, and automated production lines in the factory. This direct digital-to-physical workflow ensures extreme precision in cutting, shaping, and assembly of components, reducing human error and increasing speed.
5.2 Automation and Robotics
The integration of robotics and advanced automation into offsite manufacturing facilities is revolutionising the production of building components and modules. These technologies enhance precision, speed, and safety while addressing labour shortages for repetitive or hazardous tasks.
- Robotic Fabrication: Robotic arms can perform a wide range of tasks with extreme precision and consistency, including welding, material handling, painting, cladding installation, and even complex assembly operations. For instance, robotic systems can precisely cut and assemble steel frames, nail timber panels, or apply insulation, ensuring uniform quality that is difficult to achieve manually.
- Automated Material Handling: Automated Guided Vehicles (AGVs) and robotic cranes transport materials and sub-assemblies along the factory production line, optimising workflow, reducing manual handling injuries, and accelerating throughput. This enables a ‘just-in-time’ delivery of components to workstations, minimising bottlenecks.
- Advanced Manufacturing Processes: Beyond robotics, automated machinery for cutting (e.g., laser cutters, water jets), bending, and shaping various materials allows for highly customised and complex geometries to be produced efficiently and accurately. This opens up new design possibilities that would be prohibitively expensive or impossible with traditional methods.
- AI and Machine Learning for Optimization: Artificial Intelligence (AI) and Machine Learning (ML) algorithms are increasingly used to optimise factory layouts, predict maintenance needs for machinery, schedule production lines, and even perform quality checks using computer vision systems. This leads to higher operational efficiency and reduced downtime.
5.3 Smart Technologies and Internet of Things (IoT)
The proliferation of smart technologies and the Internet of Things (IoT) is impacting both the manufacturing process and the finished building product in offsite construction.
- Smart Factories: IoT sensors integrated into factory equipment can monitor performance, predict maintenance requirements, and track material flow in real-time, enabling proactive adjustments to the production line for maximum efficiency. This data-driven approach enhances operational predictability and reduces waste.
- Embedded Smart Systems: Offsite construction facilitates the integration of smart building technologies—such as energy management systems, automated HVAC controls, smart lighting, security systems, and environmental sensors—directly into modules during fabrication. This ‘plug-and-play’ approach reduces complex onsite installation, ensuring systems are fully functional upon delivery. Real-time monitoring of building performance, energy usage, and occupant comfort can then be conducted, leading to highly efficient and responsive buildings.
- Digital Twins: Creating a ‘digital twin’ – a virtual replica of the physical building – allows for real-time monitoring of its performance post-occupancy. Data from IoT sensors within the building is fed back to the digital twin, enabling predictive maintenance, optimising energy consumption, and informing future designs. This lifecycle approach is particularly effective with offsite construction due to the precise digital models created during the design and manufacturing phases.
5.4 Advanced Materials and Supply Chain Integration
Innovations in material science and digital supply chain management further enhance offsite capabilities:
- Engineered Wood Products: Materials like Cross Laminated Timber (CLT), Glued Laminated Timber (Glulam), and Laminated Veneer Lumber (LVL) offer high strength-to-weight ratios, excellent thermal performance, and a sustainable alternative to concrete and steel. These large-format engineered wood products are ideal for prefabrication as they can be precisely cut offsite using CNC machines and rapidly assembled on site.
- High-Performance Composites: Development of advanced composites allows for lighter, stronger, and more durable components, expanding design possibilities and reducing transportation costs.
- Supply Chain Digitization: Technologies like blockchain and advanced enterprise resource planning (ERP) systems are being used to track materials from source to factory to site, improving transparency, reducing delays, and enabling just-in-time delivery for optimal factory flow and site logistics.
These technological advancements collectively transform offsite construction from a niche alternative into a highly sophisticated, data-driven, and increasingly dominant force in the global building industry, promising higher quality, faster delivery, and greater sustainability.
Many thanks to our sponsor Focus 360 Energy who helped us prepare this research report.
6. Investment Requirements, Logistical, and Regulatory Challenges
Despite the compelling benefits, the widespread adoption of offsite construction is tempered by several significant barriers, primarily concerning substantial initial investment, complex logistical operations, and an often-unprepared regulatory landscape.
6.1 Investment Requirements
Establishing and scaling offsite manufacturing capabilities demands a significant upfront capital outlay, which can be a formidable hurdle for many traditional construction firms and new entrants.
-
Capital Intensity: Setting up a state-of-the-art offsite manufacturing facility requires substantial investment in several key areas:
- Land and Infrastructure: Acquiring suitable industrial land and constructing a large, climate-controlled factory building.
- Advanced Machinery and Equipment: Purchasing automated production lines, robotic systems, CNC machines, heavy lifting equipment (e.g., overhead gantry cranes), and specialised tooling. This equipment is often bespoke and highly capital-intensive.
- Software and IT Infrastructure: Implementing advanced BIM platforms, ERP systems, quality control software, and data analytics tools to manage the complex design-to-manufacture workflow.
- Research and Development (R&D): Continuous investment in R&D is necessary to refine processes, develop new modular systems, improve material efficiency, and integrate emerging technologies.
- Workforce Skilling and Training: Investing in training programmes to upskill the existing workforce and attract new talent with manufacturing, robotics, and digital skills, which differ significantly from traditional construction trades. This requires a long-term commitment to human capital development.
-
Financing Challenges: Traditional financial institutions and investors are often more familiar with conventional construction project finance models. Offsite construction projects, with their different cash flow profiles (larger upfront payments for factory production, lower ongoing site costs) and perceived novel risks, can face hesitancy from lenders. Valuation models for offsite facilities and projects may not be well-established, making it challenging to secure favourable financing terms. This can create a ‘chicken-and-egg’ dilemma where substantial project pipelines are needed to justify factory investment, but without the factory, large projects are difficult to win.
6.2 Logistical Challenges
While offsite methods reduce onsite complexities, they introduce a distinct set of logistical challenges, particularly concerning the transportation and final assembly of large, pre-finished components.
-
Transportation of Modules: Moving large, three-dimensional modules or oversized panels from the factory to the construction site can be extraordinarily complex and costly. This involves:
- Route Planning: Detailed route surveys are necessary to identify potential obstructions such as low bridges, tight turns, overhead power lines, and weight restrictions.
- Special Permits and Escorts: Transporting oversized or overweight loads typically requires special permits from multiple jurisdictions (states, counties, municipalities) and often necessitates police or private escorts.
- Timing Restrictions: Deliveries may be restricted to off-peak hours (e.g., night-time) to minimise traffic disruption, adding to logistical complexity and cost.
- Environmental Impact: While overall project emissions may be lower, the carbon footprint of transporting large modules over long distances needs careful consideration and optimisation.
-
Site Logistics and Cranage: Once on site, the precise placement and connection of modules require significant coordination and specialised equipment.
- Large Cranes: Heavy-lift cranes are often required to hoist and position modules, necessitating careful planning for crane access, rigging, and outrigger placement. This can be particularly challenging in dense urban environments with limited space.
- Just-in-Time Delivery: Modules must be delivered to site precisely when needed, as storage space on a compact urban site is often non-existent. Any delays in manufacturing or transport can lead to expensive crane idle time or disruption to the installation schedule.
- Precision Foundations: The success of modular assembly hinges on extremely precise foundations and connection points, requiring high accuracy in site preparation.
6.3 Regulatory and Standardization Hurdles
One of the most pervasive challenges for offsite construction, especially in fragmented markets like the United States, is navigating a patchwork of inconsistent building codes and regulatory frameworks.
- Varying Building Codes and Permitting: Building codes and inspection requirements vary significantly between cities, counties, and states. A module manufactured in one jurisdiction may need re-certification or additional inspections when installed in another, adding significant administrative burden, cost, and delay. This lack of uniformity inhibits the scalability and mass production potential inherent in offsite models.
- Lack of Industry Standardization: Unlike other manufacturing sectors, the offsite construction industry lacks broadly adopted universal standards for module dimensions, connection details, and performance criteria. This absence of interoperability can hinder the development of a mature supply chain, limit design flexibility (forcing reliance on proprietary systems), and impede cross-project learning and efficiency gains.
- Insurance and Warranties: Traditional construction insurance models and warranty providers may be unfamiliar with the risk profile of offsite construction, particularly concerning the split responsibility between factory and site, and the transportation phase. This can lead to higher premiums or difficulty in securing comprehensive coverage.
- Public and Professional Perception: Despite advancements, a persistent stigma associated with ‘prefabricated’ buildings (often linked to temporary, lower-quality structures from past eras) continues to exist among some consumers, policymakers, and even within parts of the construction industry. Overcoming this perception requires consistent delivery of high-quality projects and effective public education.
- Skills Gap in the Regulatory Body: Building code officials and inspectors may lack the specific knowledge and training required to effectively review and inspect offsite construction projects, leading to delays or misinterpretations of compliance.
Addressing these investment, logistical, and regulatory challenges is paramount for offsite construction to fully realise its transformative potential and achieve widespread mainstream adoption across global markets.
Many thanks to our sponsor Focus 360 Energy who helped us prepare this research report.
7. Offsite Construction’s Role in Addressing Housing Shortages and Promoting Sustainable Practices
Offsite construction is poised to play an increasingly critical role in tackling two of the most pressing global challenges: the pervasive housing crisis and the urgent need for more sustainable development practices within the built environment.
7.1 Addressing Housing Shortages
The global housing deficit, particularly for affordable and social housing, is a critical issue impacting economic stability and social equity. Offsite construction offers several powerful levers to alleviate this crisis:
- Rapid Deployment and Scalability: Offsite methods enable significantly faster construction of housing units, often reducing project timelines by 30-50%. This speed is crucial for meeting urgent housing demands, whether for rapidly growing urban populations, post-disaster reconstruction, or addressing homelessness. Factories can operate year-round, unhindered by weather, allowing for continuous, high-volume production of units. This scalability means thousands of homes can be produced and delivered far more quickly than through traditional methods, turning a trickle of new housing into a steady flow.
- Affordability through Efficiency: The inherent efficiencies of offsite construction—reduced labour costs, minimised waste, shorter project durations (leading to lower financing costs), and predictable pricing—translate directly into lower overall construction costs. These cost savings can then be passed on to consumers or leveraged by developers to make housing more affordable, particularly in high-demand urban regions where land values are prohibitive. This makes offsite particularly attractive for public housing initiatives, build-to-rent schemes, and key worker accommodation.
- Consistent Quality and Performance: Unlike some historical ‘prefabs’ that suffered from quality issues, modern offsite construction delivers consistent, high-quality housing units. This means that even affordable housing can be durable, energy-efficient, and aesthetically pleasing, overcoming the stigma often associated with ‘cheap’ housing and providing long-term value for residents and communities.
- Addressing Labour Shortages: By shifting labour from unpredictable construction sites to controlled factory environments, offsite construction can attract a new, more diverse workforce. Factory work is safer, more predictable, and often more amenable to training programmes, making it an effective strategy to counteract the chronic shortage of skilled trades in traditional construction and build a stable talent pipeline for housing delivery.
- Design Flexibility for Diverse Needs: While offsite construction benefits from standardisation, advancements in BIM and manufacturing technology allow for considerable design flexibility. Modular systems can be configured to meet diverse architectural styles, density requirements (from single-family homes to high-rise apartment blocks), and specific community needs, ensuring that rapid deployment does not compromise liveability or local character.
7.2 Promoting Sustainable Practices
Beyond addressing housing needs, offsite construction is a powerful enabler of sustainable building practices, contributing significantly to environmental protection and resource efficiency throughout a building’s lifecycle:
- Enhanced Energy Efficiency: Prefabricated buildings can be designed and manufactured with exceptional precision, achieving superior thermal envelopes, minimal air leakage, and consistent insulation. This enables the construction of high-performance buildings, including Passive House standards, which drastically reduce operational energy consumption for heating, cooling, and lighting. The integration of renewable energy systems (e.g., solar panels, heat pumps) can also be more efficiently performed in a factory setting.
- Reduced Environmental Impact (Carbon Footprint):
- Lower Embodied Carbon: Optimised material use, reduced waste, and efficient factory processes contribute to a lower embodied carbon footprint of building components. Furthermore, the selection of sustainable materials like engineered timber (e.g., CLT), which sequesters carbon, can further reduce the building’s overall carbon impact.
- Reduced Site Pollution: Offsite construction significantly reduces noise, dust, and light pollution on site, leading to less disruption for surrounding communities and local ecosystems. Fewer vehicle movements to and from the site also mean reduced local traffic congestion and associated emissions.
- Waste Diversion from Landfill: As detailed previously, factory environments enable higher rates of material recycling and waste minimisation, diverting substantial volumes of construction and demolition waste from landfills.
- Improved Resource Efficiency: Precision manufacturing leads to more efficient use of raw materials. Bulk purchasing for factory production also reduces individual packaging waste. Water and energy consumption within controlled factory environments can be carefully monitored and optimised, often more effectively than across numerous dispersed construction sites.
- Circular Economy Principles: The modular nature of offsite construction inherently supports circular economy principles. Buildings or modules can be designed for deconstruction rather than demolition, allowing components or entire units to be refurbished, relocated, or recycled at the end of their useful life, thereby minimising waste and maximising resource value.
- Safer and Healthier Work Environments: Shifting work to factories improves worker health and safety, reducing exposure to hazardous conditions, noise, and pollutants inherent in traditional construction sites. This humane aspect contributes to social sustainability by fostering a healthier and more attractive industry.
In conclusion, offsite construction is not merely a method of building faster or cheaper; it is a strategic imperative for addressing the dual crises of housing scarcity and environmental degradation. Its inherent efficiencies and ability to integrate advanced sustainable practices make it a cornerstone of future resilient and responsible urban development.
Many thanks to our sponsor Focus 360 Energy who helped us prepare this research report.
8. Future Outlook and Recommendations
The trajectory of offsite construction points towards a future where it transitions from a niche alternative to a foundational pillar of the global construction industry. Market forecasts consistently project robust growth, driven by an accelerating confluence of macro-economic pressures, technological advancements, and a growing recognition of its inherent advantages. The global offsite construction market size, valued in the tens of billions of US dollars, is expected to grow at a compound annual growth rate (CAGR) well into double digits over the next decade, with some reports predicting it could reach hundreds of billions of dollars by 2033 (Business Research Insights, 2024; Value Market Research, 2024).
Key drivers for this anticipated growth include the deepening skilled labour crisis, the persistent global housing affordability challenge, stringent sustainability regulations, and the compelling productivity gains offered by industrialised processes. As technology continues to mature, and as more success stories emerge, the industry is poised for wider acceptance and integration.
To fully unlock the immense potential of offsite construction and overcome the existing barriers, several strategic recommendations are critical:
8.1 Policy and Regulatory Reform
- Standardisation and Harmonisation of Building Codes: Governments and regulatory bodies must actively collaborate to harmonise building codes and permitting processes across jurisdictions. Developing national or international modular building codes and promoting mutual recognition of factory certification would drastically reduce administrative burdens and enable greater economies of scale for manufacturers.
- Incentivise Adoption: Governments should introduce robust incentives for the adoption of offsite construction, including tax breaks for factory investments, subsidies for R&D in new methodologies and materials, and preferential procurement policies for public projects utilising offsite techniques (e.g., social housing, schools, hospitals).
- Support for Workforce Development: Invest in dedicated training programmes and apprenticeships that equip the workforce with the manufacturing, digital, and robotics skills required for offsite factories, bridging the gap between traditional construction trades and modern industrialised building.
8.2 Industry Collaboration and Investment
- Cross-Sector Collaboration: Foster greater collaboration between developers, architects, engineers, contractors, manufacturers, and technology providers. Integrated project delivery models, where all stakeholders are involved from the early design stages (DfMA), are crucial for optimising offsite processes.
- Private and Public Investment: Encourage private equity and venture capital investment into offsite manufacturing facilities and technology startups. Simultaneously, public-private partnerships should be explored to de-risk initial large-scale offsite projects and demonstrate viability, thereby attracting further private investment.
- Supply Chain Integration: Develop more robust and transparent digital supply chains that integrate material suppliers, manufacturers, and logistics providers. This will enhance predictability, reduce lead times, and improve material flow.
8.3 Technological Integration and Innovation
- Advanced Digital Twins and AI: Continue to invest in the development and widespread adoption of digital twin technology for both manufacturing optimisation and post-occupancy building management. Leverage AI and machine learning for predictive analytics in project scheduling, quality control, and the optimisation of factory production lines.
- Robotics and Automation: Further scale up the deployment of robotics and automation in factories to increase efficiency, precision, and safety. Research into collaborative robots (cobots) that work alongside human operators could further enhance productivity.
- Material Innovation: Continue R&D into advanced, sustainable materials that are well-suited for factory production, such as novel composites, bio-based materials, and smart materials with integrated functionalities.
8.4 Overcoming Perception Barriers
- Showcase Successes: Proactively communicate and showcase the high quality, aesthetic appeal, and performance benefits of modern offsite buildings. Dispel historical misconceptions about ‘prefab’ through well-designed, high-profile projects across various sectors.
- Education and Awareness: Educate clients, developers, and the broader public about the advantages of offsite construction through industry reports, case studies, and public awareness campaigns. Highlight its role in sustainability, affordability, and rapid delivery.
Many thanks to our sponsor Focus 360 Energy who helped us prepare this research report.
9. Conclusion
Offsite construction represents a transformative paradigm shift in building design and delivery, offering compelling and scalable solutions to many of the deeply entrenched challenges confronting the global construction industry. Its diverse methodologies, ranging from advanced panelisation to sophisticated volumetric modular construction, are underpinned by profound economic benefits, including significant cost reductions, accelerated project timelines, predictable financial outcomes, vastly improved quality control, and enhanced worker safety. The increasing integration of cutting-edge technologies—such as Building Information Modeling, advanced robotics, artificial intelligence, and smart building systems—is continuously pushing the boundaries of what is achievable, making offsite construction more precise, efficient, and competitive than ever before.
Furthermore, offsite construction is proving to be an indispensable tool in addressing critical global imperatives, particularly the acute shortage of affordable housing and the urgent mandate for more sustainable and environmentally responsible development. Its ability to rapidly deploy high-quality, energy-efficient housing units, coupled with its inherent capacity for waste minimisation and reduced carbon emissions, positions it as a cornerstone for future resilient and resource-efficient urbanisation.
However, the widespread realisation of offsite construction’s full potential hinges on successfully navigating existing barriers. These include the substantial upfront capital investment required for state-of-the-art manufacturing facilities, the intricate logistical complexities associated with transporting large modules, and the fragmented landscape of regulatory compliance and a lingering lack of industry-wide standardisation. Moreover, overcoming lingering public and professional misconceptions about the quality and aesthetics of prefabricated buildings remains a vital task.
As the construction industry continues its inevitable evolution towards industrialised processes, a concerted effort from policymakers, industry leaders, financial institutions, and academic institutions is essential. Through strategic investment, proactive regulatory reform, continuous technological innovation, and collaborative ecosystem development, offsite construction is poised not only to reshape the future of how we build but also to fundamentally deliver a built environment that is more productive, more sustainable, and more accessible for all.
Many thanks to our sponsor Focus 360 Energy who helped us prepare this research report.
References
- Boston Consulting Group. (2019). The Offsite Revolution in Construction. https://www.bcg.com/publications/2019/offsite-revolution-construction
- Building Affordable. (2024). Advancements and Challenges in Offsite Construction. https://www.buildingaffordable.com/offsite-construction/
- Business Research Insights. (2024). Offsite Construction Market Trends | Report [2033]. https://www.businessresearchinsights.com/market-reports/offsite-construction-market-120810
- GreenBuildingAdvisor. (2019). The Path Forward for Offsite Construction. https://www.greenbuildingadvisor.com/article/the-path-forward-for-offsite-construction
- Hylman. (2024). Enabling the Sustainable and Efficient Foundations of Tomorrow: Hylman’s Strategic Guide to Steer the Future of the Landscape with Prefabricated Construction. https://news.hylman.com/news-detail/construction/enabling-the-sustainable-and-efficient-foundations-of-tomorrow-hylmans-strategic-guide-to-steer-the-future-of-the-landscape-with-prefabrica
- HUD USER. (2024). Offsite Construction: An International Perspective. https://www.huduser.gov/portal/pdredge/pdr-edge-international-philanthropic-062524.html
- MDPI. (2024). A Multi-Faceted Analysis of Enablers and Barriers of Industrialised Building: Global Insights for the Australian Context. https://www.mdpi.com/2075-5309/15/2/214
- Modular Home Source. (2024). The Complex Path of Offsite Construction in Solving the Global Housing Crisis. https://modularhomesource.com/the-complex-path-of-offsite-construction-in-solving-the-global-housing-crisis/
- Value Market Research. (2024). Offsite Construction Market Size, Share & Growth Report, 2033. https://www.valuemarketresearch.com/report/offsite-construction-market
- Wikipedia. (2024). Off-site construction. https://en.wikipedia.org/wiki/Off-site_construction
The report’s emphasis on policy and regulatory reform is vital. Streamlining building codes and creating incentives are key, but how can we ensure these changes also encourage sustainable material use within offsite construction, not just speed and cost efficiency?
That’s an excellent point! Ensuring sustainable material use alongside streamlining building codes is crucial. Perhaps incentives could be tied to using materials with lower embodied carbon or promoting designs that prioritize deconstruction and reuse. It’s about creating a holistic framework for truly sustainable offsite construction.
Editor: FocusNews.Uk
Thank you to our Sponsor Focus 360 Energy
So, modular *and* sustainable? Does this mean I can finally get that eco-friendly panic room I’ve always dreamed of? Seriously though, streamlining construction while being kind to the planet sounds like a win-win. What innovative materials are leading this charge?
Great question! The drive for sustainable offsite construction is definitely pushing material innovation. We are seeing a lot of interest in mass timber products like CLT, as well as recycled and bio-based composites. These offer a lower embodied carbon footprint compared to traditional materials. More research into material performance is needed.
Editor: FocusNews.Uk
Thank you to our Sponsor Focus 360 Energy
The discussion on policy and regulatory reform is critical. Have there been successful examples of municipalities streamlining permitting processes for offsite construction that could serve as a model for wider adoption? Understanding those mechanisms could accelerate industry growth.
That’s a fantastic question! Several municipalities are indeed leading the way with innovative permitting. Some cities have created dedicated offsite construction teams within their planning departments and fast-track approval processes for projects using modular techniques. Sharing these best practices can help promote more sustainable building policies. Let’s continue this conversation!
Editor: FocusNews.Uk
Thank you to our Sponsor Focus 360 Energy
Given the report’s focus on technology, how might advancements in virtual reality (VR) and augmented reality (AR) further optimize the design, manufacturing, and on-site assembly processes in offsite construction? Could VR/AR contribute to enhanced collaboration and reduce errors?
That’s a brilliant point! VR and AR hold immense potential. Imagine designers ‘walking through’ a modular building before it’s built, or AR overlays guiding on-site assembly, minimizing errors. Enhanced collaboration during design reviews and training simulations become much more effective with VR/AR.
Editor: FocusNews.Uk
Thank you to our Sponsor Focus 360 Energy
So, offsite construction tackles housing shortages and promotes sustainability? Time to build vertical farms on modular rooftops for the ultimate eco-friendly, self-sufficient living. Anyone else thinking this is the future of urban agriculture?