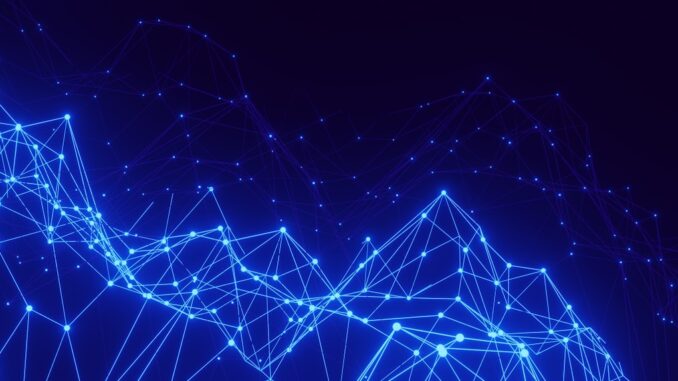
Abstract
The construction industry is a complex ecosystem characterized by intricate project lifecycles, diverse stakeholders, and significant financial investments. Selecting the right builder, while crucial, represents merely a single facet of a much broader and evolving process: construction procurement. This research report delves into the multifaceted nature of construction procurement, moving beyond the simplistic notion of builder selection to explore the intricate interplay of risk management, collaborative practices, technological adoption, and evolving contractual frameworks. We analyze the current state of procurement methodologies, including traditional approaches and innovative alternatives like Integrated Project Delivery (IPD) and lean construction principles. The report investigates the impact of digitalization on procurement processes, focusing on Building Information Modeling (BIM), data analytics, and the rise of online procurement platforms. Furthermore, we examine the critical role of sustainability in modern procurement strategies and the challenges associated with ensuring ethical and responsible sourcing. The research concludes by identifying key areas for future research and offering recommendations for optimizing construction procurement processes to enhance project outcomes, foster greater collaboration, and mitigate inherent risks.
Many thanks to our sponsor Focus 360 Energy who helped us prepare this research report.
1. Introduction: Beyond Builder Selection – A Holistic View of Construction Procurement
The construction industry stands as a significant driver of global economic activity, characterized by projects ranging from modest residential renovations to large-scale infrastructure developments. The success of any construction endeavor hinges not only on the competence of the builder but also on the efficacy of the entire procurement process. Traditionally, the selection of a builder has been viewed as a discrete task, often focusing primarily on cost considerations. However, this narrow perspective overlooks the interconnectedness of procurement decisions and their profound impact on project performance, schedule adherence, budget control, and overall stakeholder satisfaction.
Construction procurement encompasses the entire process of acquiring goods, services, and works necessary for a construction project, starting from project conception and continuing through design, construction, commissioning, and even facility management. It involves a complex network of stakeholders, including clients, architects, engineers, contractors, subcontractors, suppliers, and regulatory agencies. Each stakeholder brings unique perspectives, priorities, and contractual obligations, contributing to the inherent complexity of the procurement process.
This report argues for a holistic understanding of construction procurement, one that transcends the limitations of traditional, fragmented approaches. We propose a framework that emphasizes proactive risk management, fosters collaborative relationships, embraces technological innovation, and prioritizes sustainable practices. By adopting this broader perspective, stakeholders can make more informed decisions, mitigate potential conflicts, and ultimately achieve superior project outcomes.
Many thanks to our sponsor Focus 360 Energy who helped us prepare this research report.
2. Risk Management in Construction Procurement: Identifying, Assessing, and Mitigating Uncertainties
Construction projects are inherently risky endeavors, susceptible to a wide range of uncertainties that can significantly impact project costs, schedules, and quality. Effective risk management is therefore a critical component of any successful construction procurement strategy. This section examines the key sources of risk in construction projects and explores various techniques for identifying, assessing, and mitigating these risks throughout the procurement lifecycle.
2.1. Sources of Risk in Construction Projects:
Risks in construction projects can arise from a variety of sources, including:
- Market Conditions: Fluctuations in material prices, labor costs, and interest rates can significantly impact project budgets. Economic downturns can also lead to project delays or cancellations.
- Design Errors and Omissions: Incomplete or inaccurate design documentation can result in costly rework and schedule delays. Communication breakdowns between designers and contractors can exacerbate these issues.
- Site Conditions: Unexpected soil conditions, environmental hazards, and subsurface utilities can lead to unforeseen expenses and delays. Thorough site investigations are crucial for mitigating these risks.
- Construction Execution: Poor workmanship, inadequate quality control, and safety incidents can compromise project quality, increase costs, and delay completion. Effective project management and skilled labor are essential for mitigating these risks.
- Regulatory and Legal Requirements: Changes in building codes, environmental regulations, and permitting processes can impact project timelines and budgets. Compliance with all applicable regulations is crucial for avoiding legal liabilities.
- Contractual Disputes: Ambiguous contract language, conflicting interpretations, and disagreements over change orders can lead to costly and time-consuming disputes. Clear and well-defined contracts are essential for minimizing these risks.
- Force Majeure: Unforeseeable events such as natural disasters, pandemics, and political instability can disrupt project activities and lead to significant losses.
2.2. Risk Management Techniques:
Effective risk management involves a systematic process of identifying, assessing, and mitigating risks. Key techniques include:
- Risk Identification: Brainstorming sessions, checklists, and historical data analysis can be used to identify potential risks. Stakeholder consultations are crucial for uncovering hidden risks.
- Risk Assessment: Qualitative and quantitative techniques can be used to assess the likelihood and impact of each identified risk. Risk matrices and Monte Carlo simulations are commonly used tools.
- Risk Mitigation: Strategies for mitigating risks include risk avoidance, risk transfer (e.g., insurance), risk reduction, and risk acceptance. Contingency planning is essential for addressing risks that cannot be avoided or transferred.
2.3. The Role of Contractual Frameworks in Risk Allocation:
The choice of contractual framework plays a crucial role in allocating risks between the client, contractor, and other stakeholders. Different contract types allocate risks differently, impacting the level of risk borne by each party.
- Fixed-Price Contracts: The contractor assumes the majority of the risk, agreeing to complete the project for a fixed price. These contracts are best suited for projects with well-defined scopes and minimal uncertainties.
- Cost-Plus Contracts: The client reimburses the contractor for all allowable costs plus a fee. These contracts are best suited for projects with poorly defined scopes or significant uncertainties.
- Guaranteed Maximum Price (GMP) Contracts: The contractor agrees to complete the project for a guaranteed maximum price, sharing any cost savings with the client. These contracts offer a balance between risk and reward.
- Target Cost Contracts: The contractor and client agree on a target cost for the project, sharing any cost savings or overruns according to a pre-determined formula. These contracts incentivize collaboration and cost control.
Choosing the appropriate contract type is critical for aligning risk allocation with project objectives and fostering a collaborative relationship between the client and contractor. A careful analysis of project risks and uncertainties is essential for making an informed decision.
Many thanks to our sponsor Focus 360 Energy who helped us prepare this research report.
3. Collaborative Practices in Construction Procurement: Fostering Trust, Transparency, and Shared Objectives
The traditional adversarial relationships between clients, architects, and contractors have often hindered project success, leading to disputes, delays, and cost overruns. Collaborative procurement practices aim to overcome these limitations by fostering trust, transparency, and shared objectives among all stakeholders. This section examines the principles of collaborative procurement and explores various approaches for promoting collaboration throughout the project lifecycle.
3.1. Principles of Collaborative Procurement:
Collaborative procurement is based on the following principles:
- Shared Goals and Objectives: All stakeholders must have a clear understanding of the project goals and objectives and be committed to working together to achieve them.
- Mutual Trust and Respect: A culture of trust and respect is essential for fostering open communication and constructive problem-solving.
- Open Communication and Transparency: Information should be shared freely and transparently among all stakeholders. This includes project progress, risks, and challenges.
- Shared Risk and Reward: Risks and rewards should be shared equitably among all stakeholders. This incentivizes collaboration and discourages adversarial behavior.
- Early Involvement of Key Stakeholders: Engaging key stakeholders early in the project lifecycle allows for their input and expertise to be incorporated into the design and planning process.
- Joint Decision-Making: Decisions should be made collaboratively, taking into account the perspectives of all stakeholders.
3.2. Collaborative Procurement Approaches:
Several procurement approaches promote collaboration and integrated project delivery:
- Integrated Project Delivery (IPD): IPD is a project delivery method that integrates people, systems, business structures, and practices into a process that collaboratively harnesses the talents and insights of all participants to optimize project results, increase value to the owner, reduce waste, and maximize efficiency through all phases of design, fabrication, and construction. American Institute of Architects (AIA)
- Early Contractor Involvement (ECI): ECI involves engaging the contractor early in the design process, allowing them to provide input on constructability, cost optimization, and risk mitigation.
- Partnering: Partnering is a formal agreement between the client and contractor to work collaboratively towards shared goals. Partnering agreements often include provisions for dispute resolution and performance measurement.
- Alliancing: Alliancing is a collaborative procurement approach in which the client and contractor form an alliance to deliver the project. The alliance shares risks and rewards, incentivizing collaboration and innovation.
- Lean Construction: Lean construction principles, such as value stream mapping and pull planning, can be used to optimize project processes, reduce waste, and improve collaboration.
3.3. Benefits of Collaborative Procurement:
Collaborative procurement offers several benefits, including:
- Reduced Costs: Collaboration can lead to cost savings through value engineering, waste reduction, and improved efficiency.
- Improved Schedules: Early involvement of key stakeholders and collaborative problem-solving can help to reduce project delays.
- Enhanced Quality: Collaboration can lead to improved quality through better communication, coordination, and quality control.
- Reduced Disputes: Collaborative relationships can help to prevent disputes and resolve conflicts more effectively.
- Increased Innovation: Collaboration can foster innovation by bringing together diverse perspectives and expertise.
- Improved Stakeholder Satisfaction: Collaborative procurement can lead to increased stakeholder satisfaction through better communication, transparency, and shared success.
Many thanks to our sponsor Focus 360 Energy who helped us prepare this research report.
4. Technological Integration in Construction Procurement: Harnessing the Power of Digitalization
The construction industry has historically lagged behind other sectors in terms of technological adoption. However, recent advancements in digital technologies are transforming construction procurement processes, enabling greater efficiency, transparency, and collaboration. This section examines the key technologies that are driving digitalization in construction procurement and explores their potential benefits.
4.1. Building Information Modeling (BIM):
BIM is a digital representation of a building or infrastructure project that contains all of the information needed for design, construction, and operation. BIM can be used to improve communication and collaboration among stakeholders, reduce errors and omissions, and optimize project costs and schedules. National BIM Standard-United States
4.2. Data Analytics:
Data analytics can be used to analyze vast amounts of data generated during construction projects, providing insights into project performance, risk management, and cost control. Data analytics can also be used to identify trends, predict future outcomes, and optimize decision-making. McKinsey Global Institute
4.3. Online Procurement Platforms:
Online procurement platforms facilitate the sourcing, evaluation, and selection of suppliers and subcontractors. These platforms can streamline the procurement process, improve transparency, and reduce costs. Examples include platforms that offer e-tendering, reverse auctions, and supplier management tools.
4.4. Digital Twins:
Digital twins are virtual replicas of physical assets that can be used to monitor their performance, predict maintenance needs, and optimize their operation. Digital twins can be used to improve asset management and reduce lifecycle costs.
4.5. Artificial Intelligence (AI) and Machine Learning (ML):
AI and ML can be used to automate tasks, improve decision-making, and enhance project outcomes. For example, AI can be used to analyze design options, optimize construction schedules, and predict potential risks. ML can improve resource allocation, optimize supply chains, and create new efficiencies.
4.6. Benefits of Technological Integration:
Technological integration offers several benefits, including:
- Improved Efficiency: Automation and digitalization can streamline procurement processes and reduce administrative overhead.
- Enhanced Transparency: Digital platforms can provide greater transparency into procurement activities, reducing the risk of fraud and corruption.
- Better Communication and Collaboration: BIM and other digital tools can improve communication and collaboration among stakeholders.
- Data-Driven Decision-Making: Data analytics can provide insights into project performance, enabling more informed decision-making.
- Reduced Costs: Technological integration can lead to cost savings through improved efficiency, reduced errors, and optimized resource allocation.
Many thanks to our sponsor Focus 360 Energy who helped us prepare this research report.
5. Sustainability in Construction Procurement: Balancing Economic, Environmental, and Social Considerations
Sustainability is increasingly becoming a critical consideration in construction procurement. Clients and stakeholders are demanding more sustainable buildings and infrastructure that minimize environmental impact, conserve resources, and promote social equity. This section examines the key principles of sustainable construction procurement and explores various approaches for integrating sustainability into the procurement process.
5.1. Principles of Sustainable Construction Procurement:
Sustainable construction procurement is based on the following principles:
- Life Cycle Assessment (LCA): LCA is a method for assessing the environmental impacts of a product or service throughout its entire life cycle, from raw material extraction to disposal. LCA can be used to identify opportunities for reducing environmental impact.
- Sustainable Materials Selection: Choosing materials with low environmental impact, such as recycled content, renewable resources, and low embodied energy, is crucial for sustainable construction.
- Waste Reduction: Minimizing waste generation during construction and demolition is essential for conserving resources and reducing landfill disposal.
- Energy Efficiency: Designing buildings and infrastructure for energy efficiency can significantly reduce greenhouse gas emissions and operating costs.
- Water Conservation: Implementing water-efficient fixtures and landscaping can conserve water resources and reduce water bills.
- Indoor Environmental Quality (IEQ): Ensuring good IEQ can improve occupant health and productivity.
- Social Equity: Promoting social equity by providing opportunities for local businesses and workers is an important aspect of sustainable construction.
5.2. Integrating Sustainability into the Procurement Process:
Sustainability can be integrated into the procurement process through the following measures:
- Establishing Sustainability Goals: Setting clear and measurable sustainability goals is essential for driving sustainable construction practices.
- Developing Sustainability Criteria: Incorporating sustainability criteria into tender documents and evaluation processes can encourage bidders to propose sustainable solutions.
- Requiring Environmental Product Declarations (EPDs): Requiring EPDs for building materials can provide transparency on their environmental impacts.
- Implementing Green Building Rating Systems: Using green building rating systems such as LEED (Leadership in Energy and Environmental Design) or BREEAM (Building Research Establishment Environmental Assessment Method) can provide a framework for achieving sustainability goals. U.S. Green Building Council (USGBC), BREEAM
- Promoting Sustainable Sourcing: Ensuring that materials and products are sourced from sustainable suppliers can reduce the environmental and social impacts of the supply chain.
5.3. Challenges of Sustainable Construction Procurement:
Implementing sustainable construction procurement can be challenging due to:
- Higher Upfront Costs: Sustainable materials and technologies may have higher upfront costs compared to conventional alternatives.
- Lack of Awareness: Some stakeholders may lack awareness of the benefits of sustainable construction or the availability of sustainable products and services.
- Complexity: Integrating sustainability into the procurement process can be complex, requiring specialized knowledge and expertise.
- Data Availability: Reliable data on the environmental impacts of building materials and products may not always be readily available.
Many thanks to our sponsor Focus 360 Energy who helped us prepare this research report.
6. Conclusion: The Future of Construction Procurement – Towards a More Integrated, Collaborative, and Sustainable Approach
Construction procurement is undergoing a significant transformation, driven by technological advancements, evolving client expectations, and a growing emphasis on sustainability. The traditional, fragmented approach to procurement is giving way to a more integrated, collaborative, and sustainable model that prioritizes risk management, fosters trust, and leverages the power of digitalization.
The future of construction procurement will be characterized by:
- Greater Integration: Procurement processes will be more tightly integrated with project design, construction, and operation, enabling better communication and collaboration among stakeholders.
- Increased Collaboration: Collaborative procurement approaches such as IPD and alliancing will become more prevalent, fostering trust and shared objectives.
- Wider Adoption of Technology: Digital technologies such as BIM, data analytics, and online procurement platforms will be widely adopted, improving efficiency, transparency, and decision-making.
- Stronger Focus on Sustainability: Sustainability will be a core consideration in all procurement decisions, driving the adoption of sustainable materials, energy-efficient designs, and waste reduction strategies.
- Enhanced Risk Management: Robust risk management processes will be implemented to identify, assess, and mitigate potential risks throughout the project lifecycle.
Future research should focus on:
- Developing standardized metrics for measuring the success of collaborative procurement approaches.
- Investigating the impact of digitalization on project outcomes and stakeholder satisfaction.
- Exploring new business models that promote collaboration and innovation in the construction industry.
- Developing tools and resources to support the implementation of sustainable construction procurement practices.
By embracing these trends and addressing the challenges ahead, the construction industry can transform its procurement processes to enhance project outcomes, foster greater collaboration, and build a more sustainable future.
Many thanks to our sponsor Focus 360 Energy who helped us prepare this research report.
References
- American Institute of Architects (AIA). (n.d.). Integrated Project Delivery. Retrieved from https://www.aia.org/resources/6319-integrated-project-delivery
- BREEAM. (n.d.). BREEAM. Retrieved from https://www.breeam.com/
- McKinsey Global Institute. (2020). Imagining construction after COVID-19. Retrieved from https://www.mckinsey.com/industries/capital-projects-and-infrastructure/our-insights/imagining-construction-after-covid-19
- National BIM Standard-United States. (n.d.). National BIM Standard-United States. Retrieved from https://www.nationalbimstandard.org/
- U.S. Green Building Council (USGBC). (n.d.). LEED. Retrieved from https://www.usgbc.org/
So, if we’re making buildings ‘smarter’ with digital twins, are we also on the cusp of robot construction workers who never call in sick, or is that still firmly in the realm of science fiction?
That’s a great question! While fully autonomous robot construction crews might still be a bit further down the line, we’re definitely seeing increased automation in construction. Digital twins enabling more efficient prefabrication and modular construction could pave the way for more robotic assistance on site. What are your thoughts on the potential impact of increased automation on job roles within the construction industry?
Editor: FocusNews.Uk
Thank you to our Sponsor Focus 360 Energy
So, all this talk of sustainability… are we finally going to ditch those pesky hard hats for something biodegradable, or are we sticking with the classic until they become vintage?
That’s a great point about hard hats! It highlights the challenge of integrating sustainable materials across all aspects of construction. While biodegradable hard hats might be a while off, exploring options like recycled plastics or innovative bio-based polymers for safety gear is definitely a worthwhile avenue to investigate! What other small, everyday items on construction sites could benefit from a sustainability makeover?
Editor: FocusNews.Uk
Thank you to our Sponsor Focus 360 Energy
The report highlights the potential of online procurement platforms. Could you elaborate on the strategies for ensuring equitable access and participation for smaller subcontractors and suppliers in these digital environments, especially those with limited technological infrastructure?
Thanks for raising this important point! Ensuring equitable access is crucial. Standardizing data formats, providing training resources, and offering tiered subscription models for online procurement platforms could significantly help smaller subcontractors participate. Perhaps government subsidies could encourage adoption of technology among smaller businesses. What other initiatives might level the playing field?
Editor: FocusNews.Uk
Thank you to our Sponsor Focus 360 Energy
Sustainability in construction procurement – noble! But between ‘sustainable materials’ and “higher upfront costs,” how do we stop green choices from being just for those with deep pockets? Or will eco-friendly construction forever be a luxury upgrade?
That’s a critical question! The higher upfront costs of sustainable materials are a real barrier. Perhaps incentivizing sustainable choices through tax breaks or grants could help bridge this gap. What innovative financing models could make eco-friendly construction more accessible to a wider range of projects?
Editor: FocusNews.Uk
Thank you to our Sponsor Focus 360 Energy